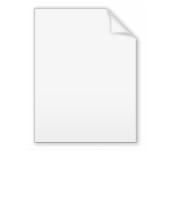
Piece work
Encyclopedia
Piece work is any type of employment
in which a worker is paid a fixed "piece rate" for each unit produced or action performed regardless of time. Piece work is a form of performance-related pay
.
In a manufacturing setting, the output of piece work can be measured by the number of physical items (pieces) produced, such as when a garment worker is paid per operational step completed, regardless of the time required. If quality is equal, piece rate rewards the more productive worker and offers less to those less productive. In this regard, it is a good example of free market
economics
. If everyone is paid the same regardless of output, some contend there is little motivation to produce at a high level beyond the natural work ethic
of that individual. An advantage for the company is that this method of payment helps to guarantee the costs per unit produced, which is useful for planning
and forecasting purposes.
In a service setting, the output of piece work can be measured by the number of operations completed, as when a telemarketer is paid by the number of calls made or completed, regardless of the outcome of the calls (pay for only certain positive outcomes is more likely to be called a sales commission or incentive pay). Crowdsourcing
systems such as Mechanical Turk
involve minute information-processing tasks (such as identifying photos or recognizing signatures) for which workers are compensated on a per-task basis.
As a term and as a common form of labor, 'piece work' had its origins in the guild
system of work during the Commercial Revolution
and before the Industrial Revolution
. Since the phrase 'piece work' first appears in writing around the year 1549, it is likely that at about this time, the master craftsmen
of the guild system began to assign their apprentices work on pieces which could be performed at home, rather than within the master's workshop. In the English system of manufacturing
, workers mass-produced parts from a fixed design as part of a division of labor, but did not have the advantage of machine tools or metalworking
jigs. Simply counting the number of pieces produced by a worker was likely easier than accounting for that worker's time, as would have been required for the computation of an hourly wage
.
Piece work took on new importance with the advent of machine tools, such as the machine lathe in 1751. Machine tools made possible by the American system of manufacturing
(attributed to Eli Whitney
) in 1799 in which workers could truly make just a single part—but make many copies of it—for later assembly by others. The reality of the earlier English System had been that handcrafted pieces rarely fit together on the first try, and a single artisan was ultimately required to rework all parts of a finished good. By the early 19th century, the accuracy of machine tools meant that piecework parts were produced fully ready for final assembly.
In the mid-19th century, the practice of distributing garment assembly among lower-skilled and lower-paid workers came to be known in Britain as the sweating system
and arose at about the same time that a practical (foot-powered) sewing machine
, was developed. Factories that collected sweating system workers at a single location, working at individual machines, and being paid piece rates became pejoratively known as sweatshop
s.
Today, piece work and sweatshops remain closely linked conceptually, even though each has continued to develop separately. Factories today may receive the label "sweatshop" more because they have the long hours and poor working conditions, even if they pay an hourly or daily wage
instead of a piece rate. Meanwhile, piece work in a service economy
, such as being a telemarketer paid per-call, may actually afford a work environment which compares favorably to other available work. Piece work was adopted in some English farming communities to dramatically improve living standards during the economic depression of the mid-1930s.
In response to the manifestation of piecework as a type of employment, employees began utilizing a method of resistance and subtle rebellion in which workers consciously and deliberately controlled the pace of their own individual work with the intention of doing the minimum amount of work with the least effort possible while still receiving compensation commonly referred to as pacing or soldiering. Pacing became a prominent mechanism of resistance in the American factory system by the 1830s, and because employers lowered piece rates dramatically within a relatively small period of time after the introduction of new techniques , the "worker quite naturally attempted to maintain the existing rate by deliberately restricting production. [...] [which] placed them in constant tension with their employers". By deliberately restricting their production, employees were attempting to retake control of their own circumstances. Specific examples of this include but are not limited to "taking unauthorized breaks to have a smoke, go to the john, share a cup of whiskey, or purchase cakes being hawked outside the mill gate [...], looking for missing tools, sharpening and repairing other tools, and reading newspapers while at work". As the captains of industry continued to increase the magnitude of their enterprises, they were the ones who "possessed the capital and felt that, by legal right, they should decide [how, when, and where the work should be executed]". It is pertinent to note that as a representation of labor values, it also represented the employees holistically rather than individually since many individuals collectively subtly rebelled in unison. As the quantity of employees utilizing this method of resistance grew, so did its effectiveness. The response of the managers came in the adoption of Scientific Management
which was presented by Frederick Taylor in 1911.
