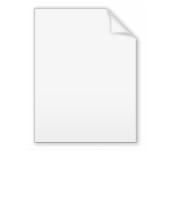
Peristaltic pump
Encyclopedia
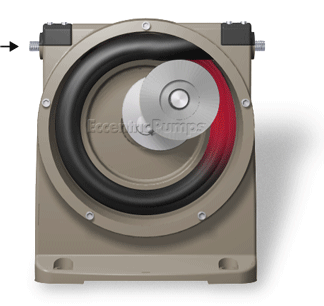
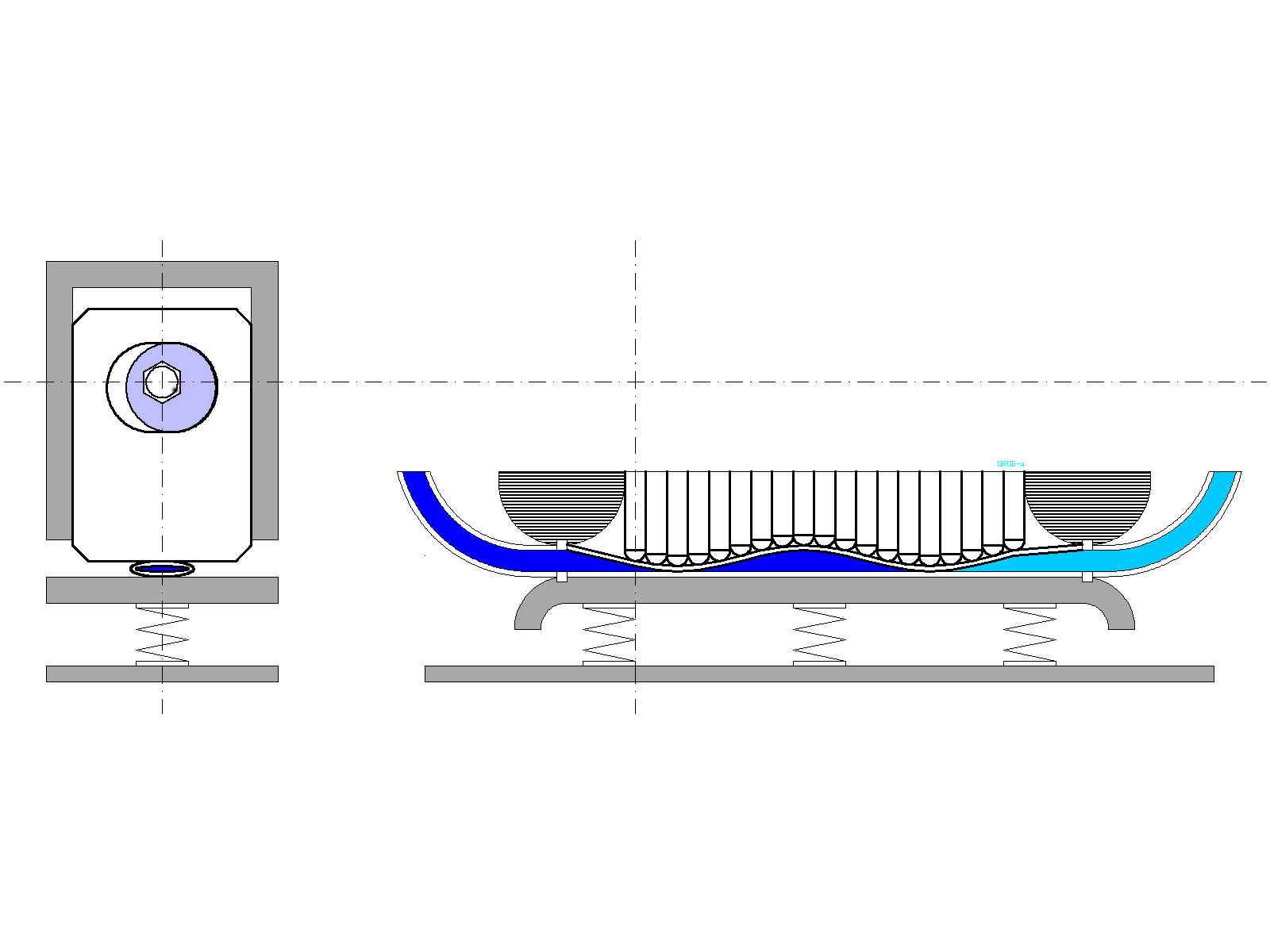
Pump
A pump is a device used to move fluids, such as liquids, gases or slurries.A pump displaces a volume by physical or mechanical action. Pumps fall into three major groups: direct lift, displacement, and gravity pumps...
