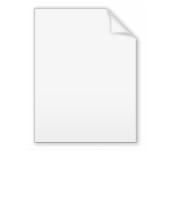
Hot working
Encyclopedia
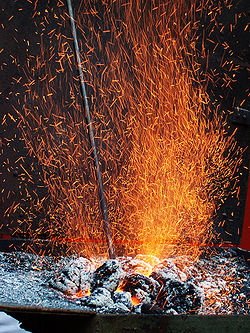
Metal
A metal , is an element, compound, or alloy that is a good conductor of both electricity and heat. Metals are usually malleable and shiny, that is they reflect most of incident light...
s are plastically deformed above their recrystallization
Recrystallization (metallurgy)
Recrystallization is a process by which deformed grains are replaced by a new set of undeformed grains that nucleate and grow until the original grains have been entirely consumed. Recrystallization is usually accompanied by a reduction in the strength and hardness of a material and a simultaneous...
temperature. Being above the recrystallization temperature allows the material to recrystallize during deformation. This is important because recrystallization keeps the materials from strain hardening, which ultimately keeps the yield strength and hardness low and ductility
Ductility
In materials science, ductility is a solid material's ability to deform under tensile stress; this is often characterized by the material's ability to be stretched into a wire. Malleability, a similar property, is a material's ability to deform under compressive stress; this is often characterized...
high. This contrasts with cold working.
Temperature
The lower limit of the hot working temperature is determined by its recrystallization temperature. As a guideline, the lower limit of the hot working temperature of a material is 0.6 times its melting temperatureMelting temperature
Melting temperature may refer to:* Melting point, the temperature at which a substance changes from solid to liquid state.* DNA melting temperature, the temperature at which a DNA double helix dissociates into single strands....
(on an absolute temperature scale). The upper limit for hot working is determined by various factors, such as: excessive oxidation, grain growth, or an undesirable phase transformation. In practice materials are usually heated to the upper limit first to keep forming forces as low as possible and to maximize the amount of time available to hot work the workpiece.
The most important aspect of any hot working process is controlling the temperature of the workpiece. 90% of the energy imparted into the workpiece is converted into heat. Therefore, if the deformation process is quick enough the temperature of the workpiece should rise, however, this does not usually happen in practice. Most of the heat is lost through the surface of the workpiece into the cooler tooling. This causes temperature gradients in the workpiece, usually due to non-uniform cross-sections where the thinner sections are cooler than the thicker sections. Ultimately, this can lead to cracking in the cooler, less ductile surfaces. One way to minimize the problem is to heat the tooling. The hotter the tooling the less heat lost to it, but as the tooling temperature rises, the tool life decreases. Therefore the tooling temperature must be compromised; commonly, hot working tooling is heated to 500–850 °F (325–450 °C).
Metal | Temperature |
---|---|
Tin | Room temperature |
Steel | 2000 °F (1,093.3 °C) |
Tungsten | 4000 °F (2,204.4 °C) |
Advantages & disadvantages
The advantages are:- Decrease in yield strength, therefore it is easier to work and uses less energy or force
- Increase in ductility
- Elevated temperatures increase diffusion which can remove or reduce chemical inhomogeneities
- Pores may reduce in size or close completely during deformation
- In steel, the weak, ductile, face-centered-cubic austeniteAusteniteAustenite, also known as gamma phase iron, is a metallic non-magnetic allotrope of iron or a solid solution of iron, with an alloying element. In plain-carbon steel, austenite exists above the critical eutectoid temperature of ; other alloys of steel have different eutectoid temperatures...
microstructure is deformed instead of the strong body-centered-cubic ferriteFerrite (iron)Ferrite or alpha iron is a materials science term for iron, or a solid solution with iron as the main constituent, with a body centred cubic crystal structure. It is the component which gives steel and cast iron their magnetic properties, and is the classic example of a ferromagnetic material...
microstructure found at lower temperatures
Usually the initial workpiece that is hot worked was originally cast
Casting
In metalworking, casting involves pouring liquid metal into a mold, which contains a hollow cavity of the desired shape, and then allowing it to cool and solidify. The solidified part is also known as a casting, which is ejected or broken out of the mold to complete the process...
. The microstructure of cast items does not optimize the engineering properties, from a microstructure standpoint. Hot working improves the engineering properties of the workpiece because it replaces the microstructure with one that has fine spherical shaped grains
Crystallite
Crystallites are small, often microscopic crystals that, held together through highly defective boundaries, constitute a polycrystalline solid. Metallurgists often refer to crystallites as grains.- Details :...
. These grains increase the strength, ductility, and toughness of the material.
The engineering properties can also be improved by reorienting the inclusions (impurities). In the cast state the inclusions are randomly oriented, which, when intersecting the surface, can be a propagation point for cracks. When the material is hot worked the inclusions tend to flow with the contour of the surface, creating stringers. As a whole the strings create a flow structure, where the properties are anisotropic (different based on direction). With the stringers oriented parallel to the surface it strengthens the workpiece, especially with respect to fracturing. The stringers act as "crack-arrestors" because the crack will want to propagate through the stringer and not along it.
The disadvantages are:
- Undesirable reactions between the metal and the surrounding atmosphere (scaling or rapid oxidation of the workpiece)
- Less precise tolerances due to thermal contraction and warping from uneven cooling
- Grain structure may vary throughout the metal for various reasons
- Requires a heating unit of some kind such as a gas or diesel furnace or an induction heater, which can be very expensive
Processes
- RollingRolling (metalworking)In metalworking, rolling is a metal forming process in which metal stock is passed through a pair of rolls. Rolling is classified according to the temperature of the metal rolled. If the temperature of the metal is above its recrystallization temperature, then the process is termed as hot rolling...
- Hot rolling
- ExtrusionExtrusionExtrusion is a process used to create objects of a fixed cross-sectional profile. A material is pushed or drawn through a die of the desired cross-section...
- ForgingForgingForging is a manufacturing process involving the shaping of metal using localized compressive forces. Forging is often classified according to the temperature at which it is performed: '"cold," "warm," or "hot" forging. Forged parts can range in weight from less than a kilogram to 580 metric tons...
- Drawing
- Rotary piercingRotary piercingRotary piercing is a hot working metalworking process for forming thick-walled seamless tubing. There are two types: the Mannesmann process and Stiefel process.-Mannesmann process:...