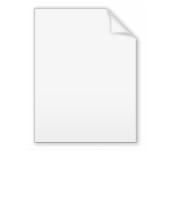
Rustproofing
Encyclopedia
Rustproofing is a condition of preservation or protection, by a process or treatment
Surface finishing
Surface finishing is a broad range of industrial processes that alter the surface of a manufactured item to achieve a certain property. Finishing processes may be employed to: improve appearance, adhesion or wettability, solderability, corrosion resistance, tarnish resistance, chemical resistance,...
whereby the rate at which objects made of iron
Iron
Iron is a chemical element with the symbol Fe and atomic number 26. It is a metal in the first transition series. It is the most common element forming the planet Earth as a whole, forming much of Earth's outer and inner core. It is the fourth most common element in the Earth's crust...
and/or steel
Steel
Steel is an alloy that consists mostly of iron and has a carbon content between 0.2% and 2.1% by weight, depending on the grade. Carbon is the most common alloying material for iron, but various other alloying elements are used, such as manganese, chromium, vanadium, and tungsten...
begin to rust
Rust
Rust is a general term for a series of iron oxides. In colloquial usage, the term is applied to red oxides, formed by the reaction of iron and oxygen in the presence of water or air moisture...
is reduced. The degradation
Chemical decomposition
Chemical decomposition, analysis or breakdown is the separation of a chemical compound into elements or simpler compounds. It is sometimes defined as the exact opposite of a chemical synthesis. Chemical decomposition is often an undesired chemical reaction...
in the long term can not be stopped completely, unless the rustproofing is periodically renewed. The term is particularly used for the automobile industry.
In the factory
In the factory, car bodies have chemicals, typically phosphatePhosphate conversion coating
Phosphate coatings are used on steel parts for corrosion resistance, lubricity, or as a foundation for subsequent coatings or painting. It serves as a conversion coating in which a dilute solution of phosphoric acid and phosphate salts is applied via spraying or immersion and chemically reacts with...
s, applied often using electrically charged systems so that layers of protection are added to the metal body. Some firms galvanize
Galvanization
Galvanization is the process of applying a protective zinc coating to steel or iron, in order to prevent rusting. The term is derived from the name of Italian scientist Luigi Galvani....
part or all of their car bodies. This is done before the primer
Primer (paint)
A primer is a preparatory coating put on materials before painting. Priming ensures better adhesion of paint to the surface, increases paint durability, and provides additional protection for the material being painted.-When primers are used:...
coat of paint is applied. If a car is body-on-frame
Body-on-frame
Body-on-frame is an automobile construction method. Mounting a separate body to a rigid frame that supports the drivetrain was the original method of building automobiles, and its use continues to this day. The original frames were made of wood , but steel ladder frames became common in the 1930s...
, then the frame (chassis) and its attachments must also be rustproofed. Paint is the final part of the rustproofing barrier between the body shell (apart from on the underside) and the atmosphere. On the underside an underseal
Underseal
Underseal is a thick resilient coating applied to the underbody or chassis of an automobile to protect against impact damage from small stones, which would rapidly chip ordinary paint, allowing rusting to begin....
, a rubberised or PVC
PVC
Polyvinyl chloride is a plastic.PVC may also refer to:*Param Vir Chakra, India's highest military honor*Peripheral venous catheter, a small, flexible tube placed into a peripheral vein in order to administer medication or fluids...
-based coating is sprayed on. These products will be breached eventually and can lead to unseen corrosion that spreads underneath the underseal. 1960s and '70s rubberised underseal can become brittle on older cars and is particularly liable to this.
Aftermarket
Aftermarket kits are available to apply rustproofing compounds both to external surfaces and inside enclosed sections, for example sills/rocker panels (see monocoqueMonocoque
Monocoque is a construction technique that supports structural load by using an object's external skin, as opposed to using an internal frame or truss that is then covered with a non-load-bearing skin or coachwork...
), through either existing or specially drilled holes. The compounds are usually wax-based and applied by pressure spray, but phosphoric acid
Phosphoric acid
Phosphoric acid, also known as orthophosphoric acid or phosphoric acid, is a mineral acid having the chemical formula H3PO4. Orthophosphoric acid molecules can combine with themselves to form a variety of compounds which are also referred to as phosphoric acids, but in a more general way...
can also be painted on already rusted areas. Loose or thick rust must be removed before anti-rust wax
Wax
thumb|right|[[Cetyl palmitate]], a typical wax ester.Wax refers to a class of chemical compounds that are plastic near ambient temperatures. Characteristically, they melt above 45 °C to give a low viscosity liquid. Waxes are insoluble in water but soluble in organic, nonpolar solvents...
