.gif)
Necking (engineering)
Encyclopedia
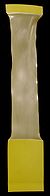
Deformation (mechanics)
Deformation in continuum mechanics is the transformation of a body from a reference configuration to a current configuration. A configuration is a set containing the positions of all particles of the body...
localize disproportionately in a small region of the material. The resulting prominent decrease in local cross-sectional area provides the basis for the name "neck". Because the local strains in the neck are large, necking is often closely associated with yielding
Yield (engineering)
The yield strength or yield point of a material is defined in engineering and materials science as the stress at which a material begins to deform plastically. Prior to the yield point the material will deform elastically and will return to its original shape when the applied stress is removed...
, a form of plastic deformation associated with ductile materials, often metals or polymers.
Formation
Necking results from an instabilityInstability
In numerous fields of study, the component of instability within a system is generally characterized by some of the outputs or internal states growing without bounds...
during tensile deformation when a material's cross-sectional area decreases by a greater proportion than the material strain hardens. Considère published the basic criterion for necking in 1885. Three concepts provide the framework for understanding neck formation.
- Before deformation, all real materials have heterogenieties such as flaws or local variations in dimensions or composition that cause local fluctuations in stressesStress (physics)In continuum mechanics, stress is a measure of the internal forces acting within a deformable body. Quantitatively, it is a measure of the average force per unit area of a surface within the body on which internal forces act. These internal forces are a reaction to external forces applied on the body...
and strains. To determine the location of the incipient neck, these fluctuations need only be infinitesimalInfinitesimalInfinitesimals have been used to express the idea of objects so small that there is no way to see them or to measure them. The word infinitesimal comes from a 17th century Modern Latin coinage infinitesimus, which originally referred to the "infinite-th" item in a series.In common speech, an...
in magnitude. - During tensile deformation the material decreases in cross-sectional area. (Poisson effect)
- During tensile deformation the material strain hardens. The amount of hardening varies with extent of deformation.
The latter two items determine the stability while the first item determines the neck's location.
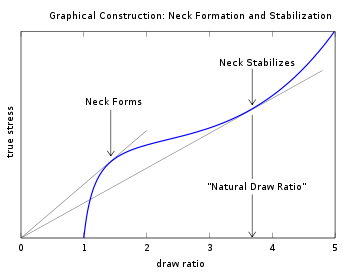
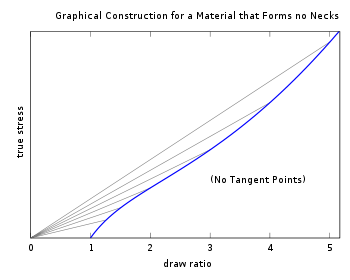
As the material deforms, all locations undergo approximately the same amount of strain as long as it hardens more than its cross-sectional area decreases, as shown at small draw ratios in the top diagram and at all draw ratios in the bottom. But if the material begins to harden by a smaller proportion than the decrease in cross-sectional area, as indicated by the first tangent point in the top diagram, strain concentrates at the location of ghdghghhdddddddd highest stress or lowest hardness. The greater the local strain, the greater the local decrease in cross-sectional area, which in turn causes even more concentration of strain, leading to an instability that causes the formation of a neck. This instability is called "geometric" or "extrinsic" because it involves the material's macroscopic decrease in cross-sectional area.