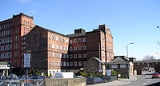
Belper North Mill
Encyclopedia
Belper North Mill, also known as Strutt's North Mill, Belper, is one of the Derwent Valley Mills
designated UNESCO World Heritage Status in 2001.
It is sited in Belper
, a town in Derbyshire
, England
roughly half way between Derby
and Matlock.
The original North Mill was completed in 1786 by Jedediah Strutt
, but was destroyed by fire in 1803. Its replacement was built in 1804 by his son, William Strutt
, on the earlier mills foundations and is one of the oldest surviving example of an industrialised iron framed 'fire-proof' building in the world. It is a central point in the Derwent Valley Mills
World Heritage Site
.
A cotton mill
was a fire hazard, the cotton dust easily ignites and burns through the ceiling and floor timbers. This had happened to previous mill on this site. To attempt to stop this happening experiments were made to construct a fireproof mill. The floor timbers were replaced with beams of cast iron
, (steel
was not available till after 1860) and between them low vaults made of brick, these has a 9 feet (2.7 m) span. Above this rubble was used to level them off and a floor made of more bricks.
The floor arches over the wheel pit were of a hollow clay construction.
Here the beams were cast in a "turtle back profile" to give the required strength, at minimum weight. They were held up by cast iron
columns, erected on top of each other. The lateral thrust of the brick arches was resisted by concealed wrought iron
ties between the column tops. The building was 15 bays wide, and the wings 6 bays wide.
This is one of the first iron frame buildings. This technology is important as it is the precursor to the steel frames used in high rise buildings. The roof was of slate and had internal gutters.
It was a suspension wheel with the power taken off at the edge by a spur wheel, this made it lighter than a clasp wheel. The power was transmitted to the machines by a vertical shaft, geared to horizontal shafts on each floor. Leather belts were used to connect the shafts to individual machines.
The raw cotton bales would be unloaded from carts at the ground floor loading bay. The opening and cleaning machines broke down the bales and prepared the cotton into 'lap' form. The lap was taken to the 3rd and 4th floors.
The 1st & 2nd floors originally housed thirty-four Arkwright Water Frames each. An Arkwright Water frames spun 4236 ends simultaneously.This meant that 4236 rovings were continuously twisted together to become threads that were collected on a small bobbins. Later some of the alternative Mule Spinning machines were introduced in order to produce the finer thread types which were being demanded. The bobbins passed to the 5th floor
On the 3rd & 4th floors were the carding rooms, housing three rows of carding engines, over 130 in total. These machines disentangle the cotton fibres to produce a long continuous 'sliver'. Sixteen drawing frames straightened out the fibres. The lantern frames pilled the slivers into 'rovings' ready for spinning, on the 1st and second floor.
On the 5th floor, reeling frames wound the spun thread into 'skeins' ready for dyeing at a factory in Milford. Doubling frames twisted two or more single spun thread together to make thicker and stronger thread. The amount of twist imparted determined the thread's properties.
The attic was later used as a schoolroom.
Derwent Valley Mills
Derwent Valley Mills is a World Heritage Site along the River Derwent in Derbyshire, England, designated in December 2001. It is administered by the Derwent Valley Mills Partnership. The modern factory, or 'mill', system was born here in the 18th century to accommodate the new technology for...
designated UNESCO World Heritage Status in 2001.
It is sited in Belper
Belper
Belper is a town and civil parish in the local government district of Amber Valley in Derbyshire, England.-Geography:Belper is situated eight miles north of Derby and is centred in the valley of the River Derwent...
, a town in Derbyshire
Derbyshire
Derbyshire is a county in the East Midlands of England. A substantial portion of the Peak District National Park lies within Derbyshire. The northern part of Derbyshire overlaps with the Pennines, a famous chain of hills and mountains. The county contains within its boundary of approx...
, England
England
England is a country that is part of the United Kingdom. It shares land borders with Scotland to the north and Wales to the west; the Irish Sea is to the north west, the Celtic Sea to the south west, with the North Sea to the east and the English Channel to the south separating it from continental...
roughly half way between Derby
Derby
Derby , is a city and unitary authority in the East Midlands region of England. It lies upon the banks of the River Derwent and is located in the south of the ceremonial county of Derbyshire. In the 2001 census, the population of the city was 233,700, whilst that of the Derby Urban Area was 229,407...
and Matlock.
The original North Mill was completed in 1786 by Jedediah Strutt
Jedediah Strutt
Jedediah Strutt or Jedidiah Strutt – as he spelt it – was a hosier and cotton spinner from Belper, England.Strutt and his brother-in-law William Woollat developed an attachment to the stocking frame that allowed the production of ribbed stockings...
, but was destroyed by fire in 1803. Its replacement was built in 1804 by his son, William Strutt
William Strutt (inventor)
William Strutt FRS, was a cotton spinner in Belper, England.-Biography:Strutt was the first son of Jedediah Strutt and, after a good education, joined his father's business at the age of fourteen...
