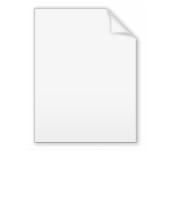
Eddy-current testing
Encyclopedia
Eddy-current testing uses electromagnetic induction
to detect flaws in conductive materials. There are several limitations, among them: only conductive materials can be tested, the surface of the material must be accessible, the finish of the material may cause bad readings, the depth of penetration into the material is limited by the materials' conductivity, and flaws that lie parallel to the probe may be undetectable.
In a standard eddy current testing a circular coil carrying current is placed in proximity to the test specimen (which must be electrically conductive).The alternating current in the coil generates changing magnetic field which interacts with test specimen and generates eddy current.Variations in the phase and magnitude of these eddy currents can be monitored using a second 'receiver' coil, or by measuring changes to the current flowing in the primary 'excitation' coil. Variations in the electrical conductivity or magnetic permeability of the test object, or the presence of any flaws, will cause a change in eddy current and a corresponding change in the phase and amplitude of the measured current. This is the basis of standard (flat coil) eddy current inspection, the most widely used eddy current technique.
However, eddy-current testing can detect very small cracks in or near the surface of the material, the surfaces need minimal preparation, and physically complex geometries can be investigated. It is also useful for making electrical conductivity and coating thickness measurements.
The testing devices are portable, provide immediate feedback, and do not need to contact the item in question.
Recently tomographic notion of ECT has been explored see for example:
Electromagnetic induction
Electromagnetic induction is the production of an electric current across a conductor moving through a magnetic field. It underlies the operation of generators, transformers, induction motors, electric motors, synchronous motors, and solenoids....
to detect flaws in conductive materials. There are several limitations, among them: only conductive materials can be tested, the surface of the material must be accessible, the finish of the material may cause bad readings, the depth of penetration into the material is limited by the materials' conductivity, and flaws that lie parallel to the probe may be undetectable.
In a standard eddy current testing a circular coil carrying current is placed in proximity to the test specimen (which must be electrically conductive).The alternating current in the coil generates changing magnetic field which interacts with test specimen and generates eddy current.Variations in the phase and magnitude of these eddy currents can be monitored using a second 'receiver' coil, or by measuring changes to the current flowing in the primary 'excitation' coil. Variations in the electrical conductivity or magnetic permeability of the test object, or the presence of any flaws, will cause a change in eddy current and a corresponding change in the phase and amplitude of the measured current. This is the basis of standard (flat coil) eddy current inspection, the most widely used eddy current technique.
However, eddy-current testing can detect very small cracks in or near the surface of the material, the surfaces need minimal preparation, and physically complex geometries can be investigated. It is also useful for making electrical conductivity and coating thickness measurements.
The testing devices are portable, provide immediate feedback, and do not need to contact the item in question.
Recently tomographic notion of ECT has been explored see for example:
External links
- An introduction to eddy current testing from the NDE/NDT resource center
- Intro to Eddy Current Testing by Joseph M. Buckley (pdf, 429 kB)
- Eddy Current Testing at Level 2, International Atomic Energy Agency, Vienna, 2011 (pdf 5.6 MB).