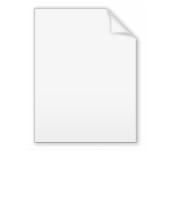
The Vanguard Method
Encyclopedia
The Vanguard Method is a method used by service organisations to change from a command and control to a systems approach to the design and management of work. The method was invented by the occupational psychologist Professor John Seddon
who began his career researching the reasons for failures of major change programmes. Based on what he learned he developed this method for change, which he describes as "a combination of systems thinking
- how the work works - and intervention theory
- how to change it".
The method represents a translation of Taiichi Ohno
's ideas behind the Toyota Production System
for service organisations. The method makes the assumption that service is different to manufacturing. According to the Vanguard Method, there is inherently greater variety in customer demand, hence the need to design to absorb that variety. Proponents of the Vanguard method recommend that service organisations avoid the ' lean tools' developed for 'lean manufacturing
' as they don't apply well in service organisations.
The Vanguard Method enables managers to study their organisation as a system and on the basis of the knowledge gained, re-design their services to improve performance and drive out costs. 'Failure demand
' is a type of waste often discovered during the 'Check' phase of the Vanguard Method. John Seddon invented the concept of failure demand when he discovered that the movement of ‘telephone work’ to call centres from local bank branches in the 1980s caused an explosion in the volumes of demand – the number of phone calls soared. He found that the rise in call volumes was attributable to the creation of ‘failure demand’, i.e people ringing back because they didn't get their problem solved the first time. The same phenomenon also occurred in the public sector as local authorities and housing associations moved telephone work into call centres. Demand was much greater than expected or planned for. Seddon argues that increasing demand was not the result of success but of failure. Seddon's work in local government shows that failure demand in such call centres can run as high as 80% of total demand.
John Seddon
John Seddon is a British occupational psychologist, author and "management guru", specialising in the service industry. He is lead consultant of Vanguard, a consultancy company he formed in 1985 and the inventor of 'The Vanguard Method'....
who began his career researching the reasons for failures of major change programmes. Based on what he learned he developed this method for change, which he describes as "a combination of systems thinking
Systems thinking
Systems thinking is the process of understanding how things influence one another within a whole. In nature, systems thinking examples include ecosystems in which various elements such as air, water, movement, plants, and animals work together to survive or perish...
- how the work works - and intervention theory
Intervention theory
Intervention theory is a term used in social studies and social policy to refer to the decision making problems of intervening effectively in a situation in order to secure desired outcomes. Intervention theory addresses the question of when it is desirable not to intervene and when it is...
- how to change it".
The method represents a translation of Taiichi Ohno
Taiichi Ohno
was a prominent Japanese businessman. He is considered to be the father of the Toyota Production System, which became Lean Manufacturing in the U.S. He devised the seven wastes as part of this system. He wrote several books about the system, including Toyota Production System: Beyond Large-Scale...
's ideas behind the Toyota Production System
Toyota Production System
The Toyota Production System is an integrated socio-technical system, developed by Toyota, that comprises its management philosophy and practices. The TPS organizes manufacturing and logistics for the automobile manufacturer, including interaction with suppliers and customers...
for service organisations. The method makes the assumption that service is different to manufacturing. According to the Vanguard Method, there is inherently greater variety in customer demand, hence the need to design to absorb that variety. Proponents of the Vanguard method recommend that service organisations avoid the ' lean tools' developed for 'lean manufacturing
Lean manufacturing
Lean manufacturing, lean enterprise, or lean production, often simply, "Lean," is a production practice that considers the expenditure of resources for any goal other than the creation of value for the end customer to be wasteful, and thus a target for elimination...
' as they don't apply well in service organisations.
The Vanguard Method enables managers to study their organisation as a system and on the basis of the knowledge gained, re-design their services to improve performance and drive out costs. 'Failure demand
Failure demand
Failure demand is a systems concept used in service organisations first discovered and articulated by Professor John Seddon as 'demand caused by a failure to do something or do something right for the customer'...
' is a type of waste often discovered during the 'Check' phase of the Vanguard Method. John Seddon invented the concept of failure demand when he discovered that the movement of ‘telephone work’ to call centres from local bank branches in the 1980s caused an explosion in the volumes of demand – the number of phone calls soared. He found that the rise in call volumes was attributable to the creation of ‘failure demand’, i.e people ringing back because they didn't get their problem solved the first time. The same phenomenon also occurred in the public sector as local authorities and housing associations moved telephone work into call centres. Demand was much greater than expected or planned for. Seddon argues that increasing demand was not the result of success but of failure. Seddon's work in local government shows that failure demand in such call centres can run as high as 80% of total demand.