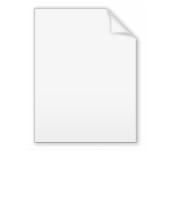
Korndörfer autotransformer starter
Encyclopedia
The reduced voltage autotransformer starter or Korndorfer starter
was invented in 1908, by Max Korndörfer of Berlin
. He filed the application with the U.S. Patent office in May 1908 and was granted the patent US 1,096,922 in May 1914. Max Korndörfer assigned his patent to the General Electric Company.
An induction motor
draws very high starting current during its acceleration to full rated speed,
typically 6 to 10 times the full load current. Reduced starting current is desirable where the electrical grid is not of sufficiant capacity, or where the driven load cannot withstand high starting torque.
One basic method to reduce the starting current is with a reduced voltage autotransformer with
taps at 50%, 65% and 80% of the applied line voltage; once the motor is started the autotransformer
is switched out of circuit.
The fourth method is with the star switch closed and as the motor accelerates a change over is made from the reduced voltage tap on the autotransformer to direct-on-line.
The starting sequence is :-
Manufactures offer their reduced voltage autotransformer in two configurations, with a 2 coil construction or with a 3 coil construction, figures 2 and 3.
Each apparatus has reduced voltage taps at 50%, 65% and 80% based upon National Electrical Manufacturers Association
recommendations.
The phase coils are traditional wound in a single coil assembly with the 0 to 50% winding section buried below the 50% to 100% windings in a single thermal mass as shown in figures 2 and 3
Figure 4 shows an improved 1000kW 11,000 Volt motor starter autotransformer with
The cast resin construction of the autotransformer may have a plurality of separate coils. This allows the selection of motor starting torque to be closely matched with the driven load requirements. Selection is by means of the connection links between the pluralities of winding sections.
The thermal dissipation of the first starting stage is maximised by being a physically separated winding from the windings of the second starting step to full line voltage.
The IEEE paper Gill, John, D “ Transfer of Motor Loads between Out-of-Phase Sources” paper IPSD 78-60, presented at the 1978 Industry Applications Society Annual Meeting, Toronto, ON, Canada October 1-5, provides evidence to the danger of using “Open Circuit Transition” in the reduced voltage Autotransformer motor starter apparatus.
There is only one recommended method to be used to switch from the first starting stage at reduced voltage to the second final stage of full voltage and that is by “closed transition” , the other method used by those unskilled in the art is an “open transition”. The “open transition” control scheme disconnects the motor from the power source causing the motor to slow down and get out of sync with the power phase, once reconnected, mechanical and electrical transients may damage the motor or its drive train.
Even with “closed transition” there is a transient produced at contact separation of the Star point switch, until recently discovered, this transient in the motor current from switching from the reduced voltage stage to full line voltage has not been recognised as a transient event by electrical engineers.
The transient is of a very short duration, less than 5 microseconds and occurs when the motor current from the secondary of the autotransformer is forced to the line voltage. This is a very fast event and is the origin of the destructive voltage transients that have caused major breakdowns of large medium and high voltage starters >1000kW.
Michael Faraday
D.C.L, F.R.S, in 1831 published a paper on his discovery of electromagnetic induction which is the time rate of change of the magnetic flux with a coil induces a voltage in that coil, the amplitude of the induced voltage is proportional to the velocity of flux linkages with the coil. With normal operation a step-up autotransformer would have flux linkages at the supply frequency; in the case of a very fast dv/dt at the instant of contact separation, the voltage induced into the redundant windings of the first starting stage, will be extremely large.
This basic principle explains the source of the destructive transient voltage in the Korndörfer motor starter apparatus.
A further transient problem is that with a single coil construction and a star switch, the autotransformer acts as a step-up transformer during the <5 microsecond period at contact separation of the Star point switch. With the motor connected to the 80% voltage tap there will be an escalation of the transient by 5:1 ratio.
To reduce the risk of any voltage surge it is desirable to replace the Korndörfer motor starter circuit with an autotransformer that has a central switch circuit that disconnects redundant windings of the first starting stage from the circuit at the transition, thereby preventing any step-up transformer connection and voltage escalation.
The root cause of destructive transients in Korndörfer starters, it is random switching of the changeover of motor current. The uncontrolled timing of the changeover allows the peak motor current to be switched at any point on the wave. Figure 5 shows the changeover at 90 degrees. This is a worst case scenario, peak current at changeover, creates a very high and fast transient.
The central switch circuit prevents voltage escalation, as discussed above.
It is therefore desirable to control the point on the wave at which to switch, the ideal point is when the motor amperes to the lowest value in all the active windings of the autotransformer.
