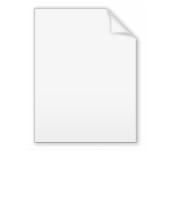
Quality costs
Encyclopedia
The concept of quality costs is a means to quantify the total cost of quality-related efforts and deficiencies. It was first described by Armand V. Feigenbaum
in a 1956 Harvard Business Review
article.
Prior to its introduction, the general perception was that higher quality requires higher costs, either by buying better materials or machines or by hiring more labor. Furthermore, while cost accounting
had evolved to categorize financial transactions into revenues, expenses, and changes in shareholder equity, it had not attempted to categorize costs relevant to quality. By classifying quality-related entries from a company's general ledger
, management and quality practitioners can evaluate investments in quality based on cost improvement and profit enhancement.
Feigenbaum defined the following quality cost areas:
The central theme of quality improvement is that larger investments in prevention drive even larger savings in quality-related failures and appraisal efforts. Feigenbaum's categorization allows the organization to verify this for itself. When confronted with mounting numbers of defects, organizations typically react by throwing more and more people into inspection roles. But inspection is never completely effective, so appraisal costs stay high as long as the failure costs stay high. The only way out of the predicament is to establish the "right" amount of prevention.
Once categorized, quality costs can serve as a means to measure, analyze, budget, and predict.
Variants of the concept of quality costs include cost of poor quality
and categorization based on account type, described by Joseph M. Juran
.
Juran also contributed the concepts of fitness for use and grades of quality. Fitness for use entails meeting or exceeding customers' expectations. Other authors with a strong influence on the topic of the Cost of Quality include Philip B. Crosby and W. Edwards Deming
. Crosby developed the notion of zero defects - do it right the first time. Deming focused on management and process as the solution to quality and put forth that 85% of the cost of quality is a management problem.
Armand V. Feigenbaum
Armand Vallin Feigenbaum is an American quality control expert and businessman. He devised the concept of Total Quality Control, later known as Total Quality Management ....
in a 1956 Harvard Business Review
Harvard Business Review
Harvard Business Review is a general management magazine published since 1922 by Harvard Business School Publishing, owned by the Harvard Business School. A monthly research-based magazine written for business practitioners, it claims a high ranking business readership among academics, executives,...
article.
Prior to its introduction, the general perception was that higher quality requires higher costs, either by buying better materials or machines or by hiring more labor. Furthermore, while cost accounting
Cost accounting
Cost accounting information is designed for managers. Since managers are taking decisions only for their own organization, there is no need for the information to be comparable to similar information from other organizations...
had evolved to categorize financial transactions into revenues, expenses, and changes in shareholder equity, it had not attempted to categorize costs relevant to quality. By classifying quality-related entries from a company's general ledger
Ledger
A ledger is the principal book or computer file for recording and totaling monetary transactions by account, with debits and credits in separate columns and a beginning balance and ending balance for each account. The ledger is a permanent summary of all amounts entered in supporting journals which...
, management and quality practitioners can evaluate investments in quality based on cost improvement and profit enhancement.
Feigenbaum defined the following quality cost areas:
Cost area | Description | Examples | |
---|---|---|---|
Costs of control (Costs of conformance) | Prevention costs | Arise from efforts to keep defects from occurring at all | Statistical process control Statistical process control is the application of statistical methods to the monitoring and control of a process to ensure that it operates at its full potential to produce conforming product. Under SPC, a process behaves predictably to produce as much conforming product as possible with the least... |
Appraisal costs | Arise from detecting defects via inspection, test, audit | ||
Costs of failure of control (Costs of non-conformance) | Internal failure costs | Arise from defects caught internally and dealt with by discarding or repairing the defective items | Scrap Scrap is a term used to describe recyclable and other materials left over from every manner of product consumption, such as parts of vehicles, building supplies, and surplus materials. Unlike waste, scrap has significant monetary value... Rework Rework is the term for the refinishing operation or repair of an electronic printed circuit board assembly. Mass processing techniques are not applicable to single device repair and/or replacement, so specialized techniques are required to replace defective components – most notably area array... |
External failure costs | Arise from defects that actually reach customers |
The central theme of quality improvement is that larger investments in prevention drive even larger savings in quality-related failures and appraisal efforts. Feigenbaum's categorization allows the organization to verify this for itself. When confronted with mounting numbers of defects, organizations typically react by throwing more and more people into inspection roles. But inspection is never completely effective, so appraisal costs stay high as long as the failure costs stay high. The only way out of the predicament is to establish the "right" amount of prevention.
Once categorized, quality costs can serve as a means to measure, analyze, budget, and predict.
Variants of the concept of quality costs include cost of poor quality
Cost of poor quality
Cost of poor quality or poor quality costs , are defined as costs that would disappear if systems, processes, and products were perfect....
and categorization based on account type, described by Joseph M. Juran
Joseph M. Juran
Joseph Moses Juran was a 20th century management consultant who is principally remembered as an evangelist for quality and quality management, writing several influential books on those subjects. He was the brother of Academy Award winner Nathan H...
.
Cost area | Examples |
---|---|
Tangible costs—factory accounts | |
Tangible costs—sales accounts | |
Intangible costs |
Juran also contributed the concepts of fitness for use and grades of quality. Fitness for use entails meeting or exceeding customers' expectations. Other authors with a strong influence on the topic of the Cost of Quality include Philip B. Crosby and W. Edwards Deming
W. Edwards Deming
William Edwards Deming was an American statistician, professor, author, lecturer and consultant. He is perhaps best known for his work in Japan...
. Crosby developed the notion of zero defects - do it right the first time. Deming focused on management and process as the solution to quality and put forth that 85% of the cost of quality is a management problem.
See also
- Cost of poor qualityCost of poor qualityCost of poor quality or poor quality costs , are defined as costs that would disappear if systems, processes, and products were perfect....
- Gold in the mineGold in the mineGold in the mine is a metaphor for the potential savings in quality improvement efforts. It is essentially a restatement of the Pareto principle in the context of quality costs; a little digging in the right place can produce great savings, though investigating every possible opportunity is not...
- Highest quality is lowest costHighest quality is lowest cost"Highest quality is lowest cost" is a Japanese manufacturing aphorism based on the premise that the highest quality manufacturer will earn a reputation that makes buyers prefer, price being reasonably similar, to buy its goods...
- Project triangleProject triangleThe Project Triangle in engineering is a triangle model of project. It is a graphic aid where the three attributes show on the corners of the triangle to show opposition. It is useful to help with intentionally choosing project biases, or analyzing the goals of your project...