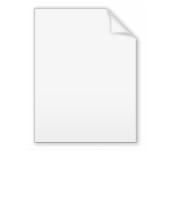
False brinelling
Encyclopedia
False brinelling is damage caused by fretting
, with or without corrosion
, that causes imprints that look similar to brinelling
, but are caused by a different mechanism. Brinell damage is characterized by permanent material deformation (without loss of material) and occurs during one load event, whereas false brinelling is characterized by material wear or removal and occurs over an extended time from vibration and light loads.
The basic cause of false brinelling is that the design of the bearing does not have a method for redistribution of lubricant without large rotational movement of all bearing surfaces in the raceway. Lubricant
is pushed out of a loaded region during small oscillatory movements and vibration where the bearings surfaces repeatedly do not move very far. Without lubricant, wear is increased when the small oscillatory movements occur again. It is possible for the resulting wear debris to oxidize and form an abrasive compound which further accelerates wear.
In normal operation, a rolling-element bearing
has the rollers and races separated by a thin layer of lubricant such as grease
or oil
. Although these lubricants normally appear liquid (not solids), under high pressure they act as solids and keep the bearing and race from touching.
If the lubricant is removed, the bearings and races can touch directly. While bearings and races appear smooth to the eye, they are microscopically rough. Thus, high points of each surface can touch, but "valleys" do not. The bearing load is thus spread over much less area increasing the contact stress, causing pieces of each surface to break off or to become pressure-welded then break off when the bearing rolls on.
The broken-off pieces are also called wear debris. Wear debris is bad because it is relatively large compared to the surrounding surface finish and thus creates more regions of high contact stress. Worse, the steel in ordinary bearings can oxidize (rust), producing a more abrasive compound which accelerates wear.
In normal operation, bearings remain lubricated. However, if a bearing is stationary but subject to a very small oscillating or vibrating load, lubricant may be pushed out of the loaded area. Since the bearing is rolling only small distances (less than roller spacing), there is no action or movement that replaces the displaced lubricant.
With the lubricant gone, the damage described above creates wear debris; and since there is a small motion in the bearing, the damage is ongoing, creating more and more wear debris; and the wear debris acts as an abrasive to further damage the bearing surfaces. Typically the races are most damaged by this action and the appearance is similar to that of brinelling (overload) damage. Thus, the damage is often described as false brinelling.
The discovery of false brinelling is unclear but one story describes how, in the 1930s, new automobiles were loaded on to trains for delivery; when they were unloaded, some would show severe wheel bearing damage. On further inspection, it turned out that many wheel bearings were slightly damaged. The damage was eventually traced to rocking of the autos and the regular impact every time a railroad car wheel passed a track joint. These conditions led to false brinelling.
Although the auto-delivery problem has been solved, there are many modern examples. For example, generator
s or pump
s may fail or need service, so it is common to have a nearby spare unit which is left off most of the time but brought in to service when needed. Surprisingly, however, vibration from the operating unit can cause bearing failure in the unit which is switched off. When that unit is turned on, the bearings may be noisy due to damage, and may fail completely within a few days or weeks even though the unit and its bearings are otherwise new. Common solutions include: keeping the spare unit at a distance from the one which is on and vibrating; manually rotating shafts of the spare units on a regular (for example, weekly) basis; or regularly switching between the units so that both are in regular (for example, weekly) operation.
Until recently, bicycle headsets
tended to suffer from false brinelling in the "straight ahead" steering position, due to small movements caused by flexing of the fork. Good modern headsets incorporate a plain bearing to accommodate this flexing, leaving the ball race to provide pure rotational movement.
Fretting
Fretting refers to wear and sometimes corrosion damage at the asperities of contact surfaces. This damage is induced under load and in the presence of repeated relative surface motion, as induced for example by vibration...
, with or without corrosion
Corrosion
Corrosion is the disintegration of an engineered material into its constituent atoms due to chemical reactions with its surroundings. In the most common use of the word, this means electrochemical oxidation of metals in reaction with an oxidant such as oxygen...
, that causes imprints that look similar to brinelling
Brinelling
Brinelling is a material surface failure caused by contact stress that exceeds the material limit. This failure is caused by just one application of a load great enough to exceed the material limit. The result is a permanent dent or "brinell" mark. It is a common cause of roller bearing failures,...
, but are caused by a different mechanism. Brinell damage is characterized by permanent material deformation (without loss of material) and occurs during one load event, whereas false brinelling is characterized by material wear or removal and occurs over an extended time from vibration and light loads.