A 3-coil autotransformer requires a 3 pole switch to control 3 phase voltages, an examination of figure 9 shows three sine waves displaced at 120 degree intervals.
There appears there is no real point on the cycle where all three phases can be switched simultaneously at any equal low motor amperage without resorting to complex staggered switching methods.
(Left)Figure 9.-3 phase power sine curves (Right)Figure 10. 3-coil Schematic
(Left)Figure11. 2-Coil 2 Phase Sine Curves (Right)Figure 12. 2-Coil Schematic
With the 2-coil autotransformer, it has only two active windings that are required to be switched at transition.
Figure 11 shows the motor current curves for a 2-coil.autotransformer,
Line 2 is not switched.
This topology is suitable for controlled switching,
Therefore the magnetic core flux in first leg of the transformer is the same as the magnetic core flux in the third leg, the centre leg has no windings and its magnetic flux is of no interest.At 30 degrees the amplitude of the motor currents supplied by the autotransformer are only half the peak motor current that occurs at 90 degrees.
(sine30° = 0.5) see Figure 8.
The central switch is therefore the means to prevent any step-up autotransformer connection and a practicable means of controlling the switching transient to a lower value than the star connected switch.
The important points for controlled central switching are:
The central switch may be an electromechanical switch or an electronic device using IGBT, EMT or other similar solid-state devices.
The electronic central switch has only to open its circuit forcing the motor current to transfer into the 80% winding in a no-break, closed transition action. It can provide frictionless, accurate and instant switching actions that are necessary to operate the changeover point at 30 degrees.
A method of detecting current zero crossing is required to provide the timing measurement for controlled switching. A current to voltage transformer is used for accurate triggering of such a timing signal for a controled switch opening.
Electromechanical central switch has to be carefully selected as it has inherent operating times both opening and closing, it has to have a stored-energy mechanism and a DC operated release solenoid for a controllable “open” command signal.
Detection of the motor current zero crossing may be obtained from a current transformer/resistor voltage sensing circuit, not a voltage crossing.
The use of electromechanical contactors is not recommended for a central switch as their switch opening speed consistency is subjected to the voltage applied to the hold-in coil, during a motor start the line voltage drop will fluctuate and the magnetic flux in the hold-in device will also vary, causing deviations in opening times.
The change in motor starting current from the reduced voltage stage can be minimised by switching at transition to a primary reactor second starting stage. In his patent Max Korndörfer shows an external reactor coil method "so as to make the gradation in voltage between steps" before a changeover to direct-on-line.
The external reactor coil method for a second starting stage has merit, as the voltage to the motor is a function of the motor current taken from the line. It can be seen that during a second stage with a series reactor, that during acceleration the motor voltage will rise as the line current drops. This relationship results in greater acceleration energy to a higher motor speed and less disturbance at changeover to full line voltage.
General Electric
engineers attempted to improve Korndörfer Methods but neither methods proposed were successful.
The application of controlled, point-on-wave switching reduces by 50%, the fast dv/dt transient surge in the autotransformer at change over from the secondary to the primary supply.
The 2-coil Autotransformer is more suited for controlled switching than the 3-coil transformer. It allows switching to be made at a precise point-on- wave that has the core fluxes equal and flowing in the same direction through the legs of the autotransformer, switching a balanced transformer is a preferred method.
A method for reducing the current surge produced by switching from reduce voltage starting to an external primary reactor stage before direct-on-line running is an optional starting method shown in the Korndörfer original patent, as per Fig 13,14,15
US patent 7,633,260 shows a variable reactor and central switched autotransformer starter for improved control of starting current and changeover for mission critical motor drives.
Knowledge of the above advances in the art, may mean that the supply /r installation of the star switched Korndörfer autotransformer, could attract liability claims by the end user, when a destructive transients cause losses in production or environmental damage.
The use of random switching methods with a star switched medium voltage autotransformer will sooner or later generate destructive transients, changing to a central switch will reduce such transients by up to a factor of 5.
The application of controlled switching as it is know skilled in the art will reduce any switching transients by a further 50%.
Existing autotransformer starters will require a replacment of the single coil construction with plurarity of coil section, the star switch reused as a central switch with some simple wiring changes, a practical and cost effective upgrade.
IEC 60947-4-1 Ed 3.0 2009 Part 4-1: Low Voltage Switchgear and Controlgear.
Contactors and Motor Starters-
Electromechanical Contactors and Motor Starters.
Korndorfer starter
Korndorfer starter is a technique used for soft starting of induction motors. The circuit uses a three-phase autotransformer and three three-phase switches....
was invented in 1908, by Max Korndörfer of Berlin
Berlin
Berlin is the capital city of Germany and is one of the 16 states of Germany. With a population of 3.45 million people, Berlin is Germany's largest city. It is the second most populous city proper and the seventh most populous urban area in the European Union...
