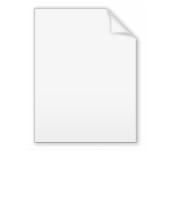
Hot isostatic pressing
Encyclopedia
Hot isostatic pressing (HIP) is a manufacturing
process used to reduce the porosity of metal
s and influence the density
of many ceramic
materials. This improves the material's mechanical properties and workability.
The HIP process subjects a component to both elevated temperature and isostatic gas pressure in a high pressure containment vessel. The pressurizing gas most widely used is argon
. An inert
gas is used, so that the material does not chemically react. The chamber is heated, causing the pressure
inside the vessel to increase. Many systems use associated gas pumping to achieve the necessary pressure level. Pressure is applied to the material from all directions (hence the term "isostatic").
For processing castings, the inert gas is applied between 7350 psi (50.7 MPa) and 45000 psi (310.3 MPa), with 15000 psi (103.4 MPa) being most common. Process soak temperatures range from 900 °F (482.2 °C) for aluminum castings to 2400 °F (1,315.6 °C) for nickel
-based superalloy
s. When castings are treated with HIP, the simultaneous application of heat and pressure eliminates internal voids and microporosity through a combination of plastic deformation, creep
, and diffusion bonding; this process improves fatigue resistance of component. Primary applications are the reduction of microshrinkage, the consolidation of powder metals, ceramic composites and metal cladding
. Hot isostatic pressing is also used as part of a sintering
(powder metallurgy
) process and for fabrication of metal matrix composite
s.
Manufacturing
Manufacturing is the use of machines, tools and labor to produce goods for use or sale. The term may refer to a range of human activity, from handicraft to high tech, but is most commonly applied to industrial production, in which raw materials are transformed into finished goods on a large scale...
process used to reduce the porosity of metal
Metal
A metal , is an element, compound, or alloy that is a good conductor of both electricity and heat. Metals are usually malleable and shiny, that is they reflect most of incident light...
s and influence the density
Density
The mass density or density of a material is defined as its mass per unit volume. The symbol most often used for density is ρ . In some cases , density is also defined as its weight per unit volume; although, this quantity is more properly called specific weight...
of many ceramic
Ceramic
A ceramic is an inorganic, nonmetallic solid prepared by the action of heat and subsequent cooling. Ceramic materials may have a crystalline or partly crystalline structure, or may be amorphous...
materials. This improves the material's mechanical properties and workability.
The HIP process subjects a component to both elevated temperature and isostatic gas pressure in a high pressure containment vessel. The pressurizing gas most widely used is argon
Argon
Argon is a chemical element represented by the symbol Ar. Argon has atomic number 18 and is the third element in group 18 of the periodic table . Argon is the third most common gas in the Earth's atmosphere, at 0.93%, making it more common than carbon dioxide...
. An inert
Inert
-Chemistry:In chemistry, the term inert is used to describe a substance that is not chemically reactive.The noble gases were previously known as inert gases because of their perceived lack of participation in any chemical reactions...
gas is used, so that the material does not chemically react. The chamber is heated, causing the pressure
Pressure
Pressure is the force per unit area applied in a direction perpendicular to the surface of an object. Gauge pressure is the pressure relative to the local atmospheric or ambient pressure.- Definition :...
inside the vessel to increase. Many systems use associated gas pumping to achieve the necessary pressure level. Pressure is applied to the material from all directions (hence the term "isostatic").
For processing castings, the inert gas is applied between 7350 psi (50.7 MPa) and 45000 psi (310.3 MPa), with 15000 psi (103.4 MPa) being most common. Process soak temperatures range from 900 °F (482.2 °C) for aluminum castings to 2400 °F (1,315.6 °C) for nickel
Nickel
Nickel is a chemical element with the chemical symbol Ni and atomic number 28. It is a silvery-white lustrous metal with a slight golden tinge. Nickel belongs to the transition metals and is hard and ductile...
-based superalloy
Superalloy
A superalloy, or high-performance alloy, is an alloy that exhibits excellent mechanical strength and creep resistance at high temperatures, good surface stability, and corrosion and oxidation resistance. Superalloys typically have a matrix with an austenitic face-centered cubic crystal structure. ...
s. When castings are treated with HIP, the simultaneous application of heat and pressure eliminates internal voids and microporosity through a combination of plastic deformation, creep
Creep
Creep may refer to:* CREEP, the Committee for the Re-Election of the President, associated with the Watergate scandal of U.S. president Nixon's administration....
, and diffusion bonding; this process improves fatigue resistance of component. Primary applications are the reduction of microshrinkage, the consolidation of powder metals, ceramic composites and metal cladding
Cladding (metalworking)
Cladding is the bonding together of dissimilar metals. It is distinct from welding or gluing as a method to fasten the metals together. Cladding is often achieved by extruding two metals through a die as well as pressing or rolling sheets together under high pressure.The United States Mint uses...
. Hot isostatic pressing is also used as part of a sintering
Sintering
Sintering is a method used to create objects from powders. It is based on atomic diffusion. Diffusion occurs in any material above absolute zero, but it occurs much faster at higher temperatures. In most sintering processes, the powdered material is held in a mold and then heated to a temperature...
(powder metallurgy
Powder metallurgy
Powder metallurgy is the process of blending fine powdered materials, pressing them into a desired shape , and then heating the compressed material in a controlled atmosphere to bond the material . The powder metallurgy process generally consists of four basic steps: powder manufacture, powder...
) process and for fabrication of metal matrix composite
Metal matrix composite
A metal matrix composite is composite material with at least two constituent parts, one being a metal. The other material may be a different metal or another material, such as a ceramic or organic compound. When at least three materials are present, it is called a hybrid composite...
s.