The basic cause of false brinelling is that the design of the bearing does not have a method for redistribution of lubricant without large rotational movement of all bearing surfaces in the raceway. Lubricant
Lubricant
A lubricant is a substance introduced to reduce friction between moving surfaces. It may also have the function of transporting foreign particles and of distributing heat...
is pushed out of a loaded region during small oscillatory movements and vibration where the bearings surfaces repeatedly do not move very far. Without lubricant, wear is increased when the small oscillatory movements occur again. It is possible for the resulting wear debris to oxidize and form an abrasive compound which further accelerates wear.
In normal operation, a rolling-element bearing
Bearing (mechanical)
A bearing is a device to allow constrained relative motion between two or more parts, typically rotation or linear movement. Bearings may be classified broadly according to the motions they allow and according to their principle of operation as well as by the directions of applied loads they can...
has the rollers and races separated by a thin layer of lubricant such as grease
Grease (lubricant)
The term grease is used to describe semisolid lubricants. Although the word grease is also used to describe rendered fat of animals, in the context of lubrication, grease typically applies to a material consisting of a soap emulsified with mineral or vegetable oil...
or oil
Oil
An oil is any substance that is liquid at ambient temperatures and does not mix with water but may mix with other oils and organic solvents. This general definition includes vegetable oils, volatile essential oils, petrochemical oils, and synthetic oils....
. Although these lubricants normally appear liquid (not solids), under high pressure they act as solids and keep the bearing and race from touching.
If the lubricant is removed, the bearings and races can touch directly. While bearings and races appear smooth to the eye, they are microscopically rough. Thus, high points of each surface can touch, but "valleys" do not. The bearing load is thus spread over much less area increasing the contact stress, causing pieces of each surface to break off or to become pressure-welded then break off when the bearing rolls on.
The broken-off pieces are also called wear debris. Wear debris is bad because it is relatively large compared to the surrounding surface finish and thus creates more regions of high contact stress. Worse, the steel in ordinary bearings can oxidize (rust), producing a more abrasive compound which accelerates wear.
In normal operation, bearings remain lubricated. However, if a bearing is stationary but subject to a very small oscillating or vibrating load, lubricant may be pushed out of the loaded area. Since the bearing is rolling only small distances (less than roller spacing), there is no action or movement that replaces the displaced lubricant.
With the lubricant gone, the damage described above creates wear debris; and since there is a small motion in the bearing, the damage is ongoing, creating more and more wear debris; and the wear debris acts as an abrasive to further damage the bearing surfaces. Typically the races are most damaged by this action and the appearance is similar to that of brinelling (overload) damage. Thus, the damage is often described as false brinelling.
The discovery of false brinelling is unclear but one story describes how, in the 1930s, new automobiles were loaded on to trains for delivery; when they were unloaded, some would show severe wheel bearing damage. On further inspection, it turned out that many wheel bearings were slightly damaged. The damage was eventually traced to rocking of the autos and the regular impact every time a railroad car wheel passed a track joint. These conditions led to false brinelling.
Although the auto-delivery problem has been solved, there are many modern examples. For example, generator
Electrical generator
In electricity generation, an electric generator is a device that converts mechanical energy to electrical energy. A generator forces electric charge to flow through an external electrical circuit. It is analogous to a water pump, which causes water to flow...
s or pump
Pump
A pump is a device used to move fluids, such as liquids, gases or slurries.A pump displaces a volume by physical or mechanical action. Pumps fall into three major groups: direct lift, displacement, and gravity pumps...
s may fail or need service, so it is common to have a nearby spare unit which is left off most of the time but brought in to service when needed. Surprisingly, however, vibration from the operating unit can cause bearing failure in the unit which is switched off. When that unit is turned on, the bearings may be noisy due to damage, and may fail completely within a few days or weeks even though the unit and its bearings are otherwise new. Common solutions include: keeping the spare unit at a distance from the one which is on and vibrating; manually rotating shafts of the spare units on a regular (for example, weekly) basis; or regularly switching between the units so that both are in regular (for example, weekly) operation.
Until recently, bicycle headsets
Headset (bicycle part)
The headset is the set of components on a bicycle that provides a rotatable interface between the bicycle fork and the head tube of the bicycle frame itself. The short tube through which the steerer of the fork passes is called the head tube. A typical headset consists of two cups that are pressed...
tended to suffer from false brinelling in the "straight ahead" steering position, due to small movements caused by flexing of the fork. Good modern headsets incorporate a plain bearing to accommodate this flexing, leaving the ball race to provide pure rotational movement.