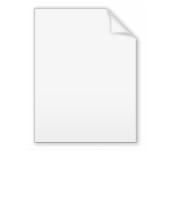
American System of Watch Manufacturing
Encyclopedia
In the mid 19th century Aaron Lufkin Dennison
became inspired by the manufacturing techniques of the United States Armory
at Springfield, Mass. The "armory practice" was mainly based on a strict system of organization, the extensive use of the machine shop and a control system based on gauges. Aaron Dennison proposed to produce watches via these techniques and, along with a few others, founded the Waltham Watch Company
.
In the rest of the world manufacturing involved making certain parts under the roof of a factory
and obtaining other parts from piece work
ers who used their own cottages as workshops.
The American system of manufacturing
by interchangeable parts
meant the establishment of working facilities for the entire manufacture. It meant that everything was made on the premises, not according to the plans or ideas or methods of work of individual workmen, but under the direct supervision of a company's foreman, according to gauges the company furnished, under conditions of time, cleanliness and care which the company prescribed.
Waltham soon found that it was necessary to invent, develop and build its own production machinery, special gauges systems adjusted to the smallest watch parts dimensions, new alloys & materials.
The chronology of production lessons at the Waltham Watch Company
can be divided into three phases:
The manufacturing of watches differed from other products that had earlier used the armory practices in two significant ways.
First, the high price of watches allowed for a large investment in research and development. The vast majority of the price of a watch was due to labor rather than materials and any system that could significantly reduce labor costs could significantly increase profits. Even after 40 years of manufacturing improvements, in 1910, labor accounted for 80% of the cost of watches made by the Elgin National Watch Company.
Secondly, watches require very strict tolerances and very few manufacturing defects. Previous products made via armory practices, such as fire arms, sewing machines, etc. had tolerances 10 to 100 times as loose. A watch gear that is offset by a few thousands of an inch from where it should be will cause increased friction, losing critical power that needed to be sent to the balance wheel and greatly accelerating the wear of the watch. Previous watch manufacturing techniques required expert watchmakers to recognize slight variations in part sizes in order to place each gear in the correct location or to make other adjustments during the manufacturing of each watch.
made by the American Watch Companyin the City of Waltham, Massachusetts in the United States of America. Prior to 1857, pocket watch
es were not made of standard parts and there was a difficulty in repairing and making the watches on a cost effective basis. Most pocketwatches made in the world were in England or France, and this was also a test for early American manufacturing to take and produce items better than the countries in Europe, where at the time was in the middle of the industrial revolution. Most of the Model 57 pocket watches were in a coin silver
, a bit different than sterling silver, that coin silver is only 80 pure.
American system of watch manufacturing in wikipedia is a great side reference on the Waltham Model 57 Pocket Watch
*http://www.pricelessads.com/m57/seminar/seminar.pdf The internal mechanical movement was key wind, and to set the watch you used the same key. Some of the Model 57 Watches were fitted in Gold
watch cases, but the majority were silver.
In order to reach these strict tolerances, watch manufactures largely manufactured their own machine tools and machine parts. Elgin manufactured almost two drill bits for each watch they manufactured. The knowledge of how to manufacture machines that could manufacture watches spread from Waltham to Elgin to dozens of other American watch companies and manufactures of other products. Techniques such as jigs, stops and measuring devices on machines were not just refined, but other techniques were developed also. For example, statistical methods were used to reduce wastage. If a gear staff (axel) and a jewel bearing hole were designed to be a given size, then the parts that most closely met those design goals were used in the highest grade watches, while staffs that were too large would be matched to watch jewels with holes that were too large and together they could be used on lower grade watches.
Aaron Lufkin Dennison
Aaron Lufkin Dennison .-Early life:Aaron Dennison was born in Freeport, Maine, after which the family moved to Brunswick, Maine. He was the son of Andrew Dennison, a boot and shoemaker who was also a music teacher. As a child Aaron earned pocket money by carrying a builder’s hod, working as a...
became inspired by the manufacturing techniques of the United States Armory
Springfield Armory
The Springfield Armory, located in the City of Springfield, Massachusetts - from 1777 until its closing in 1968 - was the primary center for the manufacture of U.S. military firearms. After its controversial closing during the Vietnam War, the Springfield Armory was declared Western Massachusetts'...
at Springfield, Mass. The "armory practice" was mainly based on a strict system of organization, the extensive use of the machine shop and a control system based on gauges. Aaron Dennison proposed to produce watches via these techniques and, along with a few others, founded the Waltham Watch Company
Waltham Watch Company
The Waltham Watch Company, also known as the American Waltham Watch Co. and the American Watch Co., produced about 40 million high quality watches, clocks, speedometers, compasses, time fuses and other precision instruments between 1850 and 1957...
.
In the rest of the world manufacturing involved making certain parts under the roof of a factory
Factory
A factory or manufacturing plant is an industrial building where laborers manufacture goods or supervise machines processing one product into another. Most modern factories have large warehouses or warehouse-like facilities that contain heavy equipment used for assembly line production...
and obtaining other parts from piece work
Piece work
Piece work is any type of employment in which a worker is paid a fixed "piece rate" for each unit produced or action performed regardless of time...
ers who used their own cottages as workshops.
The American system of manufacturing
American system of manufacturing
The American system of manufacturing was a set of manufacturing methods that evolved in the 19th century. It involved semi-skilled labor using machine tools and jigs to make standardized, identical, interchangeable parts, manufactured to a tolerance, which could be assembled with a minimum of time...
by interchangeable parts
Interchangeable parts
Interchangeable parts are parts that are, for practical purposes, identical. They are made to specifications that ensure that they are so nearly identical that they will fit into any device of the same type. One such part can freely replace another, without any custom fitting...
meant the establishment of working facilities for the entire manufacture. It meant that everything was made on the premises, not according to the plans or ideas or methods of work of individual workmen, but under the direct supervision of a company's foreman, according to gauges the company furnished, under conditions of time, cleanliness and care which the company prescribed.
