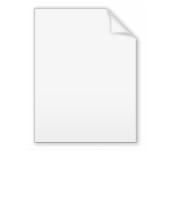
PDCA
Encyclopedia
PDCA is an iterative four-step management method used in business for the control and continuous improvement of processes and products. It is also known as the Deming
circle/cycle/wheel, Shewhart
cycle, control circle/cycle, or plan–do–study–act (PDSA).
PLAN: Establish the objectives and processes necessary to deliver results in accordance with the expected output (the target or goals). By establishing output expectations, the completeness and accuracy of the specification is also a part of the targeted improvement. When possible start on a small scale to test possible effects.
DO : Implement the plan, execute the process, make the product. Collect data for charting and analysis in the following "CHECK" and "ACT" steps.
CHECK : Study the actual results (measured and collected in "DO" above) and compare against the expected results (targets or goals from the "PLAN") to ascertain any differences. Charting data can make this much easier to see trends over several PDCA cycles and in order to convert the collected data into information. Information is what you need for the next step "ACT".
ACT : Request corrective actions
on significant differences between actual and planned results. Analyze the differences to determine their root causes. Determine where to apply changes that will include improvement of the process or product. When a pass through these four steps does not result in the need to improve, the scope to which PDCA is applied may be refined to plan and improve with more detail in the next iteration of the cycle, or attention needs to be placed in a different stage of the process.
, who is considered by many to be the father of modern quality control; however he always referred to it as the "Shewhart cycle". Later in Deming's career, he modified PDCA to "Plan, Do, Study, Act" (PDSA) because he felt that “check” emphasized inspection over analysis.
The concept of PDCA is based on the scientific method
, as developed from the work of Francis Bacon
(Novum Organum, 1620). The scientific method can be written as "hypothesis"–"experiment"–"evaluation" or plan, do and check. Shewhart described manufacture under "control"—under statistical control—as a three step process of specification, production, and inspection. He also specifically related this to the scientific method of hypothesis, experiment, and evaluation. Shewhart says that the statistician "must help to change the demand [for goods] by showing [...] how to close up the tolerance range and to improve the quality of goods". Clearly, Shewhart intended the analyst to take action based on the conclusions of the evaluation. According to Deming, during his lectures in Japan in the early 1950s, the Japanese participants shortened the steps to the now traditional plan, do, check, act. Deming preferred plan, do, study, act because "study" has connotations in English closer to Shewhart's intent than "check".
A fundamental principle of the scientific method and PDCA is iteration—once a hypothesis is confirmed (or negated), executing the cycle again will extend the knowledge further. Repeating the PDCA cycle can bring us closer to the goal, usually a perfect operation and output.
In Six Sigma
programs, the PDCA cycle is called "define, measure, analyze, improve, control" (DMAIC). The iterative nature of the cycle must be explicitly added to the DMAIC procedure.
PDCA should be repeatedly implemented in spirals of increasing knowledge of the system that converge on the ultimate goal, each cycle closer than the previous. One can envision an open coil spring, with each loop being one cycle of the scientific method - PDSA, and each complete cycle indicating an increase in our knowledge of the system under study. This approach is based on the belief that our knowledge and skills are limited, but improving. Especially at the start of a project, key information may not be known; the PDCA—scientific method—provides feedback to justify our guesses (hypotheses) and increase our knowledge. Rather than enter "analysis paralysis
" to get it perfect the first time, it is better to be approximately right than exactly wrong. With the improved knowledge, we may choose to refine or alter the goal (ideal state). Certainly, the PDCA approach can bring us closer to whatever goal we choose.
Rate of change, that is, rate of improvement, is a key competitive factor in today's world. PDCA allows for major 'jumps' in performance ('breakthroughs' often desired in a Western approach), as well as Kaizen
(frequent small improvements). In the United States a PDCA approach is usually associated with a sizable project involving numerous people's time, and thus managers want to see large 'breakthrough' improvements to justify the effort expended. However, the scientific method and PDCA apply to all sorts of projects and improvement activities.
