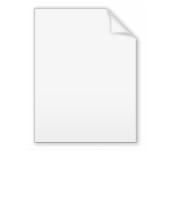
Morris Engines
Encyclopedia
Morris Engines, the factory of Morris Motors Ltd.
, Engines Branch was located in Coventry, England
. The company specialised in the mass production of engines and gearboxes, for fitment into vehicles made by the Nuffield Organisation
. Morris Motors Ltd., Engines Branch was, therefore, partly responsible for the Nuffield Organization becoming Britain's leading motor manufacturer in the 1930s.
of France, who were makers of the famous machine gun, hurriedly transferred production to England during World War I when it looked as if their St. Denis
factory near Paris was going to be overrun by the Germans. Consequently, a factory was erected at Gosford Street, Coventry, and both machines and key staff were brought over to England so that production could start as soon as possible.
At the end of the War in 1918, the factory suddenly became short of work so Hotchkiss agreed to manufacture engines and gearboxes, copied from American designs, for Morris Motors Ltd. Delivery of these power units started mid 1919 and they were fitted into “Bullnose” Morris Cowley
s and Morris Oxford
s. By 1922, the supply of power units was just sufficient to meet the level of production of Morris cars, so W.R. Morris
(later Lord Nuffield), the founder and owner of Morris Motors Ltd., asked Hotchkiss to raise production. However, Hotchkiss refused saying that they were unwilling to make more than 300 power units per week, because an expansion in England would have needed capital that they preferred to use in France.
After some negotiations, Morris bought the Hotchkiss plant and premises for £349,423 (about £15 million at 2009 values) in January 1923 and the business was renamed Morris Engines Ltd. Morris immediately set about a reorganisation and to carry out this task, he appointed F.G. Woollard
, who had been known to Morris since 1910, as General Manager. Woollard was a pioneer in the techniques of mass
and flow production and the results he achieved at the Gosford Street factory were largely due to his expertise in managing men and machines.
to flow, Woollard introduced a 24 hour working day, by introducing a 3 shift system of 8 hours each, for a 5 day week. Production increased from less than 300 power units per week in January 1923, to 600 units per week in December of that year and to a remarkable 1200 units per week in December 1924.
The engine manufacturing process started when cylinder blocks arrived form one of the supplying foundries, one of which was Morris's own. After being inspected, pickled, washed and dried, the blocks were placed on a hand-transfer machining line that carried out 53 operations in turn. The process took 223 minutes and a completed block was being produced every 4 minutes.
The idea of the first hand-transfer machining line, which was operated by 21 men, evolved in 1923. Then, in 1924, the first automated transfer machine was introduced for the production of gearbox cases, which were moved from station to station by compressed air. A second automated transfer machine, for the production of flywheels, was set up in 1924. These machines were something Morris Engines Ltd. were justifiably proud of and they encouraged the public to see the process. American engineers judged the production systems to be 20 years ahead of their time.
Although the hand-transfer machining line remained in use for many years, the automated transfer machines were subsequently divided into individual machine units, as the automatic systems proved to be over complicated for technology of the time. However, Woollard had pioneered a process which is now commonplace.
In June 1926, Morris Motors Ltd became a public company. The new company, Morris Motors (1926) Ltd., then acquired some of W.R. Morris's personally owned companies which were changed into its branches. Consequently, Morris Engines Ltd. became Morris Motors Ltd., Engines Branch.
Situated as it was in a congested area of Coventry, the Gosford Street factory site had little space for expansion on horizontal lines, so a six-storey extension had been constructed. As further expansion, to meet the rising demand for power units, was foreseen, Morris purchased a 45 acres (182,108.7 m²) site north of Coventry at Courthouse Green
in 1927 and a mechanised foundry, together with the machining of cylinder blocks, was set up there.
.
During the late 1930s, the Courthouse Green factory was turning out over 3,000 power units per week and throughout the World War II, it was working flat-out making engines for fire pumps, ambulances, military vehicles, lifeboats and tanks, as well as making component parts for aero engines and for Rotol
variable pitch air screws. The factory suffered extensive damage during a heavy bombing raid on Coventry in 1940, but production restarted within six weeks of the raid, even though some of its workforce were having to work in the open air as much of the factory's roof had been blown off and had still not been replaced.
After the War, Morris Motors Ltd., Engines Branch reverted to making power units for fitment into vehicles made by the Nuffield Organization and its factory became part of the British Motor Corporation
when Morris Motors Ltd. merged with the Austin Motor Company
Ltd. in 1952.
Morris Motor Company
The Morris Motor Company was a British car manufacturing company. After the incorporation of the company into larger corporations, the Morris name remained in use as a marque until 1984 when British Leyland's Austin Rover Group decided to concentrate on the more popular Austin marque...
