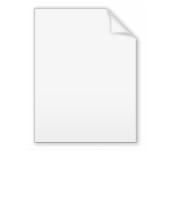
Manufacturing resource planning
Encyclopedia
Manufacturing resource planning (MRP II) is defined by APICS
as a method for the effective planning of all resources of a manufacturing company. Ideally, it addresses operational planning in units, financial planning, and has a simulation capability to answer "what-if" questions
and extension of closed-loop MRP
.
This is not exclusively a software function, but a marriage of people skills, dedication to data base accuracy, and computer resources. It is a total company management concept for using human resources more productively.
Almost every MRP II system is modular in construction. Characteristic basic modules in an MRP II system are:
together with auxiliary systems such as:
and related systems such as:
The MRP II system integrates these modules together so that they use common data and freely exchange information, in a model of how a manufacturing enterprise should and can operate. The MRP II approach is therefore very different from the “point solution” approach, where individual systems are deployed to help a company plan, control or manage a specific activity. MRP II is by definition fully integrated or at least fully interfaced.
MRP ( and MRPII ) evolved from the earliest commercial database management package developed by Gene Thomas at IBM in the 1960s. The original structure was called BOMP ( bill-of-materials processor ), which evolved in the next generation into a more generalized tool called DBOMP (Database Organization and Maintenance Program). These were run on mainframes, such as IBM/360.
The vision for MRP and MRPII was to centralize and integrate business information in a way that would facilitate decision making for production line managers and increase the efficiency of the production line overall. In the 1980s, manufacturers developed systems for calculating the resource requirements of a production run based on sales forecasts. In order to calculate the raw materials needed to produce products and to schedule the purchase of those materials along with the machine and labor time needed, production managers recognized that they would need to use computer and software technology to manage the information. Originally, manufacturing operations built custom software programs that ran on mainframes.
Material requirements planning (MRP) was an early iteration of the integrated information systems vision. MRP information systems helped managers determine the quantity and timing of raw materials purchases. Information systems that would assist managers with other parts of the manufacturing process, MRPII, followed. While MRP was primarily concerned with materials, MRPII was concerned with the integration of all aspects of the manufacturing process, including materials, finance and human relations.
Like today’s ERP systems, MRPII was designed to integrate a lot of information by way of a centralized database. However, the hardware, software, and relational database technology of the 1980s was not advanced enough to provide the speed and capacity to run these systems in real-time, and the cost of these systems was prohibitive for most businesses. Nonetheless, the vision had been established, and shifts in the underlying business processes along with rapid advances in technology led to the more affordable enterprise and application integration systems that big businesses and many medium and smaller businesses use today (Monk and Wagner).
MRP is concerned primarily with manufacturing materials while MRPII is concerned with the coordination of the entire manufacturing production, including materials, finance, and human relations. The goal of MRPII is to provide consistent data to all players in the manufacturing process as the product moves through the production line.
Paper-based information systems and non-integrated computer systems that provide paper or disk outputs result in many information errors, including missing data, redundant data, numerical errors that result from being incorrectly keyed into the system, incorrect calculations based on numerical errors, and bad decisions based on incorrect or old data. In addition, some data is unreliable in non-integrated systems because the same data is categorized differently in the individual databases used by different functional areas.
MRPII systems begin with MRP, material requirements planning. MRP allows for the input of sales forecasts from sales and marketing. These forecasts determine the raw materials demand. MRP and MRPII systems draw on a master production schedule, the breakdown of specific plans for each product on a line. While MRP allows for the coordination of raw materials purchasing, MRPII facilitates the development of a detailed production schedule that accounts for machine and labor capacity, scheduling the production runs according to the arrival of materials. An MRPII output is a final labor and machine schedule. Data about the cost of production, including machine time, labor time and materials used, as well as final production numbers, is provided from the MRPII system to accounting and finance (Monk and Wagner).
For design / engineering:
For financial and costing:
and MRP II, as well as the planning modules in current APS and ERP
systems, are actually sets of heuristics. Better production plans could be obtained by optimization over more powerful mathematical programming
models, usually integer programming
models. While they acknowledge that the use of heuristics, like those prescribed by MRP and MRP II, were necessary in the past due to lack of computational power to solve complex optimization models, this is no longer true.
