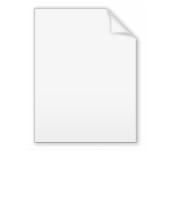
ARCASPACE
Encyclopedia
Asociația Română pentru Cosmonautică și Aeronautică (ARCA) or Romanian Cosmonautics and Aeronautics Association is a non-governmental organization
that promotes aerospace projects as well as other space-related activities. It is based in Râmnicu Vâlcea
, Romania
.
, Romania
, in front of the Hermann Oberth
memorial house, a few students
met and decided that Romania
needed to become an active pariticipant in space technology, and ARCA was born.
In 1998 ARCA's members began by developing a high-performance rocket engine. ARCA became an officially registered Romanian organization in 1999.
Since then, despite a small budget, ARCA has become the leader in Romanian rocket technology.
The high-performance rocket engine project started in 1998 featured an engine delivering 85,000 Kilogram-force
. It was an open cycle engine with four burning chambers, fed with liquid oxygen
and kerosene
at a combustion pressure of 70 bars. This project gave the group the experience needed for even more demanding space technology work. ARCA now had a proven team of rocket engineers.
The IAR-111 program aims to create a supersonic high altitude airplane
intended to extend ARCA’s HAAS II rocket launch capabilities in the Google Lunar X Prize competition, and for developing space tourism related technologies. The typical flight sequence of this aircraft includes takeoff from the sea surface, followed by a horizontal acceleration at low subsonic speeds, followed by rapid ascension, in approximately two minutes, to the altitude of 48,000 feet. At this altitude the airplane will release the Haas II rocket, that will follow its own flight sequence. IAR - 111 without its attached payload will return in glided flight to the sea surface. IAR - 111 will have supersonic flight capability of Mach 1.5 at 48,000 feet, having Haas II rocket as payload, and as space tourism technology development platform, it will reach the speed of Mach 2.6 at 90,000 feet.
The aircraft will have a crew of two persons, the pilot and the navigator, aiming to become the first Romanian supersonic airplane. The aircraft cabin is detachable and is equipped with two rocket propelled parachutes. As such the cabin can be separated form the aircraft at speeds between Mach 0-1.2 and heights above 300 feet and can return the crew safely on the sea surface.
Completion is scheduled for the middle of 2012, followed by the first takeoff at the end of 2012. First supersonic flight is estimated for the first half of the year 2013. Starting February 1st 2011, the public will be able to track the construction of the IAR-111 Excelsior daily.
The new moon rocket, named HAAS II is of a conventional design, unlike its predecessor HAAS, in order to fit underneath IAR-111. It's also powered by an 85% hydrogen peroxide mixture.
HAAS is an innovative air-launched, 3 stages orbital rocket, preliminary designed in 2006 using the technology developed at ARCA during The Ansari X Prize Competition and The European Private Manned Space Program. The rocket was named after Conrad Haas
(1509-1579) German-Romanian medieval rocket pioneer, the first creator of multiple staged rockets.
The European Lunar Explorer - ELE is a 3 stages space probe able to fly from the Earth's low orbit to the Moon surface and to send scientific data back to Earth. ELE will be placed into orbit by the HAAS launcher.
The rocket will be lifted from the sea using the world's heaviest “0 pressure” balloon ever built. ARCA already has experience with solar Montgolfier balloons. Between 2006-2007 ARCA built and launched the worlds largest solar Montgolfier balloon.
The main advantages of lifting the rocket from the sea is that no launch pad is required, and the launch point can be placed as close as possible to the Earth’s Equator.
Once the platform is in position, the rocket will be placed on the sea surface and the hydrogen peroxide oxidizer will be transferred into the fuel tanks. After the fuel tanks are filled, the team will start the balloon inflation procedure. This will take about 3 hours. When the balloon has reached the necessary lifting capability, the rocket will be lifted from the sea surface and placed into near vertical position beneath the balloon, attached with a cable. The distance between the balloon bottom and the rocket will be 200 m.
The balloon and rocket will fly to an altitude of 18,000 m for 1 hr 45 min.
The rocket’s third and last stage will be ignited and will burn for another 168 sec, putting the ELE into an elliptical LEO to an altitude of 140 km. At this altitude the rocket’s third stage will separate from the ELE probe.
At a distance of around 38,000 km from the Moon, ELE will reach the Lagrange point where the force of gravity of the Earth and the force of gravity of the Moon will be almost equal. ELE will enter in this point with an excess speed of about 500m/s, which will allow it to be further attracted by Moon’s force of gravity. Once this point is passed, the ELE will be fast attracted by Moon’s gravity. In this situation, ELE will start Stage E2 brake in an opposite direction to the speed vector. The team will try to reduce as much as possible the number of brake engine starts.
The desired Moon landing point is the North region of the Carpathian Mountains. This spot was chosen because the Carpathian Mountains
also pass through Romania from the North to the West.
STABILO is the latest suborbital manned system created by the European Team ARCA. ARCA hopes that its new spaceship, through its unique design and safety capabilities, will capture the attention and imagination of the public.
ARCA’s philosophy is that a manned suborbital ship for commercial applications must be designed taking into account the passenger and crew safety. For that purpose, the ship must have:
In respect of these statements, ARCA team proposes a new suborbital ship concept. The engine, placed at the top of the ship, offers an unconventional aspect for this spaceship.
The tractor engine offers the possibility to place the crew cabin at the rear part of the ship, which offers extended abort capabilities. STABILO will be launched in a vertical position. In this situation the pilot activities are highly reduced.
The tractor engine, generates reaction gases, close to the ship structure for a long period of time, without affecting the ship's integrity. This is possible due to the use of hydrogen peroxide as monopropellant
which offers a low temperature for the reaction products.
