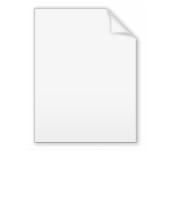
Predictive maintenance
Encyclopedia
Predictive maintenance (PdM) techniques help determine the condition of in-service equipment in order to predict when maintenance should be performed. This approach offers cost savings over routine or time-based preventive maintenance
, because tasks are performed only when warranted.
The main value of Predicted Maintenance is to allow convenient scheduling of corrective maintenance, and to prevent unexpected equipment failures. The key is "the right information in the right time". By knowing which equipment that needs maintenance, the maintenance work can be better planned (spare parts, people etc.) and what would had been "unplanned stops" are transformed to shorter and less "planned stops" thus increasing plant availability. Other values are increased equipment life time, increased plant safety, less accidents with negative impact on environment, an optimised spare parts handling, etc. Check here ->preventive maintenance
, difference between preventive and predictive maintenance
. The ultimate goal of PdM is to perform maintenance at a scheduled point in time when the maintenance activity is most cost-effective and before the equipment loses performance within a threshold. This is in contrast to time- and/or operation count-based maintenance, where a piece of equipment gets maintained whether it needs it or not. Time-based maintenance is labor intensive, ineffective in identifying problems that develop between scheduled inspections, and is not cost-effective.
The "predictive" component of predictive maintenance stems from the goal of predicting the future trend of the equipment's condition. This approach uses principles of statistical process control to determine at what point in the future maintenance activities will be appropriate.
Most PdM inspections are performed while equipment is in service, thereby minimizing disruption of normal system operations. Adoption of PdM can result in substantial cost savings and higher system reliability.
Reliability-centered maintenance
, or RCM, emphasizes the use of predictive maintenance (PdM) techniques in addition to traditional preventive measures. When properly implemented, RCM provides companies with a tool for achieving lowest asset Net Present Costs (NPC) for a given level of performance and risk.
One area that many times is overlooked is how to, in an efficient way, transfer the PdM data to a Computerized Maintenance Management System
(CMMS) system so that the equipment condition data is sent to the right equipment object in the CMMS system in order to trigger maintenace planning, execution and reporting. Unless this is achieved, the PdM solution is of limited value, at least if the PdM solution is implemented on a medium to large size plant with tens of thousands pieces of equipment. In 2010, the mining company Boliden, as a first, implemented a combined Distributed Control System
(DCS) and Pdm solution integrated with the plant CMMS system on an object to object level, transferring equipment data using protocols like Highway Addressable Remote Transducer Protocol (HART), IEC61850
and OLE for process control
(OPC).
technologies such as infrared
, acoustic (partial discharge and airborne ultrasonic), corona detection, vibration analysis, sound level measurements, oil analysis
, and other specific online tests. New methods in this area is to utilize measurements on the actual equipment in combination with measurement of process performance, measured by other devices, to trigger maintenance conditions. This is primarily available in Collaborative Process Automation Systems
(CPAS). Site measurements are often supported by wireless sensor networks to reduce the wiring cost.
Vibration analysis is most productive on high-speed rotating equipment and can be the most expensive component of a PdM program to get up and running. Vibration analysis, when properly done, allows the user to evaluate the condition of equipment and avoid failures. The latest generation of vibration analyzers comprises more capabilities and automated functions than its predecessors. Many units display the full vibration spectrum of three axes simultaneously, providing a snapshot of what is going on with a particular machine. But despite such capabilities, not even the most sophisticated equipment successfully predicts developing problems unless the operator understands and applies the basics of vibration analysis.
Acoustical analysis can be done on a sonic or ultrasonic
level. New ultrasonic techniques for condition monitoring make it possible to “hear” friction and stress in rotating machinery, which can predict deterioration earlier than conventional techniques. Ultrasonic technology is sensitive to high-frequency sounds that are inaudible to the human ear and distinguishes them from lower-frequency sounds and mechanical vibration. Machine friction and stress waves produce distinctive sounds in the upper ultrasonic range.
Changes in these friction and stress waves can suggest deteriorating conditions much earlier than technologies such as vibration or oil analysis. With proper ultrasonic measurement and analysis, it’s possible to differentiate normal wear from abnormal wear, physical damage, imbalance conditions, and lubrication problems based on a direct relationship between asset and operating conditions.
Sonic monitoring equipment is less expensive, but it also has fewer uses than ultrasonic technologies. Sonic technology is useful only on mechanical equipment, while ultrasonic equipment can detect electrical problems and is more flexible and reliable in detecting mechanical problems.
