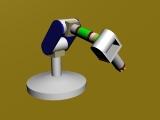
Serial manipulator
Encyclopedia
Serial manipulators are by far the most common industrial robots. Often they have an anthropomorphic
mechanical arm structure, i.e. a serial chain of rigid links, connected by (mostly revolute
) joint
s, forming a "shoulder", an "elbow", and a "wrist".
Their main advantage is their large workspace
with respect to their own volume and occupied floor space.
Their main disadvantages are
From rigid body motion it is known that it requires at least six degrees of freedom
to place a manipulated object in an arbitrary position and orientation in the workspace of the robot. Hence, many serial robots have six joints.
However the most popular application for serial robots in today's industry is pick-and-place assembly. Since this only requires four degrees of freedom, special assembly
robots of the so called SCARA
type are built.
In its most general form, a serial robot consists of a number of rigid links connected with joints. Simplicity considerations in manufacturing and control have led to robots with only revolute or prismatic joint
s and orthogonal, parallel and/or intersecting joint axes (instead of arbitrarily placed joint axes).
Donald L. Pieper derived the first practically relevant result in this context, referred to as 321 kinematic structure
:
The inverse kinematics of serial manipulators with six revolute joints, and with three consecutive joints intersecting, can be solved in closed-form, i.e. analytically
This result had a tremendous influence on the design of industrial robots.
The dextrous workspace consists of the points of the reachable workspace where the robot can generate velocities that span the complete tangent space at that point, i.e., it can translate the manipulated object with three degrees of freedom, and rotate the object with three degrees of rotation freedom.
The relationships between joint space and Cartesian space coordinates of the object held by the robot are in general multiple-valued: the same pose can be reached by the serial arm in different ways, each with a different set of joint coordinates. Hence the reachable workspace of the robot is divided in configurations (also called assembly modes), in which the kinematic relationships are locally one-to-one.
Serial robots with less than six independent joints are always singular in the sense that they can never span a six-dimensional twist space. This is often called an architectural singularity.
A singularity is usually not an isolated point in the workspace of the robot, but a sub-manifold.
Anthropomorphism
Anthropomorphism is any attribution of human characteristics to animals, non-living things, phenomena, material states, objects or abstract concepts, such as organizations, governments, spirits or deities. The term was coined in the mid 1700s...
mechanical arm structure, i.e. a serial chain of rigid links, connected by (mostly revolute
Revolute joint
A revolute joint is a one degree of freedom kinematic pair used in mechanisms. Revolute joints provide single-axis rotation function used in many places such as door hinges, folding mechanisms, and other uni-axial rotation devices. -See also:* Cylindrical joint* Kinematics* Degrees of freedom *...
) joint
Joint (disambiguation)
Joint is a location where two bones make contact.Joint may also refer to:- Physics :* Joint , a connection between two rigid bodies which allows movement with one or more degrees of freedom between them...
s, forming a "shoulder", an "elbow", and a "wrist".
Their main advantage is their large workspace
Workspace
Workspace is a term used in various branches of engineering and economic development.-Business development:Workspace refers to small premises provided, often by local authorities or economic development agencies, to help new businesses to establish themselves...
with respect to their own volume and occupied floor space.
Their main disadvantages are
- the low stiffness inherent to an open kinematic structure
- errors are accumulated and amplified from link to link
- the fact that they have to carry and move the large weight of most of the actuators
- the relatively low effective load that they can manipulate
From rigid body motion it is known that it requires at least six degrees of freedom
Degrees of freedom (engineering)
In mechanics, degrees of freedom are the set of independent displacements and/or rotations that specify completely the displaced or deformed position and orientation of the body or system...
to place a manipulated object in an arbitrary position and orientation in the workspace of the robot. Hence, many serial robots have six joints.
However the most popular application for serial robots in today's industry is pick-and-place assembly. Since this only requires four degrees of freedom, special assembly
Assembly line
An assembly line is a manufacturing process in which parts are added to a product in a sequential manner using optimally planned logistics to create a finished product much faster than with handcrafting-type methods...
robots of the so called SCARA
SCARA
The SCARA acronym stands for Selective Compliant Assembly Robot Arm or Selective Compliant Articulated Robot Arm.In 1981, Sankyo Seiki, Pentel and NEC presented a completely new concept for assembly robots. The robot was developed under the guidance of Hiroshi Makino, a professor at the University...
type are built.