Employment
Employment is a contract between two parties, one being the employer and the other being the employee. An employee may be defined as:- Employee :...
in which a worker is paid a fixed "piece rate" for each unit produced or action performed regardless of time. Piece work is a form of performance-related pay
Performance-related pay
Performance-related pay is money paid to someone relating to how well one works. Car salesmen, production line workers, for example, may be paid in this way, or through commission....
.
In a manufacturing setting, the output of piece work can be measured by the number of physical items (pieces) produced, such as when a garment worker is paid per operational step completed, regardless of the time required. If quality is equal, piece rate rewards the more productive worker and offers less to those less productive. In this regard, it is a good example of free market
Free market
A free market is a competitive market where prices are determined by supply and demand. However, the term is also commonly used for markets in which economic intervention and regulation by the state is limited to tax collection, and enforcement of private ownership and contracts...
economics
Economics
Economics is the social science that analyzes the production, distribution, and consumption of goods and services. The term economics comes from the Ancient Greek from + , hence "rules of the house"...
. If everyone is paid the same regardless of output, some contend there is little motivation to produce at a high level beyond the natural work ethic
Work ethic
Work ethic is a set of values based on hard work and diligence. It is also a belief in the moral benefit of work and its ability to enhance character. An example would be the Protestant work ethic...
of that individual. An advantage for the company is that this method of payment helps to guarantee the costs per unit produced, which is useful for planning
Planning
Planning in organizations and public policy is both the organizational process of creating and maintaining a plan; and the psychological process of thinking about the activities required to create a desired goal on some scale. As such, it is a fundamental property of intelligent behavior...
and forecasting purposes.
In a service setting, the output of piece work can be measured by the number of operations completed, as when a telemarketer is paid by the number of calls made or completed, regardless of the outcome of the calls (pay for only certain positive outcomes is more likely to be called a sales commission or incentive pay). Crowdsourcing
Crowdsourcing
Crowdsourcing is the act of sourcing tasks traditionally performed by specific individuals to a group of people or community through an open call....
systems such as Mechanical Turk
Amazon Mechanical Turk
The Amazon Mechanical Turk is a crowdsourcing Internet marketplace that enables computer programmers to co-ordinate the use of human intelligence to perform tasks that computers are unable to do yet. It is one of the suites of Amazon Web Services...
involve minute information-processing tasks (such as identifying photos or recognizing signatures) for which workers are compensated on a per-task basis.
As a term and as a common form of labor, 'piece work' had its origins in the guild
Guild
A guild is an association of craftsmen in a particular trade. The earliest types of guild were formed as confraternities of workers. They were organized in a manner something between a trade union, a cartel, and a secret society...
system of work during the Commercial Revolution
Commercial Revolution
The Commercial Revolution was a period of European economic expansion, colonialism, and mercantilism which lasted from approximately the 16th century until the early 18th century. It was succeeded in the mid-18th century by the Industrial Revolution. Beginning with the Crusades, Europeans...
and before the Industrial Revolution
Industrial Revolution
The Industrial Revolution was a period from the 18th to the 19th century where major changes in agriculture, manufacturing, mining, transportation, and technology had a profound effect on the social, economic and cultural conditions of the times...
. Since the phrase 'piece work' first appears in writing around the year 1549, it is likely that at about this time, the master craftsmen
Master craftsman
A master craftsman or master tradesman was a member of a guild. In the European guild system, only masters were allowed to be members of the guild....
of the guild system began to assign their apprentices work on pieces which could be performed at home, rather than within the master's workshop. In the English system of manufacturing
English system of manufacturing
The English system of manufacturing was an early system of industrial production that required skilled machinists who were required to produce parts from a design or model. But however skilled the machinist, parts were never absolutely identical, and each part had to be manufactured separately to...
, workers mass-produced parts from a fixed design as part of a division of labor, but did not have the advantage of machine tools or metalworking
Metalworking
Metalworking is the process of working with metals to create individual parts, assemblies, or large scale structures. The term covers a wide range of work from large ships and bridges to precise engine parts and delicate jewelry. It therefore includes a correspondingly wide range of skills,...
jigs. Simply counting the number of pieces produced by a worker was likely easier than accounting for that worker's time, as would have been required for the computation of an hourly wage
Wage
A wage is a compensation, usually financial, received by workers in exchange for their labor.Compensation in terms of wages is given to workers and compensation in terms of salary is given to employees...