APICS
APICS The Association for Operations Management, is a not-for-profit international education organization, offering certification programs, training tools and networking opportunities to increase workplace performance...
as a method for the effective planning of all resources of a manufacturing company. Ideally, it addresses operational planning in units, financial planning, and has a simulation capability to answer "what-if" questions
and extension of closed-loop MRP
Material requirements planning
Material requirements planning is a production planning and inventory control system used to manage manufacturing processes. Most MRP systems are software-based, while it is possible to conduct MRP by hand as well....
.
This is not exclusively a software function, but a marriage of people skills, dedication to data base accuracy, and computer resources. It is a total company management concept for using human resources more productively.
Key functions and features
MRP II is not a proprietary software system and can thus take many forms. It is almost impossible to visualize an MRP II system that does not use a computer, but an MRP II system can be based on either purchased–licensed or in-house software.Almost every MRP II system is modular in construction. Characteristic basic modules in an MRP II system are:
- Master production scheduleMaster Production Schedule- What is Master Production Schedule or MPS? :A Master Production Schedule or MPS is the plan that a company has developed for production, inventory, staffing, etc. It sets the quantity of each end item to be completed in each week of a short-range planning horizon. A Master Production Schedule is...
(MPS) - Item master data (technical data)
- Bill of materialsBill of materialsA bill of materials is a list of the raw materials, sub-assemblies, intermediate assemblies, sub-components, components, parts and the quantities of each needed to manufacture an end product...
(BOM) (technical data) - Production resources data (manufacturing technical data)
- Inventories and orders (inventory control)
- Purchasing managementPurchasing managementPurchasing management is the management of purchasing process, and related aspects in an organization. Because of production companies purchase nowadays about 70% of their turnover, and service companies purchase approximately 40% of their turnover , purchasing management is one of the most...
- Material requirements planningMaterial requirements planningMaterial requirements planning is a production planning and inventory control system used to manage manufacturing processes. Most MRP systems are software-based, while it is possible to conduct MRP by hand as well....
(MRP) - Shop floor control (SFC)
- Capacity planningCapacity planningCapacity planning is the process of determining the production capacity needed by an organization to meet changing demands for its products. In the context of capacity planning, "capacity" is the maximum amount of work that an organization is capable of completing in a given period of time...
or capacity requirements planning (CRP) - Standard costing (cost control)
- Cost reporting / management (cost control)
together with auxiliary systems such as:
- Business planning
- Lot traceability
- Contract management
- Tool management
- Engineering change control
- Configuration management
- Shop floor data collection
- Sales analysis and forecasting
- Finite capacity scheduling (FCS)
and related systems such as:
- General ledgerGeneral ledgerThe main accounting record of a business which uses double-entry bookkeeping. It will usually include accounts for such items as current assets, fixed assets, liabilities, revenue and expense items, gains and losses. Each General Ledger is divided into debits and credits sections. The left hand...
- Accounts payableAccounts payableAccounts payable is a file or account sub-ledger that records amounts that a person or company owes to suppliers, but has not paid yet , sometimes referred as trade payables. When an invoice is received, it is added to the file, and then removed when it is paid...
(purchase ledger) - Accounts receivableAccounts receivableAccounts receivable also known as Debtors, is money owed to a business by its clients and shown on its Balance Sheet as an asset...
(sales ledger) - Sales order management
- Distribution requirements planning (DRP)
- AutomatedAutomationAutomation is the use of control systems and information technologies to reduce the need for human work in the production of goods and services. In the scope of industrialization, automation is a step beyond mechanization...
warehouse management - Project management
- Technical records
- Estimating
- Computer-aided designComputer-aided designComputer-aided design , also known as computer-aided design and drafting , is the use of computer technology for the process of design and design-documentation. Computer Aided Drafting describes the process of drafting with a computer...
/computer-aided manufacturingComputer-aided manufacturingComputer-aided manufacturing is the use of computer software to control machine tools and related machinery in the manufacturing of workpieces. This is not the only definition for CAM, but it is the most common; CAM may also refer to the use of a computer to assist in all operations of a...
(CAD/CAM) - CAPP
The MRP II system integrates these modules together so that they use common data and freely exchange information, in a model of how a manufacturing enterprise should and can operate. The MRP II approach is therefore very different from the “point solution” approach, where individual systems are deployed to help a company plan, control or manage a specific activity. MRP II is by definition fully integrated or at least fully interfaced.
