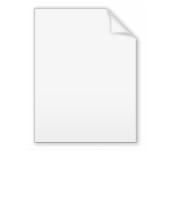
Manufacturing execution system
Encyclopedia
Manufacturing Execution Systems (MES), are information technology
systems that manage manufacturing operations in factories. Over the years, international standards and models have refined the scope of such systems in terms of activities, that typically include:
standard merged this model with the Purdue Reference Model (PRM). A functional hierarchy was defined in which MES were situated at level 3 between ERP at level 4 and process control at levels 0,1,2. Activities in level 3 were divided over four main operations: Production, Quality, Logistics and Maintenance. Additional parts of the ANSI/ISA-95 standard defined the architecture of an MES into more detail, covering how to internally distribute functionality and what information to exchange internally as well as externally.
(LIMS), Warehouse Management System
(WMS) and Computerized Maintenance Management System
(CMMS). From the MES point of view possible information flows are:
(PLM), Enterprise Resource Planning
(ERP), Customer Relationship Management
(CRM), Human Resource Management
(HRM). From the MES point of view possible information flows are:
In many cases, Middleware
Enterprise Application Integration
(EAI) systems are being used to exchange transaction messages between MES and Level 4 systems. A common data definition, B2MML
, has been defined within the ISA-95 standard to link MES systems to these Level 4 systems.
), Programmable Logic Controllers (PLC), Distributed Control Systems (DCS) and Batch Automation Systems. Information flows between MES and these process control systems are roughly similar:
Most MES systems include connectivity as part of their product offering. Direct communication of plant floor equipment data is established by connecting to the Programmable logic controllers (PLC). Often, plant floor data is first collected and diagnosed for real-time control in a Distributed control system
(DCS) or Supervisory Control and Data Acquisition (SCADA
) system. In this case, the MES systems connect to these Level 2 system for exchanging plant floor data.
The industry standard for plant floor connectivity is OLE for process control
(OPC).
Information technology
Information technology is the acquisition, processing, storage and dissemination of vocal, pictorial, textual and numerical information by a microelectronics-based combination of computing and telecommunications...
systems that manage manufacturing operations in factories. Over the years, international standards and models have refined the scope of such systems in terms of activities, that typically include:
- Management of product definitions. This may include storage, version control and exchange with other systems of master data like product production rules, bill of material, bill of resources, process set points and recipe data all focused on defining how to make a product. Management of product definitions can be part of Product lifecycle managementProduct lifecycle managementIn industry, product lifecycle management is the process of managing the entire lifecycle of a product from its conception, through design and manufacture, to service and disposal...
- Management of resources. This may include registration, exchange and analysis of resource information, aiming to prepare and execute production orders with resources of the right capabilities and availability.
- Scheduling (production processes)Scheduling (production processes)Scheduling is an important tool for manufacturing and engineering, where it can have a major impact on the productivity of a process. In manufacturing, the purpose of scheduling is to minimize the production time and costs, by telling a production facility when to make, with which staff, and on...
. These activities determine the production schedule as a collection of work orders to meet the production requirements, typically received from Enterprise resource planningEnterprise resource planningEnterprise resource planning systems integrate internal and external management information across an entire organization, embracing finance/accounting, manufacturing, sales and service, customer relationship management, etc. ERP systems automate this activity with an integrated software application...
or specialized Advanced planning and scheduling systems, making optimal use of local resources. - Dispatching production orders. Depending on the type of production processes this may include further distribution of batches, runs and work orders, issuing these to work centers and adjustment to unanticipated conditions.
- Execution of production orders. Although actual execution is done by Process controlProcess controlProcess control is a statistics and engineering discipline that deals with architectures, mechanisms and algorithms for maintaining the output of a specific process within a desired range...
systems, an MES may perform checks on resources and inform other systems about the progress of production processes. - Collection of production data. This includes collection, storage and exchange of process data, equipment status, material lot information and production logs in either a data historian or relational database.
- Production performance analysis. Create useful information out of the raw collected data about the current status of production, like Work In Progress (WIP) overviews, and the production performance of the past period like the Overall Equipment EffectivenessOverall equipment effectivenessOverall equipment effectiveness is a hierarchy of metrics which evaluates and indicates how effectively a manufacturing operation is utilized. The results are stated in a generic form which allows comparison between manufacturing units in differing industries...
or any other Performance indicator. - Production Track & TraceTrack & TraceIn distribution and logistics of many types of products, track and trace or tracking and tracing, concerns a process of determining the current and past locations of a unique item or property....
. Registration and retrieval of related information in order to present a complete history of lots, orders or equipment (particularly important in health related productions, e.g. pharmaceuticals)
History
In the early 1980s MES concepts originated from data collection systems. A wide variety of systems arose using collected data for a dedicated purpose. Further development of these systems during the 1990s introduced overlap in functionality. Then the Manufacturing Enterprise Solutions Association (MESA) introduced some structure by defining 11 functions that set the scope of MES. Early 2000 the ANSI/ISA-95ANSI/ISA-95
ANSI/ISA-95, or ISA-95 as it is more commonly referred, is an international standard for developing an automated interface between enterprise and control systems. This standard has been developed for global manufacturers...
standard merged this model with the Purdue Reference Model (PRM). A functional hierarchy was defined in which MES were situated at level 3 between ERP at level 4 and process control at levels 0,1,2. Activities in level 3 were divided over four main operations: Production, Quality, Logistics and Maintenance. Additional parts of the ANSI/ISA-95 standard defined the architecture of an MES into more detail, covering how to internally distribute functionality and what information to exchange internally as well as externally.
