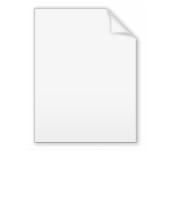
PAT Testing
Encyclopedia
Portable appliance testing (commonly known as PAT or PAT Inspection or PAT Testing) is a process in the United Kingdom, New Zealand and Australia by which electrical appliances are routinely checked for safety. The correct term for the whole process is in-service inspection & testing of electrical equipment.
Similar procedures do exist in in other parts of the world, too. E.g. testing of portable (and stationary) equipment according to BGV A3 in Germany.
When people work with electrical appliances, health and safety regulations state that the appliance must be safe, to prevent harm to the workers. Many types of equipment require testing at regular intervals to ensure continual safety; the interval between tests depending on both the type of appliance and the environment it is used in.
Evidence of testing is clearly visible to workers in the form of 'passed' , 'tested for electrical safety' and 'do not use after' labels affixed to various parts of the electrical equipment they use.
Portable appliance testing and inspection, was however, conducted on a 3 month (high risk) and 6 month (low risk) cycle from the early 1960s onwards; in government departments under the control of the Department of the Environment Property and Services Agency (circa 1970 to 2000) as the DOEPSA was known and prior to that as the Ministry of Public Buildings and Works (MoPBW) until about 1970.
Extensive record keeping was made into log-books and generally the equipment used was an insulation resistance tester, simple hand tools and visual inspection. This testing and inspection was done under a planned maintenance scheme and predated both the Health and Safety at Work Act 1974 and the Electricity at Work Act 1990 that are frequently quoted as the reason that PAT inspection is done.
In reality neither act nor their corresponding regulations detail PAT inspection as an obligation, but rather state a requirement of maintenance of safety and evidence of routine maintenance all hand-held, portable and plug-in equipment.
It seemed inevitable with the increasing amounts of such equipment in domestic, commercial and industrial environments that the system employed for all government departments would become more formalized and adopted as a method for assuring safety of appliances in the world beyond the civil service departments.
Testing equipment specifically designed for PAT inspections was developed using portable devices, which were based on the testing equipment used by manufacturers to ensure compliance with the British Standard Code of Practice relevant to that type of appliance.
One other check carried out on high risk equipment such as hand held electrical drills issued from a government department stores was an earth test, where 25 A was passed down the earth conductor to substantiate that the earth was a sound and valid connection.
, in the same way that some people say "LCD
Display" (see also RAS syndrome
). However, the phrase is commonly used in the industry, even though most people realise it is incorrect. The correct term for the whole process is In-service Inspection & Testing of Electrical Equipment (as defined by IET/IEE and City and Guilds).
To help raise awareness of the law, the HSE has produced a poster containing the above text, intended to be displayed in UK workplaces. The poster is available here: http://www.hse.gov.uk/myth/july.pdf
British law (the Electricity at Work Regulations 1989
in particular) requires that all electrical systems (including electrical appliances) are maintained (so far as is reasonably practicable) to prevent danger. Guidance from the Institution of Engineering and Technology
(IET, published under the IEE
brand) and the Health and Safety Executive
(HSE) suggest initial intervals for combined inspection and testing that range from three months (for construction equipment) to one year for inspection and, in many cases, longer periods for testing (certain types of appliance in schools, hotels, offices and shops).
Electrical systems refer to the installation as well as all the appliances connected to it. A qualified electrician or someone that has PAT testing training must inspect the installation annually in any public building and/or a place that people work, private houses do not need this test. The maintenance of the appliances can largely be carried out in-house in many organisations. This can result in cost savings and more flexibility in when PAT testing is carried out.
The European Low Voltage Directive governs the manufacture or importation of electrical appliances. Compliance to this has to be declared and indicated by the display of the CE mark on the product. The responsibility for this lies with the manufacturer or the importer and is policed by the Trading Standards. However, it is important to have a maintenance regime for electrical appliances. The Electricity at Work Regulations (1989) requires that electrical appliances be maintained so that they remain safe during use. The implementation of this is up to employers. The HSE or the local authority is responsible for the policing of this.