Industry specifics
MRP II systems have been implemented in most manufacturing industries. Some industries need specialised functions e.g. lot traceability in regulated manufacturing such as pharmaceuticals or food. Other industries can afford to disregard facilities required by others e.g. the tableware industry has few starting materials – mainly clay – and does not need complex materials planning. Capacity planning is the key to success in this as in many industries, and it is in those that MRP II is less appropriate.MRP and MRPII: History and evolution
Material requirements planning (MRP) and manufacturing resource planning (MRPII) are predecessors of enterprise resource planning (ERP), a business information integration system. The development of these manufacturing coordination and integration methods and tools made today’s ERP systems possible. Both MRP and MRPII are still widely used, independently and as modules of more comprehensive ERP systems, but the original vision of integrated information systems as we know them today began with the development of MRP and MRPII in manufacturing.MRP ( and MRPII ) evolved from the earliest commercial database management package developed by Gene Thomas at IBM in the 1960s. The original structure was called BOMP ( bill-of-materials processor ), which evolved in the next generation into a more generalized tool called DBOMP (Database Organization and Maintenance Program). These were run on mainframes, such as IBM/360.
The vision for MRP and MRPII was to centralize and integrate business information in a way that would facilitate decision making for production line managers and increase the efficiency of the production line overall. In the 1980s, manufacturers developed systems for calculating the resource requirements of a production run based on sales forecasts. In order to calculate the raw materials needed to produce products and to schedule the purchase of those materials along with the machine and labor time needed, production managers recognized that they would need to use computer and software technology to manage the information. Originally, manufacturing operations built custom software programs that ran on mainframes.
Material requirements planning (MRP) was an early iteration of the integrated information systems vision. MRP information systems helped managers determine the quantity and timing of raw materials purchases. Information systems that would assist managers with other parts of the manufacturing process, MRPII, followed. While MRP was primarily concerned with materials, MRPII was concerned with the integration of all aspects of the manufacturing process, including materials, finance and human relations.
Like today’s ERP systems, MRPII was designed to integrate a lot of information by way of a centralized database. However, the hardware, software, and relational database technology of the 1980s was not advanced enough to provide the speed and capacity to run these systems in real-time, and the cost of these systems was prohibitive for most businesses. Nonetheless, the vision had been established, and shifts in the underlying business processes along with rapid advances in technology led to the more affordable enterprise and application integration systems that big businesses and many medium and smaller businesses use today (Monk and Wagner).
MRP and MRPII: General concepts
Material requirements planning (MRP) and manufacturing resource planning (MRPII) are both incremental information integration business process strategies that are implemented using hardware and modular software applications linked to a central database that stores and delivers business data and information.MRP is concerned primarily with manufacturing materials while MRPII is concerned with the coordination of the entire manufacturing production, including materials, finance, and human relations. The goal of MRPII is to provide consistent data to all players in the manufacturing process as the product moves through the production line.
Paper-based information systems and non-integrated computer systems that provide paper or disk outputs result in many information errors, including missing data, redundant data, numerical errors that result from being incorrectly keyed into the system, incorrect calculations based on numerical errors, and bad decisions based on incorrect or old data. In addition, some data is unreliable in non-integrated systems because the same data is categorized differently in the individual databases used by different functional areas.
MRPII systems begin with MRP, material requirements planning. MRP allows for the input of sales forecasts from sales and marketing. These forecasts determine the raw materials demand. MRP and MRPII systems draw on a master production schedule, the breakdown of specific plans for each product on a line. While MRP allows for the coordination of raw materials purchasing, MRPII facilitates the development of a detailed production schedule that accounts for machine and labor capacity, scheduling the production runs according to the arrival of materials. An MRPII output is a final labor and machine schedule. Data about the cost of production, including machine time, labor time and materials used, as well as final production numbers, is provided from the MRPII system to accounting and finance (Monk and Wagner).
