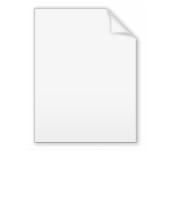
Compact wind acceleration turbine
Encyclopedia
Compact Wind Acceleration Turbines (CWATs) are a class of wind turbine that uses structures to accelerate wind before it enters the wind-generating element.
The concept of these structures has been around for decades but has not gained wide acceptance in the marketplace. In 2008, two companies targeting the mid-wind (100 kW-1 MW) marketplace have received funding from venture capital. The first company to receive funding is Optiwind, which received its series A funding in April 2008, and the second company is FloDesign Wind Turbine Corp, which also received its series A funding in April 2008. Optiwind http://www.optiwind.com is funded through Charles River Ventures and FloDesign is funded through Kleiner Perkins.
Other CWATs under development include the Windtamer and Enflo turbines.
CWATs are a new acronym that encompasses the class of machines formerly known as DAWTs (diffuser augmented wind turbines). The technologies mentioned above all use diffuser augmentation that is substantially similar to previous designs as the primary means of acceleration.
DAWTs were heavily researched by K. Foreman and Oman of Grumman Aerospace in the 1970s and 1980s and Igra in Israel in the 1970s. At the end of a decade of wind tunnel research and design funded by Grumman, NASA, and the DOE, it was determined that the DAWT system's economics were not sufficient to justify commercialization. In the 1990s the Grumman technology was licensed to a New Zealand company, Vortec Wind. The attempt to commercialize the Vortec 7 in New Zealand from 1998 to 2002 proved it to be economically untenable when compared to the dominant HAWT (horizontal axis wind turbine) technology.
The historic failure of DAWTs to gain acceptance has to do with the economics of these systems. DAWT systems have not shown improvement in the economics of HAWTs. This lack of advantage has centered around two key factors affecting the development of this type of machine.
The first factor regards power increase and the method of comparison used by DAWT (and more recently CWAT) designers to determine the whether the system is worth developing. Grumman and other attempts to commercialize these machines compare their machines to HAWTs based on a rotor area to rotor area comparison. As Van Bussel of Delft (The Science of Making More Torque from Wind: Diffuser Experiments and Theory Revisited, G.J.W. van Bussel, Delft, 2007) (http://repository.tudelft.nl/view/ir/uuid%3A2f19000e-f2b5-468e-8d10-5e338e1be888/) pointed out, this is an inaccurate comparison and the comparison of power multiples should be made on the basis of the exit area of the diffuser or shroud not the rotor area.
Grumman claimed a 4× increase over an unshrouded turbine based on an acceleration of 1.6 times the ambient wind velocity (An Investigation on Diffuser Augmented Turbines, D.G. Philips, 2003 (reference materials compiled from K.M. Foreman)). A 1.6 acceleration is in fact 2.6 times the power of a HAWT if the ratio of the shrouded rotor to the exit area is 1.6. If however the rotor to exit area ratio is 2.75 (as it was in the Grumman case), the actual power increase over a HAWT with the same swept area as the diffuser exit area is only 1.4× the power. Given that the DAWTs with this ratio have roughly a solidity of 60+% when the blades and the diffuser are accounted for and the solidity of the HAWT is roughly 10%, the cost and amount of material needed to produce the 40% gain outweighs the increase in power.
Second is the structural requirement in terms of resisting overturning and bending in extreme wind events which all wind turbines must be designed for by ISO standard. The DAWT structure has poor drag characteristics (see D.G. Philips). That combined with higher solidity leads to substantially greater structural costs than a HAWT in the support structure, the yaw bearing, and the foundation.
For these reasons, low power increase when referred to exit area and structural costs, DAWTs have not been a solution to improving wind energy at utility scale. The power increases thus far have proved insufficient to offset the structural costs. In small wind applications where structural issues are lessened they may be better than HAWTs if it can be definitively shown that they can improve output by 40% for the same cost.
The recent attempts mentioned above to improve on the DAWT type (the CWATs) appear to have similar issues.
In the case of Optiwind a 3 times increase is claimed for their 150 KW and 300 KW based on the horizontal dimension of their machine. If the power these machines produce is referred to the stack height (the vertical height - the tower height) of their system, it is only roughly 80% of the power produced by a HAWT of that diameter. The solidity and drag properties of the Optiwind are again problematic in extreme wind events and it seems unlikely that the system represents a cost improvement over a HAWT.
