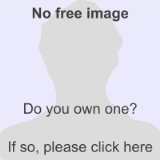
Percy Gilchrist
Encyclopedia
Percy Carlyle Gilchrist FRS (December 27, 1851 - December 16, 1935) was a British chemist and metallurgist born in Lyme Regis, Dorset, and who studied at Felsted
and the Royal School of Mines. The son of Alexander
and Anne Gilchrist, he is best known for his collaboration with his cousin, Sidney Gilchrist Thomas
on what became the standard basic process of making steel
.
The entailed producing low-phosphorus steel from local high-phosphorus ores,by changing the acidic process to a basic process and this meant that steel became cheaply available to British industry- low phosphorus ores being available by importation only.
He developed the process in 1875-77, together with his cousin and it involved melting pig iron in a converter similar to that used in the Bessemer process
and subjected to prolonged blowing. The oxygen in the blast of air oxidized carbon and other impurities, and the addition of lime at this stage caused the oxides to separate out as a slag on the surface of the molten metal. Continued blowing then brought about oxidation of the phosphorus.
Felsted School
Felsted School, an English co-educational day and boarding independent school, situated in Felsted, Essex. It is in the British Public School tradition, and was founded in 1564 by Richard Rich, 1st Baron Rich who, as Lord Chancellor and Chancellor of the Court of Augmentations, acquired...
and the Royal School of Mines. The son of Alexander
Alexander Gilchrist
Alexander Gilchrist was the biographer of William Blake. Gilchrist's biography is still a standard reference work on the poet....
and Anne Gilchrist, he is best known for his collaboration with his cousin, Sidney Gilchrist Thomas
Sidney Gilchrist Thomas
Sidney Gilchrist Thomas was an English inventor.-Life:Thomas was born at Canonbury, London and was educated at Dulwich College....
on what became the standard basic process of making steel
Steel
Steel is an alloy that consists mostly of iron and has a carbon content between 0.2% and 2.1% by weight, depending on the grade. Carbon is the most common alloying material for iron, but various other alloying elements are used, such as manganese, chromium, vanadium, and tungsten...
.
The entailed producing low-phosphorus steel from local high-phosphorus ores,by changing the acidic process to a basic process and this meant that steel became cheaply available to British industry- low phosphorus ores being available by importation only.
He developed the process in 1875-77, together with his cousin and it involved melting pig iron in a converter similar to that used in the Bessemer process
Bessemer process
The Bessemer process was the first inexpensive industrial process for the mass-production of steel from molten pig iron. The process is named after its inventor, Henry Bessemer, who took out a patent on the process in 1855. The process was independently discovered in 1851 by William Kelly...
and subjected to prolonged blowing. The oxygen in the blast of air oxidized carbon and other impurities, and the addition of lime at this stage caused the oxides to separate out as a slag on the surface of the molten metal. Continued blowing then brought about oxidation of the phosphorus.