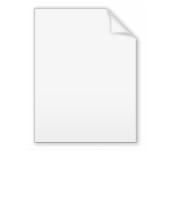
Thick film technology
Encyclopedia
Thick film technology is used to produce electronic devices such as surface mount devices, hybrid integrated circuits and sensor
s.
Thick film circuits are widely used, in automotive industry, both in sensors ex. mixture of fuel/air, pressure sensors, engine and gearbox controls, sensor for releasing airbags, ignitors to airbags, common is that high reliability is reguired, often extende temperature range also along massive thermocycling of circuits without failure.
The manufacture of such devices are an additive process where deposition of several successive layers of conductor, resistors and dieletrica layers onto an electrically insulating substrate using a screen-printing
process. A typical thick film process would consist of the following stages:
Profiling are for example used lot in the sensor, where a circuit need to fit round tubes or other different complex shapes.
Drilling of holes, provide via between the two sides of the substrate, normally hole sizes are in the range 0.15-0.2 mm.
Lasering before processing the substrates has a cost advantage to lasering or dicing using diamond saw after processing.
vehicle to produce a paste for screen-printing. To achieve a homogeneous ink the mixed components of the ink may be passed through a three roll mill
. Alternatively, ready made inks may be obtained from one of the many companies offering products for the thick film technologist.
by exposure to UV
light.
. Many chip resistors are made using thick film technology. Large substrates are printed with resistors fired, divided into small chips and these are then terminated, so they can be soldered on the PCB board. With laser trimming two modes are used; either passive trimming, where each resistor is trimmed to a specific value and tolerance, or active trimming, where the feedback is used to adjust to a specific voltage, frequency or response by laser trimming the resistors on the circuit while powered up.
.
or soldering
.
Sensor
A sensor is a device that measures a physical quantity and converts it into a signal which can be read by an observer or by an instrument. For example, a mercury-in-glass thermometer converts the measured temperature into expansion and contraction of a liquid which can be read on a calibrated...
s.
Thick film circuits are widely used, in automotive industry, both in sensors ex. mixture of fuel/air, pressure sensors, engine and gearbox controls, sensor for releasing airbags, ignitors to airbags, common is that high reliability is reguired, often extende temperature range also along massive thermocycling of circuits without failure.
The manufacture of such devices are an additive process where deposition of several successive layers of conductor, resistors and dieletrica layers onto an electrically insulating substrate using a screen-printing
Screen-printing
Screen printing is a printing technique that uses a woven mesh to support an ink-blocking stencil. The attached stencil forms open areas of mesh that transfer ink or other printable materials which can be pressed through the mesh as a sharp-edged image onto a substrate...
process. A typical thick film process would consist of the following stages:
Lasering of substrates
Most used substrates are made of 96% Alumina Al2O2. Alumina is very hard and not very machinable, therefore lasering of the material is the most efficient way to machine it. The thick film process is also a process of minuazation where one substrates normally contain many units (final circuits), with the lasering it is possible to scribe, profile and drill holes. Scribing is a lasering process where a line of laser pulses are fire into the material and 30-50% of the material is removed, this weakens the substrate, after all other process are done to build the thick film circuit the substrates can easily be divided into single units.Profiling are for example used lot in the sensor, where a circuit need to fit round tubes or other different complex shapes.
Drilling of holes, provide via between the two sides of the substrate, normally hole sizes are in the range 0.15-0.2 mm.
Lasering before processing the substrates has a cost advantage to lasering or dicing using diamond saw after processing.
Ink preparation
Inks for electrodes, terminals, resistors, dielectric layers etc. are commonly prepared by mixing the metal or ceramic powders required with an organicOrganic compound
An organic compound is any member of a large class of gaseous, liquid, or solid chemical compounds whose molecules contain carbon. For historical reasons discussed below, a few types of carbon-containing compounds such as carbides, carbonates, simple oxides of carbon, and cyanides, as well as the...
vehicle to produce a paste for screen-printing. To achieve a homogeneous ink the mixed components of the ink may be passed through a three roll mill
Three roll mill
A three roll mill is a machine that uses shear force created by three horizontally positioned rolls rotating in opposite directions and different speeds relative to each other, in order to mix, refine, disperse, or homogenize viscous materials fed into it....
. Alternatively, ready made inks may be obtained from one of the many companies offering products for the thick film technologist.
Screen-printing
Screen-printing is the process of pushing an ink through a patterned woven mesh screen or stencil using a squeegee.Drying/Curing
After allowing a period of time after printing for settling of the ink to occur, each layer of ink that is deposited is usually dried at a moderately high temperature (50 to 200°C) to evaporate the liquid component of the ink and fix the layer temporarily in position on the substrate so that it can be handled or stored before final processesing. For inks based on polymers and some solder pastes that cure at these temperatures this may be the final step that is required. Some inks also require curingCuring (chemistry)
Curing is a term in polymer chemistry and process engineering that refers to the toughening or hardening of a polymer material by cross-linking of polymer chains, brought about by chemical additives, ultraviolet radiation, electron beam or heat...
by exposure to UV
Ultraviolet
Ultraviolet light is electromagnetic radiation with a wavelength shorter than that of visible light, but longer than X-rays, in the range 10 nm to 400 nm, and energies from 3 eV to 124 eV...
light.
Firing
For many of the metal, ceramic and glass inks used in thick film processes a high temperature (usually greater than 300°C) firing is required to fix the layers in position permanently on the substrate.Laser Trimming of resistors
After firing, the substrate resistors are trimmed to the correct value. This process is named Laser trimmingLaser trimming
Laser trimming is the manufacturing process of using a laser to adjust the operating parameters of an electronic circuit.One of the most common applications uses a laser to burn away small portions of resistors, raising their resistance value...
. Many chip resistors are made using thick film technology. Large substrates are printed with resistors fired, divided into small chips and these are then terminated, so they can be soldered on the PCB board. With laser trimming two modes are used; either passive trimming, where each resistor is trimmed to a specific value and tolerance, or active trimming, where the feedback is used to adjust to a specific voltage, frequency or response by laser trimming the resistors on the circuit while powered up.
Mounting of capacitors semiconducters
The development of the SMD process actually evolves from the thick film process. Also moutning of naked dies (the actual silicon chip with out encapsulation) and wire bonding is a standard process, this provides the basis for minituarization of the circuits as all the extra encapsulation is not necessary.Separation of elements
This step is often necessary because many components are produced on one substrate at the same time. Thus, some means of separating the components from each other is required. This step may be achieved by wafer dicingWafer dicing
Wafer dicing is the process by which die are separated from a wafer of semiconductor following the processing of the wafer. The dicing process can be accomplished by scribing and breaking, by mechanical sawing or by laser cutting...
.
Integration of devices
At this stage the devices may require integrating with other electronic components, usually in the form of a printed circuit board. This may be achieved by wire bondingWire bonding
Wire bonding is the primary method of making interconnections between an integrated circuit and a printed circuit board during semiconductor device fabrication. Although less common, wire bonding can be used to connect an IC to other electronics or to connect from one PCB to another...
or soldering
Soldering
Soldering is a process in which two or more metal items are joined together by melting and flowing a filler metal into the joint, the filler metal having a lower melting point than the workpiece...
.