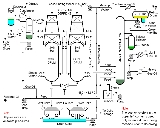
Delayed coker
Encyclopedia
A delayed coker is a type of coker
whose process consists of heating a residual oil feed to its thermal cracking temperature in a furnace
with multiple parallel passes. This cracks the heavy, long chain hydrocarbon
molecules of the residual oil into coker gas oil and petroleum coke
. Delayed coking is one of the unit processes used in many oil refineries
.
begins in the furnace, continues in the transfer line, and finishes in the coke drum.
As cracking continues in the drum, gas oil and lighter components are generated in vapor phase and separate from the liquid and solids. The drum effluent is vapor only except for any liquid or solids entrainment, and is directed to a fractionation column where it is separated into the desirable boiling point fractions. Solid coke is deposited in the drum in a porous structure that allows flow through the pores. All solids and uncracked residual liquid produced from the vapor and liquid feed are intended to remain in the drum.
After the drum is full of the solidified coke, the hot mixture from the furnace is switched to a second drum. While the second drum is filling, the full drum is steamed to further reduce hydrocarbon content of the petroleum coke, and then water quenched to cool it. The top and bottom heads of the full coke drum are removed, and the solid petroleum coke is then cut from the coke drum with a high pressure water nozzle, where it falls into a pit, pad, or sluiceway for reclamation to storage.
Larger cokers have several pairs of tandem drums.
) produced in a delayed coker and the corresponding compositions after the green coke has been calcined at 2375 °F (1302 °C):
Coker unit
A coker or coker unit is an oil refinery processing unit that converts the residual oil from the vacuum distillation column or the atmospheric distillation column into low molecular weight hydrocarbon gases, naphtha, light and heavy gas oils, and petroleum coke...
whose process consists of heating a residual oil feed to its thermal cracking temperature in a furnace
Furnace
A furnace is a device used for heating. The name derives from Latin fornax, oven.In American English and Canadian English, the term furnace on its own is generally used to describe household heating systems based on a central furnace , and sometimes as a synonym for kiln, a device used in the...
with multiple parallel passes. This cracks the heavy, long chain hydrocarbon
Hydrocarbon
In organic chemistry, a hydrocarbon is an organic compound consisting entirely of hydrogen and carbon. Hydrocarbons from which one hydrogen atom has been removed are functional groups, called hydrocarbyls....
molecules of the residual oil into coker gas oil and petroleum coke
Petroleum coke
Petroleum coke is a carbonaceous solid derived from oil refinery coker units or other cracking processes. Other coke has traditionally been derived from coal....
. Delayed coking is one of the unit processes used in many oil refineries
Oil refinery
An oil refinery or petroleum refinery is an industrial process plant where crude oil is processed and refined into more useful petroleum products, such as gasoline, diesel fuel, asphalt base, heating oil, kerosene, and liquefied petroleum gas...
.
Description
CrackingCracking (chemistry)
In petroleum geology and chemistry, cracking is the process whereby complex organic molecules such as kerogens or heavy hydrocarbons are broken down into simpler molecules such as light hydrocarbons, by the breaking of carbon-carbon bonds in the precursors. The rate of cracking and the end products...
begins in the furnace, continues in the transfer line, and finishes in the coke drum.
As cracking continues in the drum, gas oil and lighter components are generated in vapor phase and separate from the liquid and solids. The drum effluent is vapor only except for any liquid or solids entrainment, and is directed to a fractionation column where it is separated into the desirable boiling point fractions. Solid coke is deposited in the drum in a porous structure that allows flow through the pores. All solids and uncracked residual liquid produced from the vapor and liquid feed are intended to remain in the drum.
After the drum is full of the solidified coke, the hot mixture from the furnace is switched to a second drum. While the second drum is filling, the full drum is steamed to further reduce hydrocarbon content of the petroleum coke, and then water quenched to cool it. The top and bottom heads of the full coke drum are removed, and the solid petroleum coke is then cut from the coke drum with a high pressure water nozzle, where it falls into a pit, pad, or sluiceway for reclamation to storage.
Larger cokers have several pairs of tandem drums.