The purely space applications design of this ship makes it inappropriate for powered flights at low altitudes, in dense atmosphere. Because of that the system is transported to an altitude of 22,000 m with a Solar Montgolfier.
The tractor engine solution isn't new. It was previously used in escape systems onboard Mercury, Apollo and Soyuz. The main difference is that an escape system has a low burning time. STABILO's engine will run for approximately one minute, a longer time.
will start the descent which, for almost the half the distance, will be made in weightlessness. At low dynamic pressure, the RCS will keep the cabin with the base down. The aerodynamic stability system placed at the top of the capsule will keep the vehicle in a vertical position during the atmospheric phase of the reentry, without human intervention. The maximum deceleration during reentry will be -4.6 G.
The cabin's main parachute will be extracted at 4,000 m and a speed of about 350 km/h. The landing speed will be kept below 7 m/s.
There are some alternatives, from the fuel point of view, regarding the type of a potential rocket engine that can equip such a vehicle: bipropellant liquid fuel, monopropellant liquid fuel, solid fuel and hybrid fuel.
Through 2000-2004, ARCA experimented a series of rocket engines with various types of fuels. After the tests in 2003 the team decided to go forward with a hydrogen peroxide monopropellant engine. This type of engine was tested intensively through 2003-2004. Demonstrator 2B rocket which was launched from Cape Midia Air Force Test Site on September 9, 2004 used this type of technology.
A monopropellant system used as a main engine for space propulsion is an unusual proposition mainly because of its low specific impulse. A vehicle launched from the ground, using this type of propulsion, in a suborbital mission, with a payload equivalent of about three passengers will be necessary to carry about 7 t of fuel, an unacceptable value. Furthermore, the final acceleration would be around 12G.
It is clear that a ship equipped with a hydrogen peroxide (85%) monopropellant rocket engine, able to complete the above mentioned mission is not suitable for a ground launch. However a 24% higher impulse can be obtained in the case of an air launch from an altitude of around 22,000 m, with an almost fully adapted nozzle.
STABILO is the first spaceship that uses a monopropellant tractor engine this solution was chosen because it offers improved safety during the flight. Despite of the presence of the four nozzles placed at an angle of 20°, STABILO has only one engine. The reaction gases from the reaction chamber are distributed through the four nozzles. The 20° angle leads to a 6% thrust loss. Despite this, ARCA engineers considered that the advantages of having a safer flight resulting from a tractor engine are more important and the thrust loss could be compensated through a higher fuel quantity and a longer engine run.
The reaction is 100% ecological since hydrogen peroxide decomposes in oxygen and hot water vapors. Function of the mission nature, and fuel concentration (65-85%), the engine will be reusable or expandable. While the expandable engines raise no special problems, the reusable engines built from composite materials is a real challenge. Such engines were used before but with ablative cooling (inner layers vaporize in order to keep outer layers at a reasonable temperature). However, this process can be used on "hot" engines at high temperatures. At lower temperatures, the inner layers don't vaporize efficiently anymore. ARCA's engine accumulates the heat inside the inner and intermediate layers so that the outer layers don't change their mechanical characteristics even after a complete engine run. The heat is not released outside. This system is not very economical but is certainly very safe and reliable.
The cabin is pressurized at 0.8 atm and contains navigation, flight control and life support systems. It is designed for one pilot that sits on a chair, specially designed for flight accelerations. The access inside the cabin is assured by a lateral auto-pressurized hatch which can be opened both from inside and outside of the cabin. As an added safety, the pilot will use a pressurized suit, offered by another former X Prize competitor, which has a lot of experience with pressurized suits: DeLeon Company. DeLeon and ARCA are partners since 2005 and they are collaborating on various aspects regarding the manned space flight.
The pilot has a panoramic view through three portholes. The position of the portholes was chosen in order to offer the pilot a complete view without it being necessary to raise from his chair. The top engine with its four nozzles could offer a beautiful view for the passenger, since the exhaust, made of oxygen and water vapors will freeze immediately after ejection, in contact with the outside environment (-60 degrees C). The jet will form small ice particles on which the Sun will reflect. After engine stop and capsule release, the pilot could maneuver the cabin with the RCS to have a view of the Earth with the four engine traces of ice beneath the ship.
The construction of ORIZONT began in mid-2004. At that time, ARCA was more concerned with the launch of Demonstrator 2B from Cape Midia and most of the members declined involvement in the ambitious ORIZONT project. However, a small group started the design and the construction of the new vehicle.
The first element was the mold for the pressurized compartment of the spacecraft. The mold and the whole structure of the cabin were finished in February 2005.
The work itself was done in a very small workshop and it was obvious that the team needed a much larger space for the equipments and hardware.
At the beginning of June one of the major sponsors of ARCA offered an assembly facility of 1500m2. Here, they began assembling the ORIZONT vehicle.
of the wings and the solutions that were selected for the propulsion system. The launch can be executed, depending of the carrier availability, from helicopter
or airplane. In every situation the launch will be made with the wings at near 0 degrees sweep angle because it is necessary that the wing generates the highest possible lift. In the case of helicopter launch, the ORIZONT vehicle will be lifted to an altitude of around 2,000-2,500 m. At this altitude, the vehicle will be released and will gravitationally accelerate to the required speed of about 210 km/h, necessary for the stable flight. In the case of the air launch, the ORIZONT vehicle will be transported to altitudes around 11,000 m, attached to the carrier at the top or at the bottom. Due to safety reasons, it is better to attach the vehicle at the bottom of the carrier. The launch from the helicopter is easier to implement from the logistical and technical point of view, but increases the stress of the pilot, because of the necessity to fly the ship in the atmosphere for a longer period of time.