Infrared monitoring and analysis has the widest range of application (from high- to low-speed equipment), and it can be effective for spotting both mechanical and electrical failures; some consider it to currently be the most cost-effective technology.
Oil analysis is a long-term program that, where relevant, can eventually be more predictive than any of the other technologies. It can take years for a plant's oil program to reach this level of sophistication and effectiveness.
Analytical techniques performed on oil samples can be classified in two categories: used oil analysis and wear particle analysis. Used oil analysis determines the condition of the lubricant itself, determines the quality of the lubricant, and checks its suitability for continued use. Wear particle analysis determines the mechanical condition of machine components that are lubricated. Through wear particle analysis, you can identify the composition of the solid material present and evaluate particle type, size, concentration, distribution, and morphology.
Preventive maintenance
Preventive maintenance has the following meanings:#The care and servicing by personnel for the purpose of maintaining equipment and facilities in satisfactory operating condition by providing for systematic inspection, detection, and correction of incipient failures either before they occur or...
, because tasks are performed only when warranted.
The main value of Predicted Maintenance is to allow convenient scheduling of corrective maintenance, and to prevent unexpected equipment failures. The key is "the right information in the right time". By knowing which equipment that needs maintenance, the maintenance work can be better planned (spare parts, people etc.) and what would had been "unplanned stops" are transformed to shorter and less "planned stops" thus increasing plant availability. Other values are increased equipment life time, increased plant safety, less accidents with negative impact on environment, an optimised spare parts handling, etc. Check here ->preventive maintenance
Preventive maintenance
Preventive maintenance has the following meanings:#The care and servicing by personnel for the purpose of maintaining equipment and facilities in satisfactory operating condition by providing for systematic inspection, detection, and correction of incipient failures either before they occur or...
, difference between preventive and predictive maintenance
Overview
PdM, or condition-based maintenance, attempts to evaluate the condition of equipment by performing periodic or continuous (online) equipment condition monitoringCondition monitoring
Condition monitoring is the process of monitoring a parameter of condition in machinery, such that a significant change is indicative of a developing failure. It is a major component of predictive maintenance. The use of conditional monitoring allows maintenance to be scheduled, or other actions...
. The ultimate goal of PdM is to perform maintenance at a scheduled point in time when the maintenance activity is most cost-effective and before the equipment loses performance within a threshold. This is in contrast to time- and/or operation count-based maintenance, where a piece of equipment gets maintained whether it needs it or not. Time-based maintenance is labor intensive, ineffective in identifying problems that develop between scheduled inspections, and is not cost-effective.
The "predictive" component of predictive maintenance stems from the goal of predicting the future trend of the equipment's condition. This approach uses principles of statistical process control to determine at what point in the future maintenance activities will be appropriate.
Most PdM inspections are performed while equipment is in service, thereby minimizing disruption of normal system operations. Adoption of PdM can result in substantial cost savings and higher system reliability.
Reliability-centered maintenance
Reliability Centered Maintenance
Reliability Centered Maintenance, often known as RCM, is a process to ensure that assets continue to do what their users require in their present operating context....
, or RCM, emphasizes the use of predictive maintenance (PdM) techniques in addition to traditional preventive measures. When properly implemented, RCM provides companies with a tool for achieving lowest asset Net Present Costs (NPC) for a given level of performance and risk.
One area that many times is overlooked is how to, in an efficient way, transfer the PdM data to a Computerized Maintenance Management System
Computerized Maintenance Management System
Computerized maintenance management system is also known as enterprise asset management and computerized maintenance management information system ....
(CMMS) system so that the equipment condition data is sent to the right equipment object in the CMMS system in order to trigger maintenace planning, execution and reporting. Unless this is achieved, the PdM solution is of limited value, at least if the PdM solution is implemented on a medium to large size plant with tens of thousands pieces of equipment. In 2010, the mining company Boliden, as a first, implemented a combined Distributed Control System
Distributed control system
A distributed control system refers to a control system usually of a manufacturing system, process or any kind of dynamic system, in which the controller elements are not central in location but are distributed throughout the system with each component sub-system controlled by one or more...
(DCS) and Pdm solution integrated with the plant CMMS system on an object to object level, transferring equipment data using protocols like Highway Addressable Remote Transducer Protocol (HART), IEC61850
IEC61850
IEC 61850 is a standard for the design of electrical substation automation. IEC 61850 is a part of the International Electrotechnical Commission's Technical Committee 57 reference architecture for electric power systems. The abstract data models defined in IEC 61850 can be mapped to a number of...
and OLE for process control
OLE for process control
OLE for Process Control , which stands for Object Linking and Embedding for Process Control, is the original name for a standards specification developed in 1996 by an industrial automation industry task force...