Typical schematic flow diagram
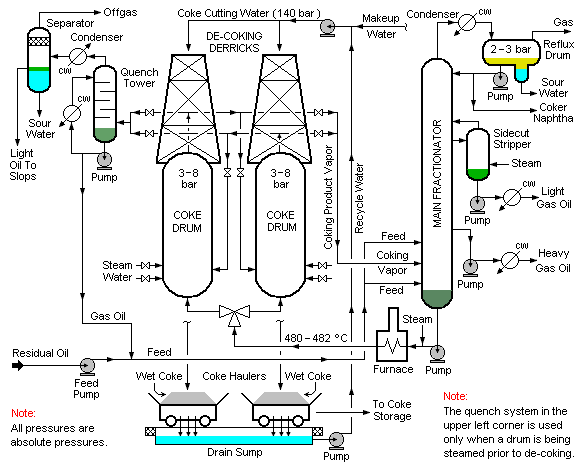
Composition of coke
The table below illustrates the wide range of compositions for raw petroleum coke (referred to as green cokeGreen coke
Green coke is the primary solid carbonization product from high boiling hydrocarbon fractions obtained at temperatures below 900 K. It contains a fraction of matter that can be released as volatiles during subsequent heat treatment at temperatures up to approximately 1600 K...
) produced in a delayed coker and the corresponding compositions after the green coke has been calcined at 2375 °F (1302 °C):
Component | Green coke as produced | Coke calcined at 2375 °F |
---|---|---|
Fixed carbon, wt % | 80 − 95 | 98.0 − 99.5 |
Hydrogen, wt % | 3.0 − 4.5 | 0.1 |
Nitrogen, wt % | 0.1 − 0.5 | |
Sulfur, wt % | 0.2 − 6.0 | |
Volatile matter, wt % | 5 − 15 | 0.2 − 0.8 |
Moisture, wt % | 0.5 − 10 | 0.1 |
Ash, wt % | 0.1 − 1.0 | 0.02 − 0.7 |
Density, g/cc | 1.2 − 1.6 | 1.9 − 2.1 |
Metals, ppm weight: | ||
Aluminum | 15 − 100 | 15 − 100 |
Boron | 0.1 − 15 | 0.1 − 15 |
Calcium | 25 − 500 | 25 − 500 |
Chromium | 5 − 50 | 5 − 50 |
Cobalt | 10 − 60 | 10 − 60 |
Iron | 50 − 5000 | 50 − 5000 |
Manganese | 2 − 100 | 2 − 100 |
Magnesium | 10 − 250 | 10 − 250 |
Molybdenum | 10 − 20 | 10 − 20 |
Nickel | 10 − 500 | 10 − 500 |
Potassium | 20 − 50 | 20 − 50 |
Silicon | 50 − 600 | 50 − 600 |
Sodium | 40 − 70 | 40 − 70 |
Titanium | 2 − 60 | 2 − 60 |
Vanadium | 5 − 500 | 5 − 500 |
See also
- Cracking (chemistry)Cracking (chemistry)In petroleum geology and chemistry, cracking is the process whereby complex organic molecules such as kerogens or heavy hydrocarbons are broken down into simpler molecules such as light hydrocarbons, by the breaking of carbon-carbon bonds in the precursors. The rate of cracking and the end products...
- Shukhov cracking processShukhov cracking processThe Shukhov cracking process is a thermal cracking process invented by Vladimir Shukhov and Sergei Gavrilov. Shukhov designed and built the first thermal cracking techniques important to the petrochemical industry. His patent The Shukhov cracking process is a thermal cracking process invented by...
- Burton processBurton processThe Burton process is a thermal cracking process invented by William Merriam Burton and Robert Humphrey.The oil industry used it to double the production of gasoline in 1913. This thermal cracking process was patented on January 7, 1913 ....
- Coke (fuel)Coke (fuel)Coke is the solid carbonaceous material derived from destructive distillation of low-ash, low-sulfur bituminous coal. Cokes from coal are grey, hard, and porous. While coke can be formed naturally, the commonly used form is man-made.- History :...
- VisbreakerVisbreakerA visbreaker is a processing unit in oil refinery whose purpose is to reduce the quantity of residual oil produced in the distillation of crude oil and to increase the yield of more valuable middle distillates by the refinery...