Manufacturing Management Software
For the companies that want to integrate their other departments with their manufacturing management, ERP softwares are necessary.Benefits
MRP II systems can provide:- Better control of inventories
- Improved scheduling
- Productive relationships with suppliers
For design / engineering:
- Improved design control
- Better quality and quality control
For financial and costing:
- Reduced working capitalWorking capitalWorking capital is a financial metric which represents operating liquidity available to a business, organization or other entity, including governmental entity. Along with fixed assets such as plant and equipment, working capital is considered a part of operating capital. Net working capital is...
for inventory - Improved cash flow through quicker deliveries
- Accurate inventory records
Criticism
Authors like Pochet and Wolsey argue that MRPMRP
The initialism MRP or M.R.P. can stand for many things:Business, economics and management* Manufacturer's recommended price* Manufacturing resource planning * Marginal Revenue Product, see Marginal revenue productivity theory of wages...
and MRP II, as well as the planning modules in current APS and ERP
Enterprise resource planning
Enterprise resource planning systems integrate internal and external management information across an entire organization, embracing finance/accounting, manufacturing, sales and service, customer relationship management, etc. ERP systems automate this activity with an integrated software application...
systems, are actually sets of heuristics. Better production plans could be obtained by optimization over more powerful mathematical programming
Mathematical Programming
Mathematical Programming, established in 1971, and published by Springer Science+Business Media, is the official scientific journal of the Mathematical Optimization Society. It currently consists of two series: A and B. The "A" series contains general publications. The "B" series focuses on topical...
models, usually integer programming
Integer programming
An integer programming problem is a mathematical optimization or feasibility program in which some or all of the variables are restricted to be integers. In many settings the term refers to integer linear programming, which is also known as mixed integer programming.Integer programming is NP-hard...
models. While they acknowledge that the use of heuristics, like those prescribed by MRP and MRP II, were necessary in the past due to lack of computational power to solve complex optimization models, this is no longer true.
See also
- CONWIPCONWIPCONstant Work in Process are pull-oriented production control systems. Such systems can be classified as pull and push systems . In a push system, the production order is scheduled and the material is pushed into the production line...
- C-VARWIP
- Document automationDocument automationDocument automation is the design of systems and workflow that assist in the creation of electronic documents. These include logic based systems that use segments of pre-existing text and/or data to assemble a new document. This process is increasingly used within certain industries to assemble...
for Supply Chain and Logistics - Enterprise resource planning (ERP)Enterprise resource planningEnterprise resource planning systems integrate internal and external management information across an entire organization, embracing finance/accounting, manufacturing, sales and service, customer relationship management, etc. ERP systems automate this activity with an integrated software application...
- Just-in-time (business)
- kanbanKanban, also spelled kamban, and literally meaning "signboard" or "billboard", is a concept related to lean and just-in-time production. According to Taiichi Ohno, the man credited with developing Just-in-time, kanban is one means through which JIT is achieved.Kanban is not an inventory control system...
- ManufacturingManufacturingManufacturing is the use of machines, tools and labor to produce goods for use or sale. The term may refer to a range of human activity, from handicraft to high tech, but is most commonly applied to industrial production, in which raw materials are transformed into finished goods on a large scale...
- Material requirements planning (MRP)Material requirements planningMaterial requirements planning is a production planning and inventory control system used to manage manufacturing processes. Most MRP systems are software-based, while it is possible to conduct MRP by hand as well....
- Scheduling (production processes)Scheduling (production processes)Scheduling is an important tool for manufacturing and engineering, where it can have a major impact on the productivity of a process. In manufacturing, the purpose of scheduling is to minimize the production time and costs, by telling a production facility when to make, with which staff, and on...
- Supply chain managementSupply chain managementSupply chain management is the management of a network of interconnected businesses involved in the ultimate provision of product and service packages required by end customers...
- Distribution resource planningDistribution Resource PlanningDistribution resource planning is a method used in business administration for planning orders within a supply chain. DRP enables the user to set certain inventory control parameters and calculate the time-phased inventory requirements...
- Warehouse management systemWarehouse management systemA warehouse management system, or WMS, is a key part of the supply chain and primarily aims to control the movement and storage of materials within a warehouse and process the associated transactions, including shipping, receiving, putaway and picking...
- Warehouse control systemWarehouse control systemA warehouse control system is a software application that directs the real-time activities within warehouses and distribution centers. As the “traffic cop” for the warehouse/distribution center, the WCS is responsible for keeping everything running smoothly, maximizing the efficiency of the...