The deceleration parachute will be extracted at a height of about 6000 m and this operation is shortly followed by the main parachute extraction ,at 4000 m. The whole parachute system is placed in the front of the ship, at the bottom of the cabin. The landing in the sea will take place at a speed no higher than 7m/s. The stress over the pilot, from the rocket engine shut-down to the landing moment is reduced significantly.
, and therefore cause the rocket to spin out of control once launched. ARCA have dismissed the claims saying that the nonrigid structure of the cables attached to points outside of the rockets prevent a pendulum like behavior of the system. The success of Mission 4b proved the viability of elastic articulation stability for launching rockets.
The old configuration used a liquid fuel rocket engine, designed to thrust 2,000 kgf during 60 sec. The fuel was: hydrogen
peroxide 85% + T1. In the new configuration will use a hybrid engine with hydrogen peroxide 85% as an oxidizer, in combination with polyethylene as fuel.
Demonstrator 2 was the starting point for the development of the successful Demonstrator 2B rocket. The first public display of this vehicle took place in Drăgășani
, on September 27, 2003.
This rocket was the end of subscale systems tests at ARCA and the beginning of the Orizont vehicle's final phase of construction.
The Demonstrator 2B rocket was successfully launched on September 9, 2004. The measurements indicated that the launch parameters were: 1,000 m altitude, 630 km/h, 2,100 m range.
ARCA’s military application rocket was presented to the Bucharest International Fair on October 3, 2006. The rocket financed by the government through the Romanian Space Agency- “SECURITY” Program, has a length of 4.1 m and is designed to fly with Mach 1.02 at sea level. The maximum flight altitude is 6.000 m. The main purpose of this project is to create a target able to simulate low altitude/high speed aggressor vehicles.
-launch for a three-stage rocket.. The new approach consists of using a supersonic rocket plane to get the HAAS II and its payload to 16 km before launch.
Non-governmental organization
A non-governmental organization is a legally constituted organization created by natural or legal persons that operates independently from any government. The term originated from the United Nations , and is normally used to refer to organizations that do not form part of the government and are...
that promotes aerospace projects as well as other space-related activities. It is based in Râmnicu Vâlcea
Râmnicu Vâlcea
Râmnicu Vâlcea is the capital city of Vâlcea County, Romania .-Geography and climate:Râmnicu Vâlcea is situated in the central-south area of Romania...
, Romania
Romania
Romania is a country located at the crossroads of Central and Southeastern Europe, on the Lower Danube, within and outside the Carpathian arch, bordering on the Black Sea...
.
Beginnings
In SibiuSibiu
Sibiu is a city in Transylvania, Romania with a population of 154,548. Located some 282 km north-west of Bucharest, the city straddles the Cibin River, a tributary of the river Olt...
, Romania
Romania
Romania is a country located at the crossroads of Central and Southeastern Europe, on the Lower Danube, within and outside the Carpathian arch, bordering on the Black Sea...
, in front of the Hermann Oberth
Hermann Oberth
Hermann Julius Oberth was an Austro-Hungarian-born German physicist and engineer. He is considered one of the founding fathers of rocketry and astronautics.- Early life :...
memorial house, a few students
met and decided that Romania
Romania
Romania is a country located at the crossroads of Central and Southeastern Europe, on the Lower Danube, within and outside the Carpathian arch, bordering on the Black Sea...
needed to become an active pariticipant in space technology, and ARCA was born.
In 1998 ARCA's members began by developing a high-performance rocket engine. ARCA became an officially registered Romanian organization in 1999.
Since then, despite a small budget, ARCA has become the leader in Romanian rocket technology.
The high-performance rocket engine project started in 1998 featured an engine delivering 85,000 Kilogram-force
Kilogram-force
A kilogram-force , or kilopond , is a gravitational metric unit of force. It is equal to the magnitude of the force exerted by one kilogram of mass in a gravitational field...
. It was an open cycle engine with four burning chambers, fed with liquid oxygen
Liquid oxygen
Liquid oxygen — abbreviated LOx, LOX or Lox in the aerospace, submarine and gas industries — is one of the physical forms of elemental oxygen.-Physical properties:...
and kerosene
Kerosene
Kerosene, sometimes spelled kerosine in scientific and industrial usage, also known as paraffin or paraffin oil in the United Kingdom, Hong Kong, Ireland and South Africa, is a combustible hydrocarbon liquid. The name is derived from Greek keros...
at a combustion pressure of 70 bars. This project gave the group the experience needed for even more demanding space technology work. ARCA now had a proven team of rocket engineers.
IAR-111 Excelsior and HAAS II
The problems and delays faced by ARCA while attempting to to launch rockets using balloon carriers prompted the development of an alternative launching device. The IAR-111 Excelsior rocket plane had been secretly in development since early 2010.The IAR-111 program aims to create a supersonic high altitude airplane
Aircraft
An aircraft is a vehicle that is able to fly by gaining support from the air, or, in general, the atmosphere of a planet. An aircraft counters the force of gravity by using either static lift or by using the dynamic lift of an airfoil, or in a few cases the downward thrust from jet engines.Although...
intended to extend ARCA’s HAAS II rocket launch capabilities in the Google Lunar X Prize competition, and for developing space tourism related technologies. The typical flight sequence of this aircraft includes takeoff from the sea surface, followed by a horizontal acceleration at low subsonic speeds, followed by rapid ascension, in approximately two minutes, to the altitude of 48,000 feet. At this altitude the airplane will release the Haas II rocket, that will follow its own flight sequence. IAR - 111 without its attached payload will return in glided flight to the sea surface. IAR - 111 will have supersonic flight capability of Mach 1.5 at 48,000 feet, having Haas II rocket as payload, and as space tourism technology development platform, it will reach the speed of Mach 2.6 at 90,000 feet.
