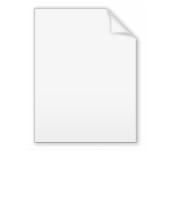
Direct Digital Control
Encyclopedia
Direct digital control (DDC) is the automated control of a condition or process by a digital device (computer).
A very early example of a DDC system meeting the above requirements was completed by the Australian business Midac
in 1981-1982 using R-Tec Australian designed hardware. The system installed at the University of Melbourne
used a serial communications network, connecting campus buildings back to a control room "front end" system in the basement of the Old Geology building. Each remote or Satellite Intelligence Unit (SIU) ran 2 Z80 microprocessors whilst the front end ran 11 in a Parallel Processing
configuration with paged common memory. The z80 microprocessors shared the load by passing tasks to each other via the common memory and the communications network. This was possibly the first successful implementation of a distributed processing direct digital control system.
s, controllers, logic, timers, trend logs, and alarms.
The unit controllers typically have analog and digital inputs, that allow measurement of the variable (temperature, humidity, or pressure) and analog
and digital
outputs for control of the medium (hot/cold water and/or steam). Digital inputs are typically (dry) contacts from a control device, and analog inputs are typically a voltage or current measurement from a variable (temperature, humidity, velocity, or pressure) sensing device. Digital outputs are typically relay contacts used to start and stop equipment, and analog outputs are typically voltage or current signals to control the movement of the medium (air/water/steam) control devices. Usually abbreviated as "DDC".
Most of the integration platforms are either a PC or a network appliance. In many cases, the HMI
(human machine interface) or SCADA
(Supervisory Control And Data Acquisition) are part of it. Integration platform examples, to name only a few, are the Tridium Niagara AX, Johnson FX40,TAC Vista and the Unified Architecture i.e. OPC (Open Connectivity) server technology used when direct connectivity is not possible.
DDC is often used to control HVAC
(heating, ventilating, and air conditioning) devices such as valves via microprocessors using software to perform the control logic. Such systems receive analog and digital inputs from the sensors and devices installed in the HVAC system and, according to the control logic, provide analog or digital outputs to control the HVAC system devices.
These systems may be mated with a software package that graphically allows operators to monitor, control, alarm and diagnose building equipment remotely.
A very early example of a DDC system meeting the above requirements was completed by the Australian business Midac
Midac
MIDAC is an acronym created in 1981 by a Sydney-based business, Combined Resources Computing . It stands for Microprocessor Intelligent Data Acquisition and Control...
in 1981-1982 using R-Tec Australian designed hardware. The system installed at the University of Melbourne
University of Melbourne
The University of Melbourne is a public university located in Melbourne, Victoria. Founded in 1853, it is the second oldest university in Australia and the oldest in Victoria...
used a serial communications network, connecting campus buildings back to a control room "front end" system in the basement of the Old Geology building. Each remote or Satellite Intelligence Unit (SIU) ran 2 Z80 microprocessors whilst the front end ran 11 in a Parallel Processing
Parallel processing
Parallel processing is the ability to carry out multiple operations or tasks simultaneously. The term is used in the contexts of both human cognition, particularly in the ability of the brain to simultaneously process incoming stimuli, and in parallel computing by machines.-Parallel processing by...
configuration with paged common memory. The z80 microprocessors shared the load by passing tasks to each other via the common memory and the communications network. This was possibly the first successful implementation of a distributed processing direct digital control system.
Overview
Central controllers and most terminal unit controllers are programmable, meaning the direct digital control program code may be customized for the intended use. The program features include time schedules, setpointSetpoint
Setpoint is the target value that an automatic control system, for example PID controller, will aim to reach. For example, a boiler control system might have a temperature setpoint, that is a temperature the control system aims to attain....
s, controllers, logic, timers, trend logs, and alarms.