Flodesign's MEWT (mixer-ejector wind turbine, another CWAT variation) is differentiated from previous DAWT's by using a lobed two stage diffuser (Grumman and Vortec machine were also two stage, but conical instead of lobed) to equalize the pressure over the exit area of the diffuser. The theory is that creating a uniform pressure distribution with the lobes and the injection of external flow will prevent boundary layer separation in the diffuser thereby allowing the maximum acceleration through rotor. Werle and Presz's (Flodesign's chief scientists) paper, AAIA technical note Ducted Water/Wind turbines revisited - 2007, details the theory behind their design. Maximum acceleration detailed in their paper is 1.8× the ambient velocity from which they derive that 3-5 times more power is available at the rotor than for an unshrouded turbine. When referred to exit area this multiple drops to between parity and 2.1 times the HAWT power. Flodesign's turbine based on released images and CAD's appears to be substantially similar to the Vortec and Grumman machines except for the lobed inner annulus. This would indicate that it's drag characteristics can be expected to be similar.
Again it is unclear that these machines can outperform HAWTs on either a power output or cost basis. Additionally many CWAT companies seem to misunderstand certain aspects of wind power. There are many claims that because these machines start at lower speeds and stop at higher speeds they can gather even more power. The fact is that there is very little power in winds below 5 meters per second (2% of annual production) and the percentage of annual wind that falls above the HAWT cut out speed of 25 meters per second is less than .05%. Many of these claims including the idea that these machines will use less material than a HAWT for the same rating seem somewhat poorly thought out.{ http://venturebeat.com/2010/01/20/flodesign-adapts-jet-engines-to-power-up-wind-turbines/ }
There is one recent DAWT design that appears to have a definitive positive power, if not cost, comparison to HAWTs. This is the Enflo turbine. Based on its rotor:exit ratio and the published power performance this turbine appears to have a confirmed 2 times increase in power output over a HAWT of the diameter of the exit area. It is still unlikely that this machine can scale to larger ratings but based on published data the Enflo appears to be the best performing DAWT/CWAT yet built.{ http://www.enflo-windtec.ch/english/turbine.html }
The concept of these structures has been around for decades but has not gained wide acceptance in the marketplace. In 2008, two companies targeting the mid-wind (100 kW-1 MW) marketplace have received funding from venture capital. The first company to receive funding is Optiwind, which received its series A funding in April 2008, and the second company is FloDesign Wind Turbine Corp, which also received its series A funding in April 2008. Optiwind http://www.optiwind.com is funded through Charles River Ventures and FloDesign is funded through Kleiner Perkins.
Other CWATs under development include the Windtamer and Enflo turbines.
CWATs are a new acronym that encompasses the class of machines formerly known as DAWTs (diffuser augmented wind turbines). The technologies mentioned above all use diffuser augmentation that is substantially similar to previous designs as the primary means of acceleration.
DAWTs were heavily researched by K. Foreman and Oman of Grumman Aerospace in the 1970s and 1980s and Igra in Israel in the 1970s. At the end of a decade of wind tunnel research and design funded by Grumman, NASA, and the DOE, it was determined that the DAWT system's economics were not sufficient to justify commercialization. In the 1990s the Grumman technology was licensed to a New Zealand company, Vortec Wind. The attempt to commercialize the Vortec 7 in New Zealand from 1998 to 2002 proved it to be economically untenable when compared to the dominant HAWT (horizontal axis wind turbine) technology.
The historic failure of DAWTs to gain acceptance has to do with the economics of these systems. DAWT systems have not shown improvement in the economics of HAWTs. This lack of advantage has centered around two key factors affecting the development of this type of machine.
The first factor regards power increase and the method of comparison used by DAWT (and more recently CWAT) designers to determine the whether the system is worth developing. Grumman and other attempts to commercialize these machines compare their machines to HAWTs based on a rotor area to rotor area comparison. As Van Bussel of Delft (The Science of Making More Torque from Wind: Diffuser Experiments and Theory Revisited, G.J.W. van Bussel, Delft, 2007) (http://repository.tudelft.nl/view/ir/uuid%3A2f19000e-f2b5-468e-8d10-5e338e1be888/) pointed out, this is an inaccurate comparison and the comparison of power multiples should be made on the basis of the exit area of the diffuser or shroud not the rotor area.