used for pumping a variety of fluid
Fluid
In physics, a fluid is a substance that continually deforms under an applied shear stress. Fluids are a subset of the phases of matter and include liquids, gases, plasmas and, to some extent, plastic solids....
s. The fluid is contained within a flexible tube fitted inside a circular pump casing (though linear peristaltic pumps have been made). A rotor with a number of "rollers", "shoes" or "wipers" attached to the external circumference compresses the flexible tube. As the rotor turns, the part of tube under compression closes (or "occludes") thus forcing the fluid to be pumped to move through the tube. Additionally, as the tube opens to its natural state after the passing of the cam ("restitution" or "resilience") fluid flow is induced to the pump. This process is called peristalsis
Peristalsis
Peristalsis is a radially symmetrical contraction and relaxation of muscles which propagates in a wave down the muscular tube, in an anterograde fashion. In humans, peristalsis is found in the contraction of smooth muscles to propel contents through the digestive tract. Earthworms use a similar...
and used in many biological systems such as the gastrointestinal tract
Gastrointestinal tract
The human gastrointestinal tract refers to the stomach and intestine, and sometimes to all the structures from the mouth to the anus. ....
.
History
The peristaltic pump was first patented in the United States by Eugene Allen in 1881 (U.S. Patent number 249285). It was popularized by heart surgeon Dr. Michael DeBakeyMichael E. DeBakey
Michael Elias DeBakey was a world-renowned Lebanese-American cardiac surgeon, innovator, scientist, medical educator, and international medical statesman...
while he was a medical student in 1932.
Applications
Peristaltic pumps are typically used to pump clean/sterile or aggressive fluids because cross contamination with exposed pump components cannot occur. Some common applications include pumping IV fluids through an infusion device, aggressive chemicals, high solids slurries and other materials where isolation of the product from the environment, and the environment from the product, are critical. It is also used in heart-lung machineHeart-lung machine
Cardiopulmonary bypass is a technique that temporarily takes over the function of the heart and lungs during surgery, maintaining the circulation of blood and the oxygen content of the body. The CPB pump itself is often referred to as a heart–lung machine or "the pump"...
s to circulate blood during a bypass surgery
Bypass surgery
Bypass surgery refers to a class of surgeries involving rerouting a tubular body part.Types include:*Cardiopulmonary bypass*Partial ileal bypass surgery*Roux-en-Y gastric bypass surgery*Vascular bypass, e.g. Coronary artery bypass surgery...
as the pump does not cause significant hemolysis
Hemolysis
Hemolysis —from the Greek meaning "blood" and meaning a "loosing", "setting free" or "releasing"—is the rupturing of erythrocytes and the release of their contents into surrounding fluid...
.
Peristaltic pumps are also used in a wide variety of industrial applications. Their unique design makes them especially suited to pumping abrasives and viscous fluids.
