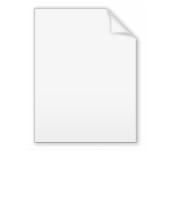
I-joist
Encyclopedia
An engineered wood joist
, more commonly known as an I-joist, is a product designed to eliminate many of the problems that occur with using conventional wood joists. Invented in 1969, the I-joist is a man made engineered wood product which has incredible strength in relation to its size and weight. The biggest notable difference, other than their look, compared to dimensional lumber is that the I-joist is designed to carry heavy loads over long distances while using less lumber than a dimensional solid wood joist of a size necessary to do the same task. As of 2005, approximately 50% of all wood light framed floors were framed using I-joists.
. The web is sandwiched between a top and bottom flange, creating the “I” shape. The flange can be made from laminated veneer
lumber or solid wood finger-jointed together for ultimate strength. It is then grooved on one side to receive the web. The web is typically made from plywood
, laminated veneer lumber, or oriented strand board
. After cutting the webs and flanges to the specified widths and lengths, they are assembled with water-resistant glue
by pressing the web into the top and bottom flange. After initial assembly, the I-joist is then end-trimmed and allowed to cure in an oven, or at room temperature to approximately equilibrium moisture content. The sizes manufactured vary on the I-joists intended load and span. Their depths can range from 9 ¼ inches to 24 inches (145mm - 600mm) and are available up to 80 feet long, although 12-13m is more common. The intended use for an I-joist is for floor joists, wall studs and roof rafters in both residential and commercial construction.
Although the I-joist may seem like a perfect choice as a building material, if it is installed incorrectly or altered the I-joist can fail. By reading the manufacturer’s instructions with the I-joist, most mistakes can be caught in advance. The most common mistake typically is with subcontractors misplacing or improperly sizing holes in the web. Doing so can greatly compromise the strength of the joist and the ones around it potentially leading to structural failure in those joists.
Some of common mistakes made with installing I-joists are: cutting or chiseling flange in any way, improperly sized joists hangers, improper nailing into rim joist and joist hangers, and wrong sized nails. Another situation to look out for is matching the rim joist depth to the I-joist size. Improper matching can lead to too much strain on the I-joist. To solve the problem the rim joist can be made from rips of ¾ inch plywood, or engineered rim joist matching the I-joist in depth.
A similar situation occurs where the I-joist crosses a main beam. Installing squash blocks (2x4 materials 1/16 inch higher than the I-joist) alongside the I-joists helps take the load of the above levels off the I-joist themselves and onto the main beam. Problems that arise while installing the sheathing are missed nails and having the glue set too fast. Both can lead to an uneven or squeaky floor.
Joist
A joist, in architecture and engineering, is one of the horizontal supporting members that run from wall to wall, wall to beam, or beam to beam to support a ceiling, roof, or floor. It may be made of wood, steel, or concrete. Typically, a beam is bigger than, and is thus distinguished from, a joist...
, more commonly known as an I-joist, is a product designed to eliminate many of the problems that occur with using conventional wood joists. Invented in 1969, the I-joist is a man made engineered wood product which has incredible strength in relation to its size and weight. The biggest notable difference, other than their look, compared to dimensional lumber is that the I-joist is designed to carry heavy loads over long distances while using less lumber than a dimensional solid wood joist of a size necessary to do the same task. As of 2005, approximately 50% of all wood light framed floors were framed using I-joists.
Design and manufacture
An I-joist comprises two main parts, the web and flangeFlange
A flange is an external or internal ridge, or rim , for strength, as the flange of an iron beam such as an I-beam or a T-beam; or for attachment to another object, as the flange on the end of a pipe, steam cylinder, etc., or on the lens mount of a camera; or for a flange of a rail car or tram wheel...
. The web is sandwiched between a top and bottom flange, creating the “I” shape. The flange can be made from laminated veneer
Wood veneer
In woodworking, veneer refers to thin slices of wood, usually thinner than 3 mm , that are typically glued onto core panels to produce flat panels such as doors, tops and panels for cabinets, parquet floors and parts of furniture. They are also used in marquetry...
lumber or solid wood finger-jointed together for ultimate strength. It is then grooved on one side to receive the web. The web is typically made from plywood
Plywood
Plywood is a type of manufactured timber made from thin sheets of wood veneer. It is one of the most widely used wood products. It is flexible, inexpensive, workable, re-usable, and can usually be locally manufactured...
, laminated veneer lumber, or oriented strand board
Oriented strand board
Oriented strand board, also known as OSB and SmartPly , is an engineered wood product formed by layering strands of wood in specific orientations. In appearance, it may have a rough and variegated surface with the individual strips Oriented strand board, also known as OSB (UK) and SmartPly (UK &...
. After cutting the webs and flanges to the specified widths and lengths, they are assembled with water-resistant glue
Glue
This is a list of various types of glue. Historically, the term "glue" only referred to protein colloids prepared from animal flesh. The meaning has been extended to refer to any fluid adhesive....
by pressing the web into the top and bottom flange. After initial assembly, the I-joist is then end-trimmed and allowed to cure in an oven, or at room temperature to approximately equilibrium moisture content. The sizes manufactured vary on the I-joists intended load and span. Their depths can range from 9 ¼ inches to 24 inches (145mm - 600mm) and are available up to 80 feet long, although 12-13m is more common. The intended use for an I-joist is for floor joists, wall studs and roof rafters in both residential and commercial construction.
Installation
I-joists were designed to help eliminate typical problems that come with using solid lumber as joists. The advantage of I-joists is they will not bow, crown, twist, cup, check, or split as would a dimensional piece of lumber. Also, I-joists are designed to help eliminate squeaky floors by being more dimensionally sound and featuring little to no shrinking.Although the I-joist may seem like a perfect choice as a building material, if it is installed incorrectly or altered the I-joist can fail. By reading the manufacturer’s instructions with the I-joist, most mistakes can be caught in advance. The most common mistake typically is with subcontractors misplacing or improperly sizing holes in the web. Doing so can greatly compromise the strength of the joist and the ones around it potentially leading to structural failure in those joists.
Some of common mistakes made with installing I-joists are: cutting or chiseling flange in any way, improperly sized joists hangers, improper nailing into rim joist and joist hangers, and wrong sized nails. Another situation to look out for is matching the rim joist depth to the I-joist size. Improper matching can lead to too much strain on the I-joist. To solve the problem the rim joist can be made from rips of ¾ inch plywood, or engineered rim joist matching the I-joist in depth.
A similar situation occurs where the I-joist crosses a main beam. Installing squash blocks (2x4 materials 1/16 inch higher than the I-joist) alongside the I-joists helps take the load of the above levels off the I-joist themselves and onto the main beam. Problems that arise while installing the sheathing are missed nails and having the glue set too fast. Both can lead to an uneven or squeaky floor.