.
Piece work took on new importance with the advent of machine tools, such as the machine lathe in 1751. Machine tools made possible by the American system of manufacturing
American system of manufacturing
The American system of manufacturing was a set of manufacturing methods that evolved in the 19th century. It involved semi-skilled labor using machine tools and jigs to make standardized, identical, interchangeable parts, manufactured to a tolerance, which could be assembled with a minimum of time...
(attributed to Eli Whitney
Eli Whitney
Eli Whitney was an American inventor best known for inventing the cotton gin. This was one of the key inventions of the Industrial Revolution and shaped the economy of the Antebellum South...
) in 1799 in which workers could truly make just a single part—but make many copies of it—for later assembly by others. The reality of the earlier English System had been that handcrafted pieces rarely fit together on the first try, and a single artisan was ultimately required to rework all parts of a finished good. By the early 19th century, the accuracy of machine tools meant that piecework parts were produced fully ready for final assembly.
In the mid-19th century, the practice of distributing garment assembly among lower-skilled and lower-paid workers came to be known in Britain as the sweating system
Sweating system
Sweating system was a term used to describe an iniquitous system of subcontracting in the tailoring trade which came into prominence around 1848. In contemporary English the term sweatshop has a similar meaning...
and arose at about the same time that a practical (foot-powered) sewing machine
Sewing machine
A sewing machine is a textile machine used to stitch fabric, cards and other material together with thread. Sewing machines were invented during the first Industrial Revolution to decrease the amount of manual sewing work performed in clothing companies...
, was developed. Factories that collected sweating system workers at a single location, working at individual machines, and being paid piece rates became pejoratively known as sweatshop
Sweatshop
Sweatshop is a negatively connoted term for any working environment considered to be unacceptably difficult or dangerous. Sweatshop workers often work long hours for very low pay, regardless of laws mandating overtime pay or a minimum wage. Child labour laws may be violated. Sweatshops may have...
s.
Today, piece work and sweatshops remain closely linked conceptually, even though each has continued to develop separately. Factories today may receive the label "sweatshop" more because they have the long hours and poor working conditions, even if they pay an hourly or daily wage
Wage
A wage is a compensation, usually financial, received by workers in exchange for their labor.Compensation in terms of wages is given to workers and compensation in terms of salary is given to employees...
instead of a piece rate. Meanwhile, piece work in a service economy
Service economy
Service economy can refer to one or both of two recent economic developments. One is the increased importance of the service sector in industrialized economies. Services account for a higher percentage of US GDP than 20 years ago...
, such as being a telemarketer paid per-call, may actually afford a work environment which compares favorably to other available work. Piece work was adopted in some English farming communities to dramatically improve living standards during the economic depression of the mid-1930s.
In response to the manifestation of piecework as a type of employment, employees began utilizing a method of resistance and subtle rebellion in which workers consciously and deliberately controlled the pace of their own individual work with the intention of doing the minimum amount of work with the least effort possible while still receiving compensation commonly referred to as pacing or soldiering. Pacing became a prominent mechanism of resistance in the American factory system by the 1830s, and because employers lowered piece rates dramatically within a relatively small period of time after the introduction of new techniques , the "worker quite naturally attempted to maintain the existing rate by deliberately restricting production. [...] [which] placed them in constant tension with their employers". By deliberately restricting their production, employees were attempting to retake control of their own circumstances. Specific examples of this include but are not limited to "taking unauthorized breaks to have a smoke, go to the john, share a cup of whiskey, or purchase cakes being hawked outside the mill gate [...], looking for missing tools, sharpening and repairing other tools, and reading newspapers while at work". As the captains of industry continued to increase the magnitude of their enterprises, they were the ones who "possessed the capital and felt that, by legal right, they should decide [how, when, and where the work should be executed]". It is pertinent to note that as a representation of labor values, it also represented the employees holistically rather than individually since many individuals collectively subtly rebelled in unison. As the quantity of employees utilizing this method of resistance grew, so did its effectiveness. The response of the managers came in the adoption of Scientific Management
Scientific management
Scientific management, also called Taylorism, was a theory of management that analyzed and synthesized workflows. Its main objective was improving economic efficiency, especially labor productivity. It was one of the earliest attempts to apply science to the engineering of processes and to management...
which was presented by Frederick Taylor in 1911.
External links
- Piece rate pay design - University of California