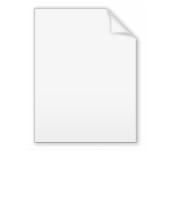
Lurgi-Ruhrgas process
Encyclopedia
The Lurgi–Ruhrgas process is an above-ground coal
liquefaction and shale oil extraction technology. It is classified as a hot recycled solids technology.
(brown coal). The technology is named after its developers Lurgi Gesellschaft für Warmetechnik G.m.b.H.
and Ruhrgas AG
. Over a time, the process was used for coal processing in Japan, Germany, the United Kingdom, Argentina, and former Yugoslavia. The plant in Japan processed also cracking petroleum oils to olefins
.
In 1947–1949, the Lurgi–Ruhrgas process was used in Germany for shale oil
production. In Lukavac
, Bosnia and Herzegovina
, two retorts for liquefaction of lignite were in operation from 1963 to 1968. The capacity of the plant was 850 ton of lignite per day. The plant in Lincolnshire
, the United Kingdom, operated in 1978–1979 with capacity of 900 ton of coal per day. In late 1960s and early 1970s oil shale
s from different European countries and from the Green River Formation
of Colorado
, the United States, were tested at the Lurgi's pilot plant in Frankfurt
. In the United States, the technology was promoted in cooperation with Dravo Corporation
. In 1970s, the technology was licensed to the Rio Blanco Shale Oil Project for construction of a modular retort in combination with the modified in situ process. However, this plan was terminated.
In 1980, the Natural Resources Authority of Jordan commissioned from the Klöckner
-Lurgi
consortium a pre-feasibility study of construction of an oil shale retorting complex in Jordan
using Lurgi-Ruhrgas process. However, although the study found the technology feasible, it was never implemented.
). The heat is transferred from the heated char or spent oil shale to the coal or raw oil shale causing pyrolysis. As a result, oil shale decomposes to shale oil vapors, oil shale gas
and spent oil shale. The oil vapor and product gases passes through a hot cyclone for cleaning before sending to the condenser
. In condenser, shale oil is separated from product gases.
The spent oil shale, still including residual carbon (char
), is burnt at a lift pipe combustor
to heat the process. If necessary, additional fuel oil is used for combustion. During the combustion process, heated solid particles in the pipe are moved to the surge bin by pre-heated air that is introduced from the bottom of the pipe. At the surge bin, solids and gases are separated, and solid particles are transferred to the mixer unit to conduct a pyrolysis of the raw oil shale.
One of the disadvantages of this technology is the fact that produced shale oil vapors are mixed with shale ash causing impurities in shale oil. Ensuring the quality of produced shale oil is complicated as compared with other mineral dusts the shale ash is more difficult to collect.
Coal
Coal is a combustible black or brownish-black sedimentary rock usually occurring in rock strata in layers or veins called coal beds or coal seams. The harder forms, such as anthracite coal, can be regarded as metamorphic rock because of later exposure to elevated temperature and pressure...
liquefaction and shale oil extraction technology. It is classified as a hot recycled solids technology.
History
The Lurgi–Ruhrgas process was originally invented in 1940s and further developed in the 1950s for a low-temperature liquefaction of ligniteLignite
Lignite, often referred to as brown coal, or Rosebud coal by Northern Pacific Railroad,is a soft brown fuel with characteristics that put it somewhere between coal and peat...
(brown coal). The technology is named after its developers Lurgi Gesellschaft für Warmetechnik G.m.b.H.
Lurgi AG
Lurgi GmbH is a German engineering, construction and chemical process licensing company. The head office is located in Frankfurt am Main. Lurgi GmbH has been part of Air Liquide S. A. since 2007.- History :...
and Ruhrgas AG
E.ON
E.ON AG, marketed with an interpunct as E•ON, is the holding company of the world's largest investor-owned energy service provider based in Düsseldorf, Germany. The name comes from the Greek word aeon which means eternity....
. Over a time, the process was used for coal processing in Japan, Germany, the United Kingdom, Argentina, and former Yugoslavia. The plant in Japan processed also cracking petroleum oils to olefins
Alkene
In organic chemistry, an alkene, olefin, or olefine is an unsaturated chemical compound containing at least one carbon-to-carbon double bond...
