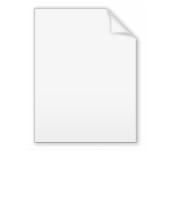
Electromagnetic forming
Encyclopedia
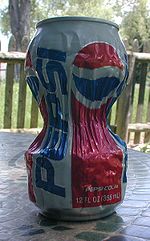
Copper
Copper is a chemical element with the symbol Cu and atomic number 29. It is a ductile metal with very high thermal and electrical conductivity. Pure copper is soft and malleable; an exposed surface has a reddish-orange tarnish...
and aluminium
Aluminium
Aluminium or aluminum is a silvery white member of the boron group of chemical elements. It has the symbol Al, and its atomic number is 13. It is not soluble in water under normal circumstances....
. The workpiece is reshaped by high intensity pulsed
Pulse (signal processing)
In signal processing, the term pulse has the following meanings:#A rapid, transient change in the amplitude of a signal from a baseline value to a higher or lower value, followed by a rapid return to the baseline value....
magnetic field
Magnetic field
A magnetic field is a mathematical description of the magnetic influence of electric currents and magnetic materials. The magnetic field at any given point is specified by both a direction and a magnitude ; as such it is a vector field.Technically, a magnetic field is a pseudo vector;...
s that induce a current in the workpiece and a corresponding repulsive magnetic field, rapidly repelling portions of the workpiece. The workpiece can be reshaped without any contact from a tool, although in some instances the piece may be pressed against a die or former. The technique is sometimes called high velocity forming or electromagnetic pulse technology.
Explanation
A rapidly changing magnetic field induces a circulating electrical currentElectric current
Electric current is a flow of electric charge through a medium.This charge is typically carried by moving electrons in a conductor such as wire...
within a nearby conductor through electromagnetic induction
Electromagnetic induction
Electromagnetic induction is the production of an electric current across a conductor moving through a magnetic field. It underlies the operation of generators, transformers, induction motors, electric motors, synchronous motors, and solenoids....
. The induced current creates a corresponding magnetic field around the conductor (see Pinch (plasma physics)
Pinch (plasma physics)
A pinch is the compression of an electrically conducting filament by magnetic forces. The conductor is usually a plasma, but could also be a solid or liquid metal...
). Because of Lenz's Law
Lenz's law
Lenz's law is a common way of understanding how electromagnetic circuits must always obey Newton's third law and The Law of Conservation of Energy...
, the magnetic fields created within the conductor and work coil strongly repel each other.
In practice the metal workpiece to be fabricated is placed in proximity to a heavily constructed coil of wire (called the work coil). A huge pulse of current is forced through the work coil by rapidly discharging a high voltage capacitor
Capacitor
A capacitor is a passive two-terminal electrical component used to store energy in an electric field. The forms of practical capacitors vary widely, but all contain at least two electrical conductors separated by a dielectric ; for example, one common construction consists of metal foils separated...
bank using an ignitron
Ignitron
An ignitron is a type of controlled rectifier dating from the 1930s. Invented by Joseph Slepian while employed by Westinghouse, Westinghouse was the original manufacturer and owned trademark rights to the name "Ignitron"....
or a spark gap
Spark gap
A spark gap consists of an arrangement of two conducting electrodes separated by a gap usually filled with a gas such as air, designed to allow an electric spark to pass between the conductors. When the voltage difference between the conductors exceeds the gap's breakdown voltage, a spark forms,...
(copper vapour thyratron) as a switch
Switch
In electronics, a switch is an electrical component that can break an electrical circuit, interrupting the current or diverting it from one conductor to another....
. This creates a rapidly oscillating, ultrastrong electromagnetic field
Electromagnetic field
An electromagnetic field is a physical field produced by moving electrically charged objects. It affects the behavior of charged objects in the vicinity of the field. The electromagnetic field extends indefinitely throughout space and describes the electromagnetic interaction...
around the work coil.
The high work coil current (typically tens or hundreds of thousands of amperes) creates ultrastrong magnetic forces that easily overcome the yield strength of the metal work piece, causing permanent deformation. The metal forming process occurs extremely quickly (typically tens of microsecond
Microsecond
A microsecond is an SI unit of time equal to one millionth of a second. Its symbol is µs.A microsecond is equal to 1000 nanoseconds or 1/1000 millisecond...
s) and, because of the large forces, portions of the workpiece undergo high acceleration
Acceleration
In physics, acceleration is the rate of change of velocity with time. In one dimension, acceleration is the rate at which something speeds up or slows down. However, since velocity is a vector, acceleration describes the rate of change of both the magnitude and the direction of velocity. ...
reaching velocities of up to 300 m/s.
Applications
The forming process is most often used to shrink or expand cylindrical tubing, but it can also form sheet metal by repelling the work piece onto a shaped dieDie (manufacturing)
A die is a specialized tool used in manufacturing industries to cut or shape material using a press. Like molds, dies are generally customized to the item they are used to create...
at a high velocity
Velocity
In physics, velocity is speed in a given direction. Speed describes only how fast an object is moving, whereas velocity gives both the speed and direction of the object's motion. To have a constant velocity, an object must have a constant speed and motion in a constant direction. Constant ...
. High-quality joints can be formed, either by electromagnetic pulse crimping with a mechanical interlock or by electromagnetic pulse welding
Magnetic pulse welding
Magnetic pulse welding is a welding process that uses magnetic forces to drive two workpieces together and weld them together. The welding mechanism is most similar to that in explosion welding.-Process:...
with a true metallurgical weld. Since the forming operation involves high acceleration and deceleration, mass of the work piece plays a critical role during the forming process. The process works best with good electrical conductor
Electrical conductor
In physics and electrical engineering, a conductor is a material which contains movable electric charges. In metallic conductors such as copper or aluminum, the movable charged particles are electrons...
s such as copper or aluminum, but it can be adapted to work with poorer conductors such as steel
Steel
Steel is an alloy that consists mostly of iron and has a carbon content between 0.2% and 2.1% by weight, depending on the grade. Carbon is the most common alloying material for iron, but various other alloying elements are used, such as manganese, chromium, vanadium, and tungsten...
.
Comparison with Mechanical Forming
Electromagnetic forming has a number of advantages and disadvantages compared to conventional mechanical forming techniques.Some of the advantages are;
- Improved formability (the amount of stretch available without tearing)
- Wrinkling can be greatly suppressed
- Forming can be combined with joining and assembling with dissimilar components including glass, plastic, composites and other metals.
- Close tolerances are possible as springback can be significantly reduced.
- Single sided dies are sufficient which can reduce tooling costs
- Lubricants are reduced or are unnecessary, so forming can be used in clean room conditions
- Mechanical contact with the workpiece is not required, this avoids surface contamination and tooling marks. As a result, a surface finish can be applied to the workpiece before forming.
The principle disadvantages are;
- Non conductive materials cannot be formed directly, but can be formed using a conductive drive plate
- The high voltages and currents involved require careful safety considerations
- Large sheet metal components cannot readily be formed, due to current limitations on the design of very large coils