The aircraft will have a crew of two persons, the pilot and the navigator, aiming to become the first Romanian supersonic airplane. The aircraft cabin is detachable and is equipped with two rocket propelled parachutes. As such the cabin can be separated form the aircraft at speeds between Mach 0-1.2 and heights above 300 feet and can return the crew safely on the sea surface.
Completion is scheduled for the middle of 2012, followed by the first takeoff at the end of 2012. First supersonic flight is estimated for the first half of the year 2013. Starting February 1st 2011, the public will be able to track the construction of the IAR-111 Excelsior daily.
The new moon rocket, named HAAS II is of a conventional design, unlike its predecessor HAAS, in order to fit underneath IAR-111. It's also powered by an 85% hydrogen peroxide mixture.
ELE and HAAS
Length: | 18 m |
---|---|
Diameter: | 4 m |
Balloon diameter: | 150 m |
Full weight: | 23,300 kg |
ELE weight: | 400 kg |
ELL weight: | 42 kg |
Stages: | 3 booster + 3 space probe |
Type: | Rocket powered, pressure feed |
Fuel: | Hydrogen peroxide + paraffin wax |
Stage 1 thrust: | 47,600 kgf |
Stage 2 thrust: | 24,800 kgf |
Stage 3 thrust: | 5,850 kgf |
Stage E1 thrust: | 500 kgf |
Stage E2 thrust: | 100 kgf |
ELL thrust: | 14 kgf |
Max Speed: | 11,880 km/h |
HAAS is an innovative air-launched, 3 stages orbital rocket, preliminary designed in 2006 using the technology developed at ARCA during The Ansari X Prize Competition and The European Private Manned Space Program. The rocket was named after Conrad Haas
Conrad Haas
Conrad Haas was a military engineer of the Holy Roman Empire, who is believed to be the first person to describe a multistage rocket in writing.Haas was perhaps born in Dornbach...
(1509-1579) German-Romanian medieval rocket pioneer, the first creator of multiple staged rockets.
The European Lunar Explorer - ELE is a 3 stages space probe able to fly from the Earth's low orbit to the Moon surface and to send scientific data back to Earth. ELE will be placed into orbit by the HAAS launcher.
The launch
The launch will be made from the sea with the help of a large marine platform designed by ARCA. The launch location will be established further, but it is preferred to launch as close as possible to the Earth Equator.The rocket will be lifted from the sea using the world's heaviest “0 pressure” balloon ever built. ARCA already has experience with solar Montgolfier balloons. Between 2006-2007 ARCA built and launched the worlds largest solar Montgolfier balloon.
The main advantages of lifting the rocket from the sea is that no launch pad is required, and the launch point can be placed as close as possible to the Earth’s Equator.
Once the platform is in position, the rocket will be placed on the sea surface and the hydrogen peroxide oxidizer will be transferred into the fuel tanks. After the fuel tanks are filled, the team will start the balloon inflation procedure. This will take about 3 hours. When the balloon has reached the necessary lifting capability, the rocket will be lifted from the sea surface and placed into near vertical position beneath the balloon, attached with a cable. The distance between the balloon bottom and the rocket will be 200 m.
The balloon and rocket will fly to an altitude of 18,000 m for 1 hr 45 min.
Booster flight
At 18,000 m the rocket will start its first stage rocket engine for 100 sec. After engine cut-off, the first stage will be detached. Soon after, the rocket’s second stage will be ignited and it will burn for 110 sec. After the burn completion the second stage will be also detached.The rocket’s third and last stage will be ignited and will burn for another 168 sec, putting the ELE into an elliptical LEO to an altitude of 140 km. At this altitude the rocket’s third stage will separate from the ELE probe.
Orbital flight
After the HAAS’s 3rd stage burnout, the ELE spacecraft will be placed into orbit. ELE will start the Stage E1 main engine at first orbit’s apogee for a ?V=260m/s in order to circularize the orbit to an altitude of 250 km. After a short time spent in Earth orbit, ELE will ignite once again the E1 main engine that will increase vehicle’s speed to 11.1 km/s. After Stage E1 fuel depletion it will be ejected on the vehicle’s way to the Moon.From Earth to Moon
As the ELE will head to the Moon, the trajectory will be periodically corrected using the Stage E2 main brake engine. During the trip from the Earth to the Moon, ELE will deploy two 100 W solar panels that will allow the vehicle to charge the internal batteries and to use the energy for the telemetry and video equipment.At a distance of around 38,000 km from the Moon, ELE will reach the Lagrange point where the force of gravity of the Earth and the force of gravity of the Moon will be almost equal. ELE will enter in this point with an excess speed of about 500m/s, which will allow it to be further attracted by Moon’s force of gravity. Once this point is passed, the ELE will be fast attracted by Moon’s gravity. In this situation, ELE will start Stage E2 brake in an opposite direction to the speed vector. The team will try to reduce as much as possible the number of brake engine starts.
Lunar landing
After Stage E2 fuel depletion, it will be ejected at an altitude of about 10 km from the lunar surface, the ELE Lunar Lander (ELL) will soft land on the Moon using the Stage E3 main engine and inertial guidance launch platform together with the onboard flight computer. The Stage E3 main engine is thrust adjustable, gimbaled, hydrogen peroxide (85% concentration), monopropellant 14 kgf, rocket motor. The time from the Earth launch to the Moon surface will be 116 hours (4 days, 2 hours).The desired Moon landing point is the North region of the Carpathian Mountains. This spot was chosen because the Carpathian Mountains
Carpathian Mountains
The Carpathian Mountains or Carpathians are a range of mountains forming an arc roughly long across Central and Eastern Europe, making them the second-longest mountain range in Europe...
also pass through Romania from the North to the West.