. He filed the application with the U.S. Patent office in May 1908 and was granted the patent US 1,096,922 in May 1914. Max Korndörfer assigned his patent to the General Electric Company.
An induction motor
Induction motor
An induction or asynchronous motor is a type of AC motor where power is supplied to the rotor by means of electromagnetic induction. These motors are widely used in industrial drives, particularly polyphase induction motors, because they are robust and have no brushes...
draws very high starting current during its acceleration to full rated speed,
typically 6 to 10 times the full load current. Reduced starting current is desirable where the electrical grid is not of sufficiant capacity, or where the driven load cannot withstand high starting torque.
One basic method to reduce the starting current is with a reduced voltage autotransformer with
taps at 50%, 65% and 80% of the applied line voltage; once the motor is started the autotransformer
is switched out of circuit.
Description of the Korndörfer patent 1,096,922
Max Korndörfer claimed four methods of using an autotransformer for reduced voltage motor starting. Three of the methods are not used by the industry and it is the 4th method of starting that has been in use for more than a hundred yearsThe fourth method is with the star switch closed and as the motor accelerates a change over is made from the reduced voltage tap on the autotransformer to direct-on-line.
The starting sequence is :-
- The Star switch is closed
- The Start switch is closed to energise the autotransformer
- The motor is connected at a selected reduced voltage tap on the autotransformer and starts to turn and accelerate
- After a predetermined period the Star switch will open
- After a mili-second delay the Run switch will close, connecting full line voltage to the motor
- The Start switch will then open and the motor will be at operational speed
Operation of Improved Korndörfer Autotransformer Starter (2007)
Since 1920, the autotransformer starter has been the most popular device for reducing the starting current inrush for induction motors; it provides maximum starting torque with minimum line current.Table 1 - Starting Torque /Current with 3 Reduced Voltage taps
Voltage | 50%tap | 65%tap | 80%tap |
Torque | 25% | 42% | 64% |
Current | 50% | 65% | 80% |
Manufactures offer their reduced voltage autotransformer in two configurations, with a 2 coil construction or with a 3 coil construction, figures 2 and 3.
Each apparatus has reduced voltage taps at 50%, 65% and 80% based upon National Electrical Manufacturers Association
National Electrical Manufacturers Association
is the association of electrical and medical imaging equipment manufacturers. Founded in 1926 and headquartered near Washington, D.C., its approximately manufacture products used in the generation, transmission, distribution, control, and end use of electricity. These products are used in utility,...
recommendations.
The phase coils are traditional wound in a single coil assembly with the 0 to 50% winding section buried below the 50% to 100% windings in a single thermal mass as shown in figures 2 and 3
Figure 4 shows an improved 1000kW 11,000 Volt motor starter autotransformer with
- Axial cooling fans,
- Cast resin encapsulated coils,
- A plurality of windings providing a means of connection as a central switching apparatus,
- 9 starting voltage tap connections allowing for ± 5% variation of starting torque around NEMANémaNéma is a town in southeastern Mauritania, close to the border with Mali. It is located at around . It is the capital of Hodh Ech Chargui Region and of the Néma Department....
recommended taps at 50%, 65% and 80%.
Table 2 - Starting Torque /Current with 9 Reduced Voltage Connections
Voltage | 45% | 50% | 55% | 60% | 65% | 70% | 75% | 80% | 85% |
Torque | 20% | 25% | 30% | 36% | 42% | 49% | 56% | 64% | 72% |
Current | 45% | 50% | 55% | 60% | 65% | 70% | 75% | 80% | 85% |
The cast resin construction of the autotransformer may have a plurality of separate coils. This allows the selection of motor starting torque to be closely matched with the driven load requirements. Selection is by means of the connection links between the pluralities of winding sections.
The thermal dissipation of the first starting stage is maximised by being a physically separated winding from the windings of the second starting step to full line voltage.
The IEEE paper Gill, John, D “ Transfer of Motor Loads between Out-of-Phase Sources” paper IPSD 78-60, presented at the 1978 Industry Applications Society Annual Meeting, Toronto, ON, Canada October 1-5, provides evidence to the danger of using “Open Circuit Transition” in the reduced voltage Autotransformer motor starter apparatus.
