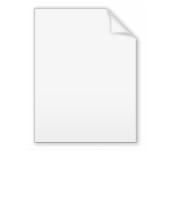
Superplastic forming
Encyclopedia
Superplastic forming is a metalworking
process for forming sheet metal
. It works upon the theory of superplasticity
, which means that a material can elongate beyond 100% of its original size.
, blow forming, and vacuum forming
; it may also be deep drawn.
. It also does not suffer from springback or residual stress
es. Products can also be made larger to eliminate assemblies or reduce weight, which is critical in aerospace
applications. Lower strength required and less tooling costs.
The biggest disadvantage is its slow forming rate. Cycle times vary from two minutes to two hours, therefore it is usually used on lower volume products. Also materials must not be superplastic at service temperatures. More recently, superplasticity has been used to form parts for automotive applications.
Metalworking
Metalworking is the process of working with metals to create individual parts, assemblies, or large scale structures. The term covers a wide range of work from large ships and bridges to precise engine parts and delicate jewelry. It therefore includes a correspondingly wide range of skills,...
process for forming sheet metal
Sheet metal
Sheet metal is simply metal formed into thin and flat pieces. It is one of the fundamental forms used in metalworking, and can be cut and bent into a variety of different shapes. Countless everyday objects are constructed of the material...
. It works upon the theory of superplasticity
Superplasticity
In materials science, superplasticity is a state in which solid crystalline material is deformed well beyond its usual breaking point, usually over about 200% during tensile deformation. Such a state is usually achieved at high homologous temperature, typically half the absolute melting point. ...
, which means that a material can elongate beyond 100% of its original size.
Process
To begin with, the material must have an ultra-fine grain size. It is then heated up to promote superplasticity. For titanium this is around 900 °C (1,652 °F) and for aluminium it is between 450–520 °C. In this state the material is not very strong so processes that are usually used on plastics can be applied, such as: thermoformingThermoforming
Thermoforming is a manufacturing process where a plastic sheet is heated to a pliable forming temperature, formed to a specific shape in a mold, and trimmed to create a usable product...
, blow forming, and vacuum forming
Vacuum forming
Vacuum forming, commonly known as vacuuforming, is a simplified version of thermoforming, whereby a sheet of plastic is heated to a forming temperature, stretched onto or into a single-surface mold , and held against the mold by applying vacuum between the mold surface and the sheet.The vacuum...
; it may also be deep drawn.
Advantages & disadvantages
The major advantage of this process is that it can form large and complex workpieces in one operation. The finished product has excellent precision and a fine surface finishSurface finish
Surface finish, also known as surface texture, is the characteristics of a surface. It has three components: lay, surface roughness, and waviness.-Lay:...
. It also does not suffer from springback or residual stress
Residual stress
Residual stresses are stresses that remain after the original cause of the stresses has been removed. They remain along a cross section of the component, even without the external cause. Residual stresses occur for a variety of reasons, including inelastic deformations and heat treatment...
es. Products can also be made larger to eliminate assemblies or reduce weight, which is critical in aerospace
Aerospace
Aerospace comprises the atmosphere of Earth and surrounding space. Typically the term is used to refer to the industry that researches, designs, manufactures, operates, and maintains vehicles moving through air and space...
applications. Lower strength required and less tooling costs.
The biggest disadvantage is its slow forming rate. Cycle times vary from two minutes to two hours, therefore it is usually used on lower volume products. Also materials must not be superplastic at service temperatures. More recently, superplasticity has been used to form parts for automotive applications.