.
In 1947–1949, the Lurgi–Ruhrgas process was used in Germany for shale oil
Shale oil
Shale oil, known also as kerogen oil or oil-shale oil, is an unconventional oil produced from oil shale by pyrolysis, hydrogenation, or thermal dissolution. These processes convert the organic matter within the rock into synthetic oil and gas...
production. In Lukavac
Lukavac
Lukavac is a town and municipality in northwestern Bosnia and Herzegovina. The town is the seat of a municipality within the Tuzla Canton of the Federation of Bosnia and Herzegovina.-Geography:Lukavac covers an area of 352,66 km2...
, Bosnia and Herzegovina
Bosnia and Herzegovina
Bosnia and Herzegovina , sometimes called Bosnia-Herzegovina or simply Bosnia, is a country in Southern Europe, on the Balkan Peninsula. Bordered by Croatia to the north, west and south, Serbia to the east, and Montenegro to the southeast, Bosnia and Herzegovina is almost landlocked, except for the...
, two retorts for liquefaction of lignite were in operation from 1963 to 1968. The capacity of the plant was 850 ton of lignite per day. The plant in Lincolnshire
Lincolnshire
Lincolnshire is a county in the east of England. It borders Norfolk to the south east, Cambridgeshire to the south, Rutland to the south west, Leicestershire and Nottinghamshire to the west, South Yorkshire to the north west, and the East Riding of Yorkshire to the north. It also borders...
, the United Kingdom, operated in 1978–1979 with capacity of 900 ton of coal per day. In late 1960s and early 1970s oil shale
Oil shale
Oil shale, an organic-rich fine-grained sedimentary rock, contains significant amounts of kerogen from which liquid hydrocarbons called shale oil can be produced...
s from different European countries and from the Green River Formation
Green River Formation
The Green River Formation is an Eocene geologic formation that records the sedimentation in a group of intermountain lakes. The sediments are deposited in very fine layers, a dark layer during the growing season and a light-hue inorganic layer in winter. Each pair of layers is called a varve and...
of Colorado
Colorado
Colorado is a U.S. state that encompasses much of the Rocky Mountains as well as the northeastern portion of the Colorado Plateau and the western edge of the Great Plains...
, the United States, were tested at the Lurgi's pilot plant in Frankfurt
Frankfurt
Frankfurt am Main , commonly known simply as Frankfurt, is the largest city in the German state of Hesse and the fifth-largest city in Germany, with a 2010 population of 688,249. The urban area had an estimated population of 2,300,000 in 2010...
. In the United States, the technology was promoted in cooperation with Dravo Corporation
Dravo Corporation
Dravo Corporation was a shipbuilding company with shipyards in Pittsburgh, Pennsylvania and Wilmington, Delaware. It was founded by Frank and Ralph Dravo in Pittsburgh during the 1890s.-Facilities:...
. In 1970s, the technology was licensed to the Rio Blanco Shale Oil Project for construction of a modular retort in combination with the modified in situ process. However, this plan was terminated.
In 1980, the Natural Resources Authority of Jordan commissioned from the Klöckner
Klöckner
Klöckner & Co. is a German metal handler headquartered in Duisburg. Europe's largest independent distributor of steel, it is a leading supplier to the European and North American markets....
-Lurgi
Lurgi AG
Lurgi GmbH is a German engineering, construction and chemical process licensing company. The head office is located in Frankfurt am Main. Lurgi GmbH has been part of Air Liquide S. A. since 2007.- History :...
consortium a pre-feasibility study of construction of an oil shale retorting complex in Jordan
Jordan
Jordan , officially the Hashemite Kingdom of Jordan , Al-Mamlaka al-Urduniyya al-Hashemiyya) is a kingdom on the East Bank of the River Jordan. The country borders Saudi Arabia to the east and south-east, Iraq to the north-east, Syria to the north and the West Bank and Israel to the west, sharing...
using Lurgi-Ruhrgas process. However, although the study found the technology feasible, it was never implemented.
