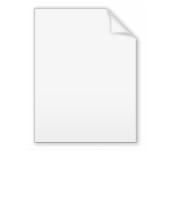
Impact extrusion
Encyclopedia
Impact extrusion is a process by which products are made with a metal slug
. The slug is pressed at a high velocity with extreme force into a die/mold by a punch.
. These machines reciprocate a cycle 20 to 60 times per minute. A cold slug is placed below the punch and over the die. The punch makes contact with the slug forcing it around the circumference of the punch and into the die. The metal slug deforms to fit the punch on the inside and the die on the outside. Lubricants are also added to aid the machines benefit for an easier punch-out. It only takes one impact for the finished shape to form from the slug. Once the slug has been contoured to the desired shape, a counter-punch ejector removes the work piece from within the die.
The thinner the wall of the work piece the tighter its tolerances are.
The end product has a better surface finish than the starting piece and the grain of the material is reformed to its new shape. This adds strength to the new form compared to cutting into the grain like in a machining process.
Slug
Slug is a common name that is normally applied to any gastropod mollusc that lacks a shell, has a very reduced shell, or has a small internal shell...
. The slug is pressed at a high velocity with extreme force into a die/mold by a punch.
Process
The punch is attached to a mechanical or hydraulic pressHydraulic press
A hydraulic is a machine using a hydraulic cylinder to generate a compressive force. It uses the hydraulic equivalenta mechanical lever, and was also known as a Bramah press after the inventor, Joseph Bramah, of England. He invented and was issued a patent on this press in 1795...
. These machines reciprocate a cycle 20 to 60 times per minute. A cold slug is placed below the punch and over the die. The punch makes contact with the slug forcing it around the circumference of the punch and into the die. The metal slug deforms to fit the punch on the inside and the die on the outside. Lubricants are also added to aid the machines benefit for an easier punch-out. It only takes one impact for the finished shape to form from the slug. Once the slug has been contoured to the desired shape, a counter-punch ejector removes the work piece from within the die.
Some Characteristics of the Process
The wall thickness of the work piece is directly correlated with the clearance between the punch and die.The thinner the wall of the work piece the tighter its tolerances are.
The end product has a better surface finish than the starting piece and the grain of the material is reformed to its new shape. This adds strength to the new form compared to cutting into the grain like in a machining process.
Effects on Work Material Properties
After going through this process the properties of the material used are altered. Its hardness and yield strength are increased, cross-sectional area is decreased, some residual surface stresses will be present and micro cracks may appear. The Physical and chemical properties are only influenced slightly.Die Style
Three major types of dies (tools) can be used. They are: forward, backward/reverse, combined, and hydrostatic extrusion. Forward extrusion pushes the slug into the die. Backward/reverse extrusion pushes the slug around the punch. Combined extrusion forces the slug both into the die and around the punch. Hydrostatic extrusion is used on brittle materials (i.e. molybdenum, beryllium, and tungsten) by applying pressure gradually to force the brittle material through the die. This is generally accomplished by the same method as forward extrusion. (1)Typical Workpiece Materials
These materials are some of the more common ones used in this process- aluminiumAluminiumAluminium or aluminum is a silvery white member of the boron group of chemical elements. It has the symbol Al, and its atomic number is 13. It is not soluble in water under normal circumstances....
- brassBrassBrass is an alloy of copper and zinc; the proportions of zinc and copper can be varied to create a range of brasses with varying properties.In comparison, bronze is principally an alloy of copper and tin...
- tinTinTin is a chemical element with the symbol Sn and atomic number 50. It is a main group metal in group 14 of the periodic table. Tin shows chemical similarity to both neighboring group 14 elements, germanium and lead and has two possible oxidation states, +2 and the slightly more stable +4...
- mild steel
- stainless steelStainless steelIn metallurgy, stainless steel, also known as inox steel or inox from French "inoxydable", is defined as a steel alloy with a minimum of 10.5 or 11% chromium content by mass....
- magnesiumMagnesiumMagnesium is a chemical element with the symbol Mg, atomic number 12, and common oxidation number +2. It is an alkaline earth metal and the eighth most abundant element in the Earth's crust and ninth in the known universe as a whole...
- titaniumTitaniumTitanium is a chemical element with the symbol Ti and atomic number 22. It has a low density and is a strong, lustrous, corrosion-resistant transition metal with a silver color....
Tool Materials
Material AISI steel | Rockwell C hardness | Applications |
---|---|---|
W1 D2 L6 S1 |
65 to 67 55 to 57 58 to 60 60 to 62 56 to 58 52 to 54 54 to 56 |
Solid die Ejector Punch Die Sleeve Stripper Ejector mandrel Punch |
Tool Geometry
When using the technique of backward impact extrusion putting an angle on the punch in the press is used to decrease the amount of pressure applied to the punch. This decreases the chance of creating a dead zone, which is an area of no pressure. While on the opposite end of things, forward impact extrusion uses a radius on punch to keep the course in the workpiece material moving.Example products made from impact extrusion
- Toothpaste tube, nozzle, impact extruded aluminium bottle, CO2 cartridge, ammunition casing (2).