Stabilo
Length: | 6 m |
---|---|
Maximum weight: | 1,000 kg |
Crew: | 1 |
Fuel: | H2O2 |
Traction: | 30,000 N |
Acceleration (boost phase) : | 4G |
Acceleration (reentry): | 4.6G |
Max speed: | 4,500 km/h |
Max altitude: | 100 km |
STABILO is the latest suborbital manned system created by the European Team ARCA. ARCA hopes that its new spaceship, through its unique design and safety capabilities, will capture the attention and imagination of the public.
ARCA’s philosophy is that a manned suborbital ship for commercial applications must be designed taking into account the passenger and crew safety. For that purpose, the ship must have:
- a high reliability
- an excellent abort scenario and escape capabilities
- the stress for the pilot during flight reduced to minimum
In respect of these statements, ARCA team proposes a new suborbital ship concept. The engine, placed at the top of the ship, offers an unconventional aspect for this spaceship.
The tractor engine offers the possibility to place the crew cabin at the rear part of the ship, which offers extended abort capabilities. STABILO will be launched in a vertical position. In this situation the pilot activities are highly reduced.
The tractor engine, generates reaction gases, close to the ship structure for a long period of time, without affecting the ship's integrity. This is possible due to the use of hydrogen peroxide as monopropellant
Monopropellant
Monopropellants are propellants composed of chemicals or mixtures of chemicals which can be stored in a single container with some degree of safety. While stable under defined storage conditions, they react very rapidly under certain other conditions to produce a large volume of energetic gases...
which offers a low temperature for the reaction products.
The purely space applications design of this ship makes it inappropriate for powered flights at low altitudes, in dense atmosphere. Because of that the system is transported to an altitude of 22,000 m with a Solar Montgolfier.
The tractor engine solution isn't new. It was previously used in escape systems onboard Mercury, Apollo and Soyuz. The main difference is that an escape system has a low burning time. STABILO's engine will run for approximately one minute, a longer time.
The launch
STABILO was designed to be launched from an altitude of 22,000 m, in a two-stage manner. The first stage consists of a 1h,35min ascension with a 350.000mc Solar Montgolfier balloon to the altitude of 22,000m (66,000 feet). The second stage commences by launching the actual suborbital vehicle vertically, through the very thin balloon envelope. At the bottom of the balloon, a composite materials ring of 2 m diameter allows the STABILO to enter into the balloon envelope.Vertical powered flight
Immediately after the engine start, the vehicle will begin to accelerate on a vertical trajectory. The max. speed will be 1,250 m/s and the max. G load will be kept below 6.8 G.Inertial vertical flight
After engine shut-down, the vehicle will continue the inertial climb. Immediately after engine shut-down the crew cabin will be separated from the rocket booster. The RCS system will command the cabin attitude. The maximum altitude is above 100 km.The reentry
After apogee the cabin and booster rocketBooster rocket
A booster rocket is either the first stage of a multi-stage launch vehicle, or else a strap-on rocket used to augment the core launch vehicle's takeoff thrust and payload capability. Boosters are generally necessary to launch spacecraft into Earth orbit or beyond...
will start the descent which, for almost the half the distance, will be made in weightlessness. At low dynamic pressure, the RCS will keep the cabin with the base down. The aerodynamic stability system placed at the top of the capsule will keep the vehicle in a vertical position during the atmospheric phase of the reentry, without human intervention. The maximum deceleration during reentry will be -4.6 G.
The recovery
The rocket booster's main parachute will be extracted from the nose-cone compartment at an altitude of 4,000 m and a speed of 400 km/h.The cabin's main parachute will be extracted at 4,000 m and a speed of about 350 km/h. The landing speed will be kept below 7 m/s.
The monopropellant rocket engine
The main preoccupation for a spaceship designer is to ensure a high reliability. Since the appearance of rockets, until today, the main element that leads to a rocket vehicle failure is the engine. ARCA considers that the main issue that a designer has to deal with in order to create a reliable ship is the creation of a reliable rocket engine.There are some alternatives, from the fuel point of view, regarding the type of a potential rocket engine that can equip such a vehicle: bipropellant liquid fuel, monopropellant liquid fuel, solid fuel and hybrid fuel.
Through 2000-2004, ARCA experimented a series of rocket engines with various types of fuels. After the tests in 2003 the team decided to go forward with a hydrogen peroxide monopropellant engine. This type of engine was tested intensively through 2003-2004. Demonstrator 2B rocket which was launched from Cape Midia Air Force Test Site on September 9, 2004 used this type of technology.
A monopropellant system used as a main engine for space propulsion is an unusual proposition mainly because of its low specific impulse. A vehicle launched from the ground, using this type of propulsion, in a suborbital mission, with a payload equivalent of about three passengers will be necessary to carry about 7 t of fuel, an unacceptable value. Furthermore, the final acceleration would be around 12G.
It is clear that a ship equipped with a hydrogen peroxide (85%) monopropellant rocket engine, able to complete the above mentioned mission is not suitable for a ground launch. However a 24% higher impulse can be obtained in the case of an air launch from an altitude of around 22,000 m, with an almost fully adapted nozzle.
