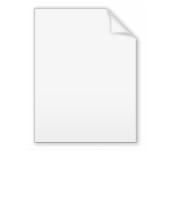
Cement tile
Encyclopedia
Cement tiles are hand-made, decorative, colorful tiles used primarily as floor coverings. Floors or walls covered with these tiles are noted for their multi-color patterns, durability and sophisticated-look. These tiles are widely used in Latin America and Europe. Their popularity spread to the US, primarily in California and Florida through the 1930s and 40s.
Although sometimes mistakenly called encaustic tile
, which refers to kiln-fired clay tile or commonly used ceramic tiles that have been placed in a kiln and heated. Cement tiles are not fired and derive their durability from the combination of finely dehydrated ground Portland cement
layer and a more course layer of sand and Portland cement. The pigment layer is hydraulically pressed into the surface and becomes a part of the tile, not a glaze or paint layer on the surface of the tile.
Depending on the locale, cement tiles are called by many names including: hydraulic cement tiles, mosaic tiles, encaustic cement tiles, mosaico hidraulicos, hydraulic tiles, ladrilhos hidráulicos, carreaux de ciments, Spanish mission tiles, Redondo tile, baldosas hidráulicas, hidraulicos antiguos, ladrilho de água, baldosas decoradas, hidráulicas de cemento.
The tile’s colorful patterns, durability and versatility have been attracting the attention of architects and designers for large commercial projects such as restaurants and hotels. Private homebuilders and “do it yourself” home improvement consumers have driven a growing segment of the cement tile market.
Following the discovery of Portland cement and development of hydraulic presses, cement tile, as we know them today is prepared without the use of clay or heating.
Cement tile appeared in the late 19th century in the south of France. Several sources say the first tiles were made near the country's first Portland cement plant. Around the turn of the 20th century, the tiles were very popular in the United States and were considered high-end floor covering. It was used in thousands of landmark public buildings and palaces. Their popularity began to wane in the U.S. sometime between the 1920s and ’30s and only started making a comeback in the 1980s and ’90s.
The metal mold, containing the desired pattern is hand-made from specific design drawings. The pigment composition is a mixture of high quality white Portland cement, marble powder, fine sand, and natural mineral color pigments.
Handmade cement tiles are each unique and are expected to have slight imperfections, which give them character and depth.
There are numerous cement tile manufacturers worldwide with the exception of the US. Presently there are no known cement tile manufacturers located in the US however there are several importers and distributors.
In general, the primary difference between manufacturers is the hydraulic method used in the production. Many small companies employ a hand-operated, manual hydraulic press in the process. The quality of these tiles varies due to inconsistent pressure, which affects the cement layers and attachment of the pigment layer.
Larger, modern manufacturers use electric-powered hydraulic presses that produce a consistently higher quality product. The higher pressure (1,500 PSI) permits a thicker pigment layer to be embedded in the cement layer, which produces a tile with a longer lifespan. The pigment layer is recommended to be 3–4 mm thick.
Another difference in manufacturers is the content of the pigments used. High quality producers use mineral-based pigments only. Non-mineral based pigments fade with age and normal wear. Another consideration is curing. Improper curing reduces quality. Tile should be cured for 2–4 weeks before installation.
floors. The durability of cement tiles for use in public areas is gaining popularity.
Cement tiles can be applied to concrete surfaces, any common underlayment, magnesium oxide wallboard
or any appropriate surface.
Although sometimes mistakenly called encaustic tile
Encaustic tile
Encaustic tiles are ceramic tiles in which the pattern or figure on the surface is not a product of the glaze but of different colors of clay. They are usually of two colors but a tile may be composed of as many as six. The pattern is inlaid into the body of the tile, so that the design remains as...
, which refers to kiln-fired clay tile or commonly used ceramic tiles that have been placed in a kiln and heated. Cement tiles are not fired and derive their durability from the combination of finely dehydrated ground Portland cement
Portland cement
Portland cement is the most common type of cement in general use around the world because it is a basic ingredient of concrete, mortar, stucco and most non-specialty grout...
layer and a more course layer of sand and Portland cement. The pigment layer is hydraulically pressed into the surface and becomes a part of the tile, not a glaze or paint layer on the surface of the tile.