Relationship with other level 3 systems
The collection of systems acting on the ISA-95 level 3 can be called Manufacturing Operations Management Systems (MOMS). Apart from an MES these are typically Laboratory Information Management SystemLaboratory Information Management System
Sometimes known as a laboratory information system or laboratory management system , a laboratory information management system is a software-based laboratory and information management system that offers a set of key features that support a modern laboratory's operations...
(LIMS), Warehouse Management System
Warehouse management system
A warehouse management system, or WMS, is a key part of the supply chain and primarily aims to control the movement and storage of materials within a warehouse and process the associated transactions, including shipping, receiving, putaway and picking...
(WMS) and Computerized Maintenance Management System
Computerized Maintenance Management System
Computerized maintenance management system is also known as enterprise asset management and computerized maintenance management information system ....
(CMMS). From the MES point of view possible information flows are:
- To LIMS: quality test requests, sample lots, statistical process data
- From LIMS: quality test results, product certificates, testing progress
- To WMS: material resource requests, material definitions, product deliveries
- From WMS: material availability, staged material lots, product shipments
- To CMMS: equipment running data, equipment assignments, maintenance requests
- FROM CMMS: maintenance progress, equipment capabilities, maintenance schedule
Relationship with level 4 systems
Examples of systems acting on ISA-95 level 4 are Product Lifecycle ManagementProduct lifecycle management
In industry, product lifecycle management is the process of managing the entire lifecycle of a product from its conception, through design and manufacture, to service and disposal...
(PLM), Enterprise Resource Planning
Enterprise resource planning
Enterprise resource planning systems integrate internal and external management information across an entire organization, embracing finance/accounting, manufacturing, sales and service, customer relationship management, etc. ERP systems automate this activity with an integrated software application...
(ERP), Customer Relationship Management
Customer relationship management
Customer relationship management is a widely implemented strategy for managing a company’s interactions with customers, clients and sales prospects. It involves using technology to organize, automate, and synchronize business processes—principally sales activities, but also those for marketing,...
(CRM), Human Resource Management
Human resource management
Human Resource Management is the management of an organization's employees. While human resource management is sometimes referred to as a "soft" management skill, effective practice within an organization requires a strategic focus to ensure that people resources can facilitate the achievement of...
(HRM). From the MES point of view possible information flows are:
- To PLM: production test results
- From PLM: product definitions, bill of operations (routings), electronic work instructions, equipment settings
- To ERP: production performance results, produced and consumed material
- From ERP: production planning, order requirements
- To CRM: product tracking and tracing information
- From CRM: product complaints
- To HRM: personnel performance
- From HRM: personnel skills, personnel availability
In many cases, Middleware
Middleware
Middleware is computer software that connects software components or people and their applications. The software consists of a set of services that allows multiple processes running on one or more machines to interact...
Enterprise Application Integration
Enterprise application integration
Enterprise Application Integration is defined as the use of software and computer systems architectural principles to integrate a set of enterprise computer applications.- Overview :...
(EAI) systems are being used to exchange transaction messages between MES and Level 4 systems. A common data definition, B2MML
B2MML
B2MML or Business To Manufacturing Markup Language is an XML implementation of the ANSI/ISA-95 family of standards , known internationally as IEC/ISO 62264...
, has been defined within the ISA-95 standard to link MES systems to these Level 4 systems.
Relationship with level 0,1,2 systems
Systems acting on ISA-95 level 2 are Supervisory Control And Data Acquisition (SCADASCADA
SCADA generally refers to industrial control systems : computer systems that monitor and control industrial, infrastructure, or facility-based processes, as described below:...
), Programmable Logic Controllers (PLC), Distributed Control Systems (DCS) and Batch Automation Systems. Information flows between MES and these process control systems are roughly similar:
- To PCS: work instructions, recipes, set points
- From PCS: process values, alarms, adjusted set points, production results
Most MES systems include connectivity as part of their product offering. Direct communication of plant floor equipment data is established by connecting to the Programmable logic controllers (PLC). Often, plant floor data is first collected and diagnosed for real-time control in a Distributed control system
Distributed control system
A distributed control system refers to a control system usually of a manufacturing system, process or any kind of dynamic system, in which the controller elements are not central in location but are distributed throughout the system with each component sub-system controlled by one or more...
(DCS) or Supervisory Control and Data Acquisition (SCADA
SCADA
SCADA generally refers to industrial control systems : computer systems that monitor and control industrial, infrastructure, or facility-based processes, as described below:...
) system. In this case, the MES systems connect to these Level 2 system for exchanging plant floor data.
The industry standard for plant floor connectivity is OLE for process control
OLE for process control
OLE for Process Control , which stands for Object Linking and Embedding for Process Control, is the original name for a standards specification developed in 1996 by an industrial automation industry task force...
(OPC).
Sources
- Manufacturing Enterprise Solutions Association http://www.mesa.org
- International Society of Automation http://www.isa.org/