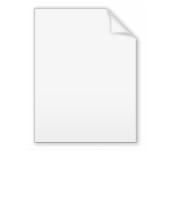
Total Productive Maintenance
Encyclopedia
Total productive maintenance (TPM) originated in Japan in 1971 as a method for improved machine availability through better utilization of maintenance and production resources.
Whereas in most production settings the operator is not viewed as a member of the maintenance team, in TPM the machine operator is trained to perform many of the day-to-day tasks of simple maintenance and fault-finding. Teams are created that include a technical expert (often an engineer or maintenance technician) as well as operators. In this setting the operators are enabled to understand the machinery and identify potential problems, righting them before they can impact production and by so doing, decrease downtime and reduce costs of production.
TPM is a critical adjunct to lean manufacturing
. If machine uptime is not predictable and if process capability
is not sustained, the process must keep extra stocks to buffer against this uncertainty and flow through the process will be interrupted. Unreliable uptime is caused by breakdowns or badly performed maintenance. Correct maintenance will allow uptime to improve and speed production through a given area allowing a machine to run at its designed capacity of production.
One way to think of TPM is "deterioration prevention": deterioration is what happens naturally to anything that is not "taken care of". For this reason many people refer to TPM as "total productive manufacturing" or "total process management". TPM is a proactive
approach that essentially aims to identify issues as soon as possible and plan to prevent any issues before occurrence. One motto is "zero error, zero work-related accident, and zero loss".
To implement TPM the production unit and maintenance unit should work jointly.
Original goal of total productive management:
“Continuously improve all operational conditions, within a production system;
by stimulating the daily awareness of all employees” (by Seiichi Nakajima, Japan, JIPM)
TPM focuses primarily on manufacturing (although its benefits are applicable to virtually any "process") and is the first methodology Toyota used to improve its global position (1950s). After TPM, the focus was stretched, and also suppliers and customers were involved (Supply Chain), this next methodology was called lean manufacturing
. This sheet gives an overview of TPM in its original form.
An accurate and practical implementation of TPM, will increase productivity within the total organization, where:
(1) .. a clear business culture is designed to continuously improve the efficiency of the total production system
(2) .. a standardized and systematic approach is used, where all losses are prevented and/or known.
(3) .. all departments, influencing productivity, will be involved to move from a reactive- to a predictive mindset.
(4) .. a transparent multidisciplinary organization is reaching zero losses.
(5) .. steps are taken as a journey, not as a quick menu.
Finally TPM will provide practical and transparent ingredients to reach operational excellence
.
The maintenance group performed equipment modification that would improve its reliability. These modifications were then made or incorporated into new equipment. The work of the maintenance group, with the support and input from operators and production engineers, is then to make changes that lead to maintenance prevention and increased quality through fewer defects and a reduction in scrap levels. Thus preventive maintenance along with maintenance prevention and maintainability improvement were grouped as productive maintenance. The aim of productive maintenance was to maximize plant and equipment effectiveness to achieve the optimum life cycle cost of production equipment.
Nippondenso already had quality circles which involved the employees in changes. Therefore, now, all employees took part in implementing Productive maintenance. Based on these developments Nippondenso was awarded the distinguished plant prize for developing and implementing TPM, by the Japanese Institute of Plant Engineers (JIPE). Thus Nippondenso of the Toyota group became the first company to obtain the TPM certifications.
Many companies struggle to implement TPM due to 2 main reasons. First is having insufficient knowledge and skills especially in understanding the linkages between the 8 Pillar-Activities in TPM http://www.tpmplus.co.uk/eight%20pillars.html. It does not help in that most TPM books are long on the theories but scanty on the implementation details. The second reason is that TPM requires more time, resources and efforts than most of these companies believe they can afford. A typical TPM implementation requires company-wide participation and full results can only be seen after 3 years and sometimes 5 years. The main reason for this long duration is due to the basic involvement and training required for Autonomous Maintenance participation where operators participate in the restoring the equipment to its original capability and condition and then improving the equipment.
An effective Fast-Track TPM Implementation Approach has been successful in a Paper Mill and Electronics Industries and documented. It circumvented this problem by assigning Project Teams to do Autonomous Maintenance for the AM Steps of 1) Initial Cleaning and 2) Eliminating Sources of Contamination and Improving Equipment Accessibility. Production Operators take over the Autonomous Maintenance after the AM Step 3 (Initial Maintenance Standards) has been established. This has been proven to reduce TPM implementation time by about 50%.