W. Edwards Deming
William Edwards Deming was an American statistician, professor, author, lecturer and consultant. He is perhaps best known for his work in Japan...
circle/cycle/wheel, Shewhart
Walter A. Shewhart
Walter Andrew Shewhart March 18, 1891 - March 11, 1967) was an American physicist, engineer and statistician, sometimes known as the father of statistical quality control.W...
cycle, control circle/cycle, or plan–do–study–act (PDSA).
Meaning
The steps in each successive PDCA cycle are :PLAN: Establish the objectives and processes necessary to deliver results in accordance with the expected output (the target or goals). By establishing output expectations, the completeness and accuracy of the specification is also a part of the targeted improvement. When possible start on a small scale to test possible effects.
DO : Implement the plan, execute the process, make the product. Collect data for charting and analysis in the following "CHECK" and "ACT" steps.
CHECK : Study the actual results (measured and collected in "DO" above) and compare against the expected results (targets or goals from the "PLAN") to ascertain any differences. Charting data can make this much easier to see trends over several PDCA cycles and in order to convert the collected data into information. Information is what you need for the next step "ACT".
ACT : Request corrective actions
Corrective and preventive action
Corrective action and preventive action are improvements to an organization's processes taken to eliminate causes of non-conformities or other undesirable situations. CAPA is a concept within good manufacturing practice...
on significant differences between actual and planned results. Analyze the differences to determine their root causes. Determine where to apply changes that will include improvement of the process or product. When a pass through these four steps does not result in the need to improve, the scope to which PDCA is applied may be refined to plan and improve with more detail in the next iteration of the cycle, or attention needs to be placed in a different stage of the process.
About
PDCA was made popular by Dr. W. Edwards DemingW. Edwards Deming
William Edwards Deming was an American statistician, professor, author, lecturer and consultant. He is perhaps best known for his work in Japan...
, who is considered by many to be the father of modern quality control; however he always referred to it as the "Shewhart cycle". Later in Deming's career, he modified PDCA to "Plan, Do, Study, Act" (PDSA) because he felt that “check” emphasized inspection over analysis.
The concept of PDCA is based on the scientific method
Scientific method
Scientific method refers to a body of techniques for investigating phenomena, acquiring new knowledge, or correcting and integrating previous knowledge. To be termed scientific, a method of inquiry must be based on gathering empirical and measurable evidence subject to specific principles of...
, as developed from the work of Francis Bacon
Francis Bacon
Francis Bacon, 1st Viscount St Albans, KC was an English philosopher, statesman, scientist, lawyer, jurist, author and pioneer of the scientific method. He served both as Attorney General and Lord Chancellor of England...
(Novum Organum, 1620). The scientific method can be written as "hypothesis"–"experiment"–"evaluation" or plan, do and check. Shewhart described manufacture under "control"—under statistical control—as a three step process of specification, production, and inspection. He also specifically related this to the scientific method of hypothesis, experiment, and evaluation. Shewhart says that the statistician "must help to change the demand [for goods] by showing [...] how to close up the tolerance range and to improve the quality of goods". Clearly, Shewhart intended the analyst to take action based on the conclusions of the evaluation. According to Deming, during his lectures in Japan in the early 1950s, the Japanese participants shortened the steps to the now traditional plan, do, check, act. Deming preferred plan, do, study, act because "study" has connotations in English closer to Shewhart's intent than "check".
A fundamental principle of the scientific method and PDCA is iteration—once a hypothesis is confirmed (or negated), executing the cycle again will extend the knowledge further. Repeating the PDCA cycle can bring us closer to the goal, usually a perfect operation and output.
In Six Sigma
Six Sigma
Six Sigma is a business management strategy originally developed by Motorola, USA in 1986. , it is widely used in many sectors of industry.Six Sigma seeks to improve the quality of process outputs by identifying and removing the causes of defects and minimizing variability in manufacturing and...
programs, the PDCA cycle is called "define, measure, analyze, improve, control" (DMAIC). The iterative nature of the cycle must be explicitly added to the DMAIC procedure.
