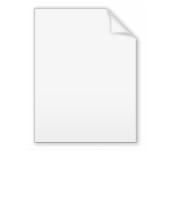
Industrial Control Systems
Encyclopedia
Industrial control system (ICS) is a general term that encompasses several types of control system
s used in industrial production, including supervisory control and data acquisition (SCADA
) systems, distributed control system
s (DCS), and other smaller control system configurations such as skid-mounted programmable logic controller
s (PLC) often found in the industrial sectors and critical infrastructures.
ICSs are typically used in industries such as electrical, water, oil, gas and data.
Based on information received from remote stations, automated or operator-driven supervisory commands can be pushed to remote station control devices, which are often referred to as field devices. Field devices control local operations such as opening and closing valves and breakers, collecting data from sensor systems, and monitoring the local environment for alarm conditions.
The PLC (programmable logic controller) evolved out of a need to replace racks of relays in ladder form. The latter were not particularly reliable, were difficult to rewire, and were difficult to diagnose. PLC control tends to be used in very regular, high-speed binary controls, such as controlling a high-speed printing press. Originally, PLC equipment did not have remote I/O
racks, and many couldn't even perform more than rudimentary analog controls.
SCADA's history is rooted in distribution applications, such as power, natural gas, and water pipelines, where there is a need to gather remote data through potentially unreliable or intermittent low-bandwidth/high-latency links. SCADA systems use open-loop control with sites that are widely separated geographically. A SCADA system uses RTUs (remote terminal units, also referred to as remote telemetry units) to send supervisory data back to a control center. Most RTU systems always did have some limited capacity to handle local controls while the master station is not available. However, over the years RTU systems have grown more and more capable of handling local controls.
The boundaries between these system definitions are blurring as time goes on. The technical limits that drove the designs of these various systems are no longer as much of an issue. Many PLC platforms can now perform quite well as a small DCS, using remote I/O and reliable that some SCADA systems actually manage closed loop control over long distances. With the increasing speed of today's processors, many DCS products have a full line of PLC-like subsystems that weren't offered when they were initially developed.
This led to the concept of a PAC (programmable automation controller
or process automation controller), that is an amalgamation of these three concepts. Time and the market will determine whether this can simplify some of the terminology and confusion that surrounds these concepts today.
are used to control industrial processes such as electric power generation, oil and gas refineries, water and wastewater treatment, and chemical, food, and automotive production. DCSs are integrated as a control architecture containing a supervisory level of control, overseeing multiple integrated sub-systems that are responsible for controlling the details of a localized process.
Product and process control are usually achieved by deploying feed back or feed forward control loops whereby key product and/or process conditions are automatically maintained around a desired set point. To accomplish the desired product and/or process tolerance around a specified set point, only specific programmable controllers are used.
provide boolean logic operations, timers, and (in some models) continuous control. The proportional, integral, and/or differential gains of the PLC continuous control feature may be tuned to provide the desired tolerance as well as the rate of self-correction during process upsets. DCSs are used extensively in process-based industries.
PLCs are computer-based solid-state devices that control industrial equipment and processes. While PLCs can control system components used throughout SCADA and DCS systems, they are often the primary components in smaller control system configurations. They are used to provide regulatory control of discrete processes such as automobile assembly lines and power plant soot blower
controls and are used extensively in almost all industrial processes.
Control system
A control system is a device, or set of devices to manage, command, direct or regulate the behavior of other devices or system.There are two common classes of control systems, with many variations and combinations: logic or sequential controls, and feedback or linear controls...
s used in industrial production, including supervisory control and data acquisition (SCADA
SCADA
SCADA generally refers to industrial control systems : computer systems that monitor and control industrial, infrastructure, or facility-based processes, as described below:...
) systems, distributed control system
Distributed control system
A distributed control system refers to a control system usually of a manufacturing system, process or any kind of dynamic system, in which the controller elements are not central in location but are distributed throughout the system with each component sub-system controlled by one or more...
s (DCS), and other smaller control system configurations such as skid-mounted programmable logic controller
Programmable logic controller
A programmable logic controller or programmable controller is a digital computer used for automation of electromechanical processes, such as control of machinery on factory assembly lines, amusement rides, or light fixtures. PLCs are used in many industries and machines...
s (PLC) often found in the industrial sectors and critical infrastructures.
ICSs are typically used in industries such as electrical, water, oil, gas and data.
Based on information received from remote stations, automated or operator-driven supervisory commands can be pushed to remote station control devices, which are often referred to as field devices. Field devices control local operations such as opening and closing valves and breakers, collecting data from sensor systems, and monitoring the local environment for alarm conditions.
A historical perspective
Industrial control system technology has evolved over the past three to four decades. DCS systems generally refer to the particular functional distributed control system design that exist in industrial process plants (e.g., oil and gas, refining, chemical, pharmaceutical, some food and beverage, water and wastewater, pulp and paper, utility power, mining, metals). The DCS concept came about from a need to gather data and control the systems on a large campus in real time on high-bandwidth, low-latency data networks. It is common for loop controls to extend all the way to the top level controllers in a DCS, as everything works in real time. These systems evolved from a need to extend pneumatic control systems beyond just a small cell area of a refinery.The PLC (programmable logic controller) evolved out of a need to replace racks of relays in ladder form. The latter were not particularly reliable, were difficult to rewire, and were difficult to diagnose. PLC control tends to be used in very regular, high-speed binary controls, such as controlling a high-speed printing press. Originally, PLC equipment did not have remote I/O
I/O
I/O may refer to:* Input/output, a system of communication for information processing systems* Input-output model, an economic model of flow prediction between sectors...
racks, and many couldn't even perform more than rudimentary analog controls.