TPM identifies the 7 losses (types of waste) (muda), namely set-up and initial adjustment time, equipment breakdown time, idling and minor losses, speed (cycle time) losses, start-up quality losses, and in process quality losses, and then works systematically to eliminate them by making improvements (kaizen
). TPM has 8 pillars of activity, each being set to achieve a “zero” target. These 8 pillars are the following: focussed improvement (Kobetsu Kaizen); autonomous maintenance (Jishu Hozen); planned maintenance; training and education; early-phase management; quality maintenance (Hinshitsu Hozen); office TPM; and safety, health, and environment. Few organisation also add Pillars according to their Work Place like: Tools Management; Information Technology & more. The Base for the TPM Activity is 5S; Seiri (Sorting out the required or not required items); Seition (Systematic Arrangement of the required items); Seiso (Cleaniness); Seiketsu (Standardisation); Shitsuke (Self Discipline).
The Pillars & their details
a) Efficient Equipment Utilisation
b) Efficient Worker Utilisation
c) Efficient Material & Energy Utilisation.
1) focussed improvement (Kobetsu Kaizen) - Continuously even small steps of improvement.
2) Planned Maintenance - It focusses on Increasing Availability of Equipments & reducing Breakdown of Machines.
3) Initial Control - To establish the system to launch the production of new product & new equipment in a minimum run up time.
4) Education & Training - Formation of Autonomous workers who have skill & technique for autonomous maintenance.
5) Autonomous Maintenance (Jishu Hozen) - It means "Maintaining one's equipment by oneself". There are 7 Steps in & Activities of Jishu Hozen.
6) Quality Maintenance (Hinshitsu Hozen) - Quality Maintenance is establishment of machine conditions that will not allow the occurrence of defects & control of such conditions is requored to sustain Zero Defect.
7) Office TPM - To make an efficient working office that eliminate losses.
8) Safety, Hygiene & Environment - The main role of SHE (Safety, Hygiene & Environment) is to create Safe & healthy work place where accidents do not occur, uncover & improve hazardous areas & do activities that preserve environment.
Other Pillars Like:
Tools Management - To increase the availability of Equipment by reducing Tool Resetting Time, To reduce Tool Consumption Cost & to increase the tool life.
TPM success measurement - A set of performance metrics which is considered to fit well in a lean manufacturing/TPM environment is overall equipment effectiveness
, or OEE. For advanced TPM world class practitioners, the OEE cannot be converted to costs using Target Costing Management (TCM) OEE measurements are used as a guide to the potential improvement that can be made to an equipment. and by identifying which of the 6 losses is the greater, then the techniques applicable to that type of loss. Consistent application of the applicable improvement techniques to the sources of major losses will positively impact the performance of that equipment.
Using a criticality analysis across the factory should identify which equipments should be improved first, also to gain the quickest overall factory performance.
The use of Cost Deployment is quite rare, but can be very useful in identifying the priority for selective TPM deployment.
..
Steps to start TPM are
Whereas in most production settings the operator is not viewed as a member of the maintenance team, in TPM the machine operator is trained to perform many of the day-to-day tasks of simple maintenance and fault-finding. Teams are created that include a technical expert (often an engineer or maintenance technician) as well as operators. In this setting the operators are enabled to understand the machinery and identify potential problems, righting them before they can impact production and by so doing, decrease downtime and reduce costs of production.
TPM is a critical adjunct to lean manufacturing
Lean manufacturing
Lean manufacturing, lean enterprise, or lean production, often simply, "Lean," is a production practice that considers the expenditure of resources for any goal other than the creation of value for the end customer to be wasteful, and thus a target for elimination...
. If machine uptime is not predictable and if process capability
Process capability
A process is a unique combination of tools, materials, methods, and people engaged in producing a measurable output; for example a manufacturing line for machine parts...
is not sustained, the process must keep extra stocks to buffer against this uncertainty and flow through the process will be interrupted. Unreliable uptime is caused by breakdowns or badly performed maintenance. Correct maintenance will allow uptime to improve and speed production through a given area allowing a machine to run at its designed capacity of production.
One way to think of TPM is "deterioration prevention": deterioration is what happens naturally to anything that is not "taken care of". For this reason many people refer to TPM as "total productive manufacturing" or "total process management". TPM is a proactive
ProActive
ProActive is Java grid middleware for parallel, distributed, and multi-threaded computing. It is developed by the OW2 Consortium, including INRIA, CNRS, University of Nice Sophia Antipolis, and ActiveEon...
approach that essentially aims to identify issues as soon as possible and plan to prevent any issues before occurrence. One motto is "zero error, zero work-related accident, and zero loss".
Introduction
TPM is a maintenance process developed for improving productivity by making processes more reliable and less wasteful.TPM is an extension of TQM(Total Quality Management). The objective of TPM is to maintain the plant or equipment in good condition without interfering the daily process. To achieve this objective, preventive and predictive maintenance is required. By following the philosophy of TPM we can minimize the unexpected failure of the equipment.To implement TPM the production unit and maintenance unit should work jointly.