Chemical compatibility
The pumped fluid contacts only the inside surface of the tubing thereby negating concern for other valves, O-rings or seals that might be incompatible with fluid being pumped. Therefore, only the composition of the tubing the eluent travels through is considered for chemical compatibility.The tubing needs to be elastomer
Elastomer
An elastomer is a polymer with the property of viscoelasticity , generally having notably low Young's modulus and high yield strain compared with other materials. The term, which is derived from elastic polymer, is often used interchangeably with the term rubber, although the latter is preferred...
ic to maintain the circular cross section after millions of cycles of squeezing in the pump. This requirement eliminates a variety of non-elastomeric polymers that have compatibility with a wide range of chemicals, such as PTFE, polyolefins, PVDF etc. from consideration as material for pump tubing. The popular elastomers for pump tubing are silicone, PVC, EPDM+polypropylene (as in Santoprene), polyurethane and Neoprene. Of these materials, the EPDM+polypropylene (-prenes) have the best fatigue resistance and a wide range of chemical compatibility. Silicone is popular with water-based fluids, such as in Bio-pharma industry, but have limited range of chemical compatibility in other industries.
Extruded fluoropolymer tubes such as FKM (Viton, Fluorel, etc.) have good compatibility with acids, hydrocarbons, and petroleum fuels. But the material has insufficient fatigue resistance to achieve an effective tube life.
There are a couple of newer pump tubing developments that offer a broad chemical compatibility: a lined tubing approach and the use of fluoroelastomer approach.
With the lined tubing, the thin inside liner is made of a chemically resistant material such as poly-olefin and PTFE that form a barrier for the rest of the tubing wall from coming in contact with the pumped fluid. These liners are materials that are not elastomeric, therefore the entire tube wall cannot be made with this material for peristaltic pump applications. This tubing provides adequate chemical compatibility and life to be used in chemically challenging applications. There are a few things to keep in mind when using these tubes - any pin holes in the liner during manufacturing could render the tubing vulnerable to chemical attack. In the case of stiff plastic liners like the polyolefins, with repeated flexing in the peristaltic pump they can develop cracks, rendering the bulk material again vulnerable to chemical attack. A common issue with all lined tubing is delamination of the liner with repeated flexing that signals the end of the tube's life. For those with need for chemically compatible tubing, these lined tubing offer a good solution.
With the fluoroelastomer tubing, the elastomer itself has the chemical resistance. In the case of Chem-Sure, it is made of a perfluoroelastomer, that has the broadest chemical compatibility of all elastomers. The two fluoroelastomer tubes listed above combine the chemical compatibility with a very long tube life stemming from their reinforcement technology, but come at a pretty high initial cost. One has to justify the cost with the total value derived over the long tube life, and compare with other options such as other tubing or even other pump technologies.
There are many online sites for checking the chemical compatibility of the tubing material with the pumped fluid. The manufacturers of these tubing may also have compatibility charts specific to their tubing.
While these charts cover a list of commonly encountered fluids, they may not have all the fluids. If there is a fluid whose compatibility is not listed anywhere, then a common test of compatibility is the immersion testing. A 1 to 2 inch sample of the tubing is immersed in the fluid to be pumped for anywhere from 24 to 48 hours, and the amount of weight change from before and after the immersion is measured. If the weight change is greater than 10% of the initial weight, then that tube is not compatible with the fluid, and should not be used in that application. This test is still a one way test, in the sense that there is still a remote chance that the tubing that passes this test can still be incompatible for the application since the combination of borderline compatibility and mechanical flexing can push the tube over the edge, resulting in premature tube failure.
In general, recent tubing developments have brought broad chemical compatibility to the peristaltic pump option that many chemical dosing applications can benefit over other current pump technologies.
Occlusion
The minimum gap between the roller and the housing determines the maximum squeeze applied on the tubing. The amount of squeeze applied to the tubing affects pumping performance and the tube life - more squeezing decreases the tubing life dramatically, while less squeezing decreases the pumping efficiency, especially in high pressure pumping. Therefore, this amount of squeeze becomes an important design parameter.The term "occlusion" is used to measure the amount of squeeze. It is either expressed as a percentage of twice the wall thickness, or as an absolute amount of the wall that is squeezed.
