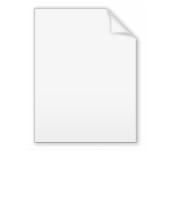
Roll slitting
Encyclopedia
Roll slitting, also known as log slitting, is a shearing
operation that cuts a large roll of material into narrower rolls. The log slitting terminology refers back to the olden days of saw mills when they would cut logs into smaller sections. They would also use these saw mills to cut iron rods into smaller sections; see slitting mill
. The multiple narrower strips of material are known as mults (short for multiple). By today's definition, slitting is a process in which a coil of material is cut down into a number of smaller coils of narrower measure. Potential workpieces are selectively thin (0.001 to 0.215 in.) and can be machined in sheet or roll form. Slitting is considered a practical alternative to other methods due to its high productivity and the versatility of materials it can manage.
s, straight, or circular blades are being used. Some blades cut through the material while others crush the material against a hard roll. Those are similar to knives and cut the material into narrow strips, which are called coils when being rewound. The cutting blades can be set to a desired width. Some machines have many blades to increase the options of cutting widths, others have just a single blade and can be set to a desired location. The slit material is being rewound on paper or plastic cores on the exit side of the machine.
The process is used because of its low cost and high precision for mass production. Some machines have a program that monitors the blades and sharpens the blades often to maintain the quality and precision of the cut. Depending on the industry and the product that is being slit these machine can run between 10m/min (special metal webs) and 5000 m/min (paper making process)
Examples of materials that can be cut this way are: adhesive tape, foam, rubber, paper products, foil, plastics (such as tarps and cling wrap), glass cloth, fabrics, release liner
and film.
, blades cannot be used. Instead a modified form of shearing is used. Two cylindrical rolls with matching ribs and grooves are used to cut a large roll into multiple narrower rolls. This continuous production process is very economical yet precise; usually more precise than most other cutting processes. However, the occurrence of rough or irregular edges known as burrs are commonplace on slit edges. Also, the geometry of these rolls is determined by specific tolerances in addition to the type of material and workpiece thickness.
Shearing (metalworking)
Shearing, also known as die cutting, is a process which cuts stock without the formation of chips or the use of burning or melting. Strictly speaking, if the cutting blades are straight the process is called shearing; if the cutting blades are curved then they are shearing-type operations...
operation that cuts a large roll of material into narrower rolls. The log slitting terminology refers back to the olden days of saw mills when they would cut logs into smaller sections. They would also use these saw mills to cut iron rods into smaller sections; see slitting mill
Slitting mill
The slitting mill was a watermill for slitting bars of iron into rods. The rods then were passed to nailers who made the rods into nails, by giving them a point and head....
. The multiple narrower strips of material are known as mults (short for multiple). By today's definition, slitting is a process in which a coil of material is cut down into a number of smaller coils of narrower measure. Potential workpieces are selectively thin (0.001 to 0.215 in.) and can be machined in sheet or roll form. Slitting is considered a practical alternative to other methods due to its high productivity and the versatility of materials it can manage.
Soft materials
Several methods are available for soft materials like plastic films and paper. Razor bladeRazor blade
Razor blade may refer to* A razor* The Razor Blade, a 1920s racing car* Razor blade steel, a type of steel originally designed specifically for razor blades...
s, straight, or circular blades are being used. Some blades cut through the material while others crush the material against a hard roll. Those are similar to knives and cut the material into narrow strips, which are called coils when being rewound. The cutting blades can be set to a desired width. Some machines have many blades to increase the options of cutting widths, others have just a single blade and can be set to a desired location. The slit material is being rewound on paper or plastic cores on the exit side of the machine.
The process is used because of its low cost and high precision for mass production. Some machines have a program that monitors the blades and sharpens the blades often to maintain the quality and precision of the cut. Depending on the industry and the product that is being slit these machine can run between 10m/min (special metal webs) and 5000 m/min (paper making process)
Examples of materials that can be cut this way are: adhesive tape, foam, rubber, paper products, foil, plastics (such as tarps and cling wrap), glass cloth, fabrics, release liner
Release liner
A Release liner is a paper or plastic based carrier web material, which is coated on one or two sides with a release agent, which provides a release effect against any type of a sticky material such as an adhesive or a mastic. Release liner are available in different colors, with or without...
and film.
Hard materials
For harder materials, such as sheet metalSheet metal
Sheet metal is simply metal formed into thin and flat pieces. It is one of the fundamental forms used in metalworking, and can be cut and bent into a variety of different shapes. Countless everyday objects are constructed of the material...
, blades cannot be used. Instead a modified form of shearing is used. Two cylindrical rolls with matching ribs and grooves are used to cut a large roll into multiple narrower rolls. This continuous production process is very economical yet precise; usually more precise than most other cutting processes. However, the occurrence of rough or irregular edges known as burrs are commonplace on slit edges. Also, the geometry of these rolls is determined by specific tolerances in addition to the type of material and workpiece thickness.