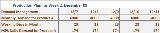
Master Production Schedule
Encyclopedia
What is Master Production Schedule or MPS?
A Master Production Schedule or MPS is the plan that a company has developed for production, inventory, staffing, etc. It sets the quantity of each end item to be completed in each week of a short-range planning horizon. A Master Production Schedule is the master of all schedules. It is a plan for future production of end items.MPS INPUTS:
--> Forecast Demand
--> Production Costs
--> Inventory Costs
--> Customer Orders
--> Inventory Levels
--> Supply
--> Lot Size
--> Production Lead Time
--> Capacity
MPS OUTPUT (production plan):
--> Amounts to be Produced
--> Staffing Levels
--> Quantity Available to Promise
--> Projected Available Balance
The Master Production Schedule gives production, planning, purchasing, and top management the information needed to plan and control the manufacturing operation. The application ties overall business planning and forecasting to detail operations through the Master Production Schedule.
The Master Production Schedule will drive detailed material and production requirements in the Material Requirements Planning module.
Due to software limitations, but especially the intense work required by the "master production schedulers", schedules do not include every aspect of production, but only key elements that have proven their control effectivity, such as forecast demand, production costs, inventory costs, lead time, working hours, capacity, inventory levels, available storage, and parts supply. The choice of what to model varies among companies and factories. The MPS is a statement of what the company expects to produce and purchase (i.e. quantity to be produced, staffing levels, dates, available to promise, projected balance).
The MPS translates the business plan
Business plan
A business plan is a formal statement of a set of business goals, the reasons why they are believed attainable, and the plan for reaching those goals. It may also contain background information about the organization or team attempting to reach those goals....
, including forecast demand, into a production plan using planned orders in a true multi-level optional component scheduling environment. Using MPS helps avoid shortages, costly expediting, last minute scheduling, and inefficient allocation of resources. Working with MPS allows businesses to consolidate planned parts, produce master schedules and forecasts for any level of the Bill of Material (BOM) for any type of part.
How an MPS works
By using several variables as inputs the MPS will generate a set of outputs used for decision makingDecision making
Decision making can be regarded as the mental processes resulting in the selection of a course of action among several alternative scenarios. Every decision making process produces a final choice. The output can be an action or an opinion of choice.- Overview :Human performance in decision terms...
. Inputs may include forecast demand, production costs, inventory
Inventory
Inventory means a list compiled for some formal purpose, such as the details of an estate going to probate, or the contents of a house let furnished. This remains the prime meaning in British English...
costs, customer orders, inventory levels, supply, lot size, production lead time, and capacity. Inputs may be automatically generated by an ERP system that links a sales
Sales
A sale is the act of selling a product or service in return for money or other compensation. It is an act of completion of a commercial activity....
department with a production department. For instance, when the sales department records a sale, the forecast demand may be automatically shifted to meet the new demand. Inputs may also be inputted manually from forecasts that have also been calculated manually. Outputs may include amounts to be produced, staffing levels, quantity available to promise, and projected available balance. Outputs may be used to create a Material Requirements Planning
Material requirements planning
Material requirements planning is a production planning and inventory control system used to manage manufacturing processes. Most MRP systems are software-based, while it is possible to conduct MRP by hand as well....
(MRP) schedule.
A master production schedule may be necessary for organizations to synchronize their operations and become more efficient. An effective MPS ultimately will:
- Give production, planning, purchasing, and management the information to plan and control manufacturing
- Tie overall business planning and forecasting to detail operations
- Enable marketing to make legitimate delivery commitments to warehouses and customers
- Increase the efficiency and accuracy of a company's manufacturing
MPS issues:
- Width of the time bucket
- Planning horizonPlanning horizonThe planning horizon is the amount of time an organization will look into the future when preparing a strategic plan. Many commercial companies use a five-year planning horizon, but other organizations such as the Forestry Commission in the UK have to use a much longer planning horizon to form...
- Rolling plan
- Time fencing
- Schedule freezing
Production plan
An example of a master production schedule for "product A".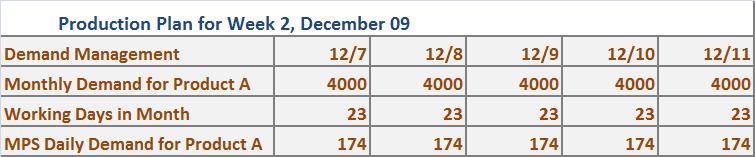
See also
- Material Requirements PlanningMaterial requirements planningMaterial requirements planning is a production planning and inventory control system used to manage manufacturing processes. Most MRP systems are software-based, while it is possible to conduct MRP by hand as well....
- MRP IIManufacturing resource planningManufacturing resource planning is defined by APICS as a method for the effective planning of all resources of a manufacturing company...
- SchedulingScheduling (production processes)Scheduling is an important tool for manufacturing and engineering, where it can have a major impact on the productivity of a process. In manufacturing, the purpose of scheduling is to minimize the production time and costs, by telling a production facility when to make, with which staff, and on...
- ERPEnterprise resource planningEnterprise resource planning systems integrate internal and external management information across an entire organization, embracing finance/accounting, manufacturing, sales and service, customer relationship management, etc. ERP systems automate this activity with an integrated software application...
- ManufacturingManufacturingManufacturing is the use of machines, tools and labor to produce goods for use or sale. The term may refer to a range of human activity, from handicraft to high tech, but is most commonly applied to industrial production, in which raw materials are transformed into finished goods on a large scale...
- Available-to-promiseAvailable-to-promiseAvailable-to-promise is a business function that provides a response to customer order enquiries, based on resource availability. It generates available quantities of the requested product, and delivery due dates...