Let
- y = occlusion
- g = minimum gap between the roller and the housing
- t = wall thickness of the tubing
Then
- y = 2 x t - g (when expressed as the absolute amount of squeeze)
- y = (2 x t - g) / (2 x t) x 100 (when expressed as a percentage of twice the wall thickness)
The occlusion is typically 10 to 20%, with a higher occlusion for a softer tube material and a lower occlusion for a harder tube material.
Thus for a given pump, the most critical tubing dimension becomes the wall thickness. An interesting point here is that the inside diameter of the tubing is not an important design parameter for the suitability of the tubing for the pump. Therefore, it is common for more than one ID be used with a pump, as long as the wall thickness remains the same.
Inside diameter
For a given rpm of the pump, a tube with larger inside diameter (ID) will give higher flow rate than one with a smaller inside diameter. Intuitively the flow rate is a function of the cross section area of the tube bore.Flow rate
Flow rate is an important customer requirement. The flow rate in a peristaltic pump is determined by many factors, such as:- Tube ID - higher flow rate with larger ID
- Length of tube in the pump measured from initial pinch point near the inlet to the final release point near the outlet - higher flow rate with longer length
- Roller RPM - higher flow rate with higher RPM
Interestingly enough, increasing the number of rollers doesn't increase the flow rate, instead it may decrease the flow rate somewhat by reducing the volume of fluid between the initial pinch point and the final release point. Increasing rollers does tend to decrease the amplitude of the fluid pulsing at the outlet by increasing the frequency of the pulsed flow.
Hose pumps
Higher pressure peristaltic hoseHose (tubing)
A hose is a hollow tube designed to carry fluids from one location to another. Hoses are also sometimes called pipes , or more generally tubing...
pumps which can typically operate against up to 16 bar
Bar (unit)
The bar is a unit of pressure equal to 100 kilopascals, and roughly equal to the atmospheric pressure on Earth at sea level. Other units derived from the bar are the megabar , kilobar , decibar , centibar , and millibar...
in continue service, use shoes (rollers only used on low pressure types) and have casings filled with lubricant
Lubricant
A lubricant is a substance introduced to reduce friction between moving surfaces. It may also have the function of transporting foreign particles and of distributing heat...
to prevent abrasion of the exterior of the pump tube and to aid in the dissipation of heat, and use reinforced tubes, often called "hoses". This class of pump is often called a "hose pump".
The hoses in a hose pump are typically reinforced, resulting in a very thick wall. For a given ID the hoses have much bigger OD than a tubing for the roller pump. This thicker wall, combined with a stiffer material typically used in the hoses make the forces necessary to occlude the hose much greater than for the tubing. This results in a bigger and slower pump (up to 50/60 RPM)and motor for a given flow rate with the hose pump than the roller pump, consuming more energy to run.
The biggest advantage with the hose pumps over the roller pumps is the high operating pressure of up to 16 bar. With rollers max pressure can arrive up to 12 Bar without any problem. If the high operating pressure is not required, a tubing pump is a better option than a hose pump if the pumped media is not abrasive. With recent advances made in the tubing technology for pressure, life and chemical compatibility, as well as the higher flow rate ranges, the advantages that hose pumps had over roller pumps continues to erode.
Tube pumps
Lower pressure peristaltic pumps typically have dry casings and use rollers along with non-reinforced, extruded tubing. This class of pump is sometimes called a "tube pump" or "tubing pump". These pumps employ rollers to squeeze the tube. Except for the 360 degree eccentric pump design as described below, these pumps have a minimum of 2 rollers 180 degrees apart, and may have as many as 8, or even 12 rollers. Increasing the number of rollers increase the frequency of the pumped fluid at the outlet, thereby decreasing the amplitude of pulsing. The downside to increasing number of rollers it that it proportionately increases number of squeezes, or occlusions, on the tubing for a given cumulative flow through that tube, thereby reducing the tubing life.There are two kinds of roller design in peristaltic pumps:
1. Fixed occlusion - the rollers have a fixed locus as it turns, keeping the occlusion constant as it squeezes the tube. This is a simple, yet effective design. The only downside to this design is that the occlusion as a percent on the tube varies with the variation of the tube wall thickness. Typically the wall thickness of the extruded tubes vary enough that the % occlusion can vary with the wall thickness (see above). Therefore, a section of tube with greater wall thickness, but within the accepted tolerance, will have higher percent occlusion, which increases the wear on the tubing, thereby decreasing the tube life. Tube wall thickness tolerances today are generally kept tight enough that this issue is not of much practical concern. For those mechanically inclined, this may be the constant strain operation.
