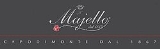
Majello
Encyclopedia
The anciest Italian factory producing Porcelain of Capodimonte
.
The first phase consists in the obtainment of the chalk model. This operation will be effected on a lathe on which a chalk block has been affixed. The sculptor will make with his hands and with some traditional and rudimental tools the forging of the model so to delineate its outline.
Gotten the model, it will be removed by the lathe and the sculptor will chisel and carve the details of the object.
Finished this operation we obtain the final model used for having the first form.
The artisan now put in the chalk model the porcelain in liquid form, this porcelain is very different from the common white ceramics, because of its greatest transparency and preciousness.
After a brief desiccation of the porcelain, we obtain the raw object.
It follows now a following phase that is the finishing touch. The artisan must eliminate possible dribbles or imperfections that can be verified in the previous phase. Besides he has to delineate the details of the piece.
We now pass to the most interesting phase of the production: The floral decoration that countersigns this art. It is thanks to the ability of neapolitan artists in creating porcelain flowers that the porcelain of capodimonte has become famous all over the world. These artists mould the porcelain in a very thin way so to render the petals, the leaves, the pistils similar to those that we can find in nature. They give to the flowers the same lightness they possess in nature.
Once completed the piece and verified that the object doesn't have any imperfection it will be affixed the mark of the signature to give guarantee of authenticity to the buyer.
We make now the first cooking to a temperature of 1250 grades that lasts minimum 8 and maximum 12 hours from which we obtain the biscuit object.
We pass to the phase of the decoration that is very fascinating. The experienced decorators paint the object only and exclusively by brush. Then, of course, each factory has its own secrets for the creation of the tonalities of colour. Each factory impresses its own style to the object. Once decorated we make a second cooking at 750 grades to fix the colour. It lasts almost 8 hours. The working trial is now ended. The piece of porcelain of Capodimonte is born.
2) The personal production of the pug of porcelain that warranties the lightness and the transparency of matter.
3) The ability of the sculptors in forging each singular detail that will form the Piece.
4) The creativity of the sculptors to project and realize each piece that becomes the witness of a “unique and recognizable” style.
5) The respect for the time necessary to exsiccate the piece before cooking.
6) The skills of the decorators in blending the colours in a very personal way so to make them inimitable.
7) The inspiration of the decorators in painting by paint-brush the piece which reveals the multitude of lively nuances of colours
8) The application of the traditional technique of cooking the “biscuit” porcelain. The first one at 1350 grades and the second one, after decoration, at 700/800 grades
9) The application of the traditional technique of cooking called “terzo fuoco” (“third fire”) for the shiny porcelain. The first one at 800 grades, the second one after varnishing at 1300 grades, and the third one, after decoration at 750 grades
10) The absolute respect of Capodimonte traditions handed from father to son for four generations
Flowers
Composition of flowers that reproduce the same thin texture and the same lively colours they possess in nature
Porcelain "spaghetto"
Plates, lamps, vases and various object completely hand made, enterlaced with very thin porcelain in "spaghetto" shape.
Classic style
Reproduction of well known masterpieces, for example "ReginAmalia", the freely ispired reproduction of the famous lamp created at the end of 1700 by the artist Giuseppe Gricci for Queen Amalia, the loved wife of king Charles of Borbon, for her personal boudoir totally made of porcelain.
Statues
Reproduction of sculptures of the Classic period.
Capodimonte porcelain
Capodimonte porcelain is porcelain created by the Capodimonte porcelain manufactory, which was established in Naples, Italy in 1743. Capodimonte porcelain was made in direct emulation of Meissen porcelain...
.