, on the earlier mills foundations and is one of the oldest surviving example of an industrialised iron framed 'fire-proof' building in the world. It is a central point in the Derwent Valley Mills
Derwent Valley Mills
Derwent Valley Mills is a World Heritage Site along the River Derwent in Derbyshire, England, designated in December 2001. It is administered by the Derwent Valley Mills Partnership. The modern factory, or 'mill', system was born here in the 18th century to accommodate the new technology for...
World Heritage Site
World Heritage Site
A UNESCO World Heritage Site is a place that is listed by the UNESCO as of special cultural or physical significance...
.
Construction
This was an iron framed mill 127 feet (38.7 m) long by 31 feet (9.4 m) wide, 63 feet (19.2 m) high. It had two wings 41.5 feet (12.6 m) by 34 feet (10.4 m).A cotton mill
Cotton mill
A cotton mill is a factory that houses spinning and weaving machinery. Typically built between 1775 and 1930, mills spun cotton which was an important product during the Industrial Revolution....
was a fire hazard, the cotton dust easily ignites and burns through the ceiling and floor timbers. This had happened to previous mill on this site. To attempt to stop this happening experiments were made to construct a fireproof mill. The floor timbers were replaced with beams of cast iron
Cast iron
Cast iron is derived from pig iron, and while it usually refers to gray iron, it also identifies a large group of ferrous alloys which solidify with a eutectic. The color of a fractured surface can be used to identify an alloy. White cast iron is named after its white surface when fractured, due...
, (steel
Steel
Steel is an alloy that consists mostly of iron and has a carbon content between 0.2% and 2.1% by weight, depending on the grade. Carbon is the most common alloying material for iron, but various other alloying elements are used, such as manganese, chromium, vanadium, and tungsten...
was not available till after 1860) and between them low vaults made of brick, these has a 9 feet (2.7 m) span. Above this rubble was used to level them off and a floor made of more bricks.
The floor arches over the wheel pit were of a hollow clay construction.
Here the beams were cast in a "turtle back profile" to give the required strength, at minimum weight. They were held up by cast iron
Cast iron
Cast iron is derived from pig iron, and while it usually refers to gray iron, it also identifies a large group of ferrous alloys which solidify with a eutectic. The color of a fractured surface can be used to identify an alloy. White cast iron is named after its white surface when fractured, due...
columns, erected on top of each other. The lateral thrust of the brick arches was resisted by concealed wrought iron
Wrought iron
thumb|The [[Eiffel tower]] is constructed from [[puddle iron]], a form of wrought ironWrought iron is an iron alloy with a very low carbon...
ties between the column tops. The building was 15 bays wide, and the wings 6 bays wide.
This is one of the first iron frame buildings. This technology is important as it is the precursor to the steel frames used in high rise buildings. The roof was of slate and had internal gutters.
The waterwheel
The breast-shot waterwheel was built by Thomas Hewes, The wheel was 18 feet (5.5 m) by 23 feet (7 m) wide.It was a suspension wheel with the power taken off at the edge by a spur wheel, this made it lighter than a clasp wheel. The power was transmitted to the machines by a vertical shaft, geared to horizontal shafts on each floor. Leather belts were used to connect the shafts to individual machines.
The Processes
Each of the five floors housed different stages of the cotton spinning processes.The raw cotton bales would be unloaded from carts at the ground floor loading bay. The opening and cleaning machines broke down the bales and prepared the cotton into 'lap' form. The lap was taken to the 3rd and 4th floors.
The 1st & 2nd floors originally housed thirty-four Arkwright Water Frames each. An Arkwright Water frames spun 4236 ends simultaneously.This meant that 4236 rovings were continuously twisted together to become threads that were collected on a small bobbins. Later some of the alternative Mule Spinning machines were introduced in order to produce the finer thread types which were being demanded. The bobbins passed to the 5th floor
On the 3rd & 4th floors were the carding rooms, housing three rows of carding engines, over 130 in total. These machines disentangle the cotton fibres to produce a long continuous 'sliver'. Sixteen drawing frames straightened out the fibres. The lantern frames pilled the slivers into 'rovings' ready for spinning, on the 1st and second floor.
On the 5th floor, reeling frames wound the spun thread into 'skeins' ready for dyeing at a factory in Milford. Doubling frames twisted two or more single spun thread together to make thicker and stronger thread. The amount of twist imparted determined the thread's properties.
The attic was later used as a schoolroom.
Machinery
Machinery contained in this mill:-- 80 spinning frames with 4236 spindles each
- 136 carding engines
- 16 draw frames
- 4 stretching frames
- Plus reeling, doubling and twisting frames
External links
- Derwent Valley Visitor's Centre - official site
- Information and photos