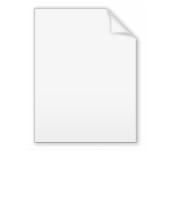
Hazop
Encyclopedia
A hazard and operability study (HAZOP) is a structured and systematic examination of a planned or existing process or operation in order to identify and evaluate problems that may represent risks to personnel or equipment, or prevent efficient
operation.
The HAZOP technique was initially developed to analyze chemical process systems, but has later been extended to other types of systems and also to complex operations and to software systems. A HAZOP is a qualitative technique based on guide-words and is
carried out by a multi-disciplinary team (HAZOP team) during a set of meetings.
, which is examined in small sections, such as individual items of equipment or pipes between them. For each of these a design Intention is specified. For example, in a chemical plant, a pipe may have the intention to transport 2.3 kg/s of 96% sulfuric acid at 20°C and a pressure of 2 bar from a pump to a heat exchanger
. The intention of the heat exchanger may be to heat 2.3 kg/s of 96% sulfuric acid from 20°C to 80 °C. The HAZOP team then determines what are the possible significant Deviations from each intention, feasible Causes and likely Consequences. It can then be decided whether existing, designed safeguards are sufficient, or whether additional actions are necessary to reduce risk to an acceptable level.
When HAZOP meetings were recorded by hand they were generally scheduled for three to four hours per day.
(Note that the last four guide words are applied to batch or sequential operations.) These are therefore combined e.g. NO FLOW, MORE TEMPERATURE, and if the combination is meaningful, it is a potential deviation. In this case LESS COMPOSITION would suggest less than 96% sulfuric acid, whereas OTHER THAN COMPOSITION would suggest something else such as oil.
The following table gives an overview of commonly used guide word - parameter pairs and common interpretations of them.
Once the causes and effects of any potential hazards have been established, the system being studied can then be modified to improve its safety. The modified design must then be subject to another HAZOP, to ensure that no new problems have been added.
In earlier publications it was suggested that the Study Leader could also be the Recorder but separate roles are now generally recommended. A minimum team size of 5 is recommended. In a large process there will be many HAZOP meetings and the team may change as specialists are brought in for different areas, and possibly different members of the design team, but the Study Leader and Recorder will usually be fixed. As many as 20 individuals may be involved but is recommended that no more than 8 are involved at any one time. Software is now available from several suppliers to aid the Study Leader and the Recorder.
, which was then a major British and international chemical company. The history has been described by Trevor Kletz
who was the company's safety advisor from 1968 to 1982, from which the following is abstracted.
In 1963 a team of 3 people met for 3 days a week for 4 months to study the design of a new Phenol
plant. They started with a technique called critical examination which asked for alternatives, but changed this to look for deviations. The method was further refined within the company, under the name operability studies, and became the third stage of its hazard analysis
procedure (the first two being done at the conceptual and specification stages) when the first detailed design was produced.
In 1974 a one-week safety course including this procedure was offered by the Institution of Chemical Engineers
(IChemE) at Teesside Polytechnic. Coming shortly after the Flixborough disaster
, the course was fully booked, as were ones in the next few years. In the same year the first paper in the open literature was also published. In 1977 the Chemical Industries Association
published a guide. Up to this time the term HAZOP had not been used in formal publications. The first to do this was Kletz in 1983, with what were essentially the course notes (revised and updated) from the IChemE courses. By this time, hazard and operability studies had become an expected part of chemical engineering
degree courses in the UK.
operation.
The HAZOP technique was initially developed to analyze chemical process systems, but has later been extended to other types of systems and also to complex operations and to software systems. A HAZOP is a qualitative technique based on guide-words and is
carried out by a multi-disciplinary team (HAZOP team) during a set of meetings.
Outline
The method applies to processes (existing or planned) for which design information is available. This commonly includes a process flow diagramProcess Flow diagram
A process flow diagram is a diagram commonly used in engineering to indicate the general flow of plant processes and equipment.The PFD displays the relationship between major equipment of a plant facility and does not show minor details such as piping details and designations...
, which is examined in small sections, such as individual items of equipment or pipes between them. For each of these a design Intention is specified. For example, in a chemical plant, a pipe may have the intention to transport 2.3 kg/s of 96% sulfuric acid at 20°C and a pressure of 2 bar from a pump to a heat exchanger
Heat exchanger
A heat exchanger is a piece of equipment built for efficient heat transfer from one medium to another. The media may be separated by a solid wall, so that they never mix, or they may be in direct contact...