Waltham soon found that it was necessary to invent, develop and build its own production machinery, special gauges systems adjusted to the smallest watch parts dimensions, new alloys & materials.
The chronology of production lessons at the Waltham Watch Company
Waltham Watch Company
The Waltham Watch Company, also known as the American Waltham Watch Co. and the American Watch Co., produced about 40 million high quality watches, clocks, speedometers, compasses, time fuses and other precision instruments between 1850 and 1957...
can be divided into three phases:
- 1849-1857 learning and experimenting
- 1858-1870 refining and gauging
- 1871-1910 automating and factory organization
The manufacturing of watches differed from other products that had earlier used the armory practices in two significant ways.
First, the high price of watches allowed for a large investment in research and development. The vast majority of the price of a watch was due to labor rather than materials and any system that could significantly reduce labor costs could significantly increase profits. Even after 40 years of manufacturing improvements, in 1910, labor accounted for 80% of the cost of watches made by the Elgin National Watch Company.
Secondly, watches require very strict tolerances and very few manufacturing defects. Previous products made via armory practices, such as fire arms, sewing machines, etc. had tolerances 10 to 100 times as loose. A watch gear that is offset by a few thousands of an inch from where it should be will cause increased friction, losing critical power that needed to be sent to the balance wheel and greatly accelerating the wear of the watch. Previous watch manufacturing techniques required expert watchmakers to recognize slight variations in part sizes in order to place each gear in the correct location or to make other adjustments during the manufacturing of each watch.
The Waltham Model 1857, a watch of standard parts
In the year of 1857, The Waltham Model 1857, is a watchWatch
A watch is a small timepiece, typically worn either on the wrist or attached on a chain and carried in a pocket, with wristwatches being the most common type of watch used today. They evolved in the 17th century from spring powered clocks, which appeared in the 15th century. The first watches were...
made by the American Watch Companyin the City of Waltham, Massachusetts in the United States of America. Prior to 1857, pocket watch
Pocket watch
A pocket watch is a watch that is made to be carried in a pocket, as opposed to a wristwatch, which is strapped to the wrist. They were the most common type of watch from their development in the 16th century until wristwatches became popular after World War I during which a transitional design,...
es were not made of standard parts and there was a difficulty in repairing and making the watches on a cost effective basis. Most pocketwatches made in the world were in England or France, and this was also a test for early American manufacturing to take and produce items better than the countries in Europe, where at the time was in the middle of the industrial revolution. Most of the Model 57 pocket watches were in a coin silver
Silver
Silver is a metallic chemical element with the chemical symbol Ag and atomic number 47. A soft, white, lustrous transition metal, it has the highest electrical conductivity of any element and the highest thermal conductivity of any metal...
, a bit different than sterling silver, that coin silver is only 80 pure.
American system of watch manufacturing in wikipedia is a great side reference on the Waltham Model 57 Pocket Watch
Pocket watch
A pocket watch is a watch that is made to be carried in a pocket, as opposed to a wristwatch, which is strapped to the wrist. They were the most common type of watch from their development in the 16th century until wristwatches became popular after World War I during which a transitional design,...
*http://www.pricelessads.com/m57/seminar/seminar.pdf The internal mechanical movement was key wind, and to set the watch you used the same key. Some of the Model 57 Watches were fitted in Gold
Gold
Gold is a chemical element with the symbol Au and an atomic number of 79. Gold is a dense, soft, shiny, malleable and ductile metal. Pure gold has a bright yellow color and luster traditionally considered attractive, which it maintains without oxidizing in air or water. Chemically, gold is a...
watch cases, but the majority were silver.
In order to reach these strict tolerances, watch manufactures largely manufactured their own machine tools and machine parts. Elgin manufactured almost two drill bits for each watch they manufactured. The knowledge of how to manufacture machines that could manufacture watches spread from Waltham to Elgin to dozens of other American watch companies and manufactures of other products. Techniques such as jigs, stops and measuring devices on machines were not just refined, but other techniques were developed also. For example, statistical methods were used to reduce wastage. If a gear staff (axel) and a jewel bearing hole were designed to be a given size, then the parts that most closely met those design goals were used in the highest grade watches, while staffs that were too large would be matched to watch jewels with holes that were too large and together they could be used on lower grade watches.
See also
- E. Howard & Co.E. Howard & Co.thumb|Street clock by E. Howard & Co.The E. Howard & Co. clock and watch company was formed by Edward Howard and Charles Rice in 1858 after the demise of the Boston Watch Company...
- Waltham Watch CompanyWaltham Watch CompanyThe Waltham Watch Company, also known as the American Waltham Watch Co. and the American Watch Co., produced about 40 million high quality watches, clocks, speedometers, compasses, time fuses and other precision instruments between 1850 and 1957...
- Elgin Watch CompanyElgin Watch CompanyThe Elgin National Watch Company, most commonly known as just the Elgin Watch company was a major US watch company.-History:The Elgin National Watch Company, was founded in August 1864 as the National Watch Company. A number of former associates of the Waltham Watch Company and Chicago watchmaker J.C...
- Armory practice
External links
- Boston The Cradle of American Watchmaking
- The Boston Watch Co
- Origins of Waltham Model 57
- Time Museum Rockford, Illinois, U.S.A.
- Philadelphia Exhibition 1876 Report to the Federal High Council by Ed. Favre-Perret (1877)
- American and Swiss Watchmaking in 1876 by Jacques David
- The Watch Factories of America Past and Present by Henry G. Abbott (1888)
- Watchmaking and the American System of Manufacturing (2009)