like Waxoyl
Waxoyl
Waxoyl is a rust-preventative fluid used first in Europe where it has been used for decades, and currently distributed in the United States...
or a similar product is used. Wax does not penetrate spot welded seams or thick rust well. A penetrating anti-rust product like WD-40
WD-40
WD-40 is the trademark name of a United States-made water-displacing spray. It was developed in 1953 by Norm Larsen, founder of the Rocket Chemical Company, San Diego, California. It was originally designed to repel water and prevent corrosion, and later was found to have numerous household...
followed by anti-rust wax can be more effective. Aftermarket "underseals" can also be applied. These are often bitumen-based products that do not dry and harden, so they cannot become brittle. They contain anti-rust chemicals similar to those in anti-rust waxes. They are particularly useful in high-impact areas like wheel arches. Petroleum based rust-inhibitors provide several benefits, including the ability to creep over metal, covering missed areas. Additionally, a petroleum, solvent-free rust inhibitor remains on the metal surface, sealing it from rust accelerating water and oxygen. Other benefits of petroleum based rust protection include the self-healing properties that come naturally to oils, which helps undercoatings to resist abrasion caused by road sand and other debris. The disadvantage of using a petroleum based coating is the film left over on surfaces, rendering these products to messy for exterior application and unsafe in areas where it can be slipped on.
Rust removal
- Main article: Rust removal
The chemicals which are sold in bottles to paint on rust, and which react with the rust to destroy it, turning it blue/black, are not called rustproofing but "rust killers" and need to be used as part of a paint system.
Car bodies
Car body corrosion was a particular problem from the 1950s to the 1980s when cars moved to monocoqueMonocoque
Monocoque is a construction technique that supports structural load by using an object's external skin, as opposed to using an internal frame or truss that is then covered with a non-load-bearing skin or coachwork...
or uni-body construction from a separate chassis frame made from thick steel. This relied on the shaped body panels designed on newly available computers and the integrity of the body shell for strength. Unfortunately the design of corrosion prevention had not kept pace with this new technology.
Rate of rusting
The rate at which vehicles rust is dependent upon:- The local climate and use of ice-melting chemicals (saltSaltIn chemistry, salts are ionic compounds that result from the neutralization reaction of an acid and a base. They are composed of cations and anions so that the product is electrically neutral...
) upon the roads. - The particular process of rustproofing used.
- The design of "rust traps" (nooks and crannies that collect road dirt and water).
- The plastic/under-seal protection on the car underside.
- The thickness and composition of the metal, for example, some dissimilar metals can accelerate the rusting of steel bodywork through electrolytic corrosion.
- Exposure to salt water in the case of boats, which strips off the protective paint and causes rust much quicker than ordinary rain water would.
Technological Advancement in Metallurgy
Stainless SteelStainless steel
In metallurgy, stainless steel, also known as inox steel or inox from French "inoxydable", is defined as a steel alloy with a minimum of 10.5 or 11% chromium content by mass....
, also known as inox steel does not stain, corrode, or rust as easily as ordinary steel.
Pierre Berthier, a Frenchman, was the first to notice the rust-resistant properties of mixing chromium with alloys in 1821, which led to new metal treating and metallurgy processes and eventually the creation of useable stainless steel.
See also
- RustRustRust is a general term for a series of iron oxides. In colloquial usage, the term is applied to red oxides, formed by the reaction of iron and oxygen in the presence of water or air moisture...
- CorrosionCorrosionCorrosion is the disintegration of an engineered material into its constituent atoms due to chemical reactions with its surroundings. In the most common use of the word, this means electrochemical oxidation of metals in reaction with an oxidant such as oxygen...
- Hot-dip galvanizingHot-dip galvanizingHot-dip galvanizing is a form of galvanization. It is the process of coating iron, steel, or aluminum with a thin zinc layer, by passing the metal through a molten bath of zinc at a temperature of around 860 °F...
- Pontypool japanPontypool japanPontypool japan is a name given to the process of japanning with the use of an oil varnish and heat which is credited to Thomas Allgood of Pontypool. In the late 17th century, during his search for a corrosion-resistant coating for iron, he developed a recipe that included asphaltum, linseed oil...
- TinningTinningTinning is the process of thinly coating sheets of wrought iron or steel with tin, and the resulting product is known as tinplate. It is most often used to prevent rust....
- Stainless SteelStainless steelIn metallurgy, stainless steel, also known as inox steel or inox from French "inoxydable", is defined as a steel alloy with a minimum of 10.5 or 11% chromium content by mass....
- Iron pillar of Delhi