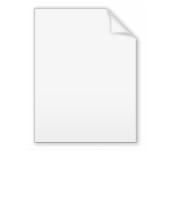
HASL
Encyclopedia
HASL or Hot Air Solder Leveling is a type of finish used on printed circuit board
s (PCB).
such that all exposed copper
surfaces are covered by solder. Excess solder is removed by scraping the PCB with hot air knives.
The HASL process consists of a pre-clean, fluxing, hot air leveling, and a post-clean. Pre-cleaning is usually done with a micro-etch. However, the usual persulfate or peroxide micro-etch is not common in the process. Dilute ferric chloride or a hydrochloric-based chemistry is favored for compatibility with the fluxes that are applied in the next step.
Fluxes perform the following functions:
Higher viscosity fluxes provide better oxidation protection and more uniform solder leveling, but reduce overall heat transfer and require a longer dwell time or higher temperature. A balance in flux use must be struck between better protection with high viscosity fluxes and superior heat transfer with lower viscosity fluxes (ref. 38).
Hot air level machines consist of a transport mechanism that carries the panel into a reservoir of molten solder (460°F, 237°C), then rapidly past jets of hot air. All areas of exposed copper are coated with solder and masked areas remain solder-free. Boards are then cleaned in hot water, the only step in the SMOBC
process where lead may enter the wastewater stream, albeit in very small quantities. Once cleaned, the panels may again enter the screening area for optional nomenclature screening, or proceed directly to the routing process.
Copper, flux and other impurities build in concentration in the solder pot as panels are processed through the hot air leveler. These impurities can be removed to some degree by performing a procedure known as drossing. From the hot operating temperature
, the temperature is reduced to 385°F (196°C) and the machine sits idle for 8 to 12 hours. The impurities will float to the surface of the solder where they are scooped out and placed in a dross bucket. This material can be returned to the vendor for reclamation of the metals. Some manufacturers go for years without changing the solder, they dross and make additions. When the time comes to change over the solder, vendors will issue credit on the purchase of new solder as long as the old solder is returned to them for processing.
The acid pre-clean will have some copper in solution and can be treated conventionally. The waste flux is collected and is sent off-site for treatment.
Printed circuit board
A printed circuit board, or PCB, is used to mechanically support and electrically connect electronic components using conductive pathways, tracks or signal traces etched from copper sheets laminated onto a non-conductive substrate. It is also referred to as printed wiring board or etched wiring...
s (PCB).
Description
The PCB is typically dipped into a bath of molten solderSolder
Solder is a fusible metal alloy used to join together metal workpieces and having a melting point below that of the workpiece.Soft solder is what is most often thought of when solder or soldering are mentioned and it typically has a melting range of . It is commonly used in electronics and...
such that all exposed copper
Copper
Copper is a chemical element with the symbol Cu and atomic number 29. It is a ductile metal with very high thermal and electrical conductivity. Pure copper is soft and malleable; an exposed surface has a reddish-orange tarnish...
surfaces are covered by solder. Excess solder is removed by scraping the PCB with hot air knives.
The HASL process consists of a pre-clean, fluxing, hot air leveling, and a post-clean. Pre-cleaning is usually done with a micro-etch. However, the usual persulfate or peroxide micro-etch is not common in the process. Dilute ferric chloride or a hydrochloric-based chemistry is favored for compatibility with the fluxes that are applied in the next step.
Fluxes perform the following functions:
- Provide oxidation protection to the pre-cleaned surface.
- Affect heat transfer during solder immersion.
- Provide oxidation protection during HASL.
Higher viscosity fluxes provide better oxidation protection and more uniform solder leveling, but reduce overall heat transfer and require a longer dwell time or higher temperature. A balance in flux use must be struck between better protection with high viscosity fluxes and superior heat transfer with lower viscosity fluxes (ref. 38).
Hot air level machines consist of a transport mechanism that carries the panel into a reservoir of molten solder (460°F, 237°C), then rapidly past jets of hot air. All areas of exposed copper are coated with solder and masked areas remain solder-free. Boards are then cleaned in hot water, the only step in the SMOBC
SMOBC
Solder Mask Over Bare Copper, also known under its acronym SMOBC, is a method of finish plating on printed circuit boards .This is done to make the "pads" on PCBs solderable and to protect the bare copper underneath from oxidizing. Several different types of materials may be used, such as tin-lead...
process where lead may enter the wastewater stream, albeit in very small quantities. Once cleaned, the panels may again enter the screening area for optional nomenclature screening, or proceed directly to the routing process.
Copper, flux and other impurities build in concentration in the solder pot as panels are processed through the hot air leveler. These impurities can be removed to some degree by performing a procedure known as drossing. From the hot operating temperature
Operating temperature
An operating temperature is the temperature at which an electrical or mechanical device operates. The device will operate effectively within a specified temperature range which varies based on the device function and application context, and ranges from the minimum operating temperature to the...
, the temperature is reduced to 385°F (196°C) and the machine sits idle for 8 to 12 hours. The impurities will float to the surface of the solder where they are scooped out and placed in a dross bucket. This material can be returned to the vendor for reclamation of the metals. Some manufacturers go for years without changing the solder, they dross and make additions. When the time comes to change over the solder, vendors will issue credit on the purchase of new solder as long as the old solder is returned to them for processing.
The acid pre-clean will have some copper in solution and can be treated conventionally. The waste flux is collected and is sent off-site for treatment.
Disadvantages of HASL
- Low planarity makes this surface finish unsuitable for use with fine pitch components
- High thermal stress during process may introduce defects to PCB