In the UK, There is no requirement to have a formal qualification for persons carrying out PAT Testing. The Electricity at Work regulations of 1989 simply state that inspecting and testing must be carried out by a competent person, however does not mention a benchmark for competency. It has become accepted practice, however, for individuals operating as PAT Testers to hold a 2377–12 City and Guilds qualification. PAT Testers in the UK do not need to be electricians or have a background in the electrical industry.
The following steps are taken when testing a business' electrical equipment.
The tests that an individual must carry out to declare an item electrically safe is dependant on the class of construction (shown below). Some of these tests are:
Class I – Single insulated wiring, which requires an earth connection. There is no symbol for a Class I product so if a rating plate has no symbol on it then it is usually Class I.
Class II – Double insulated wiring, therefore no need for a earth lead. Class II is indicated by double box.
Class III – These are appliances that are supplied at a low voltage (usually called Separated Extra Low Voltage) which must be less than 50 V. These appliances are supplied with a transformer supply that is also marked.
Class 01 – As Class 0 but appliance has an earth terminal which is unused since two core cable is used.
See appliance classes
for more info on class of construction.
It is therefore generally recommended that if a company wishes to PAT Test in-house then they have the person who will be doing the testing attend a portable appliance testing training course so as to fully understand what it is they are checking for.
The only nationally recognized qualification of competence in PAT is offered by City & Guilds
: 'Code of Practice for In-service Inspection and Testing of Electrical Equipment – Vocational 3 (No. 2377)'. although many other non-recognized PAT training courses are available.
There are also advanced PAT testers, which give much more information and testing features but are mainly aimed at competent persons qualified to City & Guilds 2377 or EAL . To use the majority of these testers, one does require a higher level of electrical skill.
At the basic level PAT test instruments are relatively simple to operate devices that carry out basic safety checks. Most are equipped with an earth continuity test, insulation resistance test and the ability to check the wiring of detachable mains cords. They do not however include tests which inolve applying mains power to the appliance under test, for example, a protective conductor current or touch current tests.
Mains powered pass / fail PAT testers
The powered Pass / Fail PAT testers are the standard for most businesses who test in-house.
It is ideal for those wanting to carry out in-house testing of electrical appliances in offices, hotels, schools, nursing homes, factories and construction sites. You usually get test result labels, which are attached to the electrical equipment that is being tested with a date stamp to show when the item next needs to be tested. The simplicity of these devices make them very popular with small businesses simply because of the PASS or FAIL display when a test is done. These testers are also safe for use on PCs and other IT equipment.
The newer battery powered testers offer much more flexibility as the tester can be moved to the equipment as opposed to the other way round.
Battery powered pass / fail PAT testers
These are the newer and more convenient pass / fail PAT testers, which you can take to the appliance to be tested making testing multiple items in a business much quicker. They usually come with rechargeable batteries
The battery powered testers are fast replacing the older powered units.
The newer battery powered PAT testers have a simple "lights" system. They have a "Pass" light , a "Fail" light, options for Class I metal / plastic or Class II. They also will show:
A knowledge of electrical readings is required, hence why these type of PAT testers are designed for use by an electrician or someone with electrical qualifications. Advanced PAT testers are also much more effective as facilities management tools because of their ability to log, capture and record the location and test status of electrical equipment and appliances.
RCD testing
In the most modern PAT testers, RCD testing is now included in the suite of test options available. This follows the inclusion of new advice in the IEE Code of Practice that when an extension lead or multiway adapter is fitted with an RCD, the operation of the RCD should be checked to determine that the trip time is within specified limits.
Bluetooth enabled computerised PAT testers make the two way transfer of test data between the tester and PC-based record keeping systems much simpler.
