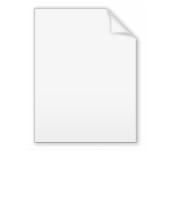
Thermal oxidizer
Encyclopedia
A thermal oxidizer is a process unit for air pollution
control in many chemical plants that decomposes hazardous gases at a high temperature and releases them into the atmosphere.
The VOC's are oxidised at high temperatures typically 800-850 degC for a period of 1-2 seconds where carbon molecules (VOC's) are bonded together with oxygen molecules prior to discharge to atmosphere. The energy efficiency is achieved storing heat ceramic media as the process air enters and exits the combustion chamber. The direction of airflow reverses every 1-3 minutes by a series of valves to alternately store and regenerate the heat - the inlet air gets pre-heated and the outlet air gives up the heat. The result is a very efficient operation. Solvent concentrations of 2-3 g/m3 and above allow the RTO to operate without support fuel using the energy within the solvent, ie auto-thermal or self-sustaining. At higher solvent concentrations of say 6-10g/m3, a high temperature bypass is necessary due to the excessive heat generated. Early RTO's had 2 towers or cannisters which regularly satisfied the emission limits at the time of 150 mgVOC/m3 (average). However, there is a spike of VOC emitted as the valves change direction - the high VOC suddenly becomes the outlet for a few seconds. As emission limits have reduced to 50 mg/m3 and even 20 mg/m3, a third tower or an entrapment chamber is necessary to treat the spikes as well.
Variations in process airflow is usually controlled by the main fan being speed controlled to maintain a constant suction pressure. During times of no process airflow, the RTO would go into standby or idle mode to minimise energy consumption.
As an example, the thermal ignition temperature of carbon monoxide is at 609°C Carbon monoxide
. However, by utilizing a suitable oxidation catalyst, the ignition temperature can be reduced to around 200°C.
This can result in even lower operating costs compared to a Regenerative Thermal Oxidizer. Most systems operate within the 500F (260°C) to 1000F (540°C) degree range. Some systems are designed to operate both as Regenerative Catalytic Systems and Regenerative Thermal Oxdizers. When these systems are used special design considerations are utilized to reduce the probability of overheating (dilution of inlet gas or recycling), these high temperatures would deactivate the catalyst, e.g. by sintering of the active material Sintering
.
.
Air pollution
Air pollution is the introduction of chemicals, particulate matter, or biological materials that cause harm or discomfort to humans or other living organisms, or cause damage to the natural environment or built environment, into the atmosphere....
control in many chemical plants that decomposes hazardous gases at a high temperature and releases them into the atmosphere.
Principle
Thermal Oxidizers are typically used to destroy Hazardous Air Pollutants (HAPs) and Volatile Organic Compounds (VOCs) from industrial air streams. These pollutants are generally hydrocarbon based and when destroyed via thermal combustion they are chemically changed to form CO2 and H2O.Regenerative thermal oxidizer (RTO)
One of today’s most widely accepted air pollution control technologies across industry is a Regenerative Thermal Oxidizer, commonly referred to as a RTO. They are very versatile and extremely efficient – thermal efficiency can reach 95%. They are regularly used for abating solvent fumes, odours, etc. from a wide range of industries. Regenerative Thermal Oxidizers are ideal in a range of low to high VOC concentrations up to 10 g/m3 solvent. There are currently many types Regenerative Thermal Oxidizer on the market with the capabitlity of 99.5+% Volatile Organic Compound (VOC) oxidisation or destruction efficiency. The ceramic heat exchanger(s) in the towers can be designed for thermal efficiencies as high as 97+%.The VOC's are oxidised at high temperatures typically 800-850 degC for a period of 1-2 seconds where carbon molecules (VOC's) are bonded together with oxygen molecules prior to discharge to atmosphere. The energy efficiency is achieved storing heat ceramic media as the process air enters and exits the combustion chamber. The direction of airflow reverses every 1-3 minutes by a series of valves to alternately store and regenerate the heat - the inlet air gets pre-heated and the outlet air gives up the heat. The result is a very efficient operation. Solvent concentrations of 2-3 g/m3 and above allow the RTO to operate without support fuel using the energy within the solvent, ie auto-thermal or self-sustaining. At higher solvent concentrations of say 6-10g/m3, a high temperature bypass is necessary due to the excessive heat generated. Early RTO's had 2 towers or cannisters which regularly satisfied the emission limits at the time of 150 mgVOC/m3 (average). However, there is a spike of VOC emitted as the valves change direction - the high VOC suddenly becomes the outlet for a few seconds. As emission limits have reduced to 50 mg/m3 and even 20 mg/m3, a third tower or an entrapment chamber is necessary to treat the spikes as well.
