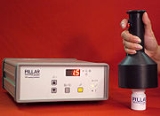
Induction sealing
Encyclopedia
Induction sealing, otherwise known as cap sealing, is a non-contact method of heating a metallic disk to hermetically seal the top of plastic
and glass
containers. This sealing process takes place after the container has been filled and capped.
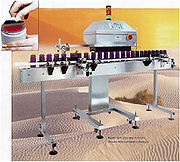
The closure is supplied to the bottler with foil liner already inserted. Although there are various liners to choose from, a typical induction liner is multi-layered. The top layer is a paper
pulp that is generally spot-glued to the cap. The next layer is wax that is used to bond a layer of aluminum foil to the pulp. The bottom layer is a polymer film laminated to the foil. After the cap or closure is applied, the container passes under an induction coil
, which emits an oscillating electromagnetic field
. As the container passes under the induction coil (sealing head) the conductive aluminum foil liner begins to heat. The heat melts the wax, which is absorbed into the pulp backing and releases the foil from the cap. The polymer film also heats and flows onto the lip of the container. When cooled, the polymer creates a bond with the container resulting in a hermetically sealed product. Neither the container nor its contents are affected, and this all happens in a matter of seconds.
It is possible to overheat the foil causing damage to the seal layer and to any protective barriers. This could result in faulty seals, even weeks after the initial sealing process, so proper sizing of the induction sealing is vital to determine the exact system necessary to run a particular product.
Sealing can be done with either a hand held unit or on a conveyor system.
A more recent development (which suits a small number of applications better) allows for induction sealing to be used to apply a foil seal to a container without the need for a closure. In this case, foil is supplied pre-cut or in a reel. Where supplied in a reel, it is die cut and transferred onto the container neck. When the foil is in place, it is pressed down by the seal head, the induction cycle is activated and the seal is bonded to the container. This process is known as direct application or sometimes "capless" induction sealing.
There are a variety of reasons companies choose to use induction sealing:
Induction sealing systems meet or exceed these government regulations. As stated in section 6 of Packaging Systems:
Some shipping companies require liquid chemical products to be sealed prior to shipping to prevent hazardous chemicals from spilling on other shipments.
of certain products.
High speed power analysis techniques (Voltage and Current measurement in near real time) can be used to intercept power delivery from mains to generator or generator to head in order to calculate energy delivered to the foil and the statistical profile of that process. As the thermal capacity of the foil is typically static, such information as true power, apparent power and power factor may be used to predict foil heating with good relevance to final weld parameters and in a dynamic manner.
Many other derivative parameters may be calculated for each weld, yielding confidence in a production environment that is notably more difficult to achieve in conduction transfer systems, where analysis, if present is generally post-weld as relatively large thermal mass of heating and conduction elements combined impair rapid temperature change. Inductive heating with quantitative feedback such as that provided by power analysis techniques further allows for the possibility of dynamic adjustments in energy delivery profile to the target. This opens the possibility of feed-forward systems where the induction generator properties are adjusted in near real-time as the heating process proceeds, allowing for a specific heating profile track and subsequent compliance feedback - something that is not generally practical for conduction heating processes.
Unlike conduction sealing systems, induction sealing systems require very little power resources, delivers instant startup time, and its sealing head can conform to “out of specification” containers when sealing.
Induction sealing also offers advantages when sealing to glass: Using a conduction sealer to seal a simple foil structure to glass gives no tolerance or compressibility to allow for any irregularity in the glass surface finish. With an induction sealer, the contact face can be of a compressible material, ensuring a perfect bond each time
Plastic
A plastic material is any of a wide range of synthetic or semi-synthetic organic solids used in the manufacture of industrial products. Plastics are typically polymers of high molecular mass, and may contain other substances to improve performance and/or reduce production costs...
and glass
Glass
Glass is an amorphous solid material. Glasses are typically brittle and optically transparent.The most familiar type of glass, used for centuries in windows and drinking vessels, is soda-lime glass, composed of about 75% silica plus Na2O, CaO, and several minor additives...
containers. This sealing process takes place after the container has been filled and capped.

How it works
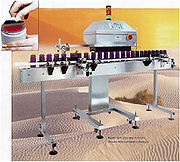
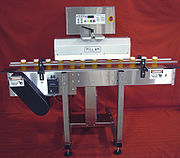
Paper
Paper is a thin material mainly used for writing upon, printing upon, drawing or for packaging. It is produced by pressing together moist fibers, typically cellulose pulp derived from wood, rags or grasses, and drying them into flexible sheets....
pulp that is generally spot-glued to the cap. The next layer is wax that is used to bond a layer of aluminum foil to the pulp. The bottom layer is a polymer film laminated to the foil. After the cap or closure is applied, the container passes under an induction coil
Induction coil
An induction coil or "spark coil" is a type of disruptive discharge coil. It is a type of electrical transformer used to produce high-voltage pulses from a low-voltage direct current supply...
