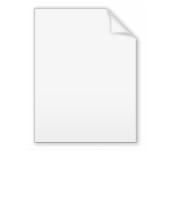
List of welding processes
Encyclopedia
This is a list of welding processes, separated into their respective categories. The associated N reference numbers (second column) are specified in ISO 4063 (in the European Union published as EN ISO 4063). Numbers in parentheses are obsolete and were removed from the current (1998) version of ISO 4063. The AWS reference codes of the American Welding Society are commonly used in North America.
Arc welding
Name | | N | | AWS | | Characteristics | | Applications |
---|---|---|---|---|
Atomic hydrogen welding Atomic hydrogen welding Atomic hydrogen welding is an arc welding process that uses an arc between two metal tungsten electrodes in a shielding atmosphere of hydrogen. The process was invented by Irving Langmuir in the course of his studies of atomic hydrogen... |
(149) | AHW | Two metal electrodes in hydrogen atmosphere | Historical |
Bare metal arc welding Bare metal arc welding Bare metal-arc welding is an arc welding process in which fusion is obtained by heating with an unshielded arc between a bare or lightly coated electrode and the work. Pressure is not used and filler metal is obtained from the electrode.... |
(113) | BMAW | Consummable electrode, no flux or shielding gas | Historical |
Carbon arc welding Carbon arc welding Carbon arc welding is a process which produces coalescence of metals by heating them with an arc between a nonconsumable carbon electrode and the work-piece. It was the first arc-welding process ever developed but is not used for many applications today, having been replaced by twin-carbon-arc... |
(181) | CAW | Carbon electrode, historical | Copper, repair (limited) |
Flux cored arc welding | 136 137 |
FCAW FCAW-S |
Continuous consumable electrode filled with flux | Industry, construction |
Gas metal arc welding Gas metal arc welding Gas metal arc welding , sometimes referred to by its subtypes metal inert gas welding or metal active gas welding, is a semi-automatic or automatic arc welding process in which a continuous and consumable wire electrode and a shielding gas are fed through a welding gun... ¹ |
131 135 |
GMAW | Continuous consumable electrode and shielding gas Shielding gas Shielding gases are inert or semi-inert gases that are commonly used in several welding processes, most notably gas metal arc welding and gas tungsten arc welding . Their purpose is to protect the weld area from atmospheric gases, such as oxygen, nitrogen, carbon dioxide, and water vapour... |
Industry |
Gas tungsten arc welding Gas tungsten arc welding Gas tungsten arc welding , also known as tungsten inert gas welding, is an arc welding process that uses a nonconsumable tungsten electrode to produce the weld... ² |
141 | GTAW | Nonconsumable electrode, slow, high quality welds | Aerospace |
Plasma arc welding Plasma arc welding Plasma arc welding is an arc welding process similar to gas tungsten arc welding . The electric arc is formed between an electrode and the workpiece... |
15 | PAW | Nonconsumable electrode, constricted arc | Tubing, instrumentation |
Shielded metal arc welding Shielded metal arc welding Shielded metal arc welding , also known as manual metal arc welding, flux shielded arc welding or informally as stick welding, is a manual arc welding process that uses a consumable electrode coated in flux to lay the weld... ³ |
111 | SMAW | Consumable electrode covered in flux, can weld any metal as long as they have the right electrode | Construction, outdoors |
Submerged arc welding Submerged arc welding Submerged arc welding is a common arc welding process. Originally developed by the Linde - Union Carbide Company. It requires a continuously fed consumable solid or tubular electrode... |
12 | SAW | Automatic, arc submerged in granular flux |
- Also known as metal inert gas (MIG) welding or metal active gas (MAG) welding
- Also known as tungsten inert gas (TIG) welding
- Also known as manual metal arc (MMA) welding or stick welding
Oxyfuel gas welding
Name | | N | | AWS | | Characteristics | | Applications |
---|---|---|---|---|
Air acetylene welding | (321) | AAW | Chemical welding process, not popular | Limited |
Oxyacetylene welding | 311 | OAW | Combustion of acetylene with oxygen produces high-temperature flame, inexpensive equipment | Maintenance, repair |
Oxygen/Propane welding | 312 | Gas welding with oxygen/propane Propane Propane is a three-carbon alkane with the molecular formula , normally a gas, but compressible to a transportable liquid. A by-product of natural gas processing and petroleum refining, it is commonly used as a fuel for engines, oxy-gas torches, barbecues, portable stoves, and residential central... flame |
||
Oxyhydrogen welding | 313 | OHW | Combustion of hydrogen with oxygen produces flame | Limited |