Uses and Styles
The Autotransformer motor starting apparatus,- Is a simple circuit easily maintained and repaired by electricians with basic training,
- It contains no electronic circuitry requiring a university graduate skilled in the art to repair/maintain,
- It supplies a reduced voltage to the motor that is a clean sine wave, no sharp rise times and limited harmonic content,
- It does not have a limitation on the length of cable from the starter to the motor , no special shielding is required or line filters or load reactors or harmonic filters,
- It does not cause erosion problems with motor bearings, common to some electronic drives,
- It can operate in adverse ambient conditions that would fry a electronic motor starter,
- It does not require continuous air cooling during its run time or a de-ionized water cooling systems of pumps and heat exchangers to maintain any semiconductor components at a safe temperature during operation.
- It has a higher MTBF when compared with the Star Switch Korndörfer Autotransformer Circuit
- It provides the maximum torque with a minimum of line current
Performance
The low voltage (<600V) Korndörfer motor starter is a proven workhorse over the years, however large medium/ high voltage motor starters has been reported random autotransformer failures, most with destructive transients at transition from the first starting stage /step and the origin of these destructive flashovers cannot be explained by electrical engineers, the only solution suggested is to fit surge arresters to limit by clipping the amplitude of the transient surges.There is only one recommended method to be used to switch from the first starting stage at reduced voltage to the second final stage of full voltage and that is by “closed transition” , the other method used by those unskilled in the art is an “open transition”. The “open transition” control scheme disconnects the motor from the power source causing the motor to slow down and get out of sync with the power phase, once reconnected, mechanical and electrical transients may damage the motor or its drive train.
Even with “closed transition” there is a transient produced at contact separation of the Star point switch, until recently discovered, this transient in the motor current from switching from the reduced voltage stage to full line voltage has not been recognised as a transient event by electrical engineers.
The transient is of a very short duration, less than 5 microseconds and occurs when the motor current from the secondary of the autotransformer is forced to the line voltage. This is a very fast event and is the origin of the destructive voltage transients that have caused major breakdowns of large medium and high voltage starters >1000kW.
Michael Faraday
Michael Faraday
Michael Faraday, FRS was an English chemist and physicist who contributed to the fields of electromagnetism and electrochemistry....
D.C.L, F.R.S, in 1831 published a paper on his discovery of electromagnetic induction which is the time rate of change of the magnetic flux with a coil induces a voltage in that coil, the amplitude of the induced voltage is proportional to the velocity of flux linkages with the coil. With normal operation a step-up autotransformer would have flux linkages at the supply frequency; in the case of a very fast dv/dt at the instant of contact separation, the voltage induced into the redundant windings of the first starting stage, will be extremely large.
This basic principle explains the source of the destructive transient voltage in the Korndörfer motor starter apparatus.
A further transient problem is that with a single coil construction and a star switch, the autotransformer acts as a step-up transformer during the <5 microsecond period at contact separation of the Star point switch. With the motor connected to the 80% voltage tap there will be an escalation of the transient by 5:1 ratio.
Star Switched Method of Starting
The low voltage Korndörfer autotransformer motor starter <600 volts is also subject to a similar voltage transient with a fast rise wave front, however with a lower operating voltage and state of the art insulation materials in use may be a factor that contributes to its longevity.To reduce the risk of any voltage surge it is desirable to replace the Korndörfer motor starter circuit with an autotransformer that has a central switch circuit that disconnects redundant windings of the first starting stage from the circuit at the transition, thereby preventing any step-up transformer connection and voltage escalation.
Controlled Switching to Reduce Destructive Transients
Destructive Transients are fast dv/dt events between 30,000 - 70,000 Volts/usThe root cause of destructive transients in Korndörfer starters, it is random switching of the changeover of motor current. The uncontrolled timing of the changeover allows the peak motor current to be switched at any point on the wave. Figure 5 shows the changeover at 90 degrees. This is a worst case scenario, peak current at changeover, creates a very high and fast transient.
The central switch circuit prevents voltage escalation, as discussed above.
It is therefore desirable to control the point on the wave at which to switch, the ideal point is when the motor amperes to the lowest value in all the active windings of the autotransformer.
A 3-coil autotransformer requires a 3 pole switch to control 3 phase voltages, an examination of figure 9 shows three sine waves displaced at 120 degree intervals.
There appears there is no real point on the cycle where all three phases can be switched simultaneously at any equal low motor amperage without resorting to complex staggered switching methods.
(Left)Figure 9.-3 phase power sine curves (Right)Figure 10. 3-coil Schematic
(Left)Figure11. 2-Coil 2 Phase Sine Curves (Right)Figure 12. 2-Coil Schematic
With the 2-coil autotransformer, it has only two active windings that are required to be switched at transition.
Figure 11 shows the motor current curves for a 2-coil.autotransformer,
Line 2 is not switched.
