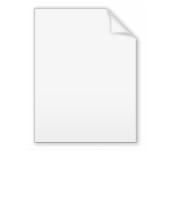
Hardening (metallurgy)
Encyclopedia
Hardening is a metallurgical and metalworking
process used to increase the hardness of a metal. The hardness of a metal is directly proportional to the uniaxial yield stress at the location of the imposed strain. A harder metal will have a higher resistance to plastic deformation than a less hard metal.
All hardening mechanisms, except of the martensitic transformation, introduce dislocations or defects in a crystal lattice that act as barriers to slip.
Metalworking
Metalworking is the process of working with metals to create individual parts, assemblies, or large scale structures. The term covers a wide range of work from large ships and bridges to precise engine parts and delicate jewelry. It therefore includes a correspondingly wide range of skills,...
process used to increase the hardness of a metal. The hardness of a metal is directly proportional to the uniaxial yield stress at the location of the imposed strain. A harder metal will have a higher resistance to plastic deformation than a less hard metal.
Processes
The five hardening processes are:- The Hall–Petch method is used to change the grain size in a material, which can affect the dislocation density. Smaller grain size will make the material harder, but if the grains get too small the hardness can actually decrease.
- In work hardeningWork hardeningWork hardening, also known as strain hardening or cold working, is the strengthening of a metal by plastic deformation. This strengthening occurs because of dislocation movements within the crystal structure of the material. Any material with a reasonably high melting point such as metals and...
(also referred to as strain or cold hardening) the material is strained past its yield point. The work done on the material adds energy and has the ability to move and generate dislocations. This process usually takes place at a temperature below the materials recrystallization temperature. - In solid solution strengtheningSolid solution strengtheningSolid solution strengthening is a type of alloying that can be used to improve the strength of a pure metal. The technique works by adding atoms of one element to the crystalline lattice of another element . The alloying element diffuses into the matrix, forming a solid solution...
, an alloying element is added to the material desired to be strengthened, and together they form a “solid solution”. Different alloying elements can be used to cause either a substitutional or an interstitial solid solution. - Precipitation hardening is a process where impure particles are distributed throughout the metal. This is achieved by first heating the metal above its phase transition temperature and then rapidly cooling the metal. Particles of the second phase become trapped and form anchor points to impede the movement of dislocations. Precipitation hardening is one of the most commonly used techniques for the hardening of metal alloys. In steels, a similar method is referred to as a martensitic transformation. In this transformation, austenite is rapidly cooled off before the dissolved carbon atoms have a chance to escape, forming martensite, a higher hardness phase of steel.
- Martensitic transformation, more commonly known as quenching and temperingTemperingTempering is a heat treatment technique for metals, alloys and glass. In steels, tempering is done to "toughen" the metal by transforming brittle martensite or bainite into a combination of ferrite and cementite or sometimes Tempered martensite...
.
All hardening mechanisms, except of the martensitic transformation, introduce dislocations or defects in a crystal lattice that act as barriers to slip.
Applications
Material hardening is required for many applications:- Machine cutting tools (drill bits, taps, lathe tools) need be much harder than the material they are operating on in order to be effective.
- Knife blades – a high hardness blade keeps a sharp edge.
- Bearings – necessary to have a very hard surface that will withstand continued stresses