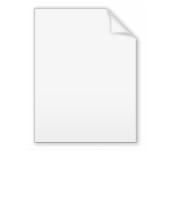
Cost of poor quality
Encyclopedia
Cost of poor quality or poor quality costs (PQC), are defined as costs that would disappear if systems, processes, and products were perfect.
COPQ was popularized by IBM
quality expert H. James Harrington in his 1987 book Poor Quality Costs.
COPQ is a refinement of the concept of quality costs
. In the 1960s, IBM undertook an effort to study its own quality costs and tailored the concept for its own use.. While Feigenbaum's term "quality costs" is technically accurate, it's easy for the uninitiated to jump to the conclusion that better quality products cost more to produce. Harrington adopted the name "poor quality costs" to emphasize the belief that investment in detection and prevention of product failures is more than offset by the savings in reductions in product failures.
COPQ decomposes COPQ into the following elements:
The damages of poor quality augment as the inception point is farther down the supply chain:
TCFP [Total Cost of Faulty Part] =
Direct Cost (manufacturing cost)
➔ failure at supplier's site (bad)
+ Labor Cost (assembly and testing)
+ Overhead Cost (Inventory, handling, shipping costs)
+ Scrapping Cost (of part and attached parts assemblies: Sometimes assemblies cannot be disassembled and have to be scrapped altogether)
+ Rework (applying a new part instead)
➔ failure at manufacturer's site (worse)
+ Repair / Recall Costs (these are costs associated with repairing or replacing a new part / assembly under warranty)
+ Product Liability Costs (These are costs resulting from damages caused by the faulty part to 3rd parties)
➔ failure at customers' site (worst)
COPQ was popularized by IBM
IBM
International Business Machines Corporation or IBM is an American multinational technology and consulting corporation headquartered in Armonk, New York, United States. IBM manufactures and sells computer hardware and software, and it offers infrastructure, hosting and consulting services in areas...
quality expert H. James Harrington in his 1987 book Poor Quality Costs.
COPQ is a refinement of the concept of quality costs
Quality costs
The concept of quality costs is a means to quantify the total cost of quality-related efforts and deficiencies. It was first described by Armand V. Feigenbaum in a 1956 Harvard Business Review article....
. In the 1960s, IBM undertook an effort to study its own quality costs and tailored the concept for its own use.. While Feigenbaum's term "quality costs" is technically accurate, it's easy for the uninitiated to jump to the conclusion that better quality products cost more to produce. Harrington adopted the name "poor quality costs" to emphasize the belief that investment in detection and prevention of product failures is more than offset by the savings in reductions in product failures.
COPQ decomposes COPQ into the following elements:
Cost | Description |
---|---|
Direct poor-quality costs
|
Direct COPQ can be directly derived from entries in the company ledger Ledger A ledger is the principal book or computer file for recording and totaling monetary transactions by account, with debits and credits in separate columns and a beginning balance and ending balance for each account. The ledger is a permanent summary of all amounts entered in supporting journals which... .
|
Indirect poor-quality costs |
Indirect COPQ is difficult to measure because it is a delayed result of time, effort, and financial costs incurred by the customer. These customer costs add up to lost sales and therefore do not appear in the company's ledger. |
Examples
Cost element | Examples | ||
---|---|---|---|
Direct poor-quality costs | Controllable poor-quality cost | Prevention cost | Quality management The term Quality management has a specific meaning within many business sectors. This specific definition, which does not aim to assure 'good quality' by the more general definition , can be considered to have four main components: quality planning, quality control, quality assurance and quality... (for test, inspection, audits, process control) Process capability A process is a unique combination of tools, materials, methods, and people engaged in producing a measurable output; for example a manufacturing line for machine parts... |
Appraisal cost | |||
Resultant poor-quality cost | Internal error cost | Scrap Scrap is a term used to describe recyclable and other materials left over from every manner of product consumption, such as parts of vehicles, building supplies, and surplus materials. Unlike waste, scrap has significant monetary value... and rework Rework Rework is the term for the refinishing operation or repair of an electronic printed circuit board assembly. Mass processing techniques are not applicable to single device repair and/or replacement, so specialized techniques are required to replace defective components – most notably area array... |
|
External error cost | Sales (accounting) In bookkeeping, accounting, and finance, Net sales are operating revenues earned by a company when it sells its products. Revenue are reported directly on the income statement as Sales or Net sales.... Service Level Agreement A service-level agreement is a part of a service contract where the level of service is formally defined. In practice, the term SLA is sometimes used to refer to the contracted delivery time or performance... penalties Warranty In business and legal transactions, a warranty is an assurance by one party to the other party that specific facts or conditions are true or will happen; the other party is permitted to rely on that assurance and seek some type of remedy if it is not true or followed.In real estate transactions, a... obligations |
||
Equipment poor-quality cost | Micrometers, voltmeters, automated test equipment (but not equipment used to make the product) | ||
Indirect poor-quality costs | Customer-incurred cost | Warranty In business and legal transactions, a warranty is an assurance by one party to the other party that specific facts or conditions are true or will happen; the other party is permitted to rely on that assurance and seek some type of remedy if it is not true or followed.In real estate transactions, a... period |
|
Customer-dissatisfaction cost | Dissatisfaction shared by word of mouth | ||
Loss-of-reputation cost | Customer perception of firm |
White collar COPQ
Harrington noted that expanding cost analyses to management and clerical workers could also make a significant dent in waste. He defined the following costs by functional area:Functional area | Controllable COPQ | Resultant COPQ |
---|---|---|
Controller COPQ | |
|
Software COPQ | |
|
Plant administration COPQ | |
|
Purchasing COPQ | |
|
Marketing COPQ | |
|
Personnel COPQ | |
|
Industrial engineering COPQ | |
|
Cost of poor quality by inception point
The damages of poor quality augment as the inception point is farther down the supply chain:
TCFP [Total Cost of Faulty Part] =
Direct Cost (manufacturing cost)
➔ failure at supplier's site (bad)
+ Labor Cost (assembly and testing)
+ Overhead Cost (Inventory, handling, shipping costs)
+ Scrapping Cost (of part and attached parts assemblies: Sometimes assemblies cannot be disassembled and have to be scrapped altogether)
+ Rework (applying a new part instead)
➔ failure at manufacturer's site (worse)
+ Repair / Recall Costs (these are costs associated with repairing or replacing a new part / assembly under warranty)
+ Product Liability Costs (These are costs resulting from damages caused by the faulty part to 3rd parties)
➔ failure at customers' site (worst)