In addition, PAT testers equipped with Bluetooth means that connectivity with other test accessories such as label printers can also be made without having to use cable connection (an example of a handheld computerised PAT tester is shown below)
When a PAT Tester is calibrated it is re-configuring it to match the original specification. This includes:
Dual purpose checkboxes have also been introduced which are capable of validating the accuracy of both electrical installation testers and portable appliance testers.
Similar procedures do exist in in other parts of the world, too. E.g. testing of portable (and stationary) equipment according to BGV A3 in Germany.
When people work with electrical appliances, health and safety regulations state that the appliance must be safe, to prevent harm to the workers. Many types of equipment require testing at regular intervals to ensure continual safety; the interval between tests depending on both the type of appliance and the environment it is used in.
Evidence of testing is clearly visible to workers in the form of 'passed' , 'tested for electrical safety' and 'do not use after' labels affixed to various parts of the electrical equipment they use.
Portable appliance testing and inspection, was however, conducted on a 3 month (high risk) and 6 month (low risk) cycle from the early 1960s onwards; in government departments under the control of the Department of the Environment Property and Services Agency (circa 1970 to 2000) as the DOEPSA was known and prior to that as the Ministry of Public Buildings and Works (MoPBW) until about 1970.
Extensive record keeping was made into log-books and generally the equipment used was an insulation resistance tester, simple hand tools and visual inspection. This testing and inspection was done under a planned maintenance scheme and predated both the Health and Safety at Work Act 1974 and the Electricity at Work Act 1990 that are frequently quoted as the reason that PAT inspection is done.
In reality neither act nor their corresponding regulations detail PAT inspection as an obligation, but rather state a requirement of maintenance of safety and evidence of routine maintenance all hand-held, portable and plug-in equipment.
It seemed inevitable with the increasing amounts of such equipment in domestic, commercial and industrial environments that the system employed for all government departments would become more formalized and adopted as a method for assuring safety of appliances in the world beyond the civil service departments.
Testing equipment specifically designed for PAT inspections was developed using portable devices, which were based on the testing equipment used by manufacturers to ensure compliance with the British Standard Code of Practice relevant to that type of appliance.
One other check carried out on high risk equipment such as hand held electrical drills issued from a government department stores was an earth test, where 25 A was passed down the earth conductor to substantiate that the earth was a sound and valid connection.
Name
Portable appliance testing is abbreviated to PAT. The phrase PAT Testing is in fact a tautologyTautology (rhetoric)
Tautology is an unnecessary or unessential repetition of meaning, using different and dissimilar words that effectively say the same thing...
, in the same way that some people say "LCD
Liquid crystal display
A liquid crystal display is a flat panel display, electronic visual display, or video display that uses the light modulating properties of liquid crystals . LCs do not emit light directly....
Display" (see also RAS syndrome
RAS syndrome
RAS syndrome , also known as PNS syndrome or RAP phrases , refers to the use of one or more of the words that make up an acronym or initialism in conjunction with the abbreviated form, thus in effect repeating one or more words...
). However, the phrase is commonly used in the industry, even though most people realise it is incorrect. The correct term for the whole process is In-service Inspection & Testing of Electrical Equipment (as defined by IET/IEE and City and Guilds).
Health and safety executive – advice to UK office-based businesses
Clear advice on PAT testing requirements for office-based UK businesses is provided by the UK Health and Safety executive on their "Health and Safety myths" site http://www.hse.gov.uk/myth/july.pdf:- Myth: All office equipment must be tested by a qualified electrician every year
- The reality: No. The law requires employers to assess risks and take appropriate action. HSE’s advice is that for most office electrical equipment, visual checks for obvious signs of damage and perhaps simple tests by a competent member of staff are quite sufficient.