2. Spring-loaded rollers - As the name indicates, the rollers are mounted on a spring. This design is a bit more elaborate than the fixed occlusion, but helps overcome the variations in the tube wall thickness over a broader range. Irrespective of the variations, the roller imparts the same amount of stress on the tubing that is proportional to the spring constant, making this a constant stress operation. The spring is selected to overcome not only the hoop strength of the tubing, but also the pressure of the pumped fluid.
The operating pressure of these pumps is determined by the tubing, and the motor's ability to overcome the hoop strength of the tubing and the pressure.
360 degree eccentric design
A unique approach to peristaltic hose pump design employs a single oversized roller on an eccentric shaft that compresses an engineered, low friction hose through 360 degrees of rotation. The benefits of this design include more flow per revolution and only one compression and expansion per cycle. At equal performance points this pump runs more slowly, with consequent longer hose lifetime, than pumps with multiple shoes or rollers.Many older hose pumps use shoes to compress the hose. When the shoe slides over the outside of the hose, it creates friction and heat, which shortens hose life. A single roller pump uses a large diameter lubricated roller on an eccentric
Eccentric (mechanism)
In mechanical engineering, an eccentric is a circular disk solidly fixed to a rotating axle with its centre offset from that of the axle ....
shaft that rolls over the hose. This means that it produces less friction, and therefore less heat, than a pump with shoes.
In addition to less heat, an eccentric shaft hose pump functions with only a single compression of the hose per revolution. For every one rotation, the pump has one compression of the hose, while pumps with multiple shoes or rollers have at least two compressions per revolution, and in some cases three or four. Since the hose is the heart of a peristaltic hose pump, and hose life is inversely proportional to the number of squeezes, this design will outperform a pump with shoes at the same speed.
The hose in this type of pump takes up the full 360 degrees of the pump housing. This is important, because at an equal size, this design will produce 55% more flow at the same speed. This means that one can get more flow at the same pump speed, or run the pump more slowly to generate the same flow.
Advantages
- No contamination. Because the only part of the pump in contact with the fluid being pumped is the interior of the tube, it is easy to sterilizeSterilization (microbiology)Sterilization is a term referring to any process that eliminates or kills all forms of microbial life, including transmissible agents present on a surface, contained in a fluid, in medication, or in a compound such as biological culture media...
and clean the inside surfaces of the pump.
- Low maintenance needs. Their lack of valves, seals and glands makes them comparatively inexpensive to maintain.
- They are able to handle slurries, viscous, shear-sensitive and aggressive fluids.
- Pump design prevents backflow and syphoning without valves.
Tubing
It is important to select tubing with appropriate chemical resistance towards the liquid being pumped. Types of tubing commonly used in peristaltic pumps include:- Polyvinyl chloridePolyvinyl chloridePolyvinyl chloride, commonly abbreviated PVC, is a thermoplastic polymer. It is a vinyl polymer constructed of repeating vinyl groups having one hydrogen replaced by chloride. Polyvinyl chloride is the third most widely produced plastic, after polyethylene and polypropylene. PVC is widely used in...
(PVC) - Silicone rubberSilicone rubberSilicone rubber is an elastomer composed of silicone—itself a polymer—containing silicon together with carbon, hydrogen, and oxygen. Silicone rubbers are widely used in industry, and there are multiple formulations...