STABILO is the first spaceship that uses a monopropellant tractor engine this solution was chosen because it offers improved safety during the flight. Despite of the presence of the four nozzles placed at an angle of 20°, STABILO has only one engine. The reaction gases from the reaction chamber are distributed through the four nozzles. The 20° angle leads to a 6% thrust loss. Despite this, ARCA engineers considered that the advantages of having a safer flight resulting from a tractor engine are more important and the thrust loss could be compensated through a higher fuel quantity and a longer engine run.
The reaction is 100% ecological since hydrogen peroxide decomposes in oxygen and hot water vapors. Function of the mission nature, and fuel concentration (65-85%), the engine will be reusable or expandable. While the expandable engines raise no special problems, the reusable engines built from composite materials is a real challenge. Such engines were used before but with ablative cooling (inner layers vaporize in order to keep outer layers at a reasonable temperature). However, this process can be used on "hot" engines at high temperatures. At lower temperatures, the inner layers don't vaporize efficiently anymore. ARCA's engine accumulates the heat inside the inner and intermediate layers so that the outer layers don't change their mechanical characteristics even after a complete engine run. The heat is not released outside. This system is not very economical but is certainly very safe and reliable.
Length: | 6 m |
---|---|
Maximum weight: | 1000 kg |
Crew: | 1 |
Fuel: | H2O2 |
Traction: | 30,000 N |
Acceleration (boost phase) : | 4G |
Acceleration (reentry): | 4.6G |
Max speed: | 4,500 km/h |
Max altitude: | 100 km |
The crew cabin
The most important goal of the whole project is safety. Therefore, safety and backup systems for the pilot were designed for every stage of the flight. With the cabin placed at the bottom of the ship, the abort sequence has a simple procedure: the crew cabin can be gravitationally separated from the rocket booster and recovered with its parachute. The cabin offers protection for almost the entire flight sequence, even in unlikely events like complete equipment failure, structural damage, etc.The cabin is pressurized at 0.8 atm and contains navigation, flight control and life support systems. It is designed for one pilot that sits on a chair, specially designed for flight accelerations. The access inside the cabin is assured by a lateral auto-pressurized hatch which can be opened both from inside and outside of the cabin. As an added safety, the pilot will use a pressurized suit, offered by another former X Prize competitor, which has a lot of experience with pressurized suits: DeLeon Company. DeLeon and ARCA are partners since 2005 and they are collaborating on various aspects regarding the manned space flight.
The pilot has a panoramic view through three portholes. The position of the portholes was chosen in order to offer the pilot a complete view without it being necessary to raise from his chair. The top engine with its four nozzles could offer a beautiful view for the passenger, since the exhaust, made of oxygen and water vapors will freeze immediately after ejection, in contact with the outside environment (-60 degrees C). The jet will form small ice particles on which the Sun will reflect. After engine stop and capsule release, the pilot could maneuver the cabin with the RCS to have a view of the Earth with the four engine traces of ice beneath the ship.
The carrier balloon
The carrier balloon used to raise the ship at the launch altitude is a zero pressure Solar Montgolfier type, made of 15 µm high density polyethylene. The balloon uses the Sun radiation to heat the inside air. This will lead to a temperature gradient between the interior and the exterior of the balloon. This gradient has a maximum value of around 30 degrees C, which makes the air from the inside to have a lower density comparing with the outside air. The balloon used for the Mission5-8 flights has a capacity of 350.000mc. It will be the biggest balloon of this type ever built.The STABILO 1B system
This variant is different compared with the initial variant because of the rocket engine position. This allows a lower fuel consumption and the possibility to use a hot rocket engine. The crew cabin and the fuel tank are almost similar with the initial variant.Orizont
Length: | 10 m |
---|---|
Maximum wingspan: | 10 m |
Jet engine length: | 1.5 m |
Maximum weight: | 2,000 kg |
Crew: | 0-1-2 |
Specific impulse: | 110s |
Fuel: | H2O2-70% |
Fuel for jet engine: | T1+ oxygen from atm |
Traction: | 50,000 N |
Acceleration: | 6G |
Max speed: | 3,500 km/h |
Max altitude: | 100 km |
The construction of ORIZONT began in mid-2004. At that time, ARCA was more concerned with the launch of Demonstrator 2B from Cape Midia and most of the members declined involvement in the ambitious ORIZONT project. However, a small group started the design and the construction of the new vehicle.
The first element was the mold for the pressurized compartment of the spacecraft. The mold and the whole structure of the cabin were finished in February 2005.
The work itself was done in a very small workshop and it was obvious that the team needed a much larger space for the equipments and hardware.
At the beginning of June one of the major sponsors of ARCA offered an assembly facility of 1500m2. Here, they began assembling the ORIZONT vehicle.
Launch
The air-launch solutions are flexible due to the variable geometryGeometry
Geometry arose as the field of knowledge dealing with spatial relationships. Geometry was one of the two fields of pre-modern mathematics, the other being the study of numbers ....
of the wings and the solutions that were selected for the propulsion system. The launch can be executed, depending of the carrier availability, from helicopter
Helicopter
A helicopter is a type of rotorcraft in which lift and thrust are supplied by one or more engine-driven rotors. This allows the helicopter to take off and land vertically, to hover, and to fly forwards, backwards, and laterally...
or airplane. In every situation the launch will be made with the wings at near 0 degrees sweep angle because it is necessary that the wing generates the highest possible lift. In the case of helicopter launch, the ORIZONT vehicle will be lifted to an altitude of around 2,000-2,500 m. At this altitude, the vehicle will be released and will gravitationally accelerate to the required speed of about 210 km/h, necessary for the stable flight. In the case of the air launch, the ORIZONT vehicle will be transported to altitudes around 11,000 m, attached to the carrier at the top or at the bottom. Due to safety reasons, it is better to attach the vehicle at the bottom of the carrier. The launch from the helicopter is easier to implement from the logistical and technical point of view, but increases the stress of the pilot, because of the necessity to fly the ship in the atmosphere for a longer period of time.