The unit controllers typically have analog and digital inputs, that allow measurement of the variable (temperature, humidity, or pressure) and analog
Analog signal
An analog or analogue signal is any continuous signal for which the time varying feature of the signal is a representation of some other time varying quantity, i.e., analogous to another time varying signal. It differs from a digital signal in terms of small fluctuations in the signal which are...
and digital
Digital
A digital system is a data technology that uses discrete values. By contrast, non-digital systems use a continuous range of values to represent information...
outputs for control of the medium (hot/cold water and/or steam). Digital inputs are typically (dry) contacts from a control device, and analog inputs are typically a voltage or current measurement from a variable (temperature, humidity, velocity, or pressure) sensing device. Digital outputs are typically relay contacts used to start and stop equipment, and analog outputs are typically voltage or current signals to control the movement of the medium (air/water/steam) control devices. Usually abbreviated as "DDC".
Data communication
When DDC controllers are networked together they can share information through a data bus. The control system may speak 'proprietary' or 'open protocol' language to communicate on the data bus. Examples of open protocol language are BACnet (Building Automation Control Network), LON (Echelon), Modbus.Integration
When different DDC data networks are linked together they can be controlled from a shared platform. This platform can then share information from one language to another. For example, a LON controller could share a temperature value with a BACnet controller. The integration platform can not only make information shareable, but can interact with all the devices.Most of the integration platforms are either a PC or a network appliance. In many cases, the HMI
HMI
HMI can refer to:* Hahn-Meitner-Institut, a research institut in Berlin, Germany, now called Helmholtz-Zentrum Berlin* Hammond–Whiting , an Amtrak station in Indiana, United States, with the code HMI....
(human machine interface) or SCADA
SCADA
SCADA generally refers to industrial control systems : computer systems that monitor and control industrial, infrastructure, or facility-based processes, as described below:...
(Supervisory Control And Data Acquisition) are part of it. Integration platform examples, to name only a few, are the Tridium Niagara AX, Johnson FX40,TAC Vista and the Unified Architecture i.e. OPC (Open Connectivity) server technology used when direct connectivity is not possible.
In HVAC
DDC is often used to control HVAC
HVAC
HVAC refers to technology of indoor or automotive environmental comfort. HVAC system design is a major subdiscipline of mechanical engineering, based on the principles of thermodynamics, fluid mechanics, and heat transfer...
(heating, ventilating, and air conditioning) devices such as valves via microprocessors using software to perform the control logic. Such systems receive analog and digital inputs from the sensors and devices installed in the HVAC system and, according to the control logic, provide analog or digital outputs to control the HVAC system devices.
These systems may be mated with a software package that graphically allows operators to monitor, control, alarm and diagnose building equipment remotely.
See also
- Building AutomationBuilding automationBuilding automation describes the functionality provided by the control system of a building. A building automation system is an example of a distributed control system...
- SCADASCADASCADA generally refers to industrial control systems : computer systems that monitor and control industrial, infrastructure, or facility-based processes, as described below:...
- PLCProgrammable logic controllerA programmable logic controller or programmable controller is a digital computer used for automation of electromechanical processes, such as control of machinery on factory assembly lines, amusement rides, or light fixtures. PLCs are used in many industries and machines...
- FieldbusFieldbusFieldbus is the name of a family of industrial computer network protocols used for real-time distributed control, now standardized as IEC 61158....
- GE FANUC GE Fanuc Intelligent Platforms
- Safety instrumented systemSafety instrumented systemA Safety Instrumented System is a form of process control usually implemented in industrial processes, such as those of a factory or an oil refinery. The SIS performs specified functions to achieve or maintain a safe state of the process when unacceptable or dangerous process conditions are detected...
, (SIS) - Industrial control systemsIndustrial Control SystemsIndustrial control system is a general term that encompasses several types of control systems used in industrial production, including supervisory control and data acquisition systems, distributed control systems , and other smaller control system configurations such as skid-mounted programmable...
- Industrial safety systemsIndustrial safety systemsAn industrial safety system is a countermeasure crucial in any hazardous plants such as oil and gas plants and nuclear plants. They are used to protect human, plant, and environment in case the process goes beyond the control margins. As the name suggests, these systems are not intended for...