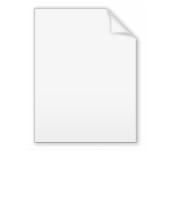
Nitrogen generator
Encyclopedia
Nitrogen generators and stations are stationary or mobile air-to-nitrogen production complexes. In advanced economies, membrane nitrogen
plants have almost ousted alternative processes of nitrogen generation in all cases where nitrogen is not required in commercial volumes.
separation process in nitrogen generators is based on the phenomenon of fixing various gas mixture components by a solid substance called an adsorbent. This phenomenon is brought about by the gas and adsorbent molecules' interaction.
The operating principle of a nitrogen generator utilizing the adsorption technology is based on the dependence of the adsorption rates featured by various gas mixture components upon pressure and temperature factors. Among nitrogen adsorption plants of various types, pressure swing adsorption
(PSA) plants have found the broadest application world-wide.
The system's design is based on the regulation of gas adsorption and adsorbent regeneration by means of changing pressures in two adsorber–adsorbent-containing vessels. This process requires constant temperature, close to ambient. With this process, nitrogen is produced by the plant at the above-atmospheric pressure, while the adsorbent regeneration is accomplished at below-atmospheric pressure.
The swing adsorption process in each of the two adsorbers consists of two stages running for a few minutes. At the adsorption stage the adsorbent serves to adsorb predominantly one of the gas mixture components with the recovery of product nitrogen. At the regeneration stage the adsorbed component is released from the adsorbent and is vented in the atmosphere. The process is then multiply repeated.
systems are unable to provide – up to 99.9995% nitrogen. This nitrogen purity may also be ensured by cryogenic systems, but they are considerably more complex and justified only by large consumption volumes. The nitrogen generators use CMS (carbon molecular sieve
) technology to produce a continuous supply of ultra high purity nitrogen and are available with internal compressors or without.
systems is based on the principle of differential velocity with which various gas mixture components permeate membrane substance. The driving force in the gas separation process is the difference in partial pressures on different membrane sides.
In the petroleum industry, nitrogen is an indispensable component in a number of processes. Most commonly, nitrogen is used to create an inert environment for preventing explosions and for fire safety and to support transportation and transfer of hydrocarbons. Additionally, nitrogen is used for pipeline testing and purging, cleaning technological vessels and cleaning liquefied gas carriers and hydrocarbon storage facilities.
The metal industry generally utilizes nitrogen as a means of protecting ferrous and non-ferrous metals during annealing. Also, nitrogen is helpful in such standard industry processes as neutral tempering, cementing, hard brazing, stress relieving, cyanide hardening, metal-powder sintering and extrusion die cooling.
The primary and very important application of nitrogen in chemical and petrochemical industries is the provision of inert environment aimed at ensuring general industrial safety during cleaning and protection of process vessels. Besides, nitrogen is used for pipelines pressure testing, chemical agents transportation, and regeneration of used catalysts in technological processes.
Paint and varnish production uses nitrogen for the creation of an inert environment in process vessels to ensure safety, as well as for oxygen displacement during packing in order to prevent polymerization of drying oils.
In pharmaceutical industry, nitrogen finds application in pharmaceuticals packaging, and ensuring against explosion and fire safety in activities where fine dispersed substances are used.
In electronics, nitrogen serves as an antioxidant in the manufacture of semi-conductors and electric circuits, heat treatment of finished products, as well as in blowing and cleaning.
In the glass production, nitrogen proves efficient as a cooling agent for bow oven electrodes, oxidation inhibitor during process procedures, as well as air cooler.
Nitrogen
Nitrogen is a chemical element that has the symbol N, atomic number of 7 and atomic mass 14.00674 u. Elemental nitrogen is a colorless, odorless, tasteless, and mostly inert diatomic gas at standard conditions, constituting 78.08% by volume of Earth's atmosphere...
plants have almost ousted alternative processes of nitrogen generation in all cases where nitrogen is not required in commercial volumes.
Adsorption concept
The adsorption gasGas
Gas is one of the three classical states of matter . Near absolute zero, a substance exists as a solid. As heat is added to this substance it melts into a liquid at its melting point , boils into a gas at its boiling point, and if heated high enough would enter a plasma state in which the electrons...
separation process in nitrogen generators is based on the phenomenon of fixing various gas mixture components by a solid substance called an adsorbent. This phenomenon is brought about by the gas and adsorbent molecules' interaction.
Swing adsorption technology
The technology of air-to-nitrogen production with the use of adsorption processes in nitrogen generators is well studied and widely applied at industrial facilities for the recovery of high-purity nitrogen.The operating principle of a nitrogen generator utilizing the adsorption technology is based on the dependence of the adsorption rates featured by various gas mixture components upon pressure and temperature factors. Among nitrogen adsorption plants of various types, pressure swing adsorption
Pressure swing adsorption
Pressure swing adsorption is a technology used to separate some gas species from a mixture of gases under pressure according to the species' molecular characteristics and affinity for an adsorbent material. It operates at near-ambient temperatures and so differs from cryogenic distillation...
(PSA) plants have found the broadest application world-wide.
The system's design is based on the regulation of gas adsorption and adsorbent regeneration by means of changing pressures in two adsorber–adsorbent-containing vessels. This process requires constant temperature, close to ambient. With this process, nitrogen is produced by the plant at the above-atmospheric pressure, while the adsorbent regeneration is accomplished at below-atmospheric pressure.