PDCA should be repeatedly implemented in spirals of increasing knowledge of the system that converge on the ultimate goal, each cycle closer than the previous. One can envision an open coil spring, with each loop being one cycle of the scientific method - PDSA, and each complete cycle indicating an increase in our knowledge of the system under study. This approach is based on the belief that our knowledge and skills are limited, but improving. Especially at the start of a project, key information may not be known; the PDCA—scientific method—provides feedback to justify our guesses (hypotheses) and increase our knowledge. Rather than enter "analysis paralysis
Analysis paralysis
The term "analysis paralysis" or "paralysis of analysis" refers to over-analyzing a situation, so that a decision or action is never taken, in effect paralyzing the outcome. A decision can be treated as over-complicated, with too many detailed options, so that a choice is never made, rather than...
" to get it perfect the first time, it is better to be approximately right than exactly wrong. With the improved knowledge, we may choose to refine or alter the goal (ideal state). Certainly, the PDCA approach can bring us closer to whatever goal we choose.
Rate of change, that is, rate of improvement, is a key competitive factor in today's world. PDCA allows for major 'jumps' in performance ('breakthroughs' often desired in a Western approach), as well as Kaizen
Kaizen
, Japanese for "improvement", or "change for the better" refers to philosophy or practices that focus upon continuous improvement of processes in manufacturing, engineering, game development, and business management. It has been applied in healthcare, psychotherapy, life-coaching, government,...
(frequent small improvements). In the United States a PDCA approach is usually associated with a sizable project involving numerous people's time, and thus managers want to see large 'breakthrough' improvements to justify the effort expended. However, the scientific method and PDCA apply to all sorts of projects and improvement activities.
See also
- AIDA process
- Business process improvementBusiness process improvementBusiness Process Improvement is a systematic approach to help an organization optimize its underlying processes to achieve more efficient results. The methodology was first documented in H. James Harrington’s 1991 book Business Process Improvement. It is the methodology that both Process...
- COBITCOBITCOBIT is a framework created by ISACA for information technology management and IT Governance. It is a supporting toolset that allows managers to bridge the gap between control requirements, technical issues and business risks.-Overview:...
- Creative Problem Solving ProcessCreative Problem Solving ProcessThe Creative Problem Solving Process , also known as the Osborn-Parnes CPS process, was developed by Alex Osborn and Dr. Sidney J. Parnes in the 1950s. CPS is a structured method for generating novel and useful solutions to problems...
- DMAIC
- Lesson studyLesson studyLesson Study is a teaching improvement process that has origins in Japanese elementary education, where it is a widespread professional development practice...
- OODA loopOODA LoopThe OODA loop is a concept originally applied to the combat operations process, often at the strategic level in military operations. It is now also often applied to understand commercial operations and learning processes...
- Performance managementPerformance managementPerformance management includes activities that ensure that goals are consistently being met in an effective and efficient manner. Performance management can focus on the performance of an organization, a department, employee, or even the processes to build a product or service, as well as many...
- Quality managementQuality managementThe term Quality management has a specific meaning within many business sectors. This specific definition, which does not aim to assure 'good quality' by the more general definition , can be considered to have four main components: quality planning, quality control, quality assurance and quality...
- Quality storyboardQuality storyboardA Quality storyboard is a visual method for displaying a Quality Control story . Some enterprises have developed a storyboard format for telling the QC story, for example at Yokogawa-Hewlett-Packard in Japan, the story is told using a flip chart which is 6 feet by 6 feet...
- Robert S. KaplanRobert S. KaplanRobert S. Kaplan is Baker Foundation Professor at Harvard Business School, United States, and co-creator, together with David P. Norton, of the balanced scorecard, a means of linking a company's current actions to its long-term goals...
(closed loop management system) - Total Security ManagementTotal Security ManagementTotal Security Management is the business practice of developing and implementing comprehensive risk management and security practices for a firm’s entire value chain. This business process improvement strategy seeks to create added value for companies by managing security and resilience...
Further reading
- The Improvement Guide: A Practical Approach to Enhancing Organizational Performance, 2nd Edition by Gerald J. Langley, Ronald Moen, Kevin M. Nolan, Thomas W. Nolan, Clifford L. Norman, Lloyd P. Provost Published by Jossey-Bass ISBN 978-0-470-19241-2