Grumman claimed a 4× increase over an unshrouded turbine based on an acceleration of 1.6 times the ambient wind velocity (An Investigation on Diffuser Augmented Turbines, D.G. Philips, 2003 (reference materials compiled from K.M. Foreman)). A 1.6 acceleration is in fact 2.6 times the power of a HAWT if the ratio of the shrouded rotor to the exit area is 1.6. If however the rotor to exit area ratio is 2.75 (as it was in the Grumman case), the actual power increase over a HAWT with the same swept area as the diffuser exit area is only 1.4× the power. Given that the DAWTs with this ratio have roughly a solidity of 60+% when the blades and the diffuser are accounted for and the solidity of the HAWT is roughly 10%, the cost and amount of material needed to produce the 40% gain outweighs the increase in power.
Second is the structural requirement in terms of resisting overturning and bending in extreme wind events which all wind turbines must be designed for by ISO standard. The DAWT structure has poor drag characteristics (see D.G. Philips). That combined with higher solidity leads to substantially greater structural costs than a HAWT in the support structure, the yaw bearing, and the foundation.
For these reasons, low power increase when referred to exit area and structural costs, DAWTs have not been a solution to improving wind energy at utility scale. The power increases thus far have proved insufficient to offset the structural costs. In small wind applications where structural issues are lessened they may be better than HAWTs if it can be definitively shown that they can improve output by 40% for the same cost.
The recent attempts mentioned above to improve on the DAWT type (the CWATs) appear to have similar issues.
In the case of Optiwind a 3 times increase is claimed for their 150 KW and 300 KW based on the horizontal dimension of their machine. If the power these machines produce is referred to the stack height (the vertical height - the tower height) of their system, it is only roughly 80% of the power produced by a HAWT of that diameter. The solidity and drag properties of the Optiwind are again problematic in extreme wind events and it seems unlikely that the system represents a cost improvement over a HAWT.
Flodesign's MEWT (mixer-ejector wind turbine, another CWAT variation) is differentiated from previous DAWT's by using a lobed two stage diffuser (Grumman and Vortec machine were also two stage, but conical instead of lobed) to equalize the pressure over the exit area of the diffuser. The theory is that creating a uniform pressure distribution with the lobes and the injection of external flow will prevent boundary layer separation in the diffuser thereby allowing the maximum acceleration through rotor. Werle and Presz's (Flodesign's chief scientists) paper, AAIA technical note Ducted Water/Wind turbines revisited - 2007, details the theory behind their design. Maximum acceleration detailed in their paper is 1.8× the ambient velocity from which they derive that 3-5 times more power is available at the rotor than for an unshrouded turbine. When referred to exit area this multiple drops to between parity and 2.1 times the HAWT power. Flodesign's turbine based on released images and CAD's appears to be substantially similar to the Vortec and Grumman machines except for the lobed inner annulus. This would indicate that it's drag characteristics can be expected to be similar.
Again it is unclear that these machines can outperform HAWTs on either a power output or cost basis. Additionally many CWAT companies seem to misunderstand certain aspects of wind power. There are many claims that because these machines start at lower speeds and stop at higher speeds they can gather even more power. The fact is that there is very little power in winds below 5 meters per second (2% of annual production) and the percentage of annual wind that falls above the HAWT cut out speed of 25 meters per second is less than .05%. Many of these claims including the idea that these machines will use less material than a HAWT for the same rating seem somewhat poorly thought out.{ http://venturebeat.com/2010/01/20/flodesign-adapts-jet-engines-to-power-up-wind-turbines/ }
There is one recent DAWT design that appears to have a definitive positive power, if not cost, comparison to HAWTs. This is the Enflo turbine. Based on its rotor:exit ratio and the published power performance this turbine appears to have a confirmed 2 times increase in power output over a HAWT of the diameter of the exit area. It is still unlikely that this machine can scale to larger ratings but based on published data the Enflo appears to be the best performing DAWT/CWAT yet built.{ http://www.enflo-windtec.ch/english/turbine.html }