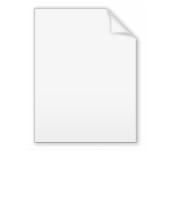
Filament winding
Encyclopedia
Filament winding is a fabrication
technique for manufacturing composite material
, usually in the form of cylindrical structures. The process involves winding filaments under varying amounts of tension over a male mould
or mandrel
. The mandrel rotates while a carriage moves horizontally, laying down fibers in the desired pattern. The most common filaments are carbon
or glass
fiber and are coated with synthetic resin as they are wound. Once the mandrel is completely covered to the desired thickness, the mandrel is placed in an oven to solidify (set) the resin. Once the resin has cured, the mandrel is removed, leaving the hollow final product.
Filament winding is well suited to automation, where the tension on the filaments can be carefully controlled. Filaments that are applied with high tension results in a final product with higher rigidity and strength; lower tension results in more flexibility. The orientation of the filaments can also be carefully controlled so that successive layers are plied
or oriented differently from the previous layer. The angle at which the fiber is laid down will determine the properties of the final product. A high angle "hoop" will provide crush strength, while a lower angle pattern (known as a closed or helical) will provide greater tensile strength.
Products currently being produced using this technique range from golf clubs
, pipes
, oars, bicycle forks, power and transmission poles, pressure vessels to missile
casings, aircraft
fuselages and lamp posts and yacht masts.
, and braiding. Compaction is through fiber tension and resin content is primarily metered. The fibers may be impregnated with resin before winding (wet winding), pre-impregnated (dry winding) or post-impregnated. Wet winding has the advantages of using the lowest cost materials with long storage life and low viscosity. The pre-impregnated systems produce parts with more consistent resin content and can often be wound faster.
Examples of filament winding machine
producers:
Manufacturing
Manufacturing is the use of machines, tools and labor to produce goods for use or sale. The term may refer to a range of human activity, from handicraft to high tech, but is most commonly applied to industrial production, in which raw materials are transformed into finished goods on a large scale...
technique for manufacturing composite material
Composite material
Composite materials, often shortened to composites or called composition materials, are engineered or naturally occurring materials made from two or more constituent materials with significantly different physical or chemical properties which remain separate and distinct at the macroscopic or...
, usually in the form of cylindrical structures. The process involves winding filaments under varying amounts of tension over a male mould
Molding (process)
Molding or moulding is the process of manufacturing by shaping pliable raw material using a rigid frame or model called a pattern....
or mandrel
Mandrel
A mandrel is one of the following:* an object used to shape machined work.* a tool component that grips or clamps materials to be machined.* a tool component that can be used to grip other moving tool components.- Variants :...
. The mandrel rotates while a carriage moves horizontally, laying down fibers in the desired pattern. The most common filaments are carbon
Carbon fiber
Carbon fiber, alternatively graphite fiber, carbon graphite or CF, is a material consisting of fibers about 5–10 μm in diameter and composed mostly of carbon atoms. The carbon atoms are bonded together in crystals that are more or less aligned parallel to the long axis of the fiber...
or glass
Fiberglass
Glass fiber is a material consisting of numerous extremely fine fibers of glass.Glassmakers throughout history have experimented with glass fibers, but mass manufacture of glass fiber was only made possible with the invention of finer machine tooling...
fiber and are coated with synthetic resin as they are wound. Once the mandrel is completely covered to the desired thickness, the mandrel is placed in an oven to solidify (set) the resin. Once the resin has cured, the mandrel is removed, leaving the hollow final product.
Filament winding is well suited to automation, where the tension on the filaments can be carefully controlled. Filaments that are applied with high tension results in a final product with higher rigidity and strength; lower tension results in more flexibility. The orientation of the filaments can also be carefully controlled so that successive layers are plied
Ply
Ply, Pli, Plies or Plying may refer to:* Ply , a turn in game play* PLY or Polygon File Format* Plying, a spinning technique to make yarn* Plies , American rapper* Pli, an academic journal...
or oriented differently from the previous layer. The angle at which the fiber is laid down will determine the properties of the final product. A high angle "hoop" will provide crush strength, while a lower angle pattern (known as a closed or helical) will provide greater tensile strength.