To help raise awareness of the law, the HSE has produced a poster containing the above text, intended to be displayed in UK workplaces. The poster is available here: http://www.hse.gov.uk/myth/july.pdf
Regulations on who must have their equipment PAT tested
The Electricity at Work Regulations (1989) requires "All electrical systems shall be maintained so as to prevent, so far as is reasonably practicable, any danger". This is interpreted as covering the fixed electrical installation as well as portable and transportable equipment connected to it. The Regulations also state "It is the duty of every employer and self employed person to comply with the provision of these Regulations."British law (the Electricity at Work Regulations 1989
Health and safety regulations in the United Kingdom
In the United Kingdom there are many regulations relevant to health, safety and welfare at work. Many of these give effect to European Union directives.-Regulations made under the Health and Safety at Work etc. Act 1974:...
in particular) requires that all electrical systems (including electrical appliances) are maintained (so far as is reasonably practicable) to prevent danger. Guidance from the Institution of Engineering and Technology
Institution of Engineering and Technology
The Institution of Engineering and Technology is a British professional body for those working in engineering and technology in the United Kingdom and worldwide. It was formed in 2006 from two separate institutions: the Institution of Electrical Engineers , dating back to 1871, and the...
(IET, published under the IEE
Institution of Electrical Engineers
The Institution of Electrical Engineers was a British professional organisation of electronics, electrical, manufacturing, and Information Technology professionals, especially electrical engineers. The I.E.E...
brand) and the Health and Safety Executive
Health and Safety Executive
The Health and Safety Executive is a non-departmental public body in the United Kingdom. It is the body responsible for the encouragement, regulation and enforcement of workplace health, safety and welfare, and for research into occupational risks in England and Wales and Scotland...
(HSE) suggest initial intervals for combined inspection and testing that range from three months (for construction equipment) to one year for inspection and, in many cases, longer periods for testing (certain types of appliance in schools, hotels, offices and shops).
Electrical systems refer to the installation as well as all the appliances connected to it. A qualified electrician or someone that has PAT testing training must inspect the installation annually in any public building and/or a place that people work, private houses do not need this test. The maintenance of the appliances can largely be carried out in-house in many organisations. This can result in cost savings and more flexibility in when PAT testing is carried out.
The European Low Voltage Directive governs the manufacture or importation of electrical appliances. Compliance to this has to be declared and indicated by the display of the CE mark on the product. The responsibility for this lies with the manufacturer or the importer and is policed by the Trading Standards. However, it is important to have a maintenance regime for electrical appliances. The Electricity at Work Regulations (1989) requires that electrical appliances be maintained so that they remain safe during use. The implementation of this is up to employers. The HSE or the local authority is responsible for the policing of this.
Who can PAT test?
It is a legal requirement to have attended a course or gained a qualification in order to PAT test in Australia. If you are a competent person and have a basic knowledge of electricity then you can be perfectly capable of testing appliances for electrical safety. It is, however, recommended that an individual wanting to PAT Test attends a course related to the subject matter. There can be much confusion on what needs PAT testing, what class an appliance is (and therefore which areas to test), and how often appliances legally need to be tested. Proof of a company’s competence in PAT testing is usually found in the form of a course certificate or qualification. A formal examination process for the topic is operated in collaboration with EAL or city and guilds (the awarding body) under the authority of the QCA (The Qualifications and Curriculum Authority) who validate and authorise the qualification.In the UK, There is no requirement to have a formal qualification for persons carrying out PAT Testing. The Electricity at Work regulations of 1989 simply state that inspecting and testing must be carried out by a competent person, however does not mention a benchmark for competency. It has become accepted practice, however, for individuals operating as PAT Testers to hold a 2377–12 City and Guilds qualification. PAT Testers in the UK do not need to be electricians or have a background in the electrical industry.
Carrying out PAT testing
This can be done by hiring an external company to test all the electrical products in a business or it can be done in-house by someone who has had some PAT training, either by an official qualification or by attending a health and safety course offered by some electrical health and safety companies.The following steps are taken when testing a business' electrical equipment.
