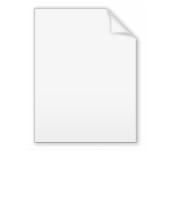
Process optimization
Encyclopedia
Process optimization is the discipline of adjusting a process so as to optimize some specified set of parameters without violating some constraint. The most common goals are minimizing cost, maximizing throughput, and/or efficiency. This is one of the major quantitative
tools in industrial decision making.
When optimizing a process, the goal is to maximize one or more of the process specifications, while keeping all others within their constraints.
The first step is to verify that the existing equipment is being used to its fullest advantage by examining operating data to identify equipment bottlenecks.
Operating procedures may vary widely from person-to-person or from shift-to-shift. Automation of the plant can help significantly. But automation will be of no help if the operators take control and run the plant in manual.
In a typical processing plant, such as a chemical plant
or oil refinery
, there are hundreds or even thousands of control loops. Each control loop is responsible for controlling one part of the process, such as maintaining a temperature, level, or flow.
If the control loop is not properly designed and tuned, the process runs below its optimum. The process will be more expensive to operate, and equipment will wear out prematurely. For each control loop to run optimally, identification of sensor, valve, and tuning problems is important. It has been well documented that over 35% of control loops typically have problems.
The process of continuously monitoring and optimizing the entire plant is sometimes called performance supervision.
Quantitative property
A quantitative property is one that exists in a range of magnitudes, and can therefore be measured with a number. Measurements of any particular quantitative property are expressed as a specific quantity, referred to as a unit, multiplied by a number. Examples of physical quantities are distance,...
tools in industrial decision making.
When optimizing a process, the goal is to maximize one or more of the process specifications, while keeping all others within their constraints.
Areas
Fundamentally, there are three parameters that can be adjusted to affect optimal performance. They are:- Equipment optimization
The first step is to verify that the existing equipment is being used to its fullest advantage by examining operating data to identify equipment bottlenecks.
- Operating procedures
Operating procedures may vary widely from person-to-person or from shift-to-shift. Automation of the plant can help significantly. But automation will be of no help if the operators take control and run the plant in manual.
- Control optimization
In a typical processing plant, such as a chemical plant
Chemical plant
A chemical plant is an industrial process plant that manufactures chemicals, usually on a large scale. The general objective of a chemical plant is to create new material wealth via the chemical or biological transformation and or separation of materials. Chemical plants use special equipment,...
or oil refinery
Oil refinery
An oil refinery or petroleum refinery is an industrial process plant where crude oil is processed and refined into more useful petroleum products, such as gasoline, diesel fuel, asphalt base, heating oil, kerosene, and liquefied petroleum gas...
, there are hundreds or even thousands of control loops. Each control loop is responsible for controlling one part of the process, such as maintaining a temperature, level, or flow.
If the control loop is not properly designed and tuned, the process runs below its optimum. The process will be more expensive to operate, and equipment will wear out prematurely. For each control loop to run optimally, identification of sensor, valve, and tuning problems is important. It has been well documented that over 35% of control loops typically have problems.
The process of continuously monitoring and optimizing the entire plant is sometimes called performance supervision.
See also
- Calculation of glass propertiesCalculation of glass propertiesThe calculation of glass properties is used to predict glass properties of interest or glass behavior under certain conditions without experimental investigation, based on past data and experience, with the intention to save time, material, financial, and environmental resources, or to gain...
, optimization of several properties - Deficit irrigationDeficit irrigationDeficit irrigation is a watering strategy that can be applied by different types of irrigation application methods. The correct application of DI requires thorough understanding of the yield response to water and of the economic impact of reductions in harvest...
to optimize water productivity - Metallurgical Process Optimization
- Process simulationProcess simulationProcess simulation is used for the design, development, analysis, and optimization of technical processes and is mainly applied to chemical plants and chemical processes, but also to power stations, and similar technical facilities.- Main principle :...
External links
- Tutorials on Process Optimization
- Reference TEXTBOOKS on Taguchi Methods
- TORSCHE Scheduling Toolbox for Matlab is a freely available toolbox of scheduling and graph algorithms.