, Engines Branch was located in Coventry, England
Coventry
Coventry is a city and metropolitan borough in the county of West Midlands in England. Coventry is the 9th largest city in England and the 11th largest in the United Kingdom. It is also the second largest city in the English Midlands, after Birmingham, with a population of 300,848, although...
. The company specialised in the mass production of engines and gearboxes, for fitment into vehicles made by the Nuffield Organisation
Nuffield Organisation
The Nuffield Organisation was a vehicle manufacturing company in the United Kingdom. Named after its founder, William Morris, 1st Viscount Nuffield, it was formed in 1938 as the merger of Nuffield's Morris Motor Company , another of Nuffield's companies the MG Car Company and Riley.Morris Motors...
. Morris Motors Ltd., Engines Branch was, therefore, partly responsible for the Nuffield Organization becoming Britain's leading motor manufacturer in the 1930s.
Early years
The Hotchkiss companyHotchkiss et Cie
Société Anonyme des Anciens Etablissements Hotchkiss et Cie was a French arms and car company established by United States engineer Benjamin B. Hotchkiss, who was born in Watertown, Connecticut. He moved to France and set up a factory, first at Viviez near Rodez in 1867, then at Saint-Denis near...
of France, who were makers of the famous machine gun, hurriedly transferred production to England during World War I when it looked as if their St. Denis
Saint-Denis
Saint-Denis is a commune in the northern suburbs of Paris, France. It is located from the centre of Paris. Saint-Denis is a sous-préfecture of the Seine-Saint-Denis département, being the seat of the Arrondissement of Saint-Denis....
factory near Paris was going to be overrun by the Germans. Consequently, a factory was erected at Gosford Street, Coventry, and both machines and key staff were brought over to England so that production could start as soon as possible.
At the end of the War in 1918, the factory suddenly became short of work so Hotchkiss agreed to manufacture engines and gearboxes, copied from American designs, for Morris Motors Ltd. Delivery of these power units started mid 1919 and they were fitted into “Bullnose” Morris Cowley
Morris Cowley
Morris Cowley was a name given to various cars produced by the Morris Motor Company from 1915 to 1958.-Morris Cowley :The original Cowley, introduced in 1915, was a cheaper version of the first Morris Oxford and featured the same "Bullnose" radiator. To reduce the price many components were bought...
s and Morris Oxford
Morris Oxford
After the Second World War the Oxford MO replaced the 10. It was introduced in 1948 and was produced until 1954. The design was shared with Nuffield Organisation stable-mate Wolseley 4/50....
s. By 1922, the supply of power units was just sufficient to meet the level of production of Morris cars, so W.R. Morris
William Morris, 1st Viscount Nuffield
William Richard Morris, 1st Viscount Nuffield GBE, CH , known as Sir William Morris, Bt, between 1929 and 1934 and as The Lord Nuffield between 1934 and 1938, was a British motor manufacturer and philanthropist...
(later Lord Nuffield), the founder and owner of Morris Motors Ltd., asked Hotchkiss to raise production. However, Hotchkiss refused saying that they were unwilling to make more than 300 power units per week, because an expansion in England would have needed capital that they preferred to use in France.
After some negotiations, Morris bought the Hotchkiss plant and premises for £349,423 (about £15 million at 2009 values) in January 1923 and the business was renamed Morris Engines Ltd. Morris immediately set about a reorganisation and to carry out this task, he appointed F.G. Woollard
Frank George Woollard
Frank George Woollard MBE , was a British mechanical engineer who worked for nearly three decades in the British motor industry in various roles in design, production, and management...
, who had been known to Morris since 1910, as General Manager. Woollard was a pioneer in the techniques of mass
Mass production
Mass production is the production of large amounts of standardized products, including and especially on assembly lines...
and flow production and the results he achieved at the Gosford Street factory were largely due to his expertise in managing men and machines.
Engines Branch Expansion
Morris invested £300,000 in extending the Gosford Street factory and in buying new machines. Having re-organised engine production from batchBatch production
Batch production is a technique used in manufacturing, in which the object in question is created stage by stage over a series of workstations. Batch production is common in bakeries and in the manufacture of sports shoes, pharmaceutical ingredients , inks, paints and adhesives. In the manufacture...
to flow, Woollard introduced a 24 hour working day, by introducing a 3 shift system of 8 hours each, for a 5 day week. Production increased from less than 300 power units per week in January 1923, to 600 units per week in December of that year and to a remarkable 1200 units per week in December 1924.
The engine manufacturing process started when cylinder blocks arrived form one of the supplying foundries, one of which was Morris's own. After being inspected, pickled, washed and dried, the blocks were placed on a hand-transfer machining line that carried out 53 operations in turn. The process took 223 minutes and a completed block was being produced every 4 minutes.