SCADA's history is rooted in distribution applications, such as power, natural gas, and water pipelines, where there is a need to gather remote data through potentially unreliable or intermittent low-bandwidth/high-latency links. SCADA systems use open-loop control with sites that are widely separated geographically. A SCADA system uses RTUs (remote terminal units, also referred to as remote telemetry units) to send supervisory data back to a control center. Most RTU systems always did have some limited capacity to handle local controls while the master station is not available. However, over the years RTU systems have grown more and more capable of handling local controls.
The boundaries between these system definitions are blurring as time goes on. The technical limits that drove the designs of these various systems are no longer as much of an issue. Many PLC platforms can now perform quite well as a small DCS, using remote I/O and reliable that some SCADA systems actually manage closed loop control over long distances. With the increasing speed of today's processors, many DCS products have a full line of PLC-like subsystems that weren't offered when they were initially developed.
This led to the concept of a PAC (programmable automation controller
Programmable automation controller
A programmable automation controller ' is a compact controller that combines the features and capabilities of a PC-based control system with that of a typical programmable logic controller . PACs are most often used in industrial settings for process control, data acquisition, remote equipment...
or process automation controller), that is an amalgamation of these three concepts. Time and the market will determine whether this can simplify some of the terminology and confusion that surrounds these concepts today.
DCSs
DCSsDistributed control system
A distributed control system refers to a control system usually of a manufacturing system, process or any kind of dynamic system, in which the controller elements are not central in location but are distributed throughout the system with each component sub-system controlled by one or more...
are used to control industrial processes such as electric power generation, oil and gas refineries, water and wastewater treatment, and chemical, food, and automotive production. DCSs are integrated as a control architecture containing a supervisory level of control, overseeing multiple integrated sub-systems that are responsible for controlling the details of a localized process.
Product and process control are usually achieved by deploying feed back or feed forward control loops whereby key product and/or process conditions are automatically maintained around a desired set point. To accomplish the desired product and/or process tolerance around a specified set point, only specific programmable controllers are used.
PLCs
PLCsProgrammable logic controller
A programmable logic controller or programmable controller is a digital computer used for automation of electromechanical processes, such as control of machinery on factory assembly lines, amusement rides, or light fixtures. PLCs are used in many industries and machines...
provide boolean logic operations, timers, and (in some models) continuous control. The proportional, integral, and/or differential gains of the PLC continuous control feature may be tuned to provide the desired tolerance as well as the rate of self-correction during process upsets. DCSs are used extensively in process-based industries.
PLCs are computer-based solid-state devices that control industrial equipment and processes. While PLCs can control system components used throughout SCADA and DCS systems, they are often the primary components in smaller control system configurations. They are used to provide regulatory control of discrete processes such as automobile assembly lines and power plant soot blower
Soot blower
A Sootblower is a system for removing the soot that is deposited on the furnace tubes of a boiler during combustion. Various types of soot blowers such as Wall Blowers, Long Retractable Blowers and Air Heater Blowers are used for the cleaning...
controls and are used extensively in almost all industrial processes.
Embedded control
Another option is the use of several small embedded controls attached to an industrial computer via a network. Examples are the Lantronix Xport and Digi/ME.See also
- AutomationAutomationAutomation is the use of control systems and information technologies to reduce the need for human work in the production of goods and services. In the scope of industrialization, automation is a step beyond mechanization...
- Industrial safety systems
- MTConnectMTConnectMTConnect is a manufacturing industry standard to facilitate the organized retrieval of process information from numerically controlled machine tools. The initiative began as a result of lectures given by David Edstrom of Sun Microsystems and Dr...
- OPC FoundationOPC FoundationThe Object Linking and Embedding for Process Control Foundation is an industry consortium that creates and maintains standards for open connectivity of industrial automation devices and systems, such as industrial control systems and process control generally...
- Programmable logic controllerProgrammable logic controllerA programmable logic controller or programmable controller is a digital computer used for automation of electromechanical processes, such as control of machinery on factory assembly lines, amusement rides, or light fixtures. PLCs are used in many industries and machines...
(PLC) - Safety instrumented systemSafety instrumented systemA Safety Instrumented System is a form of process control usually implemented in industrial processes, such as those of a factory or an oil refinery. The SIS performs specified functions to achieve or maintain a safe state of the process when unacceptable or dangerous process conditions are detected...
(SIS) - SCADASCADASCADA generally refers to industrial control systems : computer systems that monitor and control industrial, infrastructure, or facility-based processes, as described below:...
External links
- Control System Integrators Association
- ISA a leading, global, nonprofit organization that is setting the standard for automation]
- New Age of Industrial Controllers
- Proview Open source Process Control System
- http://www.softnoze.com/index.html, Components for Mounting & Applying Industrial Control/Automation Sensor & Switches, SoftNoze USA Inc, Frankfort, NY USA