Products currently being produced using this technique range from golf clubs
Golf club (equipment)
A golf club is used to hit a golf ball in a game of golf. Each club is composed of a shaft with a grip and a clubhead. Woods are mainly used for long-distance fairway or tee shots; irons, the most versatile class, are used for a variety of shots; Hybrids that combine design elements of woods and...
, pipes
Piping
Within industry, piping is a system of pipes used to convey fluids from one location to another. The engineering discipline of piping design studies the efficient transport of fluid....
, oars, bicycle forks, power and transmission poles, pressure vessels to missile
Missile
Though a missile may be any thrown or launched object, it colloquially almost always refers to a self-propelled guided weapon system.-Etymology:The word missile comes from the Latin verb mittere, meaning "to send"...
casings, aircraft
Aircraft
An aircraft is a vehicle that is able to fly by gaining support from the air, or, in general, the atmosphere of a planet. An aircraft counters the force of gravity by using either static lift or by using the dynamic lift of an airfoil, or in a few cases the downward thrust from jet engines.Although...
fuselages and lamp posts and yacht masts.
Fiberglass Laminating
Filament Winding can also be described as the manufacture of parts with high fiber volume fractions and controlled fiber orientation. Fiber tows are immersed in a resin bath where they are coated with low or medium molecular weight reactants. The impregnated tows are then literally wound around a mandrel (mold core) in a controlled pattern to form the shape of the part. After winding, the resin is then cured, typically using heat. The mold core may be removed or may be left as an integral component of the part(Rosato, D.V.).This process is primarily used for hollow, generally circular or oval sectioned components, such as pipes and tanks. Pressure vessels, pipes and drive shafts have all been manufactured using filament winding. It has been combined with other fiber application methods such as hand layup, pultrusionPultrusion
Pultrusion is a continuous process for manufacture of composite materials with constant cross-section. Reinforced fibers are pulled through a resin, possibly followed by a separate preforming system, and into a heated die, where the resin undergoes polymerization...
, and braiding. Compaction is through fiber tension and resin content is primarily metered. The fibers may be impregnated with resin before winding (wet winding), pre-impregnated (dry winding) or post-impregnated. Wet winding has the advantages of using the lowest cost materials with long storage life and low viscosity. The pre-impregnated systems produce parts with more consistent resin content and can often be wound faster.
Materials
Glass fibre is the fibre most frequently used for filament winding, carbon and aramid fibres are also used. Most high strength critical aerospace structures are produced with epoxy resins, with either epoxy or cheaper polyester resins being specified for most other applications. The ability to use continuous reinforcement without any breaks or joins is a definite advantage, as is the high fibre volume fraction that is obtainable, about 60% to 80%. Only the inner surface of a filament wound structure will be smooth unless a secondary operation is performed on the outer surface. The component is normally cured at high temperature before removing the mandrel. Finishing operations such as machining or grinding are not normally necessary (Furness, J., Azom.com).Options
- Resins: Any, e.g. epoxy, polyester, vinylester, phenolic.
- Fibers: Glass, aramid, carbon and boron fibers. The fibers are used straight from a creel and not woven or stitched into a fabric form.
- Cores: Any, although components are usually single skin.
Process
- Uses a continuous length of fiber strand, roving, or tape
- Results in a shell of materials with a high strength-to-weight ratio
- Requires thermal curing of workpieces
- Patterns may be longitudinal, circumferential, or helical
Manufacturers
Examples of manufacturers that make large varieties of custom filament winding:- Saudi Arabia Amiantit, KSA
- Advanced Composites, Inc. (ACI)
- Future Pipe Industries (FPI)
- PCT
- PLP Comp
Examples of filament winding machine
Continuous filament winding machine
A continuous filament winding machine is a machine for laying filament windings continuously over a cylindrical steel band. The steel band is carried on a forward moving mandrel which is able to collapse and return to the beginning of the travel...
producers:
- TECHNOBELL LIMITED
- Entec Composite Machines
- Mikrosam A.D.
- VEM S.p.A.