The idea of the first hand-transfer machining line, which was operated by 21 men, evolved in 1923. Then, in 1924, the first automated transfer machine was introduced for the production of gearbox cases, which were moved from station to station by compressed air. A second automated transfer machine, for the production of flywheels, was set up in 1924. These machines were something Morris Engines Ltd. were justifiably proud of and they encouraged the public to see the process. American engineers judged the production systems to be 20 years ahead of their time.
Although the hand-transfer machining line remained in use for many years, the automated transfer machines were subsequently divided into individual machine units, as the automatic systems proved to be over complicated for technology of the time. However, Woollard had pioneered a process which is now commonplace.
In June 1926, Morris Motors Ltd became a public company. The new company, Morris Motors (1926) Ltd., then acquired some of W.R. Morris's personally owned companies which were changed into its branches. Consequently, Morris Engines Ltd. became Morris Motors Ltd., Engines Branch.
Situated as it was in a congested area of Coventry, the Gosford Street factory site had little space for expansion on horizontal lines, so a six-storey extension had been constructed. As further expansion, to meet the rising demand for power units, was foreseen, Morris purchased a 45 acres (182,108.7 m²) site north of Coventry at Courthouse Green
Courthouse Green
Courthouse Green is a suburb in the north of Coventry. It is bordered by Bell Green in the northwest, by Stoke Heath in the south, and by Foleshill in the southeast.-Longfield House:...
in 1927 and a mechanised foundry, together with the machining of cylinder blocks, was set up there.
1930s Engine Production
During the mid 1930s, new buildings were erected at Courthouse Green, into which personnel and machinery were transferred from both the Gosford Street factory and from Wolseley Motors Ltd. With the exception of those built by Morris Commercial Cars Ltd for their heavy trucks, the Courthouse Green factory of Morris Motors Ltd., Engines Branch then specialized in making power units for cars and light commercial vehicles made by the entire Nuffield Organization; notably, Morris Motors Ltd., The M.G. Car Co. Ltd., Morris Commercial Cars Ltd., and Wolseley Motors LtdWolseley Motor Company
The Wolseley Motor Company was a British automobile manufacturer founded in 1901. After 1935 it was incorporated into larger companies but the Wolseley name remained as an upmarket marque until 1975.-History:...
.
During the late 1930s, the Courthouse Green factory was turning out over 3,000 power units per week and throughout the World War II, it was working flat-out making engines for fire pumps, ambulances, military vehicles, lifeboats and tanks, as well as making component parts for aero engines and for Rotol
Dowty Rotol
Dowty Rotol is a British engineering company based in Cheltenham specialised in the manufacture of propellers and propeller components. It is owned by General Electric, forming part of its GE Aviation Systems division.-History:...
variable pitch air screws. The factory suffered extensive damage during a heavy bombing raid on Coventry in 1940, but production restarted within six weeks of the raid, even though some of its workforce were having to work in the open air as much of the factory's roof had been blown off and had still not been replaced.
After the War, Morris Motors Ltd., Engines Branch reverted to making power units for fitment into vehicles made by the Nuffield Organization and its factory became part of the British Motor Corporation
British Motor Corporation
The British Motor Corporation, or commonly known as BMC was a vehicle manufacturer from United Kingdom, formed by the merger of the Austin Motor Company and the Nuffield Organisation in 1952...
when Morris Motors Ltd. merged with the Austin Motor Company
Austin Motor Company
The Austin Motor Company was a British manufacturer of automobiles. The company was founded in 1905 and merged in 1952 into the British Motor Corporation Ltd. The marque Austin was used until 1987...
Ltd. in 1952.
See also
- William Morris, 1st Viscount NuffieldWilliam Morris, 1st Viscount NuffieldWilliam Richard Morris, 1st Viscount Nuffield GBE, CH , known as Sir William Morris, Bt, between 1929 and 1934 and as The Lord Nuffield between 1934 and 1938, was a British motor manufacturer and philanthropist...
- Morris Motor CompanyMorris Motor CompanyThe Morris Motor Company was a British car manufacturing company. After the incorporation of the company into larger corporations, the Morris name remained in use as a marque until 1984 when British Leyland's Austin Rover Group decided to concentrate on the more popular Austin marque...
- Hotchkiss et CieHotchkiss et CieSociété Anonyme des Anciens Etablissements Hotchkiss et Cie was a French arms and car company established by United States engineer Benjamin B. Hotchkiss, who was born in Watertown, Connecticut. He moved to France and set up a factory, first at Viviez near Rodez in 1867, then at Saint-Denis near...
- Frank George WoollardFrank George WoollardFrank George Woollard MBE , was a British mechanical engineer who worked for nearly three decades in the British motor industry in various roles in design, production, and management...