. The intention of the heat exchanger may be to heat 2.3 kg/s of 96% sulfuric acid from 20°C to 80 °C. The HAZOP team then determines what are the possible significant Deviations from each intention, feasible Causes and likely Consequences. It can then be decided whether existing, designed safeguards are sufficient, or whether additional actions are necessary to reduce risk to an acceptable level.
When HAZOP meetings were recorded by hand they were generally scheduled for three to four hours per day.
Parameters and guide words
The key feature is to select appropriate parameters which apply to the design intention. These are general words such as Flow, Temperature, Pressure, Composition. In the above example, it can be seen that variations in these parameters could constitute Deviations from the design Intention. In order to identify Deviations, the Study Leader applies (systematically, in order) a set of Guide Words to each parameter for each section of the process. The current standard Guide Words are as follows:Guide Word | Meaning |
---|---|
NO OR NOT | Complete negation of the design intent |
MORE | Quantitative increase |
LESS | Quantitative decrease |
AS WELL AS | Qualitative modification/increase |
PART OF | Qualitative modification/decrease |
REVERSE | Logical opposite of the design intent |
OTHER THAN | Complete substitution |
EARLY | Relative to the clock time |
LATE | Relative to the clock time |
BEFORE | Relating to order or sequence |
AFTER | Relating to order or sequence |
(Note that the last four guide words are applied to batch or sequential operations.) These are therefore combined e.g. NO FLOW, MORE TEMPERATURE, and if the combination is meaningful, it is a potential deviation. In this case LESS COMPOSITION would suggest less than 96% sulfuric acid, whereas OTHER THAN COMPOSITION would suggest something else such as oil.
The following table gives an overview of commonly used guide word - parameter pairs and common interpretations of them.
Parameter / Guide Word | More | Less | None | Reverse | As well as | Part of | Other than |
---|---|---|---|---|---|---|---|
Flow | high flow | low flow | no flow | reverse flow | deviating concentration | contamination | deviating material |
Pressure | high pressure | low pressure | vacuum | delta-p | explosion | ||
Temperature | high temperature | low temperature | |||||
Level | high level | low level | no level | different level | |||
Time | too long / too late | too short / too soon | sequence step skipped | backwards | missing actions | extra actions | wrong time |
Agitation | fast mixing | slow mixing | no mixing | ||||
Reaction | fast reaction / runaway | slow reaction | no reaction | unwanted reaction | |||
Start-up / Shut-down | too fast | too slow | actions missed | wrong recipe | |||
Draining / Venting | too long | too short | none | deviating pressure | wrong timing | ||
Inertising | high pressure | low pressure | none | contamination | wrong material | ||
Utility failure (instrument air, power) | failure | ||||||
DCS failure | failure | ||||||
Maintenance | none | ||||||
Vibrations | too low | too high | none | wrong frequency |
Once the causes and effects of any potential hazards have been established, the system being studied can then be modified to improve its safety. The modified design must then be subject to another HAZOP, to ensure that no new problems have been added.
Team
HAZOP is normally carried out by a team of people, with roles as follows (with alternative names from other sources):Name | Alternative | Role |
---|---|---|
Study leader | Chairman | someone experienced in HAZOP but not directly involved in the design, to ensure that the method is followed carefully |
Recorder | Secretary or scribe | to ensure that problems are documented and recommendations passed on |
Designer | (or representative of the team which has designed the process) | To explain any design details or provide further information |
User | (or representative of those who will use it) | To consider it in use and question its operability, and the effect of deviations |
Specialist | (or specialists) | someone with relevant technical knowledge |
Maintainer | (if appropriate) | someone concerned with maintenance of the process. |
In earlier publications it was suggested that the Study Leader could also be the Recorder but separate roles are now generally recommended. A minimum team size of 5 is recommended. In a large process there will be many HAZOP meetings and the team may change as specialists are brought in for different areas, and possibly different members of the design team, but the Study Leader and Recorder will usually be fixed. As many as 20 individuals may be involved but is recommended that no more than 8 are involved at any one time. Software is now available from several suppliers to aid the Study Leader and the Recorder.