- FluoropolymerFluoropolymerA fluoropolymer is a fluorocarbon based polymer with multiple strong carbon–fluorine bonds. It is characterized by a high resistance to solvents, acids, and bases.-History:Fluoropolymers were accidentally discovered in 1938 by Dr. Roy J...
Trade names include:http://www.tblplastics.com/tubing_pharmaline_1.html http://www.tblplastics.com/tubing_clear_green.html Marprene, Bioprene, Fluorel, Pumpsil-D, Pumpsil, Tygon
Tygon Tubing
Tygon is a brand name for a family of flexible tubing consisting of a variety of base materials. Tygon is a registered trademark of Saint-Gobain Corporation. It is an invented word, owned and used by Saint-Gobain and originated in the late 1930s. Tygon products are produced in three countries, but...
, Viton
Viton
Viton is a brand of synthetic rubber and fluoropolymer elastomer commonly used in O-rings and other molded or extruded goods. The name is a registered trademark of DuPont Performance Elastomers L.L.C.....
, Pharmed, Norprene, STA-PURE, CHEM-SURE, GORE High-Resilience Tubing, Neoprene
Neoprene
Neoprene or polychloroprene is a family of synthetic rubbers that are produced by polymerization of chloroprene. Neoprene in general has good chemical stability, and maintains flexibility over a wide temperature range...
.
Example of tube being changed on a peristaltic pump.
Typical applications
- DialysisDialysisIn medicine, dialysis is a process for removing waste and excess water from the blood, and is primarily used to provide an artificial replacement for lost kidney function in people with renal failure...
machines - Open-heart bypass pump machines
- Infusion pumpInfusion pumpAn infusion pump infuses fluids, medication or nutrients into a patient's circulatory system. It is generally used intravenously, although subcutaneous, arterial and epidural infusions are occasionally used....
- AutoAnalyzerAutoAnalyzerAutoAnalyzer is an automated analyzer using a special flow technique named "continuous flow analysis " first made by the Technicon Corporation. The instrument was invented 1957 by Leonard Skeggs, PhD and commercialized by Jack Whitehead's Technicon Corporation...
- SewageSewageSewage is water-carried waste, in solution or suspension, that is intended to be removed from a community. Also known as wastewater, it is more than 99% water and is characterized by volume or rate of flow, physical condition, chemical constituents and the bacteriological organisms that it contains...
sludge - Aquariums, particularly calcium reactorCalcium reactorIn marine and reef aquariums, a calcium reactor is a device used to create a balance of alkalinity in the system. An acidic solution is produced by injecting carbon dioxide into a chamber with salt water and calcium rich media. The carbon dioxide lowers the pH by producing a solution high in...
s - Analytical chemistryAnalytical chemistryAnalytical chemistry is the study of the separation, identification, and quantification of the chemical components of natural and artificial materials. Qualitative analysis gives an indication of the identity of the chemical species in the sample and quantitative analysis determines the amount of...
experiments - Carbon monoxideCarbon monoxideCarbon monoxide , also called carbonous oxide, is a colorless, odorless, and tasteless gas that is slightly lighter than air. It is highly toxic to humans and animals in higher quantities, although it is also produced in normal animal metabolism in low quantities, and is thought to have some normal...
monitors (e.g., at Longannet power stationLongannet power stationLongannet power station is a large coal-fired power station in Fife capable of co-firing biomass, natural gas and sludge. The station is situated on the north bank of the Firth of Forth, near Kincardine on Forth. Its generating capacity of 2,400 megawatts is the highest of any power station in...
) - Agriculture
- Food manufacturing
- Beverage dispensing
- Chemical
- Engineering
- Construction - pumping cement
- Pharmaceutical production
- OEM applications
- Print and packaging
- Paint and pigments
- Pulp and paper
- Science and research
- Water and Waste
- 'Sapsucker' pumps to apply vacuum to maple trees to enhance sap extraction and pump the sap to the evaporator
- Liquid food fountains