(OPC).
Technologies
To evaluate equipment condition, predictive maintenance utilizes nondestructive testingNondestructive testing
Nondestructive testing or Non-destructive testing is a wide group of analysis techniques used in science and industry to evaluate the properties of a material, component or system without causing damage....
technologies such as infrared
Infrared
Infrared light is electromagnetic radiation with a wavelength longer than that of visible light, measured from the nominal edge of visible red light at 0.74 micrometres , and extending conventionally to 300 µm...
, acoustic (partial discharge and airborne ultrasonic), corona detection, vibration analysis, sound level measurements, oil analysis
Oil analysis
Oil analysis is the laboratory analysis of a lubricant's properties, suspended contaminants, and wear debris. OA is performed during routine preventive maintenance to provide meaningful and accurate information on lubricant and machine condition...
, and other specific online tests. New methods in this area is to utilize measurements on the actual equipment in combination with measurement of process performance, measured by other devices, to trigger maintenance conditions. This is primarily available in Collaborative Process Automation Systems
Collaborative Process Automation Systems
Distributed control systems evolved into Process Automation Systems by the inclusion of additional functionality beyond basic control. The evolution of PAS into the CPAS will add even more capability. In the next phase of their evolution, process automation systems will be considered the sentinel...
(CPAS). Site measurements are often supported by wireless sensor networks to reduce the wiring cost.
Vibration analysis is most productive on high-speed rotating equipment and can be the most expensive component of a PdM program to get up and running. Vibration analysis, when properly done, allows the user to evaluate the condition of equipment and avoid failures. The latest generation of vibration analyzers comprises more capabilities and automated functions than its predecessors. Many units display the full vibration spectrum of three axes simultaneously, providing a snapshot of what is going on with a particular machine. But despite such capabilities, not even the most sophisticated equipment successfully predicts developing problems unless the operator understands and applies the basics of vibration analysis.
Acoustical analysis can be done on a sonic or ultrasonic
Ultrasound
Ultrasound is cyclic sound pressure with a frequency greater than the upper limit of human hearing. Ultrasound is thus not separated from "normal" sound based on differences in physical properties, only the fact that humans cannot hear it. Although this limit varies from person to person, it is...
level. New ultrasonic techniques for condition monitoring make it possible to “hear” friction and stress in rotating machinery, which can predict deterioration earlier than conventional techniques. Ultrasonic technology is sensitive to high-frequency sounds that are inaudible to the human ear and distinguishes them from lower-frequency sounds and mechanical vibration. Machine friction and stress waves produce distinctive sounds in the upper ultrasonic range.
Changes in these friction and stress waves can suggest deteriorating conditions much earlier than technologies such as vibration or oil analysis. With proper ultrasonic measurement and analysis, it’s possible to differentiate normal wear from abnormal wear, physical damage, imbalance conditions, and lubrication problems based on a direct relationship between asset and operating conditions.
Sonic monitoring equipment is less expensive, but it also has fewer uses than ultrasonic technologies. Sonic technology is useful only on mechanical equipment, while ultrasonic equipment can detect electrical problems and is more flexible and reliable in detecting mechanical problems.
Infrared monitoring and analysis has the widest range of application (from high- to low-speed equipment), and it can be effective for spotting both mechanical and electrical failures; some consider it to currently be the most cost-effective technology.
Oil analysis is a long-term program that, where relevant, can eventually be more predictive than any of the other technologies. It can take years for a plant's oil program to reach this level of sophistication and effectiveness.
Analytical techniques performed on oil samples can be classified in two categories: used oil analysis and wear particle analysis. Used oil analysis determines the condition of the lubricant itself, determines the quality of the lubricant, and checks its suitability for continued use. Wear particle analysis determines the mechanical condition of machine components that are lubricated. Through wear particle analysis, you can identify the composition of the solid material present and evaluate particle type, size, concentration, distribution, and morphology.
See also
- Reliability-centered maintenanceReliability Centered MaintenanceReliability Centered Maintenance, often known as RCM, is a process to ensure that assets continue to do what their users require in their present operating context....
- Proactive maintenanceProactive maintenanceProactive maintenance is a maintenance strategy for stabilizing the reliability of machines or equipment. Its central theme involves directing corrective actions aimed at failure root causes, not active failure symptoms, faults, or machine wear conditions....