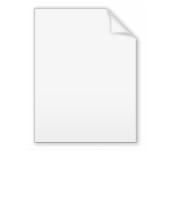
Electrical CAD
Encyclopedia
Electrical CAD refers to software packages
that allow an electrical engineer to create and manage electrical schematics. Advanced packages will not only manage electrical schematics, but also integrate functionalities such as cabinet and panel lay-outs and terminal management.
The benefit of using E-CAD solutions is to create harnesses using among logic information provided from the user geometrical information from the CAD system.
Electrical components within any kind of construction need to be connected with harnesses. This can be components like PCBs (printed circuite boards), controls, drives, gauges or any other kind which has to be connected either to just provide electrical energy or to exchange information. These components are located anywhere in the construction and the harness has to connect them with their correspondents. First, of course, the harness needs to reach all electrical components using a defined path. The path should be defined early in the conception phase to avoid intersections. Second, the harness underlies environmental conditions, like heat, humiditiy or chemical aggressive substances in certain zones. Finally, each wire terminates in a connector who fits to the environmental conditions, too. Connectors are also necessary to break a harness into two parts for physical reason. Example: The interior of a car door is connected to the other harness after mounting the pre-equipped door.
In the E-CAD solution, the electrical logic will be defined parallel to the space reservation made in a 3D CAD system (if any).
In a following step the defined wires are (auto-)routed to join the logic with the predefinition. This step is mostly to take the length information coming from M-CAD into account. Then, protections have to be added or wires have to be defined according the environmental conditions. The final output of the E-CAD will be a so called "nailboard" drawing, which was nothing else than a wooden table in which nails were positioned to manufacture the cable tree, and a part list and the pin-out number lists. Today, this becomes more and more automated, too. Data exchange between E-CAD and the harness creator is done with native data and the manufacturing can be automated.
Some packages are even becoming Product Lifecycle Management
packages as they allow to manage the entire electrical design process.
Computer software
Computer software, or just software, is a collection of computer programs and related data that provide the instructions for telling a computer what to do and how to do it....
that allow an electrical engineer to create and manage electrical schematics. Advanced packages will not only manage electrical schematics, but also integrate functionalities such as cabinet and panel lay-outs and terminal management.
The benefit of using E-CAD solutions is to create harnesses using among logic information provided from the user geometrical information from the CAD system.
Electrical components within any kind of construction need to be connected with harnesses. This can be components like PCBs (printed circuite boards), controls, drives, gauges or any other kind which has to be connected either to just provide electrical energy or to exchange information. These components are located anywhere in the construction and the harness has to connect them with their correspondents. First, of course, the harness needs to reach all electrical components using a defined path. The path should be defined early in the conception phase to avoid intersections. Second, the harness underlies environmental conditions, like heat, humiditiy or chemical aggressive substances in certain zones. Finally, each wire terminates in a connector who fits to the environmental conditions, too. Connectors are also necessary to break a harness into two parts for physical reason. Example: The interior of a car door is connected to the other harness after mounting the pre-equipped door.
In the E-CAD solution, the electrical logic will be defined parallel to the space reservation made in a 3D CAD system (if any).
In a following step the defined wires are (auto-)routed to join the logic with the predefinition. This step is mostly to take the length information coming from M-CAD into account. Then, protections have to be added or wires have to be defined according the environmental conditions. The final output of the E-CAD will be a so called "nailboard" drawing, which was nothing else than a wooden table in which nails were positioned to manufacture the cable tree, and a part list and the pin-out number lists. Today, this becomes more and more automated, too. Data exchange between E-CAD and the harness creator is done with native data and the manufacturing can be automated.
Some packages are even becoming Product Lifecycle Management
Product lifecycle management
In industry, product lifecycle management is the process of managing the entire lifecycle of a product from its conception, through design and manufacture, to service and disposal...
packages as they allow to manage the entire electrical design process.