Autonomous atmospheric flight
After the carrier release, the ORIZONT vehicle will start the air-breathing engine and will start to climb with the wings completely open to an altitude of around 17,000 m with a speed range of about 400–700 km/h. The maximum acceleration for this stage of the flight will be no higher than +4.6/-1.6 GRocket engine
Immediately after the vehicle reaches the desired altitude, the air-breathing engine will be detached. This action is shortly followed by the modification of the wing sweep angle to a minimum value. The lift and drag will decrease significantly.Rocket engine vertical flight
The rocket engine will be started when ORIZONT will have 45 degrees angle of altitude which can be obtained from the stabilizers. Immediately after the start, the vehicle will begin to accelerate rapidly, the aerodynamic surfaces putting the vehicle to a near vertical trajectory. This trajectory will be kept for the entire time of the rocket engine run.Inertial vertical flight and the reentry preparations
After the rocket engine shut-down, the ship will continue to climb inertly in a vertical position; in this time frame, the pilot will start the reconfiguration of the whole ship for re-entry mode: the wing sweep angle will be changed to a negative position and the stabilizers will change their position by 180˚. The low atmospheric density at that altitude will not allow the pilot to control the attitude of the ship from the aerodynamic surfaces and the ship will be controlled with the reaction control system (RCS).Flight
At the maximum altitude of 100 km, the ship will have the lowest speed in the entire flight sequence. The pilot will continue to control the ship with the RCS.Re-entry
After reaching the 100 km altitude, the vehicle will start the descent. For less than half the distance, the pilot will experience the effects of weightlessness. The ship must be kept with the RCS in a vertical position with the nose up. This process does not require an intense effort from the pilot since, to some degree, even big attitude errors are allowed. When the ship encounters the first dense atmospheric layers the use of the RCS becomes unnecessary;the ship, due to the unique variable geometry system, will become auto-stabilized aerodynamically and inert. The maximum deceleration at reentry will reach -6.2 G for only 4 sec.Recovery
Even though the variable geometry of the vehicle would allow a landing procedure on a runway, ARCA decided that the parachuted recovery system is safer from the following considerations:- In the case of a trajectory error during the rocket engine powered flight, the vehicle could be deviated far away from the runway.
- The necessity of a runway presence limits the flight corridor definition possibilities.
- The stress for the pilot is lower because the necessity of a runway landing procedure is suppressed.
- It offers the possibility to abort the mission in almost every sequence of the flight and to bring the ship safely to the ground.
The deceleration parachute will be extracted at a height of about 6000 m and this operation is shortly followed by the main parachute extraction ,at 4000 m. The whole parachute system is placed in the front of the ship, at the bottom of the cabin. The landing in the sea will take place at a speed no higher than 7m/s. The stress over the pilot, from the rocket engine shut-down to the landing moment is reduced significantly.
Description
The Helen vehicle has three stages: Demonstrator2, 2B, and 2C. Demonstrator2 and 2B were created between 2003-2004 during the Ansari X Prize Competition. Demonstrator2C is a new rocket created in 2009. Helen 2 is a vehicle based on the Stabilo platform built after the failure of Mission 3.Flight
The Helen vehicle was supposed fly on Mission 3 with The ELL avionics payload transported on this flight, while the Stabilo vehicle will be used for future manned flights. Helen was to be transported to 14000m via a solar carrier balloon. After the failure of Mission 3, due to an unexpected twisting of the solar balloon, and the failure of Mission 4 due to a rupture in the helium balloon, Helen 2 was transported on Mission 4b by another helium balloon on October 1st 2010 to 14000m. It successfully flew up to 40km, but the capsule was not recovered. This wasn't a problem, however, as data had been transmitted live to the ARCA command center.Popescu-Diaconu stabilization method
Besides the ELL avionics test, the Helen 2 vehicle will tested an innovative flight stability system for the Moon landing sequence of the ELL module. Helen 2 used a gravitational stability method in vertical flight without aerodynamic surfaces or jet commands, by towing the component stages and payload. The towing can be made by cable, or rigid-articulated system. In order to have a stabilized rocket in vertical flight, in a gravitational field, this method is using a towed mass in the same direction with the thrust. This mass consists in the next rocket stages and payload. The stability effect depends of several elements: the mass of the stabilized body, the mass of the towed mass and the length between the centers of gravity of the stabilized body and the stabilizer body. This method can be applied in the extra atmospheric space on vertical ascendant or descendent trajectory under the influence of gravitational field. The name of this method is Popescu-Diaconu, after the names of the people that designed it. This method was used for the first time on the Mission 4b flight of the Helen 2 vehicle for the Google Lunar X Prize.Controversy
A number of people have speculated that the Popescu-Diaconu method can be reduced to the pendulum rocket fallacyPendulum Rocket Fallacy
Pendulum rocket fallacy is a common fundamental misunderstanding of the mechanics of rocket flight and how rockets remain on a stable trajectory. The first liquid-fuel rocket, constructed by Robert Goddard in 1926, differed significantly from modern rockets in that the rocket engine was at the top...
, and therefore cause the rocket to spin out of control once launched. ARCA have dismissed the claims saying that the nonrigid structure of the cables attached to points outside of the rockets prevent a pendulum like behavior of the system. The success of Mission 4b proved the viability of elastic articulation stability for launching rockets.