Variations in process airflow is usually controlled by the main fan being speed controlled to maintain a constant suction pressure. During times of no process airflow, the RTO would go into standby or idle mode to minimise energy consumption.
Regenerative catalytic oxidizer (RCO)
In some applications, the use of a catalyst helps allow oxidation at somewhat reduced temperatures.As an example, the thermal ignition temperature of carbon monoxide is at 609°C Carbon monoxide
Carbon monoxide
Carbon monoxide , also called carbonous oxide, is a colorless, odorless, and tasteless gas that is slightly lighter than air. It is highly toxic to humans and animals in higher quantities, although it is also produced in normal animal metabolism in low quantities, and is thought to have some normal...
. However, by utilizing a suitable oxidation catalyst, the ignition temperature can be reduced to around 200°C.
This can result in even lower operating costs compared to a Regenerative Thermal Oxidizer. Most systems operate within the 500F (260°C) to 1000F (540°C) degree range. Some systems are designed to operate both as Regenerative Catalytic Systems and Regenerative Thermal Oxdizers. When these systems are used special design considerations are utilized to reduce the probability of overheating (dilution of inlet gas or recycling), these high temperatures would deactivate the catalyst, e.g. by sintering of the active material Sintering
Sintering
Sintering is a method used to create objects from powders. It is based on atomic diffusion. Diffusion occurs in any material above absolute zero, but it occurs much faster at higher temperatures. In most sintering processes, the powdered material is held in a mold and then heated to a temperature...
.
Ventilation air methane thermal oxidizer (VAMTOX)
Ventilation Air Methane Thermal Oxidizers are used to destroy methane in the exhaust air of underground coal mine shafts. Methane is a greenhouse gas and, when destroyed via thermal combustion, is chemically altered to form CO2 and H2O. CO2 is 25 times less potent than methane when emitted into the atmosphere with regards to global warming. Concentrations of methane in mine ventilation exhaust air of coal and trona mines are very dilute; typically below 1% and often below 0.5%. VAMTOX units have a system of valves and dampers that direct the air flow across one or more ceramic filled bed(s). On start-up, the system preheats by raising the temperature of the heat exchanging ceramic material in the bed(s) at or above the auto-oxidation temperature of methane (1,000°C or 1,832°F), at which time the preheating system is turned off and mine exhaust air is introduced. Then the methane-filled air reaches the preheated bed(s), releasing the heat from combustion. This heat is then transferred back to the bed(s), thereby maintaining the temperature at or above what is necessary to support auto-thermal operation.Thermal recuperative oxidizer
A less commonly used thermal oxidizer technology is a thermal recuperative oxidizer. Thermal recuperative oxidizers have a primary and/or secondary heat exchanger within the system. A primary heat exchanger preheats the incoming dirty air by recuperating heat from the exiting clean air. This is done by a shell and tube heat exchanger or a plate-type exchanger. As the incoming air passes on one side of the metal tube or plate, hot clean air from the combustion chamber passes on the other side of the tube or plate and heat is transferred to the incoming air through the process of conduction using the metal as the medium of heat transfer. In a secondary heat exchanger the same concept applies for heat transfer, but the air being heated by the outgoing clean process stream is being returned to another part of the plant – perhaps back to the process.Catalytic oxidizer
Catalytic oxidation occurs through a chemical reaction between the VOC hydrocarbon molecules and a precious-metal catalyst bed that is internal to the oxidizer system. A catalyst is a substance that is used to accelerate the rate of a chemical reaction, allowing the reaction to occur in a normal temperature range of 550°F - 650°F (275°C to 350°C).Direct fired thermal oxidizer - afterburner
A direct-fired oxidizer is the simplest technology of thermal oxidation. A process stream is introduced into a firing box through or near the burner and enough residence time is provided to get the desired destruction removal efficiency (DRE) of the VOCs. Also called afterburners, these systems are the least capital intensive, but when applied incorrectly, the operating costs can be devastating because there is no form of heat recovery. These are best applied where there is a very high concentration of VOCs to act as the fuel source (instead of natural gas or oil) for complete combustion at the targeted operating temperatureOperating temperature
An operating temperature is the temperature at which an electrical or mechanical device operates. The device will operate effectively within a specified temperature range which varies based on the device function and application context, and ranges from the minimum operating temperature to the...
.
External links
- "RTO Innovation," Pollution Engineering magazine, Feature Article, Oct. 2007
- "Thermal Oxidisers Applications in the UK" Process Combustion Ltd., April 2010
- "Different Types of Thermal Oxidizers" Gulf Coast Environmental Systems, Sep. 2009
- "O2 Monitoring & Combustion Air System" American Environmental Fabrication & Supply, July. 2010
- "ReVAM" Series Of Thermal Oxidizers - American Environmental Fabrication & Supply, Sept. 2010