History
The technique originated in the Heavy Organic Chemicals Division of ICIImperial Chemical Industries
Imperial Chemical Industries was a British chemical company, taken over by AkzoNobel, a Dutch conglomerate, one of the largest chemical producers in the world. In its heyday, ICI was the largest manufacturing company in the British Empire, and commonly regarded as a "bellwether of the British...
, which was then a major British and international chemical company. The history has been described by Trevor Kletz
Trevor Kletz
Trevor Kletz OBE is a prolific British author on the topic of chemical engineering safety. He is credited with introducing the concept of inherent safety, and was a major promoter of Hazop.-Early life and education:...
who was the company's safety advisor from 1968 to 1982, from which the following is abstracted.
In 1963 a team of 3 people met for 3 days a week for 4 months to study the design of a new Phenol
Phenol
Phenol, also known as carbolic acid, phenic acid, is an organic compound with the chemical formula C6H5OH. It is a white crystalline solid. The molecule consists of a phenyl , bonded to a hydroxyl group. It is produced on a large scale as a precursor to many materials and useful compounds...
plant. They started with a technique called critical examination which asked for alternatives, but changed this to look for deviations. The method was further refined within the company, under the name operability studies, and became the third stage of its hazard analysis
Hazard analysis
A hazard analysis is used as the first step in a process used to assess risk. The result of a hazard analysis is the identification of risks. Preliminary risk levels can be provided in the hazard analysis. The validation, more precise prediction and acceptance of risk is determined in the Risk...
procedure (the first two being done at the conceptual and specification stages) when the first detailed design was produced.
In 1974 a one-week safety course including this procedure was offered by the Institution of Chemical Engineers
Institution of Chemical Engineers
The Institution of Chemical Engineers is a global professional engineering institution with over 33,000 members in over 120 countries worldwide, founded in 1922, and awarded a Royal Charter in 1957.-Structure:...
(IChemE) at Teesside Polytechnic. Coming shortly after the Flixborough disaster
Flixborough disaster
The Flixborough disaster was an explosion at a chemical plant close to the village of Flixborough, England, on 1 June 1974. It killed 28 people and seriously injured 36.-Background:...
, the course was fully booked, as were ones in the next few years. In the same year the first paper in the open literature was also published. In 1977 the Chemical Industries Association
Chemical Industries Association
The Chemical Industries Association is the largest trade association for the chemical and chemistry-using industries in the United Kingdom.-Function:...
published a guide. Up to this time the term HAZOP had not been used in formal publications. The first to do this was Kletz in 1983, with what were essentially the course notes (revised and updated) from the IChemE courses. By this time, hazard and operability studies had become an expected part of chemical engineering
Chemical engineering
Chemical engineering is the branch of engineering that deals with physical science , and life sciences with mathematics and economics, to the process of converting raw materials or chemicals into more useful or valuable forms...
degree courses in the UK.
Further reading
- Gould, J., (2000) Review of Hazard Identification Techniques, HSE
- Summary of HAZOP Explanation by the US Coastguard
- Hazard and Operability Studies Explanation by a software supplier
See also
- Hazard analysisHazard analysisA hazard analysis is used as the first step in a process used to assess risk. The result of a hazard analysis is the identification of risks. Preliminary risk levels can be provided in the hazard analysis. The validation, more precise prediction and acceptance of risk is determined in the Risk...
- Hazard Analysis and Critical Control PointsHazard Analysis and Critical Control PointsHazard analysis and critical control points, or HACCP , is a systematic preventive approach to food safety and pharmaceutical safety that addresses physical, chemical, and biological hazards as a means of prevention rather than finished product inspection...
- Process Safety ManagementProcess Safety ManagementProcess Safety Management is a regulation, promulgated by the U.S. Occupational Safety and Health Administration . A process is any activity or combination of activities including any use, storage, manufacturing, handling or the on-site movement of Highly Hazardous Chemicals as defined by OSHA...
- Risk assessmentRisk assessmentRisk assessment is a step in a risk management procedure. Risk assessment is the determination of quantitative or qualitative value of risk related to a concrete situation and a recognized threat...
- Safety engineeringSafety engineeringSafety engineering is an applied science strongly related to systems engineering / industrial engineering and the subset System Safety Engineering...
- HAZID