This topology is suitable for controlled switching,
- An inspection of the sine curves shows that at 30 degrees and 210 degrees, both motor currents are at the same value
- And in the same phase quadrant.
Therefore the magnetic core flux in first leg of the transformer is the same as the magnetic core flux in the third leg, the centre leg has no windings and its magnetic flux is of no interest.At 30 degrees the amplitude of the motor currents supplied by the autotransformer are only half the peak motor current that occurs at 90 degrees.
(sine30° = 0.5) see Figure 8.
The central switch is therefore the means to prevent any step-up autotransformer connection and a practicable means of controlling the switching transient to a lower value than the star connected switch.
The important points for controlled central switching are:
- The central switch is closed before the motor has power supplied,
- There is no break in motor current, only a transfer of current,
- A synchronized, controlled opening of the central switch.
- Synchronized by means of zero crossing of the motor current waveform.
The central switch may be an electromechanical switch or an electronic device using IGBT, EMT or other similar solid-state devices.
The electronic central switch has only to open its circuit forcing the motor current to transfer into the 80% winding in a no-break, closed transition action. It can provide frictionless, accurate and instant switching actions that are necessary to operate the changeover point at 30 degrees.
A method of detecting current zero crossing is required to provide the timing measurement for controlled switching. A current to voltage transformer is used for accurate triggering of such a timing signal for a controled switch opening.
Electromechanical central switch has to be carefully selected as it has inherent operating times both opening and closing, it has to have a stored-energy mechanism and a DC operated release solenoid for a controllable “open” command signal.
Detection of the motor current zero crossing may be obtained from a current transformer/resistor voltage sensing circuit, not a voltage crossing.
The use of electromechanical contactors is not recommended for a central switch as their switch opening speed consistency is subjected to the voltage applied to the hold-in coil, during a motor start the line voltage drop will fluctuate and the magnetic flux in the hold-in device will also vary, causing deviations in opening times.
Controlled Switching for reducing motor current surge
Motor current surge is the step change from reduced voltage to direct-on-lineThe change in motor starting current from the reduced voltage stage can be minimised by switching at transition to a primary reactor second starting stage. In his patent Max Korndörfer shows an external reactor coil method "so as to make the gradation in voltage between steps" before a changeover to direct-on-line.
The external reactor coil method for a second starting stage has merit, as the voltage to the motor is a function of the motor current taken from the line. It can be seen that during a second stage with a series reactor, that during acceleration the motor voltage will rise as the line current drops. This relationship results in greater acceleration energy to a higher motor speed and less disturbance at changeover to full line voltage.
General Electric
General Electric
General Electric Company , or GE, is an American multinational conglomerate corporation incorporated in Schenectady, New York and headquartered in Fairfield, Connecticut, United States...
engineers attempted to improve Korndörfer Methods but neither methods proposed were successful.
Conclusions
The object is to reduce destructive transients in the Korndörfer autotransformer starter, by relocation of the “Star” switch as a “Central” switch.The application of controlled, point-on-wave switching reduces by 50%, the fast dv/dt transient surge in the autotransformer at change over from the secondary to the primary supply.
The 2-coil Autotransformer is more suited for controlled switching than the 3-coil transformer. It allows switching to be made at a precise point-on- wave that has the core fluxes equal and flowing in the same direction through the legs of the autotransformer, switching a balanced transformer is a preferred method.
A method for reducing the current surge produced by switching from reduce voltage starting to an external primary reactor stage before direct-on-line running is an optional starting method shown in the Korndörfer original patent, as per Fig 13,14,15
US patent 7,633,260 shows a variable reactor and central switched autotransformer starter for improved control of starting current and changeover for mission critical motor drives.
Knowledge of the above advances in the art, may mean that the supply /r installation of the star switched Korndörfer autotransformer, could attract liability claims by the end user, when a destructive transients cause losses in production or environmental damage.
The use of random switching methods with a star switched medium voltage autotransformer will sooner or later generate destructive transients, changing to a central switch will reduce such transients by up to a factor of 5.
The application of controlled switching as it is know skilled in the art will reduce any switching transients by a further 50%.
Existing autotransformer starters will require a replacment of the single coil construction with plurarity of coil section, the star switch reused as a central switch with some simple wiring changes, a practical and cost effective upgrade.
Standards
IEC 62271-106:2011 Part 106: Alternating Current Contactors, Contactor-based Controllers and Motor Starters. (Replaces IEC 60470:2000.)IEC 60947-4-1 Ed 3.0 2009 Part 4-1: Low Voltage Switchgear and Controlgear.
Contactors and Motor Starters-
Electromechanical Contactors and Motor Starters.