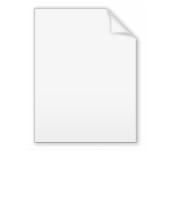
Glass cutter
Encyclopedia
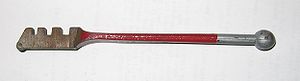
Typically the metal tool is six inches long with a rolling V-shaped cutting wheel of hardened steel
Hardened steel
The term hardened steel is often used for a medium or high carbon steel that has been given the heat treatments of quenching followed by tempering. The quenching results in the formation of metastable martensite, the fraction of which is reduced to the desired amount during tempering. This is the...
or tungsten carbide
Tungsten carbide
Tungsten carbide is an inorganic chemical compound containing equal parts of tungsten and carbon atoms. Colloquially, tungsten carbide is often simply called carbide. In its most basic form, it is a fine gray powder, but it can be pressed and formed into shapes for use in industrial machinery,...
. The wheel is slightly smaller than the diameter of a pencil. Some glass cutters hold a small amount of cutting oil, so the cutting wheel is automatically lubricated as it turns.
The wheel of the glass cutter is the all important part. The ordinary type is made of very high grade tool steel, carefully ground, balanced and axeled. When properly lubricated and maintained it can give a log period of satisfactory service. Within the past decade ( article written 1968) carbide wheels have come into rather popular acceptance. Utilizing tungsten carbide, long recognized as one of the "hardest metal known to man", (sic) these wheels permit a relatively longer life than the standard steel wheel and offer certain advantages in use-greater penetration in cutting and greater ease in parting the glass after use of the glass cutter.
In the middle ages glass was cut with a tool which was nothing more than a sharply pointed rod of iron, heated to a high temperature. The red hot point was drawn along the moistened surface of the glass causing it to snap apart. The fracture was not very accurate and the rough piece had to be chipped or grozed down to the exact shape with the help of a hooked tool called a grozing iron. The present day Steel Wheel Cutter, which is almost universally used, was invented in 1869 by Samuel Monce in Bristol. Connecticut.
At the time the first steel wheel glass cutter was invented in 1869, glass manufacturers produced mostly plain flat glass which was used primarily for windows. Great progress has taken place over the years until now we have hard glass, soft glass, heat-resisting glass, thick glass, thin glass, decorative glass and countless other varieties.With these many variations it becomes necessary to change the penetration action of the wheel to compensate for the difference in the structural composition of the glass. This is accomplished by varying the degree of the bevel which produces a progressively sharper or duller "cut." A soft glass such as plate glass requires a dull cutting while the harder glass requires a sharper wheel.
There is a reason for the difference in cutter wheel diameters. The great majority of wheels are 7/32" in diameter. The pressure of the wheel as it rolls over the glass has a bearing on the penetration, and there is a ratio between the pressure and the arc of the wheel that is important. With average hand pressure the 7/32" diameter wheel gives best results. For a duller wheel on soft glass a slightly different pressure is required. This is compensated for with a larger wheel, 1/4" in diameter making it unnecessary for the operator to change the hand pressure. The smaller wheel, 1/8" in diameter, is used for cutting patterns, and for cutting circles. Here the wheel with a small arc is necessary to follow curved lines without dragging.
A computer-assisted CNC semi-automatic glass cutting table is usually used to score large sheets of glass, which are then broken out by hand into the individual sheets of glass (also known as "lites" in the glass industry).
Cutting process
The glass cutter or the glass itself is carefully lubricated along the cut line with light oil (cutting oil) or paraffinParaffin
In chemistry, paraffin is a term that can be used synonymously with "alkane", indicating hydrocarbons with the general formula CnH2n+2. Paraffin wax refers to a mixture of alkanes that falls within the 20 ≤ n ≤ 40 range; they are found in the solid state at room temperature and begin to enter the...
. Then the cutter is pressed tightly against the glass and a line is scribed with the help of a ruler to form a split in the surface of the glass. This split is referred to as a "score". The score may then be widened by carefully tapping on the opposite side of the glass with a hard tool, but this reduces the smoothness of the broken edge. Finally, the glass is broken along the score. After breaking, the cut edge of the glass may be polished to smooth the sharp and dangerous edges. If the break deviates from the score, the lite can often be salvaged by snapping off the extra glass with a special pair of pliers or using the notches in the glass cutter. Glass thickness affects the ability to cut and break glass. Generally, thicker glass is more difficult to cut and break. Quarter inch (6.4 mm) plate glass requires considerable strength to break along the score. Extremely thin glass, for example 1/16 inch (1.6 mm) glass, behaves differently and will often not follow the score, regardless of the glass cutter's expertise and experience.
Breaking methods
Three methods are usually used to break the glass along the score. In the first method, the operator uses two hands and holds the edge of the glass, perpendicular to the score, with the forefingers under the glass and the thumbs on top. The operator then rotates both hands outward to break the glass along the line. The second method consists of placing one finger underneath the sheet of glass, directly under the scribed line, and in one smooth motion, lifting the edge of the glass and giving it a small push horizontally. The second method is quicker than the first, but requires more practice. These two methods are usually used when breaking glass on a glass cutting table that lifts the glass gently by forcing air up through the table. The third method is used with smaller sheets of glass, and consists of placing the score along the edge of the table and snapping the overhanging part of the glass in a downward motion. With experience, the break follows the score.However breaking with one finger under the score is dangerous and will pinch the finger as the glass rolls away.
Also, along the cut glasses edge, one can tell which way the cutter was run and which way the glass was run or snapped, by looking at the flow of feathers, in the edge.
In most scenarios, glass will break where you want it, so long as its well lubricated and run before it has a chance to cool off.