Original goal of total productive management:
“Continuously improve all operational conditions, within a production system;
by stimulating the daily awareness of all employees” (by Seiichi Nakajima, Japan, JIPM)
TPM focuses primarily on manufacturing (although its benefits are applicable to virtually any "process") and is the first methodology Toyota used to improve its global position (1950s). After TPM, the focus was stretched, and also suppliers and customers were involved (Supply Chain), this next methodology was called lean manufacturing
Lean manufacturing
Lean manufacturing, lean enterprise, or lean production, often simply, "Lean," is a production practice that considers the expenditure of resources for any goal other than the creation of value for the end customer to be wasteful, and thus a target for elimination...
. This sheet gives an overview of TPM in its original form.
An accurate and practical implementation of TPM, will increase productivity within the total organization, where:
(1) .. a clear business culture is designed to continuously improve the efficiency of the total production system
(2) .. a standardized and systematic approach is used, where all losses are prevented and/or known.
(3) .. all departments, influencing productivity, will be involved to move from a reactive- to a predictive mindset.
(4) .. a transparent multidisciplinary organization is reaching zero losses.
(5) .. steps are taken as a journey, not as a quick menu.
Finally TPM will provide practical and transparent ingredients to reach operational excellence
Operational excellence
Operational Excellence is a philosophy of leadership, teamwork and problem solving resulting in continuous improvement throughout the organization by focusing on the needs of the customer, empowering employees, and optimizing existing activities in the process....
.
History
TPM is an evolving process, starting from a Japanese idea that can be traced back to 1951, when preventive maintenance was introduced into Japan from the USA (Deming). Nippondenso, part of Toyota, was the first company in Japan to introduce plant wide preventive maintenance in 1960. In preventive maintenance operators produced goods using machines and the maintenance group was dedicated to the work of maintaining those machines. However with the high level of automation of Nippondenso, maintenance became a problem as so many more maintenance personnel were now required. So the management decided that much of the routine maintenance of equipment would now be carried out by the operators themselves. (Autonomous Maintenance, one of the features of TPM is more cost effective to use as the operator (compared to a highly skilled engineer) is on a lower pay rate. This is not to reduce costs, however; the operator has a better understanding of the how the equipment works on a daily basis, can tell if an issue is appearing, can tell if quality is decreasing, and, through constant learning, is allowed to follow a career path to a better job. The maintenance group then focused only on more complex problems and project work for long term upgrades.The maintenance group performed equipment modification that would improve its reliability. These modifications were then made or incorporated into new equipment. The work of the maintenance group, with the support and input from operators and production engineers, is then to make changes that lead to maintenance prevention and increased quality through fewer defects and a reduction in scrap levels. Thus preventive maintenance along with maintenance prevention and maintainability improvement were grouped as productive maintenance. The aim of productive maintenance was to maximize plant and equipment effectiveness to achieve the optimum life cycle cost of production equipment.
Nippondenso already had quality circles which involved the employees in changes. Therefore, now, all employees took part in implementing Productive maintenance. Based on these developments Nippondenso was awarded the distinguished plant prize for developing and implementing TPM, by the Japanese Institute of Plant Engineers (JIPE). Thus Nippondenso of the Toyota group became the first company to obtain the TPM certifications.
Implementation
TPM has basically 3 goals - Zero Product Defects, Zero Equipment Unplanned Failures and Zero Accidents. It sets out to achieve these goals by Gap Analysis of previous historical records of Product Defects, Equipment Failures and Accidents. Then through a clear understanding of this Gap Analysis (Fishbone Cause-Effect Analysis, Why-Why Cause-Effect Analysis, and P-M Analysis) plan a physical investigation to discover new latent fuguai (slight deterioration) during the first step in TPM Autonomous Maintenance called "Initial Cleaning".Many companies struggle to implement TPM due to 2 main reasons. First is having insufficient knowledge and skills especially in understanding the linkages between the 8 Pillar-Activities in TPM http://www.tpmplus.co.uk/eight%20pillars.html. It does not help in that most TPM books are long on the theories but scanty on the implementation details. The second reason is that TPM requires more time, resources and efforts than most of these companies believe they can afford. A typical TPM implementation requires company-wide participation and full results can only be seen after 3 years and sometimes 5 years. The main reason for this long duration is due to the basic involvement and training required for Autonomous Maintenance participation where operators participate in the restoring the equipment to its original capability and condition and then improving the equipment.
An effective Fast-Track TPM Implementation Approach has been successful in a Paper Mill and Electronics Industries and documented. It circumvented this problem by assigning Project Teams to do Autonomous Maintenance for the AM Steps of 1) Initial Cleaning and 2) Eliminating Sources of Contamination and Improving Equipment Accessibility. Production Operators take over the Autonomous Maintenance after the AM Step 3 (Initial Maintenance Standards) has been established. This has been proven to reduce TPM implementation time by about 50%.