Structure
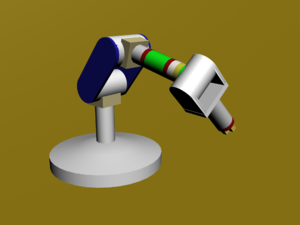
Prismatic joint
A prismatic joint provides a linear sliding movement between two bodies, and is often called a slider, as in the slider-crank linkage. A prismatic joint is formed with a polygonal cross-section to resist rotation...
s and orthogonal, parallel and/or intersecting joint axes (instead of arbitrarily placed joint axes).
Donald L. Pieper derived the first practically relevant result in this context, referred to as 321 kinematic structure
321 kinematic structure
321 kinematic structure is a design method for robotic arms , invented by Donald L. Pieper and used in most commercially produced robotic arms. The inverse kinematics of serial manipulators with six revolute joints, and with three consecutive joints intersecting, can be solved in closed form, i.e...
:
The inverse kinematics of serial manipulators with six revolute joints, and with three consecutive joints intersecting, can be solved in closed-form, i.e. analytically
This result had a tremendous influence on the design of industrial robots.
Kinematics
The position and orientation of a robot's end effector are derived from the joint positions by means of a geometric model of the robot arm. For serial robots, the mapping from joint positions to end-effector pose is easy, the inverse mapping is more difficult. Therefore, most industrial robots have special designs that reduce the complexity of the inverse mapping.Workspace
The reachable workspace of a robot's end-effector is the manifold of reachable frames.The dextrous workspace consists of the points of the reachable workspace where the robot can generate velocities that span the complete tangent space at that point, i.e., it can translate the manipulated object with three degrees of freedom, and rotate the object with three degrees of rotation freedom.
The relationships between joint space and Cartesian space coordinates of the object held by the robot are in general multiple-valued: the same pose can be reached by the serial arm in different ways, each with a different set of joint coordinates. Hence the reachable workspace of the robot is divided in configurations (also called assembly modes), in which the kinematic relationships are locally one-to-one.
Singularities
At a singularity the end-effector loses one or more degrees of twist freedom (instantaneously, the end-effector cannot move in these directions).Serial robots with less than six independent joints are always singular in the sense that they can never span a six-dimensional twist space. This is often called an architectural singularity.
A singularity is usually not an isolated point in the workspace of the robot, but a sub-manifold.
Redundancies
A manipulator with 7 joints is called redundant if it exceeds this number up to n joints, it is called hyper-redundant. An example of such a robot is Robotics Design's ANAT AMI-100, an arm with a combined SCARA-articulated configuration.Manufacturers
- ABB Robotics
- Adept TechnologyAdept TechnologyAdept Technology, Inc. is a multinational corporation with headquarters in Pleasanton, California . The company focuses on industrial automation and robotics, including software and vision guidance. Adept has offices throughout the United States as well as in Dortmund, Germany, Paris, France, and...
- ComauComauComau is part of "Fiat Group". Among many manufacturing solutions, it is specialized in welding robots. Comau's C3G controller was the first controller capable of multi-arm syncronization with up to 4 six-axis arms moving syncronized...
- FANUC RoboticsFANUC RoboticsFANUC or is a Japanese electromechanical manufacturer specializing in robotics. It is one of the largest maker of industrial robots in the world. It is part of the Furukawa Group. FANUC had its beginnings as part of Fujitsu developing numerical control and servo systems...
- KUKAKUKAKUKA is a leading German producer of industrial robots for a variety of industries - from automotive and fabricated metals to food and plastics...
- MitsubishiMitsubishiThe Mitsubishi Group , Mitsubishi Group of Companies, or Mitsubishi Companies is a Japanese multinational conglomerate company that consists of a range of autonomous businesses which share the Mitsubishi brand, trademark and legacy...
- MotomanMotomanMotoman Inc. is an American subsidiary of the Japanese company Yaskawa Electric Corporation.Motoman produces robotic automation for industry and robotic applications, including arc welding, assembly, clean room, coating, dispensing, material cutting , materials handling, materials removal, and spot...
- StaubliStäubliStäubli is an international mechatronics company, primarily known for its textile machinery, connectors and robotics products.-History:...
- Robotics DesignRobotics DesignRobotics Design Inc. is a company that designs and builds modular robots, founded and incorporated in Montreal, Quebec, Canada in 1997. The company produces mobile robots, robotic manipulators and manual arms as well as custom solutions using modular robotic technology...