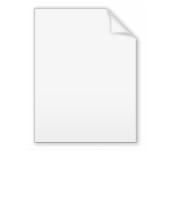
UV Coating
Encyclopedia
"UV coating" refers to surface treatments which are either cured
by ultraviolet
radiation, or protect the underlying material from its harmful effects.
can be applied over ink printed on paper and dried by exposure to UV radiation. UV coatings can be formulated up to 100% solids so that they have no volatile component that contributes to pollution. This high solids level also allows for the coating to be applied in very thin films. UV coatings can be formulated to a wide variety of gloss ranges. UV coating can be applied via most conventional industrial coating applications as well as by silkscreen.
Due to the normally high solids content of UV coating/varnish the surface of the cured film can be extremely reflective and glossy. 80 lb text and heavier weights of paper can be UV coated, however, cover weights are preferred.
UV can be applied on spot locations of the paper or by flooding the page. This coating application can deepen the color of the printed area. Drying is virtually instantaneous when exposed to the correct level of UV light so projects can move quickly into the bindery
. Like the other coatings, consult the bindery for projects requiring gluing. Using a strippable coating blanket can eliminate glue issues. New, innovative coating blanket solutions have been developed recently that allow for this to be done.
A printed page with UV coating applied can be very shiny or flattened to a matte finish. A good example of UV coated paper is photo paper sold for home printing projects. UV coatings that are not fully cured can have a slightly sticky feeling.
by invisible light. UV curable coatings can be used to impart a variety of properties to polymeric surfaces, including glare reduction, wear or scratch resistance, anti-fogging, microbial resistance, chemical resistance. Computer screens, keyboards, cel phone surfaces, and most other personal electronic devices are treated with some type of UV-curable coating. Coatings are usually applied to plastic substrates via spray, dip, roll, flow and other processes. UV-curable coatings are often specified for plastic parts because the process does not require heat, which can distort the plastic shape. http://www.pcoatingsintl.com/article/2007/0503/article_205.html
The selection of the UV-curable coating type applied by any method is really a matter of finish build or thickness, the ease to achieve certain finish subtleties (gloss, leveling, etc.), and the ease of use of the coating system. In general, if 100% UV-curable coatings can be used to produce the desired finish quality, it is best to set a course of action to use them.
Costs, operation expenses and reporting requirements will be most advantageous with 100% UV-curable coatings. If very thin film builds are desired, less than 100% actives may be necessary and the use of water-reduced UV-curable coatings is most preferential
Curing (chemistry)
Curing is a term in polymer chemistry and process engineering that refers to the toughening or hardening of a polymer material by cross-linking of polymer chains, brought about by chemical additives, ultraviolet radiation, electron beam or heat...
by ultraviolet
Ultraviolet
Ultraviolet light is electromagnetic radiation with a wavelength shorter than that of visible light, but longer than X-rays, in the range 10 nm to 400 nm, and energies from 3 eV to 124 eV...
radiation, or protect the underlying material from its harmful effects.
Ultra-violet coating of paper
Ultra-violet cured coatingsCoated paper
Coated paper is paper which has been coated by a compound to impart certain qualities to the paper, including weight, surface gloss, smoothness or reduced ink absorbency. Kaolinite or calcium carbonate are used to coat paper for high quality printing used in packaging industry and in magazines...
can be applied over ink printed on paper and dried by exposure to UV radiation. UV coatings can be formulated up to 100% solids so that they have no volatile component that contributes to pollution. This high solids level also allows for the coating to be applied in very thin films. UV coatings can be formulated to a wide variety of gloss ranges. UV coating can be applied via most conventional industrial coating applications as well as by silkscreen.
Due to the normally high solids content of UV coating/varnish the surface of the cured film can be extremely reflective and glossy. 80 lb text and heavier weights of paper can be UV coated, however, cover weights are preferred.
UV can be applied on spot locations of the paper or by flooding the page. This coating application can deepen the color of the printed area. Drying is virtually instantaneous when exposed to the correct level of UV light so projects can move quickly into the bindery
Bindery
Bindery refers to a studio, workshop or factory where sheets of paper are fastened together to make books, but also where gold and other decorative elements are added to the exterior of books, where boxes or slipcases for books are made and where the restoration of books is carried out.-Overview:A...
. Like the other coatings, consult the bindery for projects requiring gluing. Using a strippable coating blanket can eliminate glue issues. New, innovative coating blanket solutions have been developed recently that allow for this to be done.
A printed page with UV coating applied can be very shiny or flattened to a matte finish. A good example of UV coated paper is photo paper sold for home printing projects. UV coatings that are not fully cured can have a slightly sticky feeling.
Ultra-violet coating of glass and plastic
Glass and plastic can be coated to diminish the amount of ultraviolet radiation that passes through. Common uses of such coating include eyeglasses and automotive windows. Photographic filters remove ultraviolet to prevent exposure of the film or sensorSensor
A sensor is a device that measures a physical quantity and converts it into a signal which can be read by an observer or by an instrument. For example, a mercury-in-glass thermometer converts the measured temperature into expansion and contraction of a liquid which can be read on a calibrated...
by invisible light. UV curable coatings can be used to impart a variety of properties to polymeric surfaces, including glare reduction, wear or scratch resistance, anti-fogging, microbial resistance, chemical resistance. Computer screens, keyboards, cel phone surfaces, and most other personal electronic devices are treated with some type of UV-curable coating. Coatings are usually applied to plastic substrates via spray, dip, roll, flow and other processes. UV-curable coatings are often specified for plastic parts because the process does not require heat, which can distort the plastic shape. http://www.pcoatingsintl.com/article/2007/0503/article_205.html
Ultra-violet coating of Wood
The industrial wood finisher has essentially three options in types of UV-curable coatings to use—100% UV, water-reduced UV and solvent reduced UV. Each type of UV-curable coating can be applied by virtually any method of application. The selected method of application is dependent on the surface structure/property to be finished, the finish quality desired on that surface, and the production rate that finishing must achieve. Another consideration is recovery, typically UV-curable coatings are more expensive than conventional cure coatings and as such any material that does not get applied to the part would need to be recovered as efficiently as possible.The selection of the UV-curable coating type applied by any method is really a matter of finish build or thickness, the ease to achieve certain finish subtleties (gloss, leveling, etc.), and the ease of use of the coating system. In general, if 100% UV-curable coatings can be used to produce the desired finish quality, it is best to set a course of action to use them.
Costs, operation expenses and reporting requirements will be most advantageous with 100% UV-curable coatings. If very thin film builds are desired, less than 100% actives may be necessary and the use of water-reduced UV-curable coatings is most preferential