Pressure gas welding | PGW | Gas flames heat surfaces and pressure produces the weld | Pipe, railroad rails (limited) |
Resistance welding
Name | | N | | AWS | | Characteristics | | Applications |
---|---|---|---|---|
Resistance spot welding | 21 | RSW | Two pointed electrodes apply pressure and current to two or more thin workpieces | Automobile industry, Aerospace industry |
Resistance seam welding | 22 | ERW | Two wheel-shaped electrodes roll along workpieces, applying pressure and current | Aerospace industry |
Projection welding | 23 | PW | ||
Flash welding Flash welding Flash welding is a type of resistance welding that involves pressing two ends together, while simultaneously running a current between them. This has the effect of forming a joint between the two metals that is free of oxides as the surfaces of the two joining parts is forced out the sides of the... |
24 | FW | ||
Upset welding Upset welding Upset welding is a welding technique that produces coalescence simultaneously over the entire area of abutting surfaces or progressively along a joint, by the heat obtained from resistance to electric current through the area where those surfaces are in contact.Pressure is applied before heating... |
25 | RSEW | Butt joint surfaces heated and brought together by force |
Solid-state welding
Name | | N | | AWS | | Characteristics | | Applications |
---|---|---|---|---|
Coextrusion welding | CEW | Dissimilar metals are extruded through the same die | Joining of corrosion resistant alloys to cheaper alloys | |
Cold pressure welding | 48 | CW | Joining of soft alloys such as copper and aluminium below their melting point | Electrical contacts |
Diffusion welding Diffusion welding Diffusion welding is a solid state welding process by which two metals can be bonded together. Diffusion involves the migration of atoms across the joint, due to concentration gradients. The two materials are pressed together at an elevated temperature usually between 50 and 70% of the melting... |
45 | DFW | No weld line visible | Titanium pump impellor wheels |
Explosion welding Explosion welding Explosion welding is a solid state process where welding is accomplished by accelerating one of the components at extremely high velocity through the use of chemical explosives. This process is most commonly utilized to clad carbon steel plate with a thin layer of corrosion resistant material... |
441 | EXW | Joining of dissimilar materials, e.g. corrosion resistant alloys to structural steels | Transitition joints for chemical industry and shipbuilding. Bimetal pipelines |
Electromagnetic pulse welding Magnetic pulse welding Magnetic pulse welding is a welding process that uses magnetic forces to drive two workpieces together and weld them together. The welding mechanism is most similar to that in explosion welding.-Process:... |
Tubes or sheets are accelerated by electromagnetic forces. Oxides are expelled during impact | Automotive industry, pressure vessels, dissimilar material joints | ||
Forge welding Forge welding Forge welding is a solid-state welding process that joins two pieces of metal by heating them to a high temperature and then hammering them together. The process is one of the simplest methods of joining metals and has been used since ancient times. Forge welding is versatile, being able to join a... |
(43) | FOW | The oldest welding process in the world. Oxides must be removed by flux or flames. | Damascus steel Damascus steel Damascus steel was a term used by several Western cultures from the Medieval period onward to describe a type of steel used in swordmaking from about 300 BCE to 1700 CE. These swords are characterized by distinctive patterns of banding and mottling reminiscent of flowing water... |
Friction welding Friction welding Friction welding is a class of solid-state welding processes that generates heat through mechanical friction between a moving workpiece and a stationary component, with the addition of a lateral force called "upset" to plastically displace and fuse the materials... |
42 | FRW | Thin heat affected zone, oxides disrupted by friction, needs sufficient pressure | Aerospace industry, railway, land transport |
Friction stir welding Friction stir welding Friction-stir welding is a solid-state joining process and is used for applications where the original metal characteristics must remain unchanged as far as possible... |
FSW | A rotating consumable tool is traversed along the joint line | Shipbuilding, aerospace, railway rolling stock, automotive industry | |
Hot pressure welding | HPW | Metals are pressed together at elevated tempeartures below the melting point in vacuum or an inert gas athmosphere | Aerospace components | |
Hot isostatic pressure welding Hot isostatic pressing Hot isostatic pressing is a manufacturing process used to reduce the porosity of metals and influence the density of many ceramic materials. This improves the material's mechanical properties and workability.... |