User checks
Advising the user of potential danger signs can result in problems being picked up before they can result in any danger. For example, if the power cable is frayed or the plug is cracked, users need to be advised NOT TO USE the appliance and report the fault to a supervisor. This information can be put across, say by the use of a poster or in a memo. User checks are always carried out before operation, and the results are generally not recorded, unless a defect is identified.Formal visual inspections
This is a process of simply inspecting the appliance, the cable and the plug for any obvious signs of damage. According to the HSE, this process can find more than 90% of faults.Combined inspections and PAT testing
At periodic intervals, it is essential to test the portable appliances to measure that the degree of protection to ensure that it is adequate. At these intervals, a formal visual inspection is carried out and then followed by PAT testing. Note the inside of the plug MUST be checked unless it is moulded or there is an unbroken seal covering the screws (bad internal wiring or an unsuitable fuse would cause the item to be classed as dangerous).The tests that an individual must carry out to declare an item electrically safe is dependant on the class of construction (shown below). Some of these tests are:
- earth continuity
- insulation resistance
- polarity of wiring
Class of construction
Electrical appliances are differentiated by a series of IEC protection classes. In PAT Testing it is essential for the person PAT Testing to know the difference in classes and therefore what checks must be completed before declaring the item electrically safe.Class I – Single insulated wiring, which requires an earth connection. There is no symbol for a Class I product so if a rating plate has no symbol on it then it is usually Class I.
Class II – Double insulated wiring, therefore no need for a earth lead. Class II is indicated by double box.
Class III – These are appliances that are supplied at a low voltage (usually called Separated Extra Low Voltage) which must be less than 50 V. These appliances are supplied with a transformer supply that is also marked.
Other
Class 0 – Non-earthed metal appliance with two core cable. Sales of these items have been banned since 1975.Class 01 – As Class 0 but appliance has an earth terminal which is unused since two core cable is used.
See appliance classes
Appliance classes
In the electrical appliance manufacturing industry, the following IEC protection classes are used to differentiate between the protective-earth connection requirements of devices.-Class 0:...
for more info on class of construction.
PAT training and qualifications
It is not stated in the health and safety regulations for an individual to have any qualifications to PAT Test but it does state that it must be done by a competent person who has been given instruction – i.e. Someone who understands the process and can perform the necessary checks in a safe manner.It is therefore generally recommended that if a company wishes to PAT Test in-house then they have the person who will be doing the testing attend a portable appliance testing training course so as to fully understand what it is they are checking for.
The only nationally recognized qualification of competence in PAT is offered by City & Guilds
City and Guilds of London Institute
The City and Guilds of London Institute is a leading United Kingdom vocational education organisation. City & Guilds offers more than 500 qualifications over the whole range of industry sectors through 8500 colleges and training providers in 81 countries worldwide...
: 'Code of Practice for In-service Inspection and Testing of Electrical Equipment – Vocational 3 (No. 2377)'. although many other non-recognized PAT training courses are available.
Types of PAT testers
There are many different types of PAT testers available. The main kind for businesses are simple PASS/FAIL PAT testers that are very easy to use, and are aimed at in-house PAT testing. To use the majority of them, one does not require a high level of electrical skill.There are also advanced PAT testers, which give much more information and testing features but are mainly aimed at competent persons qualified to City & Guilds 2377 or EAL . To use the majority of these testers, one does require a higher level of electrical skill.
Pass / fail PAT testers
These are the simple-to-use and comparatively much cheaper portable appliance testers for most businesses who will test in-house to carry out the testing and suitable for a wide range of businesses. They simply say PASS or FAIL when a test is carried out. Battery operated PAT testers are particularly useful in getting into those awkward spaces to PAT Test. As with any inspections, it is important the test results are recorded onto a record sheet,or computer database, and stored in a safe place.At the basic level PAT test instruments are relatively simple to operate devices that carry out basic safety checks. Most are equipped with an earth continuity test, insulation resistance test and the ability to check the wiring of detachable mains cords. They do not however include tests which inolve applying mains power to the appliance under test, for example, a protective conductor current or touch current tests.