History
In 1867 Alfonso Majello, awarded "knight of Job" founded the Majello factory that continued the tradition of producing porcelains of Capodimonte started in 1743 with the Real Factory of Capodimonte founded by the Spanish king Charles. This tradition handed on from father to son for four generation. Today it continues thanks to the sculptor Lucio Majello and his sons.Manufacture
First of all the object always departs from an idea, from the fancy of the artist and therefore, with the use of the traditional old pencil the artist will trace the sketch of the object that he will go to realize.The first phase consists in the obtainment of the chalk model. This operation will be effected on a lathe on which a chalk block has been affixed. The sculptor will make with his hands and with some traditional and rudimental tools the forging of the model so to delineate its outline.
Gotten the model, it will be removed by the lathe and the sculptor will chisel and carve the details of the object.
Finished this operation we obtain the final model used for having the first form.
The artisan now put in the chalk model the porcelain in liquid form, this porcelain is very different from the common white ceramics, because of its greatest transparency and preciousness.
After a brief desiccation of the porcelain, we obtain the raw object.
It follows now a following phase that is the finishing touch. The artisan must eliminate possible dribbles or imperfections that can be verified in the previous phase. Besides he has to delineate the details of the piece.
We now pass to the most interesting phase of the production: The floral decoration that countersigns this art. It is thanks to the ability of neapolitan artists in creating porcelain flowers that the porcelain of capodimonte has become famous all over the world. These artists mould the porcelain in a very thin way so to render the petals, the leaves, the pistils similar to those that we can find in nature. They give to the flowers the same lightness they possess in nature.
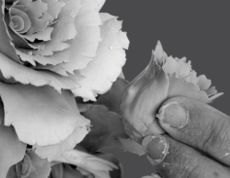
We make now the first cooking to a temperature of 1250 grades that lasts minimum 8 and maximum 12 hours from which we obtain the biscuit object.
We pass to the phase of the decoration that is very fascinating. The experienced decorators paint the object only and exclusively by brush. Then, of course, each factory has its own secrets for the creation of the tonalities of colour. Each factory impresses its own style to the object. Once decorated we make a second cooking at 750 grades to fix the colour. It lasts almost 8 hours. The working trial is now ended. The piece of porcelain of Capodimonte is born.
Decalogue of authentic Capodimonte
1) The usage of moulds and shapes that are a perfect reproduction of those ones used in 18th century in the Real Factory of Capodimonte.2) The personal production of the pug of porcelain that warranties the lightness and the transparency of matter.
3) The ability of the sculptors in forging each singular detail that will form the Piece.
4) The creativity of the sculptors to project and realize each piece that becomes the witness of a “unique and recognizable” style.
5) The respect for the time necessary to exsiccate the piece before cooking.
6) The skills of the decorators in blending the colours in a very personal way so to make them inimitable.
7) The inspiration of the decorators in painting by paint-brush the piece which reveals the multitude of lively nuances of colours
8) The application of the traditional technique of cooking the “biscuit” porcelain. The first one at 1350 grades and the second one, after decoration, at 700/800 grades
9) The application of the traditional technique of cooking called “terzo fuoco” (“third fire”) for the shiny porcelain. The first one at 800 grades, the second one after varnishing at 1300 grades, and the third one, after decoration at 750 grades
10) The absolute respect of Capodimonte traditions handed from father to son for four generations
Typical "Capodimonte" subjects
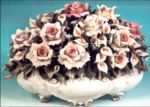
Composition of flowers that reproduce the same thin texture and the same lively colours they possess in nature
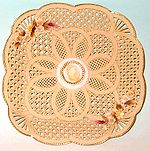
Plates, lamps, vases and various object completely hand made, enterlaced with very thin porcelain in "spaghetto" shape.
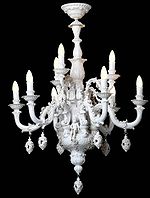
Reproduction of well known masterpieces, for example "ReginAmalia", the freely ispired reproduction of the famous lamp created at the end of 1700 by the artist Giuseppe Gricci for Queen Amalia, the loved wife of king Charles of Borbon, for her personal boudoir totally made of porcelain.
Statues
Reproduction of sculptures of the Classic period.