Depending on the locale, cement tiles are called by many names including: hydraulic cement tiles, mosaic tiles, encaustic cement tiles, mosaico hidraulicos, hydraulic tiles, ladrilhos hidráulicos, carreaux de ciments, Spanish mission tiles, Redondo tile, baldosas hidráulicas, hidraulicos antiguos, ladrilho de água, baldosas decoradas, hidráulicas de cemento.
The tile’s colorful patterns, durability and versatility have been attracting the attention of architects and designers for large commercial projects such as restaurants and hotels. Private homebuilders and “do it yourself” home improvement consumers have driven a growing segment of the cement tile market.
History
Originally decorative tiles, known as encaustic tiles, were prepared from a pigmented clay base then heated or fired in a kiln. Tiles made by this method were very popular and can still be seen widely in Europe, Latin America and the US.Following the discovery of Portland cement and development of hydraulic presses, cement tile, as we know them today is prepared without the use of clay or heating.
Cement tile appeared in the late 19th century in the south of France. Several sources say the first tiles were made near the country's first Portland cement plant. Around the turn of the 20th century, the tiles were very popular in the United States and were considered high-end floor covering. It was used in thousands of landmark public buildings and palaces. Their popularity began to wane in the U.S. sometime between the 1920s and ’30s and only started making a comeback in the 1980s and ’90s.
Manufacture and quality
Cement tiles are made by hand, one at a time using a mold, mineral pigments, Portland cement and fine aggregate with a manual or electronic hydraulic press. There is no glaze or kiln. Cement tiles are cured by water and air only –just like ordinary cement.The metal mold, containing the desired pattern is hand-made from specific design drawings. The pigment composition is a mixture of high quality white Portland cement, marble powder, fine sand, and natural mineral color pigments.
Handmade cement tiles are each unique and are expected to have slight imperfections, which give them character and depth.
There are numerous cement tile manufacturers worldwide with the exception of the US. Presently there are no known cement tile manufacturers located in the US however there are several importers and distributors.
In general, the primary difference between manufacturers is the hydraulic method used in the production. Many small companies employ a hand-operated, manual hydraulic press in the process. The quality of these tiles varies due to inconsistent pressure, which affects the cement layers and attachment of the pigment layer.
Larger, modern manufacturers use electric-powered hydraulic presses that produce a consistently higher quality product. The higher pressure (1,500 PSI) permits a thicker pigment layer to be embedded in the cement layer, which produces a tile with a longer lifespan. The pigment layer is recommended to be 3–4 mm thick.
Another difference in manufacturers is the content of the pigments used. High quality producers use mineral-based pigments only. Non-mineral based pigments fade with age and normal wear. Another consideration is curing. Improper curing reduces quality. Tile should be cured for 2–4 weeks before installation.
Uses and applications
Cement tiles are widely used around the world in residences and commercial buildings and they are experiencing a revival in the US. Architects and interior decorators find cement a versatile product. The vibrant colors and ornate designs provide elements reminiscent of RenaissanceRenaissance
The Renaissance was a cultural movement that spanned roughly the 14th to the 17th century, beginning in Italy in the Late Middle Ages and later spreading to the rest of Europe. The term is also used more loosely to refer to the historical era, but since the changes of the Renaissance were not...
floors. The durability of cement tiles for use in public areas is gaining popularity.
Cement tiles can be applied to concrete surfaces, any common underlayment, magnesium oxide wallboard
Magnesium oxide wallboard
Magnesium oxide more commonly called magnesia is a versatile mineral that when used as part of a cement mixture and cast into thin cement panels under proper curing procedures and practices can be used in residential and commercial building construction...
or any appropriate surface.
Special considerations
Installation of cement tiles is different than installing ceramic tiles.- Cement tiles are normally seated with butt joints – without spacers. A small space between tiles will be visible and will require a grout mixture (unsanded) applied. Spacers to produce a larger grout line may be used, if so, sanded grout may be used.
- Prior to use each tile should be submerged in water and allow to stand 10–15 minutes before placement.It prevents the tiles from absorbing moisture from the thin-set too quickly and results in poor adherence to the surface and the tile.
- Sealing cement tile is not required prior to grouting; however, to prevent any stain from a colored grout sealing the tile is a good idea.
- Cement tiles are easily cared for wash with mild detergent and water. Avoid scrubbing with abrasives that can remove the finish and damage the pigment layer of the tile.