Mains powered pass / fail PAT testers
The powered Pass / Fail PAT testers are the standard for most businesses who test in-house.
It is ideal for those wanting to carry out in-house testing of electrical appliances in offices, hotels, schools, nursing homes, factories and construction sites. You usually get test result labels, which are attached to the electrical equipment that is being tested with a date stamp to show when the item next needs to be tested. The simplicity of these devices make them very popular with small businesses simply because of the PASS or FAIL display when a test is done. These testers are also safe for use on PCs and other IT equipment.
The newer battery powered testers offer much more flexibility as the tester can be moved to the equipment as opposed to the other way round.
Battery powered pass / fail PAT testers
These are the newer and more convenient pass / fail PAT testers, which you can take to the appliance to be tested making testing multiple items in a business much quicker. They usually come with rechargeable batteries
The battery powered testers are fast replacing the older powered units.
The newer battery powered PAT testers have a simple "lights" system. They have a "Pass" light , a "Fail" light, options for Class I metal / plastic or Class II. They also will show:
- earth continuity
- insulation resistance
- polarity
Advanced PAT testers
These are PAT testers designed to display more information than just pass or fail. As well as giving the pass/fail results, they will give readings for the tester to interpret. Some of these include:- Earth Continuity Resistance (aka Earth Bond) tests with a measurement range of 0 – 1.99 Ω at high test currents (usually 8 A, 10 A or 25 A) and lower test currents (in the range 20 mA to 200 mA), enabling a complete range of appliances including personal computers to be tested.
- Insulation Resistance tests at test voltages of 500 V DC or 250 V DC.
- Protective Conductor/touch current measurement (sometimes referred to as Earth Leakage tests on some older PAT units).
- Fuse test.
- Lead polarity
- Some units incorporate an RCDResidual-current deviceA Residual Current Device is a generic term covering both RCCBs and RCBOs.A Residual-Current Circuit Breaker is an electrical wiring device that disconnects a circuit whenever it detects that the electric current is not balanced between the energized conductor and the return neutral conductor...
test function. - Testing both 230 V and 110 V appliances
A knowledge of electrical readings is required, hence why these type of PAT testers are designed for use by an electrician or someone with electrical qualifications. Advanced PAT testers are also much more effective as facilities management tools because of their ability to log, capture and record the location and test status of electrical equipment and appliances.
RCD testing
In the most modern PAT testers, RCD testing is now included in the suite of test options available. This follows the inclusion of new advice in the IEE Code of Practice that when an extension lead or multiway adapter is fitted with an RCD, the operation of the RCD should be checked to determine that the trip time is within specified limits.
Computerised PAT testers
Also some advanced PAT testers have the capability of downloading the information to a pc or laptop for recordings (examples are shown below left and right).Bluetooth enabled computerised PAT testers make the two way transfer of test data between the tester and PC-based record keeping systems much simpler.
In addition, PAT testers equipped with Bluetooth means that connectivity with other test accessories such as label printers can also be made without having to use cable connection (an example of a handheld computerised PAT tester is shown below)
Calibration of PAT testers
As PAT testers are sophisticated instruments, it is important to make sure that they are continuing to measure correctly. If a company fails to check and maintain calibration, it could face difficulty substantiating any measurements in the event of a claim. It is usually recommended that calibration is carried out annually on a PAT testing unit.When a PAT Tester is calibrated it is re-configuring it to match the original specification. This includes:
- Calibrating the unit back to national standards. This is best performed by the product manufacturer (if they offer a calibration service) or a laboratory accredited by UKAS
- If it is mains powered, then a safety test must be carried out.
- A calibration certificate should be issued to prove the PAT unit has been electrically tested.
Dual purpose checkboxes have also been introduced which are capable of validating the accuracy of both electrical installation testers and portable appliance testers.
External links
- UK Health and Safety Executive – Portable appliance testing myths debunked
- IET/IEE Code of practice for in-service inspection and testing of electrical equipment
- HSE Maintaining electrical equipment safety