Technology
The Lurgi–Ruhrgas process is a hot recycled solids technology, which processes fine particles of coal or oil shale in size of 0.25 to 0.5 in (6.4 to 12.7 mm). As a heat carrier, it uses spent char or spent oil shale (oil shale ash), mixed with sand or other more durable materials. In this process, crushed coal or oil shale is fed into the top of the retort. In retort, coal or oil shale is mixed with the 550 °C (1,022 °F) heated char or spent oil shale particles in the mechanical mixer (screw conveyorConveyor belt
A conveyor belt consists of two or more pulleys, with a continuous loop of material - the conveyor belt - that rotates about them. One or both of the pulleys are powered, moving the belt and the material on the belt forward. The powered pulley is called the drive pulley while the unpowered pulley...
). The heat is transferred from the heated char or spent oil shale to the coal or raw oil shale causing pyrolysis. As a result, oil shale decomposes to shale oil vapors, oil shale gas
Oil shale gas
Oil shale gas is a synthetic gas mixture produced by oil shale pyrolysis. Although often referred to as shale gas, it differs from the natural gas produced from shale, which is also known as shale gas.-Process:...
and spent oil shale. The oil vapor and product gases passes through a hot cyclone for cleaning before sending to the condenser
Condenser (heat transfer)
In systems involving heat transfer, a condenser is a device or unit used to condense a substance from its gaseous to its liquid state, typically by cooling it. In so doing, the latent heat is given up by the substance, and will transfer to the condenser coolant...
. In condenser, shale oil is separated from product gases.
The spent oil shale, still including residual carbon (char
Char
Char is the solid material that remains after light gases and tar coal tar have been driven out or released from a carbonaceous material during the initial stage of combustion, which is known as carbonization, charring, devolatilization or pyrolysis.Further stages of efficient combustion are...
), is burnt at a lift pipe combustor
Combustor
A combustor is a component or area of a gas turbine, ramjet, or scramjet engine where combustion takes place. It is also known as a burner, combustion chamber or flame holder. In a gas turbine engine, the combustor or combustion chamber is fed high pressure air by the compression system. The...
to heat the process. If necessary, additional fuel oil is used for combustion. During the combustion process, heated solid particles in the pipe are moved to the surge bin by pre-heated air that is introduced from the bottom of the pipe. At the surge bin, solids and gases are separated, and solid particles are transferred to the mixer unit to conduct a pyrolysis of the raw oil shale.
One of the disadvantages of this technology is the fact that produced shale oil vapors are mixed with shale ash causing impurities in shale oil. Ensuring the quality of produced shale oil is complicated as compared with other mineral dusts the shale ash is more difficult to collect.
See also
- Galoter processGaloter processThe Galoter process is a shale oil extraction technology for a production of shale oil, a type of synthetic crude oil. In this process, the oil shale is decomposed into shale oil, oil shale gas, and spent residue...
- Alberta Taciuk processAlberta Taciuk ProcessThe Alberta Taciuk process is an above-ground dry thermal retorting technology for extracting oil from oil sands, oil shale and other organics-bearing materials, including oil contaminated soils, sludges and wastes...
- Petrosix processPetrosixPetrosix is currently the world’s largest surface oil shale pyrolysis retort with an diameter vertical shaft kiln, operational since 1992. It is located in São Mateus do Sul, Brazil, and it is owned and operated by the Brazil energy company Petrobras. Petrosix means also the Petrosix process, an...
- Kiviter processKiviter process-History:The Kiviter process is based on the earlier vertical retort technology . This technology underwent a long process of development...
- TOSCO II processTOSCO II processThe TOSCO II process is an above ground retorting technology for shale oil extraction, which uses fine particles of oil shale that are heated in a rotating kiln. The particularity of this process is that it use hot ceramic balls for the heat transfer between the retort and a heater...
- Fushun processFushun processThe Fushun process is an above-ground retorting technology for shale oil extraction. It is named after the main production site of Fushun, Liaoning province in northeastern China.-History:...
- Paraho processParaho processThe Paraho process is an above ground retorting technology for shale oil extraction. The name "Paraho" is delivered from the words "para homem", which means in Portuguese "for mankind".-History:...
- KENTORT II
- Union processUnion processThe Union process is an above ground shale oil extraction technology for production of shale oil, a type of synthetic crude oil. The process uses a vertical retort where heating causes decomposition of oil shale into shale oil, oil shale gas and spent residue...