Demonstrator
This technological demonstrator is at 1:2 scale of that of the X PRIZE vehicle, named Orizont and it is the first rocket designed by ARCA Team. It is an unguided but self-stabilized rocket. On this vehicle and on the sub-assembly systems many constructive solutions were tested, especially composite materials fuel tanks. Almost the entire structure is made of composite materials, but also from aluminium aloys. This rocket was created to simulate an almost complete (unmanned) X Prize mission. Demonstrator 1 was also used in public exhibitions in order to attract more funds for ARCA projects.The old configuration used a liquid fuel rocket engine, designed to thrust 2,000 kgf during 60 sec. The fuel was: hydrogen
Hydrogen
Hydrogen is the chemical element with atomic number 1. It is represented by the symbol H. With an average atomic weight of , hydrogen is the lightest and most abundant chemical element, constituting roughly 75% of the Universe's chemical elemental mass. Stars in the main sequence are mainly...
peroxide 85% + T1. In the new configuration will use a hybrid engine with hydrogen peroxide 85% as an oxidizer, in combination with polyethylene as fuel.
Demonstrator 2
The technological demonstrator "2" is at 1:2.5 scale of that of the X PRIZE vehicle, named Orizont. ARCA started the work to this rocket in May 2003. The entire structure is made of composite materials. For this vehicle was created a whole launch complex, including the launch pad, the fuel transfer facility, etc. For this vehicle two propulsion configurations were proposed: monopropellant and hybrid.Demonstrator 2 was the starting point for the development of the successful Demonstrator 2B rocket. The first public display of this vehicle took place in Drăgășani
Dragasani
Drăgăşani is a city in Vâlcea County, Romania, near the right bank of the Olt river, and on the railway between Caracal and Râmnicu Vâlcea. The city is well known for the vineyards on the neighboring hills that produce some of the best Wallachian wines....
, on September 27, 2003.
Demonstrator 2B
Demonstrator 2B is a modified version of Demonstrator 2, equipped with the world's first reusable rocket engine made of composite materials. The main objective of this rocket was to test in flight the engine and the vehicle-launch pad interaction in order to gather more data for the Orizont vehicle construction. For the Demonstrator 2B launch was used the Demonstrator 2 launch pad which was modified (the length was increased to 18.2 m) and also the command panel and fuel transfer facility previously developed at ARCA.This rocket was the end of subscale systems tests at ARCA and the beginning of the Orizont vehicle's final phase of construction.
The Demonstrator 2B rocket was successfully launched on September 9, 2004. The measurements indicated that the launch parameters were: 1,000 m altitude, 630 km/h, 2,100 m range.
STRACAAT
In November 2005 ARCA succeeded to win a contract with the Research Ministry/Romanian Space Agency for the development of a rocket system with military applications. The contract was awarded for a period of 12 months.ARCA’s military application rocket was presented to the Bucharest International Fair on October 3, 2006. The rocket financed by the government through the Romanian Space Agency- “SECURITY” Program, has a length of 4.1 m and is designed to fly with Mach 1.02 at sea level. The maximum flight altitude is 6.000 m. The main purpose of this project is to create a target able to simulate low altitude/high speed aggressor vehicles.
BASMATES
High Altitude Commercial Solar Balloon for Scientific Equipment - BASMATES project consists in designing, constructing, launching and recovering a high altitude solar balloon and pressurized capsule, built for transporting scientific and commercial payload. This program started in 2007 and has a duration of 30 months.VECSS
The project "Vehicle for commercial operation of suborbital space – VECSS" consists in designing, accomplishing, lanunching and recovering from suborbital flight, of a vehicle intended for transportation of scientific commercial payload, to 100 km altitude. This program started in 2007 and has a duration of 36 months.Lunar X-Prize competition
The agency has committed itself as a competitor in the Google Lunar X-Prize. ARCA, the first European Union team to register for the competition, had a unique approach to completing their objective. The project is labeled "HAAS-ELE" and consists of a (high altitude) balloonHigh altitude balloon
High-altitude balloons are unmanned balloons, usually filled with helium or hydrogen that are released into the stratosphere, generally reaching between ....
-launch for a three-stage rocket.. The new approach consists of using a supersonic rocket plane to get the HAAS II and its payload to 16 km before launch.
Flights
Flight | Program | Category | Altitude/Destination | Ship configuration | Engine start | Status |
---|---|---|---|---|---|---|
First Flight | Demonstrator 2B | Unmanned | 1.000 m | Ground launched rocket | Yes | Completed |
Mission1 | Stabilo | Unmanned | 22.000 m | Carrier balloon + Crew cabin | No | Completed |
Mission2 | Stabilo | Unmanned | 22.000 m | Carrier balloon + Complete ship | No | Completed |
Mission3 | Lunar Project (Helen Test Rocket) | Unmanned | 100.000 m | Carrier balloon + Helen (3 stages) | Yes | Unsuccessful |
Mission4 | Lunar Project (Helen 2 Test Rocket) | Unmanned | 100.000 m | Carrier balloon + Helen 2 (2 stages) | Yes | Unsuccessful |
Mission4b | Lunar Project (Helen 2 Test Rocket) | Unmanned | 40.000 m | Carrier balloon + Helen 2 (1 stage) | Yes | Completed |
Mission5 | Avionics & TV Transmission Test | Manned | 5.000 m | Carrier balloon + Stage 1 (Helen 2) + ELL | No | Completed |
E-111 cabin test | Safety Features and Instruments Test | Unmanned | 10.000 m | E-111 cabin | No | TBL 2011 |
E-111 flight test | Full Carrier Plane Test | Manned | 16.000 m (?) | E-111 | Yes | TBL 2012-2013 |
Moon Mission | X-Prize Flight | Manned E-111 / Unmanned HAAS | Lunar Surface | E-111 & HAAS II - ELL | Yes | TBL 2013 |