47 | HPW | A hot inert gas applies the pressure inside a pressure vessel, i.e. an autoclave Autoclave An autoclave is an instrument used to sterilize equipment and supplies by subjecting them to high pressure saturated steam at 121 °C for around 15–20 minutes depending on the size of the load and the contents. It was invented by Charles Chamberland in 1879, although a precursor known as the... |
Aerospace components |
Roll welding | ROW | Bimetallic materials are joined by forcing them between two rotating wheels | Dissimilar materials | |
Ultrasonic welding Ultrasonic welding Ultrasonic welding is an industrial technique whereby high-frequency ultrasonic acoustic vibrations are locally applied to workpieces being held together under pressure to create a solid-state weld. It is commonly used for plastics, and especially for joining dissimilar materials... |
41 | USW | High-frequency vibratory energy is applied to foils, thin metal sheets or plastics. | Solar industry. Electronics. Rear lights of cars. |
Other welding
Name | | N | | AWS | | Characteristics | | Applications |
---|---|---|---|---|
Electron beam welding Electron beam welding Electron beam welding is a fusion welding process in which a beam of high-velocity electrons is applied to the materials being joined. The workpieces melt as the kinetic energy of the electrons is transformed into heat upon impact, and the filler metal, if used, also melts to form part of the weld... |
51 511 |
EBW | Deep penetration, fast, high equipment cost | |
Electroslag welding Electroslag welding Electroslag welding ' is a highly productive, single pass welding process for thick materials in a vertical or close to vertical position. is similar to electrogas welding, but the main difference is the arc starts in a different location... |
72 | ESW | Welds thick workpieces quickly, vertical position, steel only, continuous consumable electrode. |
Heavy plate fabrication, construction Construction, shipbuilding. |
Flow welding | ||||
Induction welding Induction welding Induction welding is a form of welding that uses electromagnetic induction to heat the workpiece. The welding apparatus contains an induction coil that is energised with a radio-frequency electric current. This generates a high-frequency electromagnetic field that acts on either an electrically... |
74 | IW | ||
Laser beam welding Laser beam welding Laser beam welding is a welding technique used to join multiple pieces of metal through the use of a laser. The beam provides a concentrated heat source, allowing for narrow, deep welds and high welding rates... |
521 522 |
LBW | Deep penetration, fast, high equipment cost | Automotive industry |
Laser-hybrid welding Laser-hybrid welding Laser Hybrid welding is a type of welding process that combines the principles of laser beam welding and arc welding.The combination of laser light and an electrical arc into an amalgamated welding process has existed since the 1970s, but has only recently been used in industrial applications... |
Combines LBW Laser beam welding Laser beam welding is a welding technique used to join multiple pieces of metal through the use of a laser. The beam provides a concentrated heat source, allowing for narrow, deep welds and high welding rates... with GMAW Gas metal arc welding Gas metal arc welding , sometimes referred to by its subtypes metal inert gas welding or metal active gas welding, is a semi-automatic or automatic arc welding process in which a continuous and consumable wire electrode and a shielding gas are fed through a welding gun... in the same welding head, able to bridge gaps up to 2mm (between plates), previously not possible with LBW alone. |
Automotive, Shipbuilding, Steelwork industries | ||
Percussion welding Percussion Welding Percussion welding is a type of resistance welding that blends dissimilar metals together. Percussion welding creates a high temperature arc that is formed from a short quick electrical discharge. Immediately following the electrical discharge, pressure is applied which forges the materials together... |
77 | PEW | Following an electrical discharge, pressure is applied which forges the materials together | Components of switch gear devices |
Thermite welding | 71 | TW | Exothermic reaction between alumnium powder and iron oxide powder | Railway tracks |
Electrogas welding Electrogas welding Electrogas welding is a continuous vertical position arc welding process developed in 1961, in which an arc is struck between a consumable electrode and the workpiece. A shielding gas is sometimes used, but pressure is not applied... |
73 | Continuous consumable electrode, vertical positioning, steel only | Storage tanks, shipbuilding | |
Stud arc welding | 78 | Welds studs to base material with heat and pressure | ||