The swing adsorption process in each of the two adsorbers consists of two stages running for a few minutes. At the adsorption stage the adsorbent serves to adsorb predominantly one of the gas mixture components with the recovery of product nitrogen. At the regeneration stage the adsorbed component is released from the adsorbent and is vented in the atmosphere. The process is then multiply repeated.
High nitrogen purity
Adsorption nitrogen generator plants allow production of high-purity nitrogen from air, which membraneMembrane technology
The membrane technology covers all process engineering measures for the transport of substances between two fractions with the help of permeable membranes...
systems are unable to provide – up to 99.9995% nitrogen. This nitrogen purity may also be ensured by cryogenic systems, but they are considerably more complex and justified only by large consumption volumes. The nitrogen generators use CMS (carbon molecular sieve
Molecular sieve
A molecular sieve is a material containing tiny pores of a precise and uniform size that is used as an adsorbent for gases and liquids.Molecules small enough to pass through the pores are adsorbed while larger molecules are not. It is different from a common filter in that it operates on a...
) technology to produce a continuous supply of ultra high purity nitrogen and are available with internal compressors or without.
Low operating costs
- By substitution of out-of-date air separation plants nitrogen production savings largely exceed 50%.
- The net cost of nitrogen produced by nitrogen generators is 20 to 30 times less than the cost of bottled or liquefied nitrogen.
Membrane technology
Gas separation concept
The operation of membraneArtificial membrane
An artificial membrane, or synthetic membrane, is a synthetically created membrane which is usually intended for separation purposes in laboratory or in industry. Synthetic membranes have been successfully used for small and large-scale industrial processes since the middle of twentieth century. A...
systems is based on the principle of differential velocity with which various gas mixture components permeate membrane substance. The driving force in the gas separation process is the difference in partial pressures on different membrane sides.
Membrane cartridge
Structurally, a hollow-fiber membrane represents a cylindrical cartridge functioning as a spool with specifically reeled polymer fibers. Gas flow is supplied under pressure into a bundle of membrane fibers. Due to the difference in partial pressures on the external and internal membrane surface gas flow separation is accomplished.Economic benefits
- By substitution of out-of-date cryogenic or adsorption systems nitrogen production savings generally exceed 50%.
- The net cost of nitrogen produced by nitrogen complexes is 20 to 30 times less than the cost of cylinder or liquefied nitrogen.
Module design
With respect to the simplicity of the system, a nitrogen generator can be split into modules. This is in direct contrast to classical systems where the equipment is designed for a certain stage of the separation process. Using a modular system, the generation facility may be built from a selection of preexisting equipment and where necessary, the output capacity of a plant may be increased at the minimum cost. This option appears all the more useful where a project envisages a subsequent increase in enterprise capacity, or where demand may simply require on site production of nitrogen by employing equipment that is already present.Dependability
Gas separation units have no moving component parts, thus ensuring the exceptional reliability of Company plants. Membranes are highly resistant to vibration and shocks, chemically inert to greases, moisture-insensitive, and capable of operating over a wide temperature range of –40°С to +60°С. With appropriate maintenance, membrane unit useful life ranges between 130,000 and 180,000 hours (15 to 20 years of continuous operation).Disadvantages
- limited capacity
- relativity low purity (higher purity applications are available at lower flow rates ≤ 10L/min)
Applications of nitrogen generators
- PetroleumPetroleumPetroleum or crude oil is a naturally occurring, flammable liquid consisting of a complex mixture of hydrocarbons of various molecular weights and other liquid organic compounds, that are found in geologic formations beneath the Earth's surface. Petroleum is recovered mostly through oil drilling...
industry
In the petroleum industry, nitrogen is an indispensable component in a number of processes. Most commonly, nitrogen is used to create an inert environment for preventing explosions and for fire safety and to support transportation and transfer of hydrocarbons. Additionally, nitrogen is used for pipeline testing and purging, cleaning technological vessels and cleaning liquefied gas carriers and hydrocarbon storage facilities.
- MetallurgyMetallurgyMetallurgy is a domain of materials science that studies the physical and chemical behavior of metallic elements, their intermetallic compounds, and their mixtures, which are called alloys. It is also the technology of metals: the way in which science is applied to their practical use...
The metal industry generally utilizes nitrogen as a means of protecting ferrous and non-ferrous metals during annealing. Also, nitrogen is helpful in such standard industry processes as neutral tempering, cementing, hard brazing, stress relieving, cyanide hardening, metal-powder sintering and extrusion die cooling.
- Chemical and petrochemical industries
The primary and very important application of nitrogen in chemical and petrochemical industries is the provision of inert environment aimed at ensuring general industrial safety during cleaning and protection of process vessels. Besides, nitrogen is used for pipelines pressure testing, chemical agents transportation, and regeneration of used catalysts in technological processes.
- Paint-and-varnish industry
Paint and varnish production uses nitrogen for the creation of an inert environment in process vessels to ensure safety, as well as for oxygen displacement during packing in order to prevent polymerization of drying oils.
- Pharmaceutical industry
In pharmaceutical industry, nitrogen finds application in pharmaceuticals packaging, and ensuring against explosion and fire safety in activities where fine dispersed substances are used.
- Electronics
In electronics, nitrogen serves as an antioxidant in the manufacture of semi-conductors and electric circuits, heat treatment of finished products, as well as in blowing and cleaning.
- Glass industry
In the glass production, nitrogen proves efficient as a cooling agent for bow oven electrodes, oxidation inhibitor during process procedures, as well as air cooler.