TPM identifies the 7 losses (types of waste) (muda), namely set-up and initial adjustment time, equipment breakdown time, idling and minor losses, speed (cycle time) losses, start-up quality losses, and in process quality losses, and then works systematically to eliminate them by making improvements (kaizen
Kaizen
, Japanese for "improvement", or "change for the better" refers to philosophy or practices that focus upon continuous improvement of processes in manufacturing, engineering, game development, and business management. It has been applied in healthcare, psychotherapy, life-coaching, government,...
). TPM has 8 pillars of activity, each being set to achieve a “zero” target. These 8 pillars are the following: focussed improvement (Kobetsu Kaizen); autonomous maintenance (Jishu Hozen); planned maintenance; training and education; early-phase management; quality maintenance (Hinshitsu Hozen); office TPM; and safety, health, and environment. Few organisation also add Pillars according to their Work Place like: Tools Management; Information Technology & more. The Base for the TPM Activity is 5S; Seiri (Sorting out the required or not required items); Seition (Systematic Arrangement of the required items); Seiso (Cleaniness); Seiketsu (Standardisation); Shitsuke (Self Discipline).
The Pillars & their details
a) Efficient Equipment Utilisation
b) Efficient Worker Utilisation
c) Efficient Material & Energy Utilisation.
1) focussed improvement (Kobetsu Kaizen) - Continuously even small steps of improvement.
2) Planned Maintenance - It focusses on Increasing Availability of Equipments & reducing Breakdown of Machines.
3) Initial Control - To establish the system to launch the production of new product & new equipment in a minimum run up time.
4) Education & Training - Formation of Autonomous workers who have skill & technique for autonomous maintenance.
5) Autonomous Maintenance (Jishu Hozen) - It means "Maintaining one's equipment by oneself". There are 7 Steps in & Activities of Jishu Hozen.
6) Quality Maintenance (Hinshitsu Hozen) - Quality Maintenance is establishment of machine conditions that will not allow the occurrence of defects & control of such conditions is requored to sustain Zero Defect.
7) Office TPM - To make an efficient working office that eliminate losses.
8) Safety, Hygiene & Environment - The main role of SHE (Safety, Hygiene & Environment) is to create Safe & healthy work place where accidents do not occur, uncover & improve hazardous areas & do activities that preserve environment.
Other Pillars Like:
Tools Management - To increase the availability of Equipment by reducing Tool Resetting Time, To reduce Tool Consumption Cost & to increase the tool life.
TPM success measurement - A set of performance metrics which is considered to fit well in a lean manufacturing/TPM environment is overall equipment effectiveness
Overall equipment effectiveness
Overall equipment effectiveness is a hierarchy of metrics which evaluates and indicates how effectively a manufacturing operation is utilized. The results are stated in a generic form which allows comparison between manufacturing units in differing industries...
, or OEE. For advanced TPM world class practitioners, the OEE cannot be converted to costs using Target Costing Management (TCM) OEE measurements are used as a guide to the potential improvement that can be made to an equipment. and by identifying which of the 6 losses is the greater, then the techniques applicable to that type of loss. Consistent application of the applicable improvement techniques to the sources of major losses will positively impact the performance of that equipment.
Using a criticality analysis across the factory should identify which equipments should be improved first, also to gain the quickest overall factory performance.
The use of Cost Deployment is quite rare, but can be very useful in identifying the priority for selective TPM deployment.
..
Steps to start TPM are
- Management should learn the philosophy.
- Management must promote the philosophy.
- Training for all the employees.
- Identify the areas where improvement are needed.
- Make an implementation plan.
- Form an autonomous group.
See also
- Six sigmaSix SigmaSix Sigma is a business management strategy originally developed by Motorola, USA in 1986. , it is widely used in many sectors of industry.Six Sigma seeks to improve the quality of process outputs by identifying and removing the causes of defects and minimizing variability in manufacturing and...
- Total quality managementTotal Quality ManagementTotal quality management or TQM is an integrative philosophy of management for continuously improving the quality of products and processes....
- Lean manufacturingLean manufacturingLean manufacturing, lean enterprise, or lean production, often simply, "Lean," is a production practice that considers the expenditure of resources for any goal other than the creation of value for the end customer to be wasteful, and thus a target for elimination...
- Statistical Process ControlStatistical process controlStatistical process control is the application of statistical methods to the monitoring and control of a process to ensure that it operates at its full potential to produce conforming product. Under SPC, a process behaves predictably to produce as much conforming product as possible with the least...