, which emits an oscillating electromagnetic field
Electromagnetic field
An electromagnetic field is a physical field produced by moving electrically charged objects. It affects the behavior of charged objects in the vicinity of the field. The electromagnetic field extends indefinitely throughout space and describes the electromagnetic interaction...
. As the container passes under the induction coil (sealing head) the conductive aluminum foil liner begins to heat. The heat melts the wax, which is absorbed into the pulp backing and releases the foil from the cap. The polymer film also heats and flows onto the lip of the container. When cooled, the polymer creates a bond with the container resulting in a hermetically sealed product. Neither the container nor its contents are affected, and this all happens in a matter of seconds.
It is possible to overheat the foil causing damage to the seal layer and to any protective barriers. This could result in faulty seals, even weeks after the initial sealing process, so proper sizing of the induction sealing is vital to determine the exact system necessary to run a particular product.
Sealing can be done with either a hand held unit or on a conveyor system.
A more recent development (which suits a small number of applications better) allows for induction sealing to be used to apply a foil seal to a container without the need for a closure. In this case, foil is supplied pre-cut or in a reel. Where supplied in a reel, it is die cut and transferred onto the container neck. When the foil is in place, it is pressed down by the seal head, the induction cycle is activated and the seal is bonded to the container. This process is known as direct application or sometimes "capless" induction sealing.
Reasons that induction sealing may be useful
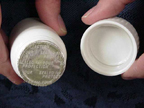
- Tamper evidenceTamper-evidentTamper-evident describes a device or process that makes unauthorized access to the protected object easily detected. Seals, markings or other techniques may be tamper indicating.-Tampering:...
- Leak prevention
- Freshness Retention
- Pilferage protection
- Sustainability
- Production Speed
Tamper evidence
With the U.S. Food and Drug Administration (FDA) regulations concerning tamper-resistant packaging, pharmaceutical packagers must find ways to comply as outlined in Sec. 450.500 Tamper-Resistant Packaging Requirements for Certain over-the-counter (OTC) Human Drug Products (CPG 7132a.17).Induction sealing systems meet or exceed these government regulations. As stated in section 6 of Packaging Systems:
“…6. CONTAINER MOUTH INNER SEALS. Paper, thermal plastic, plastic film, foil, or a combination thereof, is sealed to the mouth of a container (e.g., bottle) under the cap. The seal must be torn or broken to open the container and remove the product. The seal cannot be removed and reapplied without leaving visible evidence of entry. Seals applied by heat induction to plastic containers appear to offer a higher degree of tamper-resistance than those that depend on an adhesive to create the bond…”
Leak prevention/protection
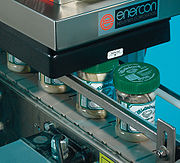
Freshness
Induction sealing keeps unwanted pollutants from seeping into food products, and may assist in extending shelf lifeShelf life
Shelf life is the length of time that food, drink, medicine, chemicals, and many other perishable items are given before they are considered unsuitable for sale, use, or consumption...
of certain products.
Pilferage protection
Induction-sealed containers help prevent the product from being broken into by leaving a noticeable residue from the liner itself. Pharmaceutical companies purchase liners that will purposely leave liner film/foil residue on bottles. Food companies that use induction seals do not want the liner residue as it could potentially interfere with the product itself upon dispensing. They, in turn, put a notice on the product that it has been induction-sealed for their protection; letting the consumer know there was a liner on the plastic bottle prior to purchase.Sustainability
In some applications, induction sealing can be considered to contribute towards sustainability goals by allowing lower bottle weights as the pack relies on the presence of an induction foil seal for its security, rather than a mechanically strong bottle neck and closure.Induction heating analysis
Some manufacturers have produced devices which can monitor the magnetic field strength present at the induction head (either directly or indirectly via such mechanisms as pick up coils), dynamically predicting the heating effect in the foil. Such devices provide quantifiable data post-weld in a production environment where uniformity - particularly in parameters such as foil peel-off strength, is important. Analysers may be portable or designed to work in conjunction with conveyor belt systems.High speed power analysis techniques (Voltage and Current measurement in near real time) can be used to intercept power delivery from mains to generator or generator to head in order to calculate energy delivered to the foil and the statistical profile of that process. As the thermal capacity of the foil is typically static, such information as true power, apparent power and power factor may be used to predict foil heating with good relevance to final weld parameters and in a dynamic manner.
Many other derivative parameters may be calculated for each weld, yielding confidence in a production environment that is notably more difficult to achieve in conduction transfer systems, where analysis, if present is generally post-weld as relatively large thermal mass of heating and conduction elements combined impair rapid temperature change. Inductive heating with quantitative feedback such as that provided by power analysis techniques further allows for the possibility of dynamic adjustments in energy delivery profile to the target. This opens the possibility of feed-forward systems where the induction generator properties are adjusted in near real-time as the heating process proceeds, allowing for a specific heating profile track and subsequent compliance feedback - something that is not generally practical for conduction heating processes.
Benefits of induction vs. conduction sealing
Conduction sealing requires a hard metal plate to make perfect contact with the container being sealed. Conduction sealing systems delay production time because of required system warm-up time. They also have complex temperature sensors and heaters.Unlike conduction sealing systems, induction sealing systems require very little power resources, delivers instant startup time, and its sealing head can conform to “out of specification” containers when sealing.
Induction sealing also offers advantages when sealing to glass: Using a conduction sealer to seal a simple foil structure to glass gives no tolerance or compressibility to allow for any irregularity in the glass surface finish. With an induction sealer, the contact face can be of a compressible material, ensuring a perfect bond each time
Variety of products that use induction sealing
- Pharmaceutical
- Nutraceutical
- FoodFoodFood is any substance consumed to provide nutritional support for the body. It is usually of plant or animal origin, and contains essential nutrients, such as carbohydrates, fats, proteins, vitamins, or minerals...
- DairyDairyA dairy is a business enterprise established for the harvesting of animal milk—mostly from cows or goats, but also from buffalo, sheep, horses or camels —for human consumption. A dairy is typically located on a dedicated dairy farm or section of a multi-purpose farm that is concerned...
- Beverage
- CosmeticsCosmeticsCosmetics are substances used to enhance the appearance or odor of the human body. Cosmetics include skin-care creams, lotions, powders, perfumes, lipsticks, fingernail and toe nail polish, eye and facial makeup, towelettes, permanent waves, colored contact lenses, hair colors, hair sprays and...
, health & beauty - Automotive petroleumPetroleumPetroleum or crude oil is a naturally occurring, flammable liquid consisting of a complex mixture of hydrocarbons of various molecular weights and other liquid organic compounds, that are found in geologic formations beneath the Earth's surface. Petroleum is recovered mostly through oil drilling...
products - Chemical
- Agricultural and ag chem.
- Animal care and medicines
- Sporting goods supplies
- Children’s toys (clays, bubbles, etc.)
- Pastes
- PaintPaintPaint is any liquid, liquefiable, or mastic composition which after application to a substrate in a thin layer is converted to an opaque solid film. One may also consider the digital mimicry thereof...
s - Home remodeling products
- Musical instrument supplies (cleaners, resins, lubricants, polishes)
- Dental
- Personal pleasure products
- HuntingHuntingHunting is the practice of pursuing any living thing, usually wildlife, for food, recreation, or trade. In present-day use, the term refers to lawful hunting, as distinguished from poaching, which is the killing, trapping or capture of the hunted species contrary to applicable law...
/ fishingFishingFishing is the activity of trying to catch wild fish. Fish are normally caught in the wild. Techniques for catching fish include hand gathering, spearing, netting, angling and trapping....
aids - ComputerComputerA computer is a programmable machine designed to sequentially and automatically carry out a sequence of arithmetic or logical operations. The particular sequence of operations can be changed readily, allowing the computer to solve more than one kind of problem...
aids/ inkInkInk is a liquid or paste that contains pigments and/or dyes and is used to color a surface to produce an image, text, or design. Ink is used for drawing and/or writing with a pen, brush, or quill...
s - Laundry detergentLaundry detergentLaundry detergent, or washing powder, is a substance that is a type of detergent that is added for cleaning laundry. In common usage, "detergent" refers to mixtures of chemical compounds including alkylbenzenesulfonates, which are similar to soap but are less affected by "hard water." In most...
/products - Manufacturing shop supplies
- School supply products
- Inks, dyes , carbon products….
- condoms
History
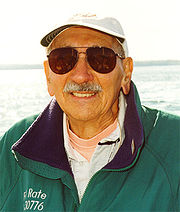
- 1957-1958 - Original concept and method for Induction Sealing is conceived and proven by Jack Palmer (a process engineer at that time for the FR Corporation - Bronx, NY) as a means of solving liquid leakage from polyethylene bottles during shipment
- 1960 - U.S. Patent (# 2,937,481) is awarded to Jack Palmer, in which his concept and process of Induction Sealing is made public
- Mid-1960s - Induction sealing is used worldwide
- 1973 – First solid state cap sealer introduced
- 1982 – Chicago Tylenol murders1982 Chicago Tylenol murdersThe Chicago Tylenol murders occurred when seven people died after taking pain-relief medicine capsules that had been poisoned. The poisonings, code-named TYMURS by the Federal Bureau of Investigation, took place in late 1982 in the Chicago area of the United States.These poisonings involved...
- 1983 – First transistorTransistorA transistor is a semiconductor device used to amplify and switch electronic signals and power. It is composed of a semiconductor material with at least three terminals for connection to an external circuit. A voltage or current applied to one pair of the transistor's terminals changes the current...
ized air-cooled power supply for induction cap sealing - 1985 – Universal coil technology debuted
- 1992 – Water-cooled, IGBT-based sealer introduced
- 1997 – Waterless cap sealers introduced